Did you know that high-chrome content white cast irons, as defined by ASTM A532, are key in mining and construction? They are known for their hardness and wear resistance. Our guide explores this material in detail, showing its impact on industries.
ASTM A532 is a standard that sets the rules for this special cast iron alloy. It has hardness levels between 500 and 520 HV, making it perfect for tough environments. The material's makeup, heat treatment, and structure all contribute to its wear resistance. Let's dive into what makes ASTM A532 cast irons ideal for many industrial uses.
KT Foundryleads in making high-quality ASTM A532 abrasion-resistant cast iron parts. They serve industries like mining and mineral processing. Check out our guide to learn more about this material and its role in improving industrial efficiency.
Understanding ASTM A532 Standards and Specifications
ASTM A532 is a standard for casting wear-resistant steel, primarily used for producing wear-resistant castings. According to the ASTM A532 standard, the material is typically divided into several grades, including:
Type I: White cast iron with higher carbon and silicon content, mainly applied in high-impact and wear applications. It is commonly used in castings that require wear resistance, such as mining machinery and ball mills.
Type II: Contains alloying elements such as chromium, nickel, and molybdenum, providing excellent wear resistance and strength, and is typically used in more demanding wear environments.
Type III: Offers superior corrosion and wear resistance, making it suitable for high-temperature and high-pressure working environments.
In summary, ASTM A532 primarily describes high-alloy wear-resistant cast iron materials, commonly used in heavy machinery, mining, metallurgy, and other industrial sectors.
Here is an overview table of the chemical composition and mechanical properties of ASTM A532 Type I white cast iron grades:
rade | Main Chemical Composition (Weight Percent) | Hardness (HRC) | Tensile Strength (MPa) | Application |
Grade I-A | Carbon: 2.5-3.6% | 50-63 | 350-450 | Mining equipment, ball mill liners |
Silicon: 0.7-1.3% | ||||
Chromium: 11-13% | ||||
Manganese: ≤ 1.5% | ||||
Grade I-B | Carbon: 2.3-3.6% | 55-66 | 300-400 | Crusher hammers, grinding tools |
Silicon: 0.7-1.3% | ||||
Chromium: 15-18% | ||||
Manganese: ≤ 1.5% | ||||
Grade I-C | Carbon: 2.5-3.5% | 58-70 | 250-350 | Grinding equipment for high-wear conditions |
Silicon: 0.5-1.0% | ||||
Chromium: 23-28% | ||||
Manganese: ≤ 1.5% | ||||
Grade I-D | Carbon: 2.4-3.4% | 45-60 | 400-500 | Moderate wear and impact resistance |
Silicon: 0.8-1.5% | ||||
Chromium: 10-12% | ||||
Molybdenum: ≤ 0.5% | ||||
Grade I-E | Carbon: 2.0-3.0% | 60-72 | 200-300 | Industrial equipment requiring high wear resistance |
Silicon: 0.5-1.0% | ||||
Chromium: 25-30% | ||||
Nickel: ≤ 1.5% |
Table Explanation
- Main Chemical Composition: Each grade varies in carbon, silicon, and chromium content to meet specific hardness and wear-resistance needs; some grades include minor amounts of manganese, molybdenum, or nickel.
- Hardness: The hardness is indicated in Rockwell Hardness (HRC) and varies by grade to accommodate different levels of wear.
- Tensile Strength: Tensile strength indicates the maximum stress in MPa each grade can withstand under tension.
- Application: Specific applications for each grade, such as crushers, grinding tools, and ball mills, based on wear resistance needs.
Here is an overview table of the chemical composition and mechanical properties of ASTM A532 Type II white cast iron grades:
Grade | Main Chemical Composition (Weight Percent) | Hardness (HRC) | Tensile Strength (MPa) | Applications |
Grade II-A | Carbon: 2.5-3.5% | 45-60 | 300-450 | Mining equipment, slurry pumps, chute liners |
Silicon: 0.7-1.2% | ||||
Chromium: 11-14% | ||||
Molybdenum: 0.5-1.5% | ||||
Grade II-B | Carbon: 2.8-3.4% | 50-62 | 250-400 | Crusher hammers, high-impact wear parts |
Silicon: 0.7-1.2% | ||||
Chromium: 15-18% | ||||
Nickel: 1.0-3.0% | ||||
Grade II-C | Carbon: 2.6-3.2% | 55-65 | 200-350 | Grinding mills, ball mill liners, heavy wear applications |
Silicon: 0.6-1.1% | ||||
Chromium: 20-23% | ||||
Molybdenum: 1.0-2.0% | ||||
Grade II-D | Carbon: 2.4-2.8% | 48-60 | 250-400 | Crusher liners, mill hammers, high-stress equipment |
Silicon: 0.5-1.0% | ||||
Chromium: 18-21% | ||||
Nickel: 1.0-2.5% | ||||
Grade II-E | Carbon: 2.7-3.2% | 60-70 | 200-300 | High-abrasion environments like ore processing equipment |
Silicon: 0.4-0.8% | ||||
Chromium: 25-28% | ||||
Nickel: 2.0-4.0% |
Table Explanation
- Main Chemical Composition: Type II grades contain significant amounts of chromium, with additional elements like molybdenum or nickel to improve hardness and toughness.
