Aluminum alloy casting is a key method for making complex parts. It uses molten aluminum poured into a mold to create parts. This method is vital in the aluminum industry, offering benefits like low melting points and strong solids when cooled.
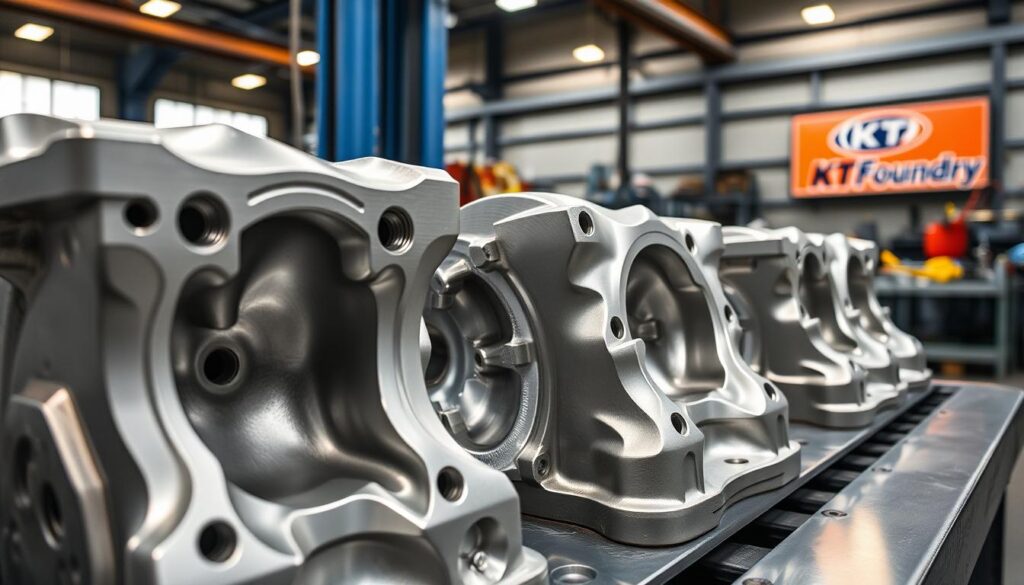
Brief overview of aluminum alloy castings
Aluminum alloy castings are made by mixing aluminum with other elements. This mix boosts certain properties. They are strong, flexible, and can handle heat well, making them useful in many fields.
Aluminum castings are known for being light yet strong. They resist corrosion and conduct heat and electricity well. Different alloys are made for different needs, like handling high temperatures or being easy to cast.
The unique qualities of aluminum alloy castings make them popular in many areas. They are used in cars, planes, electronics, and sports equipment because of their lightness, strength, and resistance to corrosion.
Benefits of Aluminum Alloy Castings
- Lightweight
- High Strength
- Corrosion Resistance
- Excellent Castability
- Thermal and Electrical Conductivity
- Recyclability
- Cost-Effectiveness
- Good Wear Resistance
- Ductility and Machinability
- Versatility
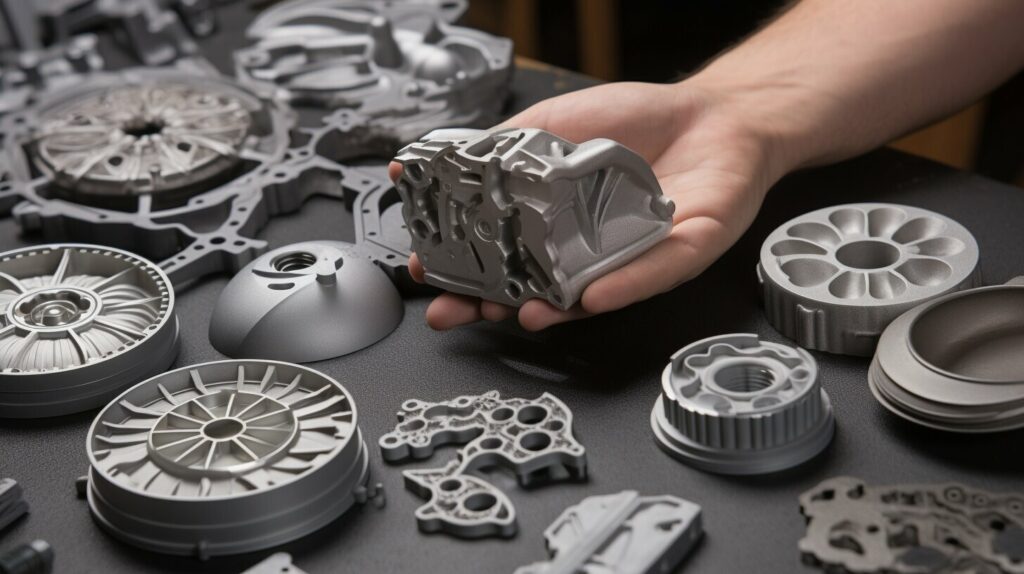
"The close tolerance maintained in the production of castings leads to negligible dimensional variation and high accuracy piece-to-piece consistency."
