Reducing casting costs without compromising quality is crucial for foundries and manufacturers aiming to stay competitive. At KT-FOUNDRY, we understand the challenges of managing production expenses, and we’ve identified strategic approaches that can lead to substantial cost savings. This article outlines key strategies for reducing casting costs, with insights and practical applications that are relevant to the industry.
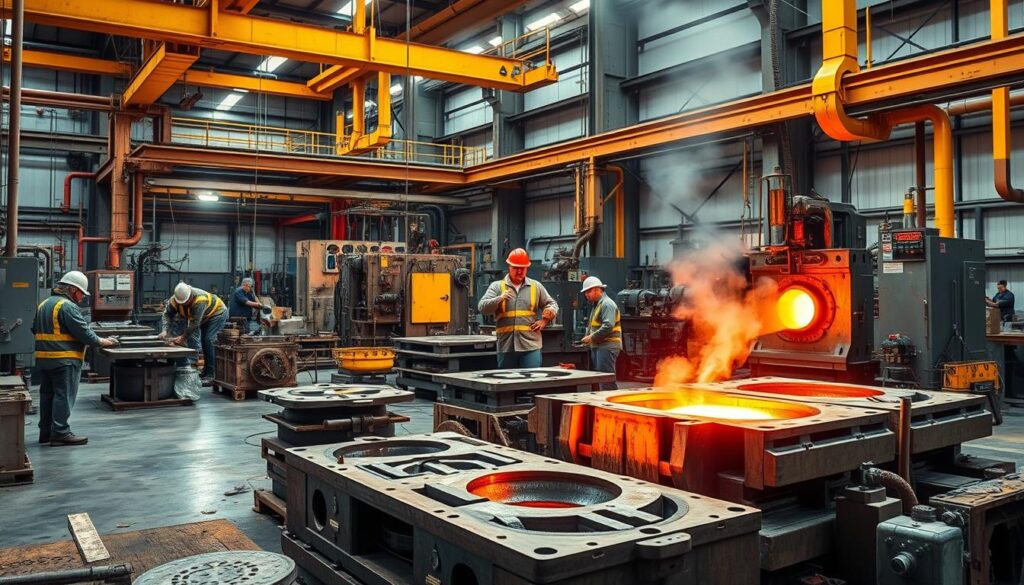
The casting process is both complex and expensive. Foundries are always looking for ways to work better and spend less. Whether you make unique parts or lots of the same thing, the right cost-saving steps can really help your profits.
In this article, we'll look at seven smart ways to make your casting process more efficient. These tips can help you stay on top in the market.
Introduction: Understanding Cost Drivers in Casting
Lowering costs in casting is key for keeping operations efficient and competitive. Foundries must tackle several cost drivers to boost profitability and sustainability. Knowing these factors is crucial for improving the casting process.
Why Cost Reduction Matters
The casting industry faces many challenges, like changing raw material prices and rising energy costs. Focusing on cost optimization helps foundries stay profitable and competitive. Lower costs mean better prices for customers, making the foundry more appealing.
The Benefits of Cost Reduction
Cost-saving efforts in casting bring many benefits. They increase profitability and financial stability. They also make the business more sustainable, helping it grow and stay competitive in the long run.
Cost Driver | Description | Impact on Casting Costs |
---|---|---|
Material Usage | The type and quantity of metals, alloys, and other materials used in the casting process. | Material costs can significantly impact the overall cost of casting, especially for high-quality or specialty alloys. |
Energy Consumption | The energy required for melting, heating, and powering the casting equipment and facilities. | Rising energy prices, such as for electricity and natural gas, can drive up the energy-related costs of casting operations. |
Labor | The workforce involved in various stages of the casting process, including mold making, metal pouring, and finishing. | Labor costs, including wages, benefits, and training, are a significant component of the overall casting costs. |
Equipment Maintenance | The costs associated with maintaining and repairing casting equipment, molds, and dies. | Proper maintenance and timely replacement of tools and equipment can help minimize downtime and related costs. |
Foundries can develop strategies to tackle these cost drivers. This way, they can make their casting operations more profitable and sustainable.
