Turbochargers are key in today's engines. They boost power, improve fuel use, and cut emissions. The turbo impellers, the compressor and turbine wheels, are vital. They use exhaust gas energy to compress air.
Knowing the materials and how they're made is key. It helps make turbochargers work better, last longer, and be more reliable.
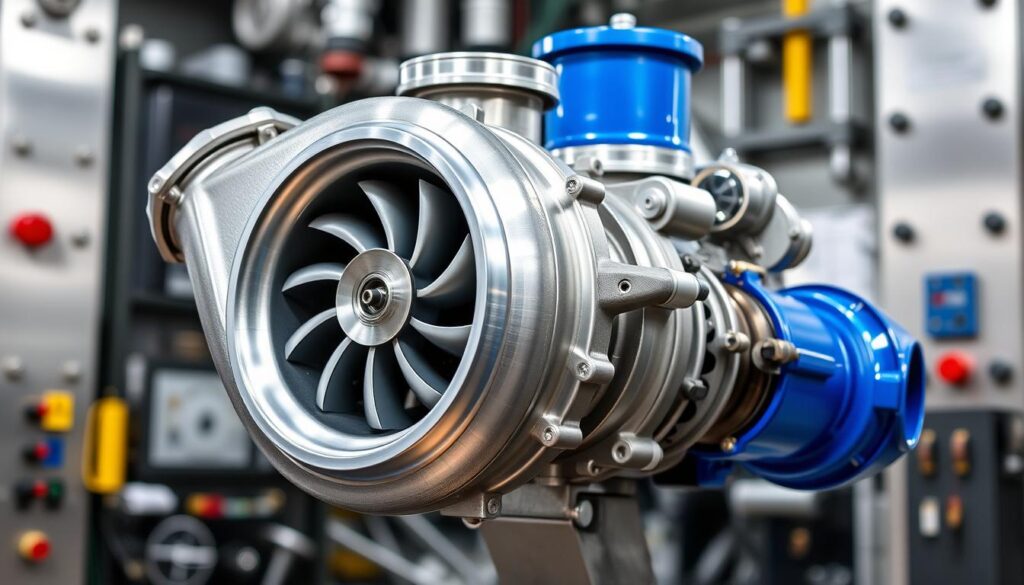
This guide explores turbo impeller design in detail. We look at the materials used, their properties, and how they're made. We cover aluminum, titanium, and stainless steel, discussing their pros and cons.
We also focus on design aspects. These ensure the turbocharger works efficiently, manages pressure well, and flows smoothly.
Core Function of Turbo Impellers
Turbo impellers are key to turbochargers' success. They compress intake air, boosting engine power and saving fuel. This is crucial for modern engines.
Energy Optimization
Turbo impellers use exhaust gas energy to power the compressor. This makes the engine more efficient. It also means more power without using more fuel.
Pressure Maintenance
Keeping the right pressure between intake and exhaust is vital. Turbo impellers control this pressure. They ensure the engine runs well under different conditions.
Enhanced Flow Dynamics
The design of turbocharger impellers improves air flow. This leads to better engine performance and fuel use. Their shape reduces air turbulence and increases air volume.
Impeller Material | Key Benefits |
---|---|
Lightweight, High-Strength Alloy | Reduced mass, improved acceleration, lower overall turbocharger load |
Excellent Heat and Corrosion Resistance | Enhanced durability in high-temperature, high-pressure environments |
Optimized Fluid Mechanics Design | Greater intake volume, higher compression ratio, improved power output |
Advanced Manufacturing Processes | Consistent performance characteristics, improved reliability |
Turbo impellers are essential for better engine performance and fuel efficiency. They are vital for the automotive industry's success.
