Investment casting, also known as precision casting or lost wax casting, is a traditional method. It has evolved to meet today's industry needs. It starts with creating a wax pattern, then encloses it in a ceramic shell. After melting out the wax, molten metal is poured into the cavity.
This method allows for parts with intricate details and tight tolerances. It's perfect for complex shapes and high-quality finishes. Investment casting works with many metals, including aluminum, and is good for small batches or prototypes.
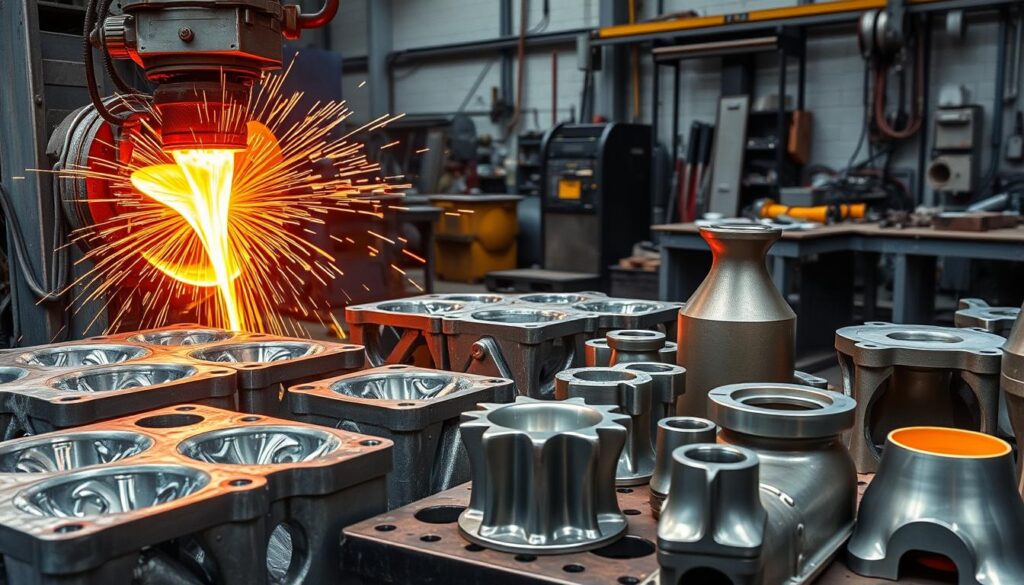
Die casting and sand casting are also common metal casting techniques. Die casting uses molds made from strong alloys to press molten metal, resulting in high-quality products. Sand casting, however, is better for making large parts but doesn't offer the same precision or consistency.
Understanding the differences between aluminum investment casting and other methods is key. We'll look at precision, material choices, production sizes, and costs. This will help businesses choose the best casting process for their needs.
Understanding the Fundamentals of Investment Casting Process
The investment casting process, also known as the lost wax method, is a precise way to make high-quality aluminum alloy parts. It starts with making a wax pattern of the part you want. This wax is then covered in a ceramic slurry to make a strong shell.
After the shell hardens, it's heated to melt the wax. This leaves a cavity that looks just like the original part design. This cavity is where the molten metal will be poured to create the part.
The Lost Wax Method Explained
The lost wax casting process has several key steps. First, a wax pattern is made to match the final part's exact details. This wax model is then dipped in ceramic slurry, layer by layer, to build a strong shell.
Once the shell is hard, it's heated to melt the wax. This leaves a cavity ready for molten aluminum alloy. The alloy is then poured into this cavity, solidifying into the finished part.
Key Components and Materials Used
- Wax patterns: These detailed models are the starting point for the final part. They are made to match the desired specifications.
- Ceramic shell: Layers of ceramic slurry are applied to the wax pattern. This creates a durable shell that can handle the molten metal pouring process.
- Aluminum alloy: Various aluminum alloys, like A07130, are used for their strength and other benefits.
Process Steps and Quality Control
- Wax pattern creation: Skilled artisans make the wax model to the exact dimensions and contours of the desired part.
- Ceramic shell formation: The wax pattern is covered in multiple layers of ceramic slurry, making a strong shell.
- Wax removal: The ceramic shell is heated, causing the wax to melt and drain away, leaving a precise cavity.
- Molten metal pouring: Molten aluminum alloy is poured into the cavity, solidifying into the finished component.
- Ceramic shell removal: After the metal cools, the ceramic shell is broken away, revealing the final cast part.
- Quality control: Throughout the process, strict quality control measures are followed to ensure precision and consistency.