- Hardness: Ranges between HRC 45-70, indicating high wear resistance across different grades.
- Tensile Strength: Moderate tensile strength suited for wear-intensive applications where ductility is not a priority.
- Applications: Type II white cast iron grades are suitable for moderate to high-impact wear environments such as mining, grinding, and crushing equipment, providing durability in applications that involve abrasive materials.
Here is an overview table of the chemical composition and mechanical properties of ASTM A532 Type III white cast iron grades:
Grade | Main Chemical Composition (Weight Percent) | Hardness (HRC) | Tensile Strength (MPa) | Applications |
Grade III-A | Carbon: 2.5-3.5% | 60-72 | 200-300 | High-wear parts such as pump casings and crusher liners |
Silicon: 0.5-1.0% | ||||
Chromium: 28-30% | ||||
Molybdenum: 1.0-2.0% | ||||
Grade III-B | Carbon: 2.8-3.2% | 55-65 | 300-400 | High-impact, wear-resistant applications like ball mill liners and hammer heads |
Silicon: 0.6-1.0% | ||||
Chromium: 20-25% | ||||
Nickel: 2.0-4.0% | ||||
Grade III-C | Carbon: 2.6-3.0% | 58-68 | 250-350 | Mining equipment, crusher wear liners |
Silicon: 0.5-1.0% | ||||
Chromium: 25-30% | ||||
Molybdenum: 0.5-1.5% | ||||
Grade III-D | Carbon: 2.4-2.8% | 65-75 | 180-250 | High-wear, high-temperature applications like coal pulverizers and mining crushers |
Silicon: 0.5-1.2% | ||||
Chromium: 30-35% | ||||
Vanadium: 0.5-1.0% | ||||
Grade III-E | Carbon: 2.8-3.3% | 68-78 | 150-250 | Extreme wear environments such as heavy grinding and ore-crushing equipment |
Silicon: 0.4-0.8% | ||||
Chromium: 32-37% | ||||
Nickel: 1.5-3.5% |
Table Explanation
- Main Chemical Composition: Type III grades generally contain high chromium levels to enhance wear resistance. Some grades also include molybdenum, nickel, or vanadium for improved high-temperature stability and wear resistance.
- Hardness: The hardness range is relatively high, typically between HRC 55-78, suitable for applications with extreme wear conditions.
- Tensile Strength: Tensile strength is generally low, making Type III cast irons suitable for high-wear, low-impact environments.
- Applications: Type III white cast iron is used in extreme wear applications, particularly where high temperatures are involved, such as coal mills, mining crushers, and heavy grinding equipment.
Testing and Certification Procedures
To follow the ASTM A532 standard, strict testing is done. This checks the material's hardness, tensile strength, and wear and erosion resistance. The certification process makes sure the cast iron parts meet these standards. This gives users confidence in their purchase of high-quality, dependable products.