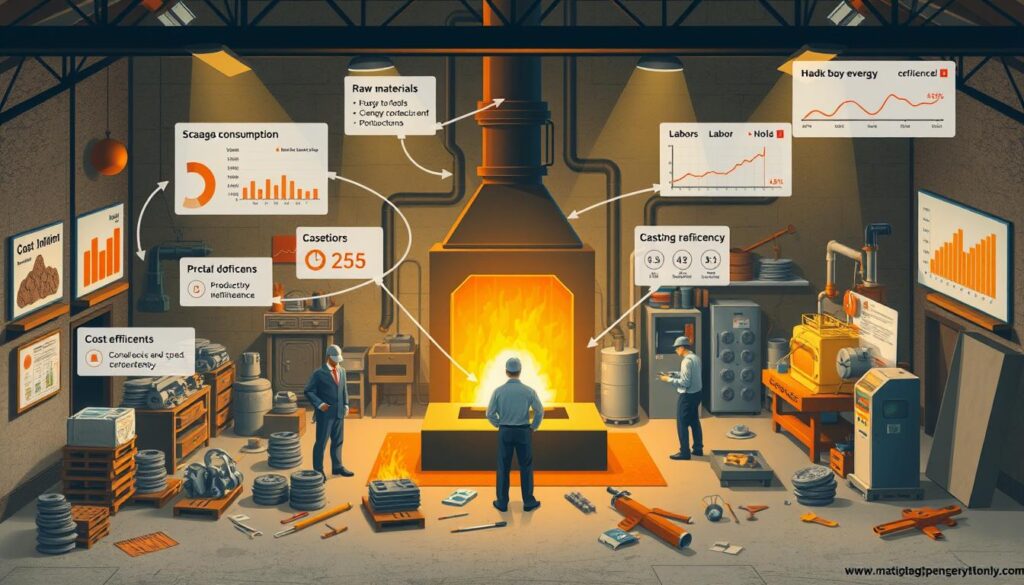
1. Optimize Material Selection and Usage
Choosing the right material for each casting project is foundational in controlling costs. While high-quality materials may come with a higher price tag, the cost is often offset by the durability and minimal waste they offer. At KT-FOUNDRY, we often help clients evaluate materials based on both performance and budget requirements, guiding them toward choices that reduce scrap and ensure consistent quality.
For instance, when working with clients who require corrosion-resistant properties, we may recommend alloys that not only meet durability needs but also reduce the need for extensive finishing. This approach has proven effective in several projects, including our custom cast iron pump shells that offer durability at an optimized cost.
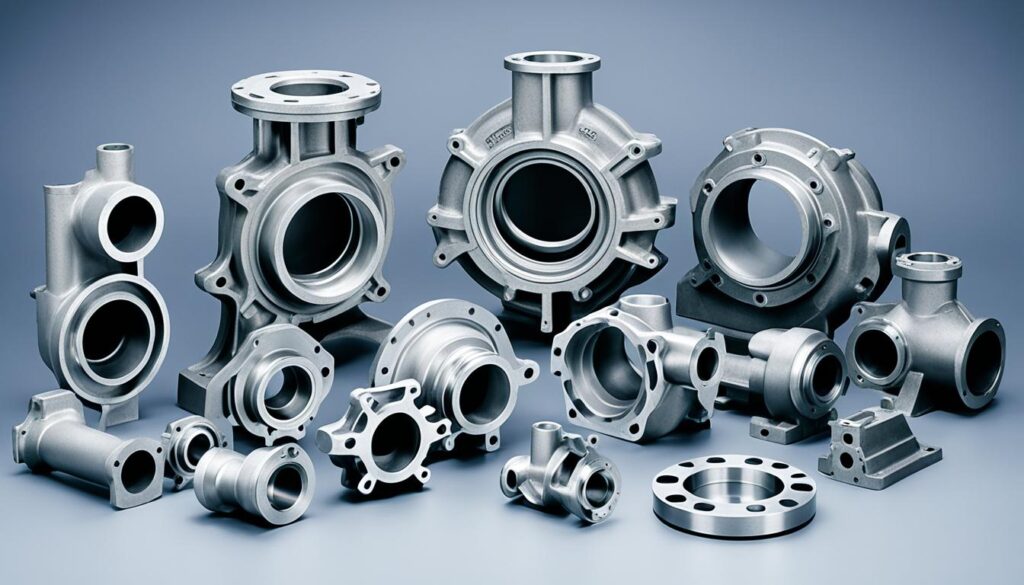
"Approximately 70% of a product's production costs stem from initial design decisions that influence material choices and manufacturing techniques."
Understanding the casting process and always looking for ways to improve is crucial. By focusing on material selection and waste reduction, you can save a lot of money and make your casting operations more efficient.
2. Enhance Design for Manufacturing Efficiency
An efficient casting design minimizes the need for excess material and complex processing, which directly reduces production costs. Casting designs should focus on simplicity, avoiding unnecessary features that add to manufacturing time and expense. By collaborating closely with clients on design specifications, KT-FOUNDRY has optimized production processes and reduced costs on multiple projects.
One recent example involved re-engineering a customer’s motor housing design. Our team simplified the layout, reducing material use and achieving better mold filling, which decreased cycle time by 10%. This optimized design not only cut down the client's production costs but also resulted in a stronger, more efficient component. Learn more about our motor housing solutions.
3. Invest in Quality Tooling and Maintenance
Investing in durable molds and maintaining them properly ensures that they remain effective over many production cycles, saving significant costs on repairs or replacements. At KT-FOUNDRY, we maintain a strict maintenance schedule for all molds, prolonging their lifespan and preserving casting precision.