Aluminum alloy castings are versatile and precise. They're great for making lots of parts quickly and affordably. They're used in many fields, like medicine, robotics, and aerospace.
Common Aluminum Casting Alloys
Aluminum casting alloys are classified based on their composition, particularly the primary alloying elements. The most common aluminum casting alloys include:
1.A356 (Al-SiMg) Alloy
Composition: 92-94% Aluminum, 6-7% Silicon, 0.3-0.45% Magnesium
Properties: This is one of the most widely used aluminum alloys for casting due to its excellent castability, good corrosion resistance, and moderate strength. It’s commonly used in automotive and aerospace applications.
Applications: Engine blocks, transmission cases, and aerospace components.
2.A380 (Al-SiCu) Alloy
Composition: 8-12% Silicon, 2.5-4% Copper, 0.5-1% Magnesium, balance Aluminum
Properties: Known for its excellent fluidity and high dimensional stability, A380 is often used for high-pressure die casting. It offers good wear resistance, making it suitable for parts requiring high durability.
Applications: Automotive parts, including engine components, and electronics housings.
3.A319 (Al-SiCu) Alloy
Composition: 5-8% Silicon, 3-4% Copper, 0.5-1.5% Magnesium, balance Aluminum
Properties: This alloy has good mechanical properties, including strength and wear resistance. It also features good casting ability and is often used for medium-strength applications.
Applications: Castings for automotive engines, pistons, and parts exposed to moderate wear.
4.B319 (Al-SiCu) Alloy
Composition: 6-9% Silicon, 3-4% Copper, 1-1.5% Magnesium, balance Aluminum
Properties: Offers good strength and thermal conductivity with higher wear resistance compared to other alloys. It also has good resistance to oxidation.
Applications: Engine parts, transmission cases, and automotive housings.
5.C355 (Al-SiCuMg) Alloy
Composition: 6-9% Silicon, 2-3% Copper, 0.3-0.45% Magnesium, balance Aluminum
Properties: C355 is a high-strength alloy with excellent corrosion resistance. It is used in applications where both strength and durability are critical.
Applications: Heavy-duty engine blocks and structural components.
6.F357 (Al-SiMg) Alloy
Composition: 7-9% Silicon, 0.3-0.5% Magnesium, balance Aluminum
Properties: Known for excellent fluidity, high corrosion resistance, and strength, making it suitable for both casting and post-casting processes like machining and welding.
Applications: Aerospace, automotive, and industrial machinery components.
7.LM6 (Al-Si) Alloy
Composition: 11-13% Silicon, balance Aluminum
Properties: LM6 offers excellent castability, high corrosion resistance, and good wear properties. It is often used in applications exposed to the elements or extreme conditions.
Applications: Marine and outdoor applications such as pump components and engine parts.
8.505.2 (Al-SiMg) Alloy
Composition: 6-7% Silicon, 0.25-0.45% Magnesium, balance Aluminum
Properties: Offers excellent corrosion resistance and good weldability, making it ideal for marine and transportation industries.
Applications: Boat parts, truck components, and other outdoor machinery.
9.Aluminum 2024 (Al-Cu) Alloy
Composition: 3.8-4.9% Copper, 1.2-1.8% Magnesium, balance Aluminum
Properties: Known for its high strength, but it is generally used for casting in applications where high strength-to-weight ratios are required. It has good fatigue resistance and is commonly used in aerospace applications.
Applications: Aircraft structures, structural components, and aircraft engine parts.
10.Aluminum 7075 (Al-Zn-Mg) Alloy
Composition: 5.1-6.1% Zinc, 2.1-2.9% Magnesium, 1.2-2.0% Copper, balance Aluminum
Properties: Known for its exceptional strength, particularly at high temperatures. It’s often used in aerospace, military, and other high-stress applications.
Applications: Aerospace, military, and high-performance applications requiring high strength and stress resistance.
These alloys vary in their composition, properties, and suitability for different casting methods (such as sand casting, die casting, and investment casting). The choice of alloy depends on the intended application, required mechanical properties, and environmental conditions the final product will face. At KT-FOUNDRY, we specialize in providing customized aluminum alloy castings tailored to meet the specific needs of our clients, ensuring that each part is designed for optimal performance and longevity.
KT-Casting
Bring Your Designs to Reality– Experience Custom Perfection with On-Demand Casting!
For more information about our casting services and capabilities, visit KT-FOUNDRY.
The right aluminum alloy depends on your project's needs. By knowing what each alloy can do, you can make your product better. This helps it last longer and work better.