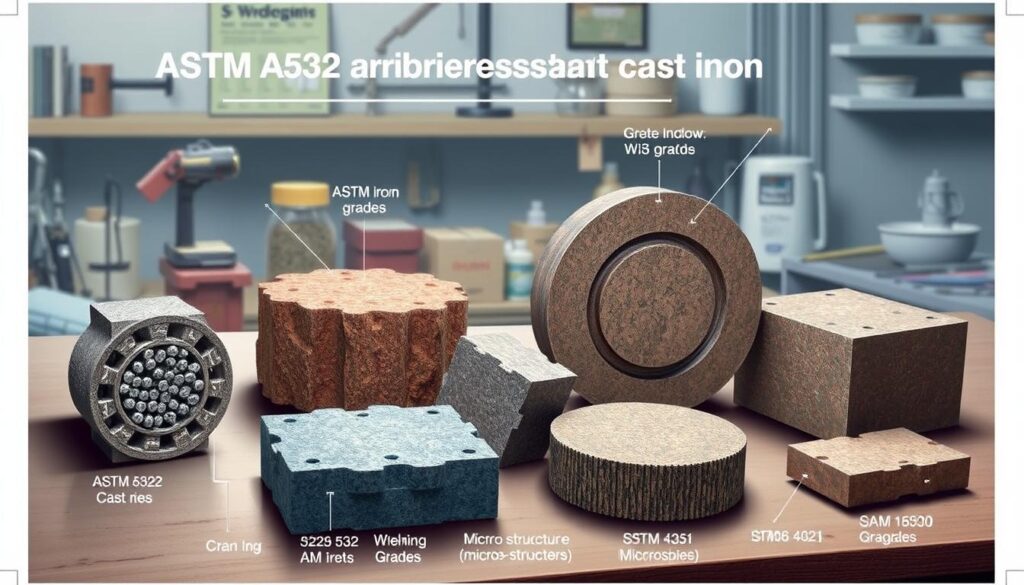
"Following the ASTM A532 standard is vital for both makers and buyers. It guarantees the quality, durability, and consistent performance of abrasion-resistant cast iron parts."
Applications and Uses in Industrial Settings
ASTM A532 abrasion-resistant cast irons are widely used in many industrial settings. They are key in mining and mineral processing. These materials are perfect for making crusher liners, grinding mill liners, and wear plates.
Their high wear resistance is a big plus. It makes them great for parts that face tough abrasive conditions.
Slurry Handling Systems
Slurry handling systems, like pump casings and impellers, also benefit. High-chromium cast irons protect against corrosion and erosion. This means these parts last longer, saving time and money on repairs.
Industrial Application | ASTM A532 Cast Iron Components |
---|---|
Mining and Mineral Processing | Crusher liners, Grinding mill liners, Wear plates |
Slurry Handling Systems | Pump casings, Impellers |
ASTM A532 cast irons are vital in mining equipment, crusher parts, grinding mills, and slurry pumps. Their wear-resistant liners help extend the life of important parts. This boosts productivity and cuts down on maintenance costs.
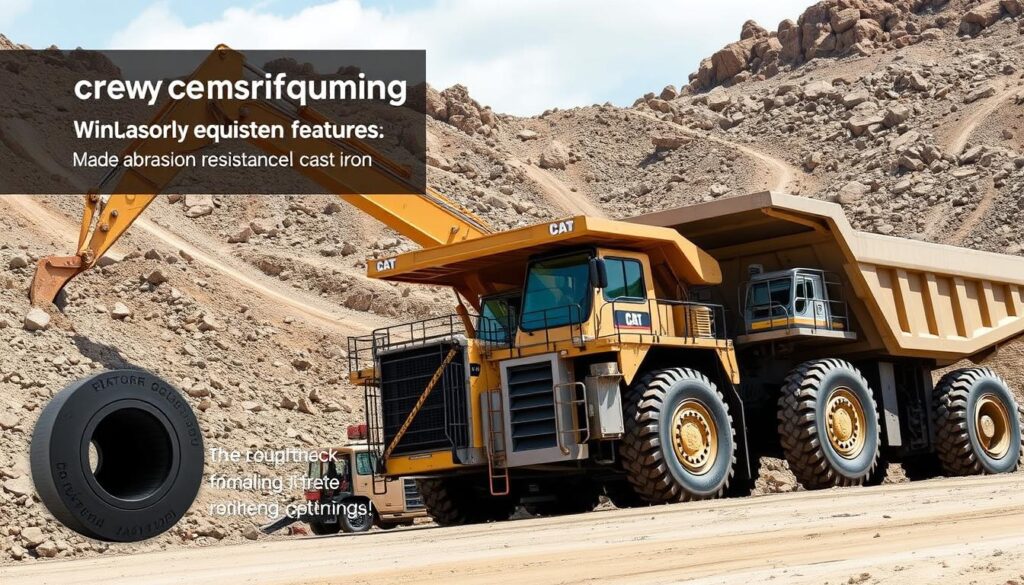
"ASTM A532 abrasion-resistant cast irons are essential for industries that rely on durable and reliable equipment, as they provide unparalleled protection against the harsh conditions found in mining, mineral processing, and slurry handling applications."