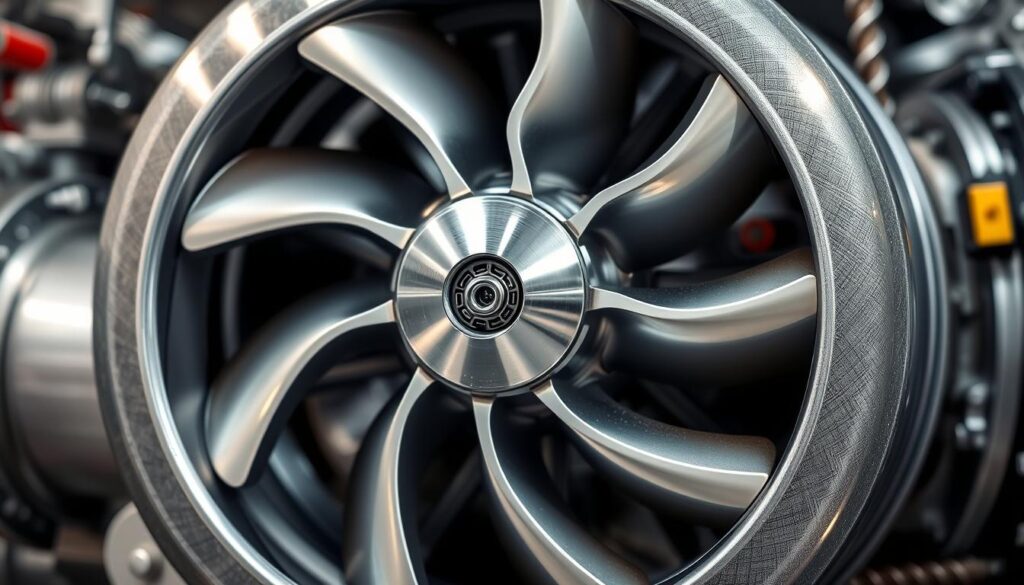
Common Materials Used for Turbo Impellers
Turbocharger impellers are key parts that boost engine performance and efficiency. They face high temperatures, pressures, and stresses. So, picking the right materials is very important.
Let's look at the common materials for turbo impellers and their benefits.
Aluminum Alloys
Aluminum alloys, like AA2618 T652, are light and good at cooling. They balance strength, corrosion resistance, and heat management well. This makes them great for improving fuel efficiency and power.
Titanium
Titanium alloys are strong, light, and resistant to corrosion. They handle high temperatures and pressures well. This ensures turbochargers work reliably for a long time.
Stainless Steel
Stainless steel is durable and affordable for turbo impellers. It's not as light as aluminum or as strong as titanium. But, it's a good mix of mechanical properties and cost for many turbocharger needs.
Composite Materials
Composite materials, like Inconel alloy, are used more in turbo impellers. They resist high temperatures better and perform well in tough applications. This can make turbochargers more efficient and powerful.
Choosing the right material for turbo impellers is key. It affects the turbocharger's performance, efficiency, and durability. Manufacturers and designers must weigh factors like weight, strength, temperature resistance, and cost. This ensures the turbocharger works well and reliably.
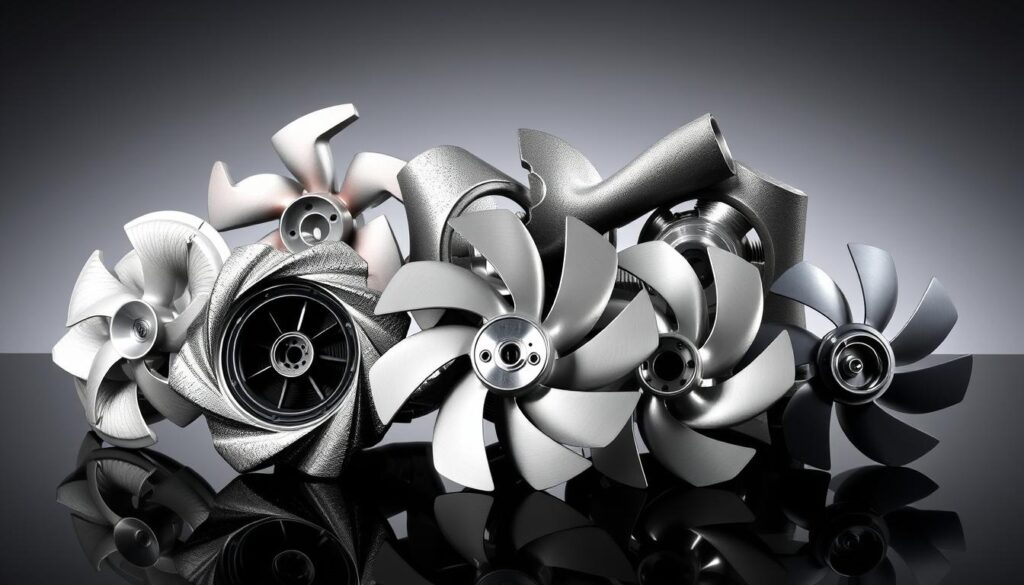
"Choosing the right material for turbo impellers is crucial in achieving the desired performance, efficiency, and reliability in various engine applications."