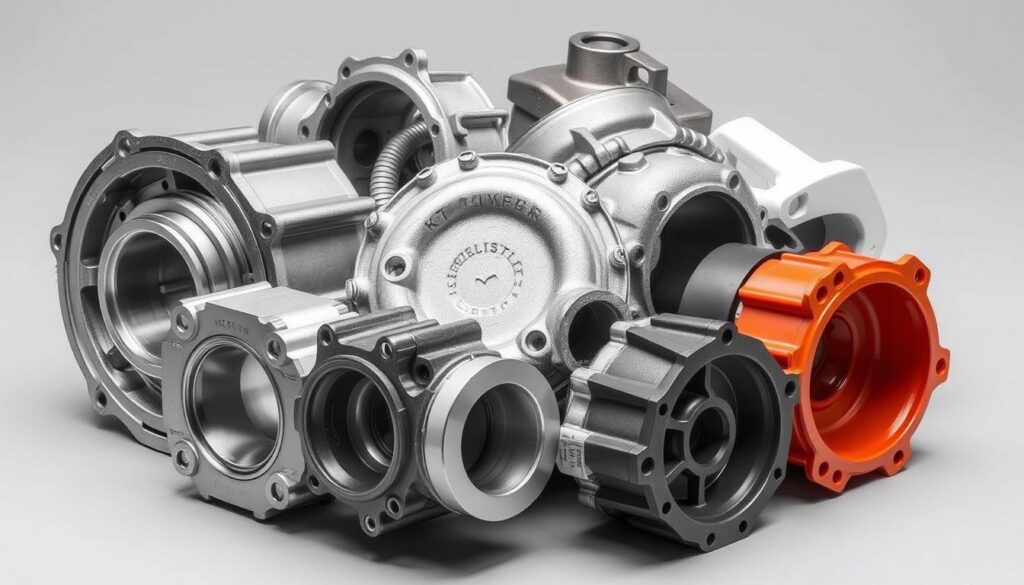
Our customers have found that this attention to tooling quality helps to reduce variations in casting, lowering the likelihood of costly rework. For instance, in a project for custom counterweights, we maintained tooling integrity for a high-volume order, leading to a smooth production run and minimal tooling expenses. Check out our custom counterweight options for more insights on our tailored solutions.
4. Streamline Production Processes
Optimizing production workflows directly affects the labor and overhead costs associated with each casting project. Automated systems, such as robotic handling, can reduce manual labor, while a lean manufacturing approach ensures efficient material use and minimal waste.
KT-FOUNDRY has adopted these principles across our operations, allowing us to deliver high-quality castings on schedule and within budget. In one case, we implemented a workflow enhancement for a client’s large order of pulley wheel sheaves. By refining our process, we minimized cycle times and decreased labor costs by 15%. Read more about our pulley wheel sheave production process.
Energy use is a big cost in the casting industry. To stay competitive and green, foundries need to use energy-saving methods. These methods help cut down energy use and costs. By using smart strategies, casting can save a lot of money and improve its profits
5. Leverage Energy-Efficient Techniques
Energy expenses in casting are substantial, making energy efficiency a key driver for cost reduction. We use advanced, energy-efficient furnaces and have optimized our preheating cycles to reduce energy consumption. Additionally, recovering waste heat has proven to be an effective method for further energy savings.
For example, in a recent production run for cast aluminum housings, KT-FOUNDRY reduced energy use by 20% through efficient temperature control and heat recovery measures. These savings were directly passed on to the client, proving the benefits of energy optimization in casting.
6. Reduce Scrap and Rework with Quality Control
Quality control measures can help minimize waste by ensuring that issues are detected early in the process. At KT-FOUNDRY, we use in-process inspections and conduct defect analysis to prevent scrap and rework. This approach is especially beneficial for large-scale projects, where minor quality deviations can lead to substantial expenses.
In a recent project involving heavy-duty castings, we identified minor defects early, allowing us to make adjustments and avoid potential rework. As a result, we reduced scrap rates by 8%, providing a significant cost advantage for the client while maintaining high standards.
7. Consider Outsourcing and Supplier Partnerships
Outsourcing specialized casting processes or working with reliable suppliers can lead to cost advantages by leveraging economies of scale and expertise. KT-FOUNDRY frequently collaborates with industry partners to provide tailored casting solutions that maximize savings for our clients.
Conclusion: Prioritize Long-Term Savings Over Short-Term Cuts
At KT-FOUNDRY, we stress the need to focus on long-term savings over quick cost cuts. A balanced strategy for sustainable cost reduction boosts your competitiveness and profitability. By using the strategies we've discussed, foundries can see big improvements in their casting work. This leads to lower costs, better quality, and more market share.
It might seem appealing to go for fast, short-term savings. But we think a long-term approach is the best way to unlock your casting operations' full potential. By investing in making things better, streamlining processes, and always looking to improve, you build a stronger business. This business can handle market changes and stay ahead of the competition.
When you start working to cut the cost of your casting, aim for long-term savings and sustainable cost reduction. This way of thinking will not only make your bottom line better. It will also make your place in the industry stronger, boosting your competitiveness and profitability for the long haul.
KT-Casting
Bring Your Designs to Reality– Experience Custom Perfection with On-Demand Casting!