Die casting has changed the game in the automotive world. It lets us make parts that are both strong and detailed. These parts are key for today's cars.
The car industry needs parts that are precise, strong, and efficient. Die casting fits the bill perfectly. It uses special methods and materials to make top-notch parts. Plus, it helps the environment by using materials wisely.
Key Takeaways
- Die casting is a vital technology for meeting the stringent requirements of the automotive industry.
- Automotive die casting enables the creation of complex and durable components essential for modern vehicles.
- The process aligns with the industry's need for precision, strength, and efficiency, while also promoting environmental sustainability.
- Specialized methods and materials used in die casting ensure the production of high-quality automotive parts.
- Die casting's versatility and adaptability make it a game-changer in the automotive manufacturing landscape.
Let's dive into the world of automotive castings. We'll look at the materials, uses, and methods that have changed this field. Join us as we explore how die casting is changing the car industry.
The article highlights the significanceof stainless steel exhaust manifolds, especially in turbocharged engines. They last long, resist corrosion, and handle high temperatures well. Stainless steel exhaust systems are great because they need little maintenance and work better.
The article also talks about making stainless steel turbo manifolds. It shows how important it is to design and make them with precision. This ensures they are strong and can handle heat well.
Introduction to Automotive Die Casting
The automotive industry relies heavily on automotive die casting for making top-notch parts. Die casting is a method that injects molten metal into a mold under pressure. It's key in automotive parts manufacturing for parts like engine blocks and body panels.
What Is Automotive Die Casting?
Die casting uses high pressure to fill a mold with molten metal, turning it into the desired shape. It's great for making parts with complex geometries and tight tolerances. The casting continues to be a top pick for automotive parts manufacturing because of its quality and performance.
Advantages of Die Casting in the Automotive Industry
Die casting in the automotive industry brings many benefits, including:
- Precision Manufacturing: It makes auto parts casting with exact dimensions and smooth finishes, cutting down on post-processing needs.
- Design Flexibility: The process allows for parts with complex shapes, giving design engineers more freedom.
- High Production Efficiency: Die casting used for casting automotive components has quick production cycles and high material use, saving costs.
- Lightweight Components: Using materials like aluminum and magnesium in die casting leads to lightweight automotive castings, essential for better fuel efficiency and lower emissions.
These benefits make die casting a top choice for the automotive industry in producing high-performance, precision parts and components.
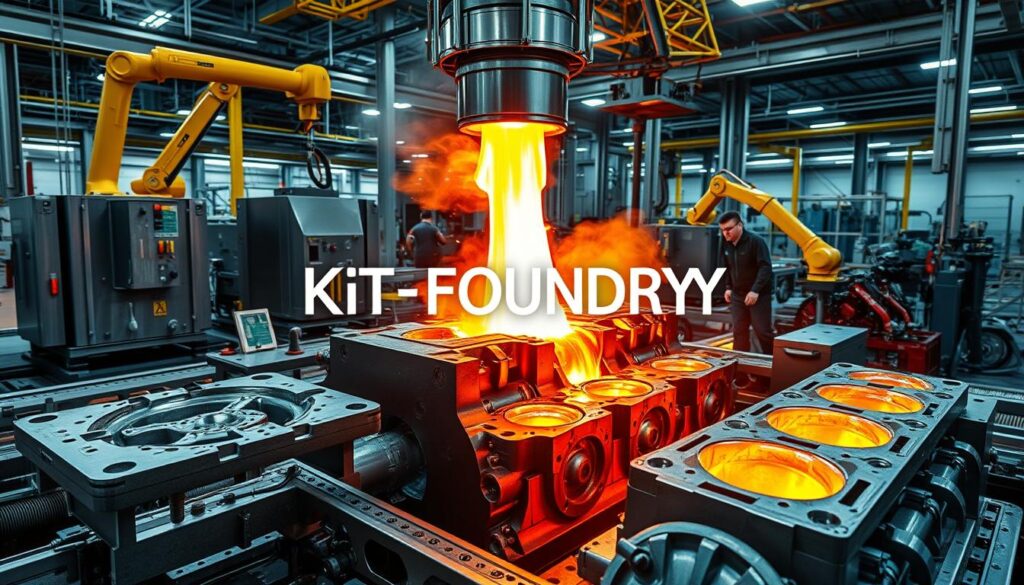
Common Metals for Automotive Castings
In the world of car making, picking the right metal for parts is key. Aluminum, magnesium, and zinc are top picks. Each metal has special qualities that meet different needs in the car industry.
Aluminum: Lightweight and Corrosion-Resistant
Aluminum is a favorite for car parts because it's strong yet light. It also resists corrosion and conducts heat well. This makes it perfect for outside parts where saving weight is important.