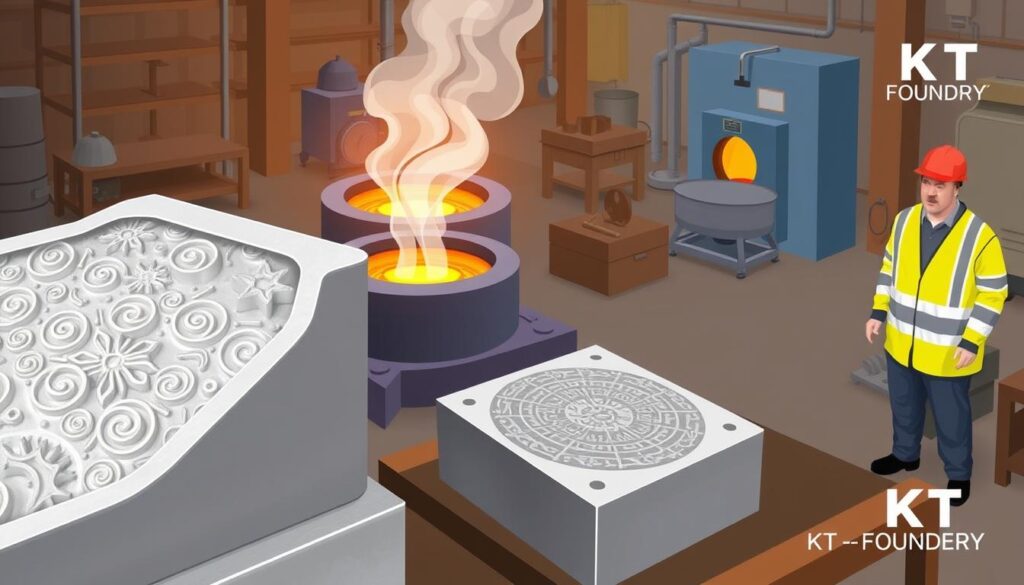
"The investment casting process allows us to create complex, high-precision aluminum parts with exceptional dimensional accuracy and surface finish."
Precision and Accuracy in Aluminum Investment Casting
Aluminum investment casting is known for its high precision and accuracy. It can make detailed components with tight tolerances. This is hard to do with other methods.
It's great for making complex shapes and thin parts. This makes it perfect for industries needing precision and light materials.
This method has a high dimensional accuracy. It can achieve tolerances as tight as +/- 0.010 inches per inch. This is better than sand casting, which has a range of CT8 to CT9.
High-quality ceramic molds are used. They help keep the precision by controlling mold changes during solidification.
Accuracy Grade | Tolerance Range (40-63 mm dimension) |
---|---|
CT4 | 0.36 mm |
CT8 | 1.4 mm |
It can also make thin-walled aluminum parts. These parts are as thin as 0.070 inches. This is great for industries like aerospace and automotive, where weight matters.
The process can also get very good surface finishes. The RMS values can be as low as 125. This means less need for extra machining, saving time and money.
"Aluminum investment casting is a game-changer for industries that require precision, complex shapes, and tight tolerances. Its ability to deliver consistent dimensional accuracy and outstanding surface finishes makes it an increasingly popular choice for a wide range of applications."
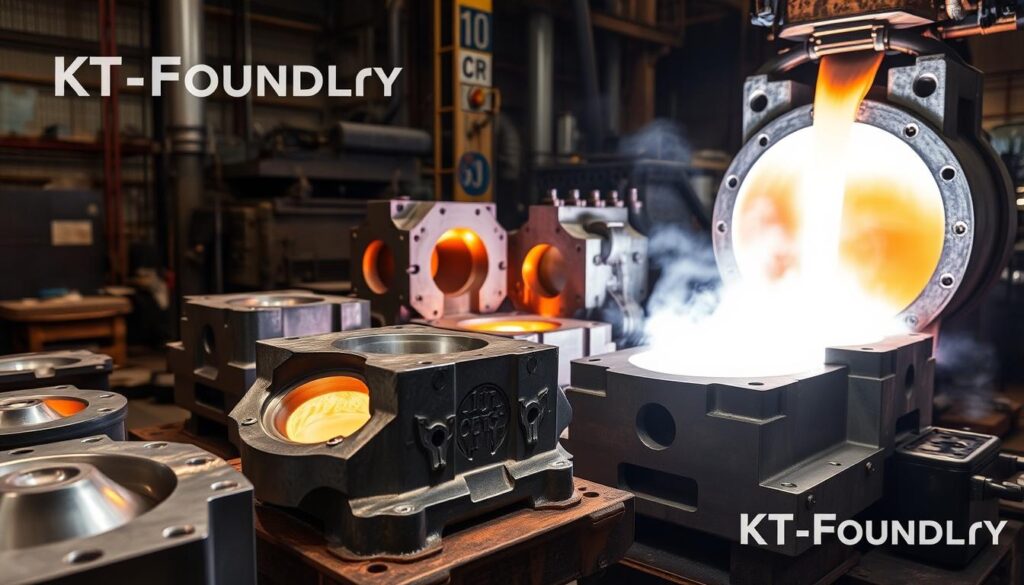
In conclusion, aluminum investment casting is a top choice for making high-quality, light, and detailed parts. It meets the strict needs of aerospace, automotive, and medical device industries. This makes it a leading casting method.