Critical Design Aspects
The design of turbo impellers is key to making turbochargers work better. Many important parts need to be carefully made. This ensures air flows well, gets compressed right, and the system works smoothly. Let's look at the main design points that make turbo impellers successful.
Blade Geometry
The shape and layout of the impeller blades are very important. They affect how air flows and gets compressed. Designing these blades well helps air get in, get compressed, and leave efficiently. This boosts the turbocharger's performance.
Impeller Diameter
The size of the turbo impeller matters a lot. A bigger impeller can push air harder but might take longer to start. Finding the perfect size is key for the turbocharger to work its best.
Shaft Design
The turbo shaft connects the compressor and turbine impellers. It's vital for balance and to stop vibrations at high speeds. Good design and materials in the shaft keep the impellers stable and prevent damage.
Inducer and Exducer
The inducer and exducer areas are designed to handle air intake and discharge. The inducer brings air in, and the exducer lets compressed air out. Making these areas work well improves the system's efficiency and performance.
Clearances
Keeping the right clearances between the impeller and the housing is crucial. These small gaps prevent the impeller from touching other parts at high speeds. Managing these clearances well ensures the turbocharger works efficiently and safely.
Design Aspect | Key Considerations |
---|---|
Blade Geometry | Curvature, angle, and spacing |
Impeller Diameter | Boost pressure and response time |
Shaft Design | Balance, vibration, and stability |
Inducer and Exducer | Air intake and discharge management |
Clearances | Radial and axial clearances for efficiency and safety |
By focusing on these design points, engineers can make turbo impellers better. This improves the whole turbocharger system's performance, efficiency, and reliability.
KT-Foundry
Bring Your Designs to Reality– Experience Custom Perfection with On-Demand CNC Machining!
"Achieving the right balance between impeller size, boost, and responsiveness is the key to unlocking the full potential of turbocharger technology."
Key Manufacturing Processes for Turbo Impellers
Turbochargers boost engine performance by compressing intake air and delivering it at higher pressures. The turbo impeller is key in this process. It's made with care to ensure top efficiency and performance.
Precision casting is a common method for making turbo impellers. These cast impellers are then heat treated to make them stronger and more durable. On the other hand, CNC machining allows for tighter tolerances and better balance in the impellers.
Special forming techniques like shot peening or coatings are used to boost the impellers' wear resistance and aerodynamic properties. These steps help the impellers handle the high temperatures and pressures they face. This lets the engine burn fuel efficiently and compress the air well.
Strict quality control measures are in place. These include dimensional inspection and high-speed balancing. They ensure the turbo impellers work at their best and are reliable.
Manufacturing Process | Key Features |
---|---|
Precision Casting | Enhances strength and durability through heat treatment |
CNC Machining | Provides tighter tolerances and improved balance |
Advanced Forming Techniques | Improves wear resistance and aerodynamic properties through surface treatments |
Using these advanced manufacturing methods, engineers can make turbo impellers that improve engine performance, compression, and efficiency. This leads to a more responsive and fuel-efficient drive.