Aluminum can be shaped into complex designs. This makes it great for many car parts.
Zinc Alloys: Strength and Ductility
Zinc alloys are known for their strength and flexibility. They're often used in sturdier car parts, like chassis components. These alloys have a smooth finish and can be shaped into detailed designs.
This makes them ideal for enhancing both the look and function of car parts.
Magnesium Alloys: Lightweight and Strong
Magnesium alloys are valued for their light weight and strength. They're great for making cars lighter. These alloys are stable, can be recycled, and can be cast into large, thin parts.
This makes them a top choice for parts where saving weight is crucial.
Choosing the right metal for car parts is a careful process. It depends on the part's design and function. Things like how well the metal conducts electricity and heat, its hardness, and how it handles the environment are all important.
Metal | Key Properties | Automotive Applications |
---|---|---|
Aluminum | Lightweight, corrosion-resistant, high strength-to-weight ratio, good thermal and electrical conductivity | Exterior parts, engine components, transmission housings |
Zinc Alloys | High strength, ductility, smooth surface finish, tight tolerances, complex shapes | Chassis components, structural parts, gear housings |
Magnesium Alloys | Lightweight, high strength-to-weight ratio, dimensional stability, recyclability, thin wall capability | Instrument panels, steering wheel components, seat frames |
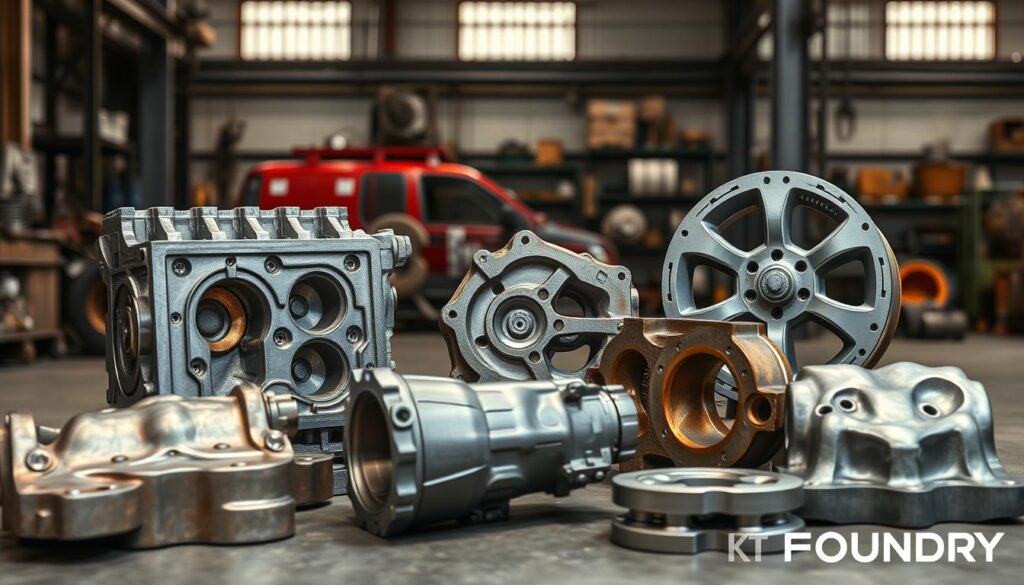
By using the special qualities of these metals, car makers can make parts that are light, strong, and efficient. This meets the changing needs of the car industry.
Applications of Automotive Castings
Automotive die casting is used in many parts of a vehicle. It helps make automotive parts that are strong and precise. This is key for the car industry's high standards.
Engine blocks are made with die casting for their complex designs. This ensures they work well and last long. Suspension systems and transmission systems also benefit from die casting's accuracy. This makes them more reliable and durable.
Brake parts and steering components are made safer with die casting. Body and chassis parts are built to exact standards. This improves the car's structure and safety. Electrical systems parts are also made with die casting, meeting today's car tech needs.
Die casting is not just for engine parts. It's used for many car parts, like body and chassis parts. This ensures all parts fit together well and work as they should.
"The automotive industry's reliance on die casting is a testament to its ability to deliver the performance, durability, and consistency that modern vehicles demand."
Diverse Applications of Automotive Castings
- Engine blocks and components
- Suspension system parts
- Transmission system housings and gears
- Brake calipers and rotors
- Steering knuckles and housings
- Body and chassis structural components
- Electrical system housings and enclosures
Automotive castings are crucial for a car's performance, safety, and reliability. The car industry depends on die casting for its high-quality parts. This shows how important it is for making cars.
Quality Control in Automotive Castings
Keeping the quality of automotive castings high is key for makers. At Auto Cast, we've set up a detailed quality control system. This ensures our die-cast parts meet the high standards of the auto industry. Our dedication to quality shows in our investments, certifications, and ongoing improvement efforts.