Comparing Different Metal Casting Techniques
In the world of metal casting, there are many techniques. Each has its own benefits and drawbacks. Knowing these differences is key to picking the best method for your needs.
Die Casting Methods and Applications
Die casting uses high pressure to pour molten metal into a mold. It's great for making lots of parts from non-ferrous metals like aluminum. But, it's not the best for big or complex parts.
Sand Casting Benefits and Limitations
Sand casting is affordable and works with many metals. It uses temporary sand molds, which saves money upfront. But, it's not as precise as some other methods, and costs can add up.
Permanent Mold Casting Characteristics
Permanent mold casting, or Permold, is more precise than sand casting. It's a good balance between cost and quality. Permold parts are dense, have consistent properties, and are easy to work with.
Casting Technique | Production Volumes | Tooling Cost | Unit Cost | Precision |
---|---|---|---|---|
Die Casting | Very High | High | Low | Medium |
Sand Casting | Low | Low | High | Low |
Permanent Mold Casting | Medium | Medium | Medium | High |
Every metal casting method has its own strengths and weaknesses. It's important to think about your project's needs to choose the right one.
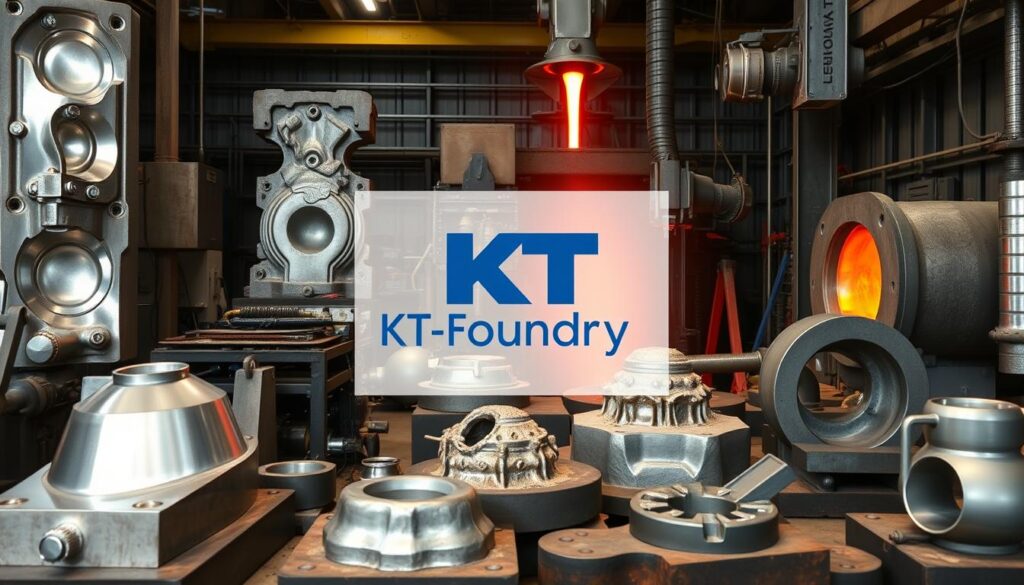
Material Properties and Selection Criteria
In the world of investment casting, picking the right material is key. Aluminum alloys, especially A356, stand out for their great properties. They have low density, high strength, excellent corrosion resistance, and good thermal conductivity. The right aluminum alloy can greatly affect the casting's strength, durability, and performance.
When choosing materials, we look at tensile strength, elongation, and heat treatability. A356 offers a mix of these qualities, making it a top choice for casting projects.