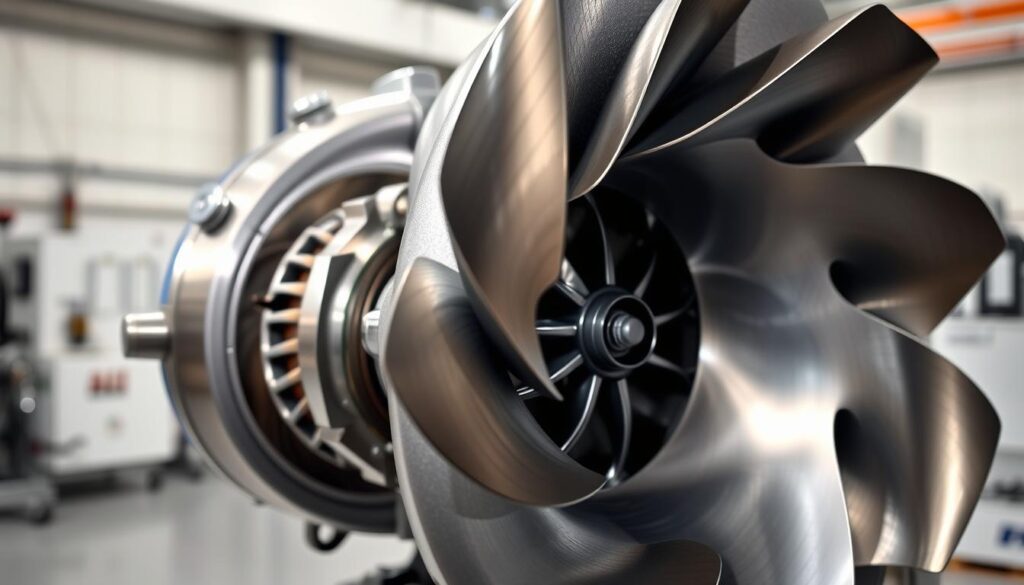
Conclusion
Turbo impellers are key parts in today's engines. They help engines use less fuel, make more power, and pollute less. New materials and ways to make them are making turbochargers better and better.
The car world keeps changing, and turbo impellers lead the way in engine tech. They help meet tough rules on pollution and meet people's wants for cars that go fast and use little fuel.
Studies show picking the right materials and making them right is key for turbo impellers. Inconel and Incoloy are top choices because they handle stress and heat well. But, aluminum can crack and rust, showing we need to keep improving.
As engines get better, turbo impellers will play an even bigger role. They help engines work better, handle more pressure, and run smoothly. With new materials and making techniques, turbochargers will get even better. This will help make engines that are good for the planet and use less fuel, for cars and planes too.
FAQ
What is a turbocharger and how does it work?
A turbocharger is a device that increases the power output of an engine by forcing more air into the combustion chamber. It consists of two main components: the compressor and the turbine. The exhaust gas from the engine spins the turbine, which in turn drives the compressor wheel to compress the incoming air. This process allows the engine to burn more fuel and improve fuel efficiency. The turbocharger system is crucial for enhancing engine performance and reducing emissions.
What materials are commonly used for turbo impellers?
Turbo impellers are typically made from materials that can withstand high temperatures and pressures. Common materials include various alloys such as aluminum and titanium. Titanium is preferred for its strength-to-weight ratio and resistance to corrosion, making it ideal for high-performance applications. The choice of material directly affects the efficiency and durability of the impeller, as it needs to resist wear and maintain structural integrity during operation.
What manufacturing processes are used for turbo impellers?
The manufacturing of turbo impellers involves several processes, including casting, machining, and forging. Investment casting is often used for creating complex shapes with high precision. After casting, machining processes such as milling and turning are employed to achieve the desired specifications. Forging is another method that enhances the material properties of the impeller by aligning the grain structure, thus improving strength and resistance to fatigue.
How do the dimensions of an impeller affect its performance?
The dimensions of an impeller, including its diameter and blade design, significantly affect the performance of a turbocharger. A larger impeller can move more air, thus increasing boost and power output. However, this can also lead to increased vibration and potential <