Challenges in Quality Control
Keeping quality high in mass production of auto castings faces many hurdles. Issues like material changes, human mistakes, and machine wear can lead to problems. To tackle these, we've put in place strong quality control steps in our making processes.
Solutions for Consistent Quality
- Regular calibration of our equipment to maintain precision and accuracy
- Implementation of automated monitoring systems to detect and address quality deviations in real-time
- Ongoing training and development for our staff to enhance their skills and knowledge in quality control
- Adherence to industry-leading quality standards, such as IATF 16949:2016, to align our processes with best practices
- Participation in the AIAG CQI-27 Special Process: Casting System Assessment to evaluate and continuously improve our casting operations
By investing in these quality control solutions, we ensure quality automotive castings that meet or exceed our customers' expectations. Our dedication to quality assurance and quality standards drives our success in the auto industry.
At Auto Cast, quality control is a habit. We make sure every auto casting we produce is of the highest quality and consistent quality. Our focus on solving quality issues and using effective quality solutions makes us a trusted supplier in the auto casting field.
Trends in Automotive Castings
The automotive industry is changing fast, and die casting is becoming more important. New technologies and changing needs are driving trends in automotive castings to grow and improve.
New materials and green practices are key to the future of automotive castings. Die casting's ability to make precise and strong parts is crucial. It helps meet the industry's needs for quality, efficiency, and sustainability.
Advancements in automotive castings are happening now. Semi-solid casting, or thixoforming, is making parts stronger and less prone to defects. It also reduces waste.
Also, innovations in automotive castings are leading to better metal alloys and composites. These materials are lighter and more durable, helping make cars more fuel-efficient and eco-friendly.
Die casting will be key in the future of car making. It will help create precise, lightweight, and green parts. These trends in die casting will drive the industry forward, making it a leader in innovation.
"The automotive casting market is poised for significant growth, driven by the industry's need for high-quality, efficient, and sustainable solutions. Die casting's versatility and precision make it a strategic choice for automotive manufacturers seeking to meet these evolving demands."
Die Casting Processes for Automotive Parts
Die casting is a highly efficient method used in the automotive industry to produce precise, complex metal parts. This process involves injecting molten metal into a mold under high pressure, resulting in components like engine blocks and transmission housings with excellent strength and surface finish. It’s ideal for reducing production time and costs.
Aluminum and zinc alloys are commonly used in die casting for their balance of strength and light weight, which helps improve fuel efficiency. High-pressure die casting is perfect for producing thin-walled parts with tight tolerances, while low-pressure casting suits larger parts with superior durability.
Once the metal solidifies, parts require minimal machining, speeding up production. Additional treatments can enhance performance and customization. Overall, die casting is crucial for manufacturing lightweight, durable automotive parts, ensuring high-quality production and vehicle efficiency.In the automotive world, two main die casting methods are used: hot chamber and cold chamber die casting. Each has its own benefits, and the right choice depends on the part's needs.
Hot Chamber Die Casting
Hot chamber die casting is a key process for producing intricate metal parts, particularly with low-melting-point metals like zinc, magnesium, and lead. This method injects molten metal into a heated chamber and mold under high pressure, allowing for detailed, complex shapes and fast production rates. It also minimizes oxidation and ensures excellent surface finishes, making it ideal for automotive and electronic components.
The process offers high dimensional accuracy, reducing assembly time and costs. Additionally, the molds used in hot chamber die casting have a longer lifespan, further lowering production expenses. Industries rely on this technique for efficiency and precision, often partnering with specialized die casting services for custom solutions, from mold design to post-casting treatments.
In short, hot chamber die casting is a versatile, cost-effective method for producing high-quality, reliable metal parts, meeting the growing demands of modern manufacturing.It's especially good for high-volume automotive parts.
Cold Chamber Die Casting
The cold chamber method uses a ladle to pour molten metal into the mold. It's better for metals that melt at higher temperatures, like aluminum and copper. This method gives more control over the casting, making it great for complex parts.
Both hot chamber die casting and cold chamber die casting have their own strengths. The choice depends on the part's needs. These methods help make parts that are precise, durable, and affordable for today's cars.
"Die casting is a crucial manufacturing process that allows us to create complex, high-quality automotive parts with unparalleled efficiency and consistency."
Automotive Castings: Finishes and Surface Treatments
In the world of automotive die casting, the goal is more than just making parts. It's about getting the perfect finish. This finish must look good and also make the parts last longer and work better. The industry uses many techniques to improve the quality of these parts.
The way parts are made affects their finish. According to the American Foundry Society, surface finishes for automotive castings can range from 20 to 900 RMS. Shell mold casting, for example, usually has a finish between 75 to 150 RMS. Vacuum casting can get up to 200 RMS. But die casting and squeeze casting can get as low as 20 RMS.