Aluminum Alloy | Tensile Strength (PSI) | Yield Strength (PSI) | Elongation (%) | Hardness (HB) |
---|---|---|---|---|
A356 | 45,000 - 50,000 | 30,000 - 35,000 | 3 - 5 | 75 - 85 |
A357 | 48,000 - 53,000 | 32,000 - 37,000 | 4 - 6 | 80 - 90 |
A380 | 40,000 - 45,000 | 25,000 - 30,000 | 2 - 4 | 70 - 80 |
Aluminum alloys are versatile and have excellent corrosion resistance, lightweight, and thermal conductivity. They are favored in many industries, like aerospace, automotive, and medical devices. By choosing the right aluminum alloy, casting experts can achieve the desired mechanical properties and performance.
"Aluminum alloy selection is a critical step in the investment casting process, as it directly impacts the casting's durability, functionality, and overall quality."
Whether you're making a high-performance aerospace part or a precise medical device, the material properties and selection criteria are crucial. They determine the success of your investment casting project.
Surface Finish and Dimensional Tolerances
Aluminum investment casting is known for its top-notch surface finishes and precise dimensions. The process controls every step carefully. This leads to parts that meet high quality standards, often better than other casting methods.
Achieving Precise Surface Quality
Investment castings have a smoother surface than sand-molded ones. For high-temperature alloys, they can reach a surface roughness average (Ra) of about 5 μm. This is much smoother than the minimum of RMS560 for sand-molded castings.
The investment casting process makes this possible. The wax pattern and ceramic mold create a smooth surface. This method is best for high-melting-point alloys that need a fine finish.
Precise Dimensional Control
Investment casting also offers tight dimensional tolerances. Parts can have tolerances of about ±0.005 inches per inch. This precision comes from controlling the entire casting process.
This method also avoids the need for drafts on vertical walls. This boosts the accuracy of the parts. Plus, the smooth finish often means less need for post-processing and machining.
Post-Processing for Enhanced Functionality
Even with great surface quality and accuracy, parts might need extra work. Heat treatment, machining, and surface treatments like polishing can improve them. These steps can enhance the part's look, strength, and performance.
Investment casting's flexibility and precision make it a top choice for many industries. This includes aerospace, automotive, and medical devices.
Cost Considerations and Production Volumes
The cost of aluminum investment casting changes with the amount produced. The initial setup costs are often lower than die casting. But, the process needs more labor, which can raise the total cost.
Investment casting is best for small to medium batches. It's great for complex parts that need a lot of machining. This method can create detailed shapes and high precision without extra steps.
For making lots of parts, die casting might be cheaper. This is because it can handle large quantities better. The cost depends on the material, part design, how many are made, and any extra steps needed.
Cost Factors | Impact on Investment Casting |
---|---|
Material Selection | The choice of alloy can significantly affect the overall cost, with some materials being more expensive than others. |
Part Complexity | Complex parts that require intricate designs or additional machining can increase production costs. |
Production Quantity | Investment casting can be more cost-effective for smaller production runs, while die casting may be more economical for high-volume manufacturing. |
Post-Processing Requirements | The need for additional finishing steps, such as heat treatment or surface treatments, can impact the overall cost of the casting process. |
To keep costs down and production efficient, choose experienced foundries. They should offer good prices and quick delivery for your projects. This ensures your needs are met.
Applications Across Industries
Aluminum investment casting is used in many industries. It's great for making complex, precise parts. This makes it perfect for aerospace, automotive, medical, and industrial needs.
Aerospace and Defense
In aerospace and defense, it's used for key parts like turbine blades and fuel system components. It creates detailed shapes and tight fits. This ensures these parts work well under stress.
Automotive Components
Car makers use it for engine parts, transmission housings, and more. It makes parts that are both light and strong. This helps cars use less fuel and perform better.
Medical Device Manufacturing
The medical field uses it for implants, surgical tools, and diagnostic parts. It's all about precision and consistency here.
It's also used in power generation, oil and gas, and making consumer goods. Its skill in complex shapes and quality parts is unmatched.
Aluminum is light, strong, and resistant to corrosion. Frigate uses its casting skills to make top-notch parts. These parts help drive innovation and efficiency in many fields.
Conclusion
At KT-FOUNDRY, we think aluminum investment casting is a game-changer. It brings precision, versatility, and complex shapes to the table. Yes, it might cost more upfront than other methods. But the quality and savings in the long run make it worth it.
Investment casting is a favorite for industries needing top-notch products. Our team at KT-FOUNDRY is all about bringing new ideas to the table. We serve sectors like aerospace, defense, automotive, and medical devices. We make sure our clients get products that exceed expectations.
KT-FOUNDRY is always looking to improve in casting technology. We want our clients to have the best tools and solutions. If you want better components or new designs, we're here to help. Let's move forward together.