The Importance of Heat Treatment for Aluminum Castings and Its Types
Heat treatment is essential for optimizing the mechanical properties of aluminum castings, improving strength, hardness, and overall performance. By applying controlled heating and cooling, manufacturers can tailor the alloy's characteristics to meet specific application requirements. Common heat treatment types include annealing, which softens the material; solution heat treatment and aging, which enhance strength; and stress relieving, which reduces internal stresses. These processes ensure that aluminum castings perform reliably in demanding industries like automotive, aerospace, and machinery.
Heat Treatment Types of Aluminum Alloys Used in Casting
- Annealing (O-Condition)
- Solution Heat Treatment (T6-Condition)
- Aging (T5, T6, T7 Conditions)
- Stress Relieving (W-Condition)
- T4 Condition
- T3 Condition
- T2 Condition (Strain-Hardened)
- Welding and Post-Weld Heat Treatment (PWHT)
Manufacturing Process of Aluminum Alloy Castings
Aluminum alloy castings can be made in several ways, each suited for different needs. These include die casting, investment casting, and sand casting. Knowing the benefits of each method helps choose the best one for a project.
Die Casting
Die casting uses high pressure to pour molten aluminum into steel molds. It's great for making lots of parts quickly and accurately. This method is perfect for complex shapes and thin parts, used in cars, machines, and gadgets.
Investment Casting
Known as lost wax casting, this method makes detailed aluminum parts. It uses wax patterns covered in a special material. Investment casting is ideal for parts needing a high-quality finish, like in aerospace and medicine.
Sand Casting
Sand casting makes big, simple parts or small batches. It's cheaper upfront than other methods. Though not as precise, it's flexible for unique parts.
Each casting method has its own strengths. Knowing these helps manufacturers choose the best way to make aluminum parts. This ensures they meet the needs of today's industries.
Casting Method | Dimensional Accuracy | Surface Finish | Production Speed | Tooling Cost |
---|---|---|---|---|
Die Casting | Excellent | Excellent | Highest | Highest |
Investment Casting | Very Good | Premium | Moderate | Moderate |
Sand Casting | Good | Good | Highest | Lowest |
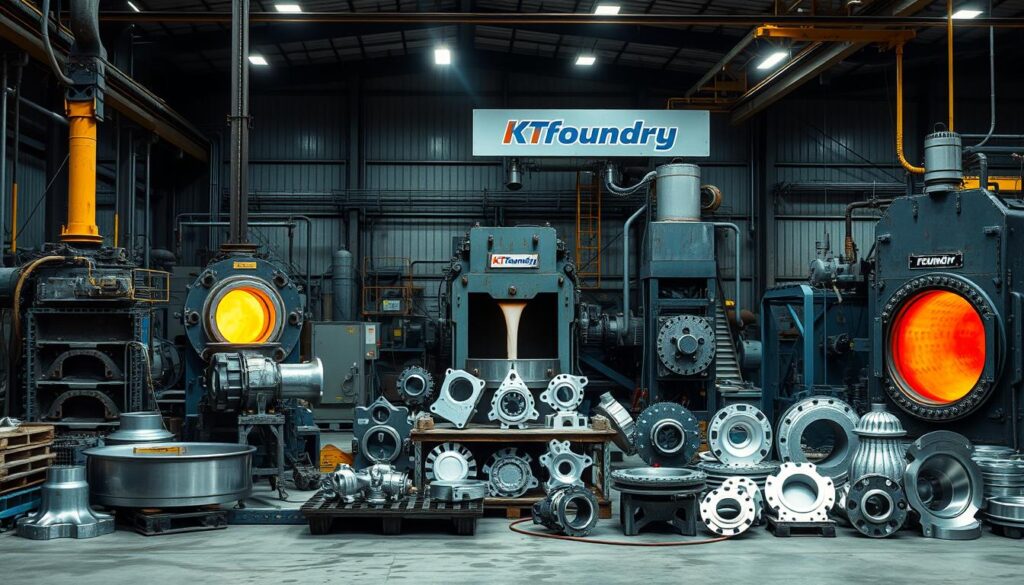
Using the right aluminum casting method helps make parts that are both high-quality and affordable. This meets the changing needs of today's industries.
Conclusion
Aluminum alloy castings are key in today's manufacturing world. They offer a mix of light weight, strength, and resistance to corrosion. These castings are used in many fields, from cars and planes to industrial tools and everyday items.
Choosing the right casting method and alloy is crucial. This way, makers can create products that fit exact needs. This is how aluminum castings help meet various industry demands.
As we need lighter, stronger materials more than ever, aluminum castings will keep leading in innovation. Companies like KT-Foundry are at the top, offering top-notch aluminum casting solutions. They use the latest tech and know-how to serve many industries.
These castings are vital in today's industrial world. They bring new chances for makers to create innovative products. This meets the changing needs of customers and industries all over the globe.