The type of material used also matters for the finish. Aluminum castings tend to have a smoother finish compared to iron or steel castings due to their lower melting points. Sand casting makes parts look rougher. But nobake or shell molding can make them look like ceramic.
To meet the needs of the automotive industry, many finishing techniques are used. These include:
- Polishing
- Shot blasting
- Power coating
- Painting
- Anodizing
- Electroplating
- Chromate conversion coating
- Passivation
- Electrophoretic coating
Each method has its own benefits. They can make parts look better, last longer, and work better. Proper tool quality and die maintenance are crucial for achieving the best surface finish in mold casting.
The automotive industry is always looking to improve. They need parts that are not just good but great. By focusing on surface finishing, they can make parts that exceed what customers expect.
Industries Utilizing Automotive Castings
Die casting is key in many industries, known for its ability to make complex parts efficiently. It's used in the automotive industry, electronics, aerospace, and consumer goods. This process is shaping the future of these sectors.
Automotive Industry
In the automotive world, die casting makes engine blocks, transmission housings, and more. The global market for automotive castings was over $107.2 billion in 2020. It's expected to grow by more than 5% from 2021 to 2027.
Electronics Industry
The electronics field uses die casting for parts like housings, connectors, and heat sinks. As technology advances, the need for durable, precise parts grows.
Aerospace Industry
The aerospace sector also benefits from die casting. It's used for lightweight parts and avionics. The market was $15,051 million in 2021 and could hit $24,451.2 million by 2030.
Consumer Goods Industry
The consumer goods industry uses die casting for many products. This includes appliance parts, hardware, and toys. Its ability to make detailed, high-quality parts is valuable.
Die casting's versatility and precision make it essential in many industries. It drives innovation and meets the needs of modern products.
Industry | Die Casting Applications | Market Size and Growth |
---|---|---|
Automotive | Engine blocks, transmission housings, and other essential parts | $107.2 billion in 2020, projected to grow over 5% from 2021 to 2027 |
Electronics | Housings, connectors, and heat sinks | N/A |
Aerospace | Lightweight structural components and avionics parts | $15,051 million in 2021, expected to reach $24,451.2 million by 2030 |
Consumer Goods | Appliance parts, hardware, and toys | N/A |
"Die casting's versatility and precision have solidified its position as a crucial manufacturing process across numerous industries, driving innovation and meeting the evolving demands of modern-day products and applications."
FAQ
What are automotive castings and why are they important in the automotive industry?
Automotive castings refer to the process of creating automotive parts through various casting methods. These methods involve pouring molten metal into a mold to form components that are integral to the operation of vehicles. The importance of casting in the automotive industry lies in its ability to produce complex shapes and designs with high dimensional accuracy, which is crucial for performance, safety, and efficiency in automobiles. Additionally, automotive castings can be made from different materials, such as aluminum and zinc, which are known for their lightweight properties and strength, making them ideal for automotive applications.
What are the different types of casting processes used in the automotive sector?
There are several casting processes employed in the automotive sector, including:
1. Die casting: This involves forcing molten metal into a mold at high pressure. It can be categorized into:
- Cold chamber die casting: Used for metals with high melting points.
- Hot chamber die casting: Suitable for metals with lower melting points.
2. Sand casting: A traditional method that uses sand molds to create automotive components.
3. Gravity die casting: Relies on gravity to fill the mold with molten metal, ideal for larger parts.
4. Investment casting: Also known as lost-wax casting, this process is used for intricate automotive parts requiring fine detail.
Each method has its own advantages and is chosen based on the specific requirements of the automotive parts being produced.
What materials are commonly used for automotive castings?
The most common materials used for automotive castings include:
- Aluminum alloys: Known for their lightweight properties and corrosion resistance, making them ideal for engine parts and automotive components.
- Zinc die casting: Offers good strength and durability, often used in die-cast components for exterior parts.
- Iron and steel: Used for heavier components, where strength is a key factor.
These materials are selected based on their mechanical properties, weight considerations, and cost-effectiveness for the manufacture of automotive
Conclusion
Die casting is key in the automotive world. It meets the industry's needs for quality, efficiency, and new ideas. It makes parts strong, precise, and flexible in design.
Die casting is used in many car parts, like engine blocks and suspension systems. It shows how wide its impact is. As technology gets better, die casting will be even more important in making cars.
Using die casting helps make cars better, stronger, and more efficient. The market for die-casting car parts is growing. New technologies, like giga-castings, are changing the game. At KT-FOUNDRY, we're ready to lead in this fast-changing field. We make top-notch die cast parts for the car industry.