Manufacturing Processes and Heat Treatment
The making of ASTM A532 abrasion-resistant cast irons uses special casting methods like sand and investment casting. The casting process is key to getting the right structure and properties. Heat treatment is vital to boost the wear resistance of these materials. Quenching and tempering are used to control carbide formation and adjust the matrix structure.
The tempering temperature greatly affects the final properties. Lower temperatures make the material harder but can make it more brittle. It's important to heat treat these cast irons right to balance hardness, wear resistance, and toughness.
High chrome white cast irons in the ASTM A532 range have 11% to 30% Cr. These alloys can get very hard, making them good for many uses:
- Pliant25 alloy can get >600 BHN, great for hydraulic fracturing pumps.
- Granite25 is often >650 BHN, used a lot in mining and Oil Sands.
- Diamond25, with hardness over 680 BHN, is used in mining and recycling.
- Tough25 aims to boost toughness and hardness in thick castings, good for mining crushers.
Heat treatment steps like stress relief annealing, white mouth elimination annealing, and normalizing are key for ASTM A532 cast irons. Right heat treatment ensures the material has the right mix of hardness, wear resistance, and toughness for its use.
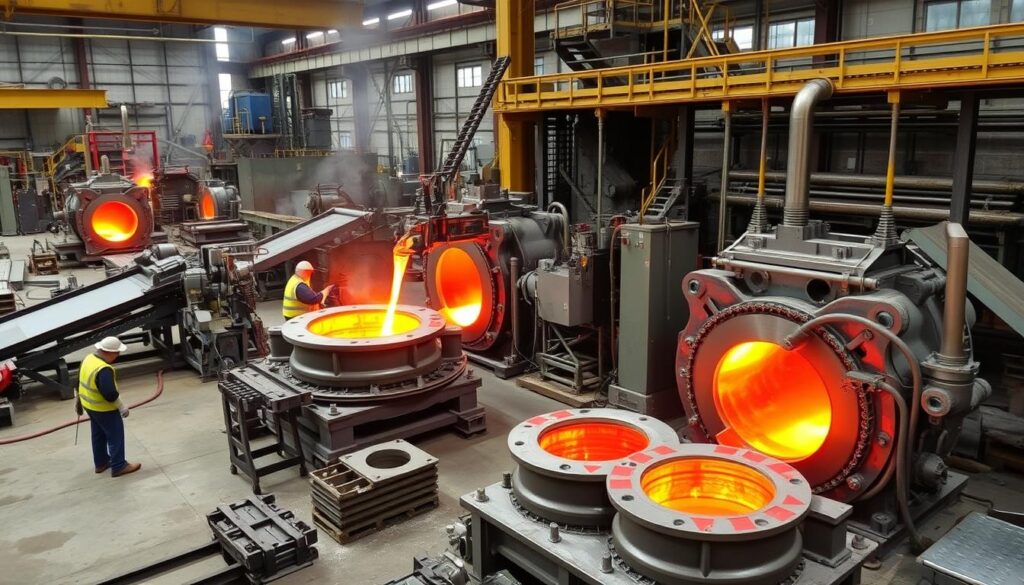
Heat Treatment Process | Temperature Range | Holding Time | Objective |
---|---|---|---|
Stress Relief Annealing | 500-550°C | 2-8 hours | Eliminate 90-95% of internal stress in castings |
White Mouth Elimination Annealing | 550-950°C | 2-5 hours | Eliminate white mouths in castings |
Normalizing of Ductile Iron | 820-860°C | - | Improve mechanical properties |
Quenching and Tempering of Ductile Iron | 30-50°C above Afc1 | - | Control microstructure and properties |
"Proper heat treatment is essential for balancing hardness, wear resistance, and toughness in ASTM A532 cast irons."
Conclusion
ASTM A532 abrasion-resistant cast irons are key for industries with tough wear challenges. They offer hardness, wear resistance, and toughness. This makes them vital in mining, mineral processing, and heavy industries.
Knowing the ASTM A532 standard and how these materials are made is important. It helps choose the right grade for each job.
KT-FOUNDRY is a leader in making high-quality, ASTM A532 compliant cast iron products. They offer custom solutions for industrial wear applications. Their knowledge in material science and casting ensures their products meet the ASTM A532 standard.
This means their abrasion-resistant cast iron solutions work well in tough environments.
The need for durable, wear-resistant materials like ASTM A532 compliant cast irons will keep growing. Staying updated and working with trusted suppliers like KT-FOUNDRY is key. This helps keep equipment running well and boosts business success.