Aluminum casting is a key part of making things in metallurgy. It lets us create complex parts from liquid metal. We pour molten aluminum into a mold to make a finished product.
Aluminum is the third most common element on Earth. It's used a lot because it melts easily and turns into strong solids when it cools. The process has come a long way from ancient copper casting to today's advanced methods.
At KT-Foundry, we offer top-notch aluminum casting services. We help our clients with all sorts of aluminum casting needs. This guide will dive into the details of aluminum casting, its benefits, and the different methods used in the industry.
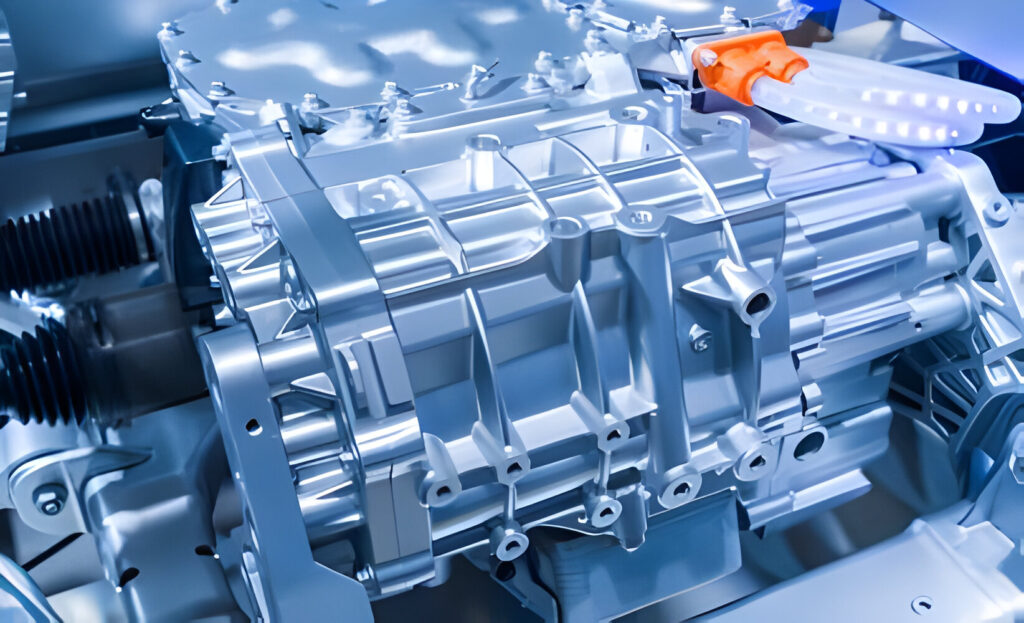
Understanding Aluminum Casting Techniques
Aluminum is a versatile material used in many industries. we offer top-notch aluminum casting solutions. We use advanced techniques like sand casting, die casting, and permanent mold casting.
Sand Casting
Sand casting is a cost-effective method for making aluminum parts. It starts with a wooden pattern that's packed into sand with a binding agent. The pattern is then filled with molten aluminum by hand or with automation.
This method is great for making parts in small quantities. It's also good for creating larger parts quickly. However, the tool is destroyed after each use, making it a one-time process. It's perfect for making prototypes because it's affordable.
Die Casting
Die casting is very efficient. It uses a hardened steel tool to pour or force molten aluminum into. This process can be automated for making lots of parts.
It's done in cold chamber machines, where aluminum is ladled from a separate pot. This method makes parts with high accuracy and quality. It's perfect for big production needs in industries like aerospace and medical.
Permanent Mold Casting
Permanent mold casting is similar to die casting but uses gravity. It clamps two steel mold halves together and fills them by hand pouring. This makes parts stronger and with a good finish.
It's great for making parts for cars and planes. This method balances strength, accuracy, and surface quality. It's a favorite in many industries.
Each casting method has its own benefits. The choice depends on how many parts you need, their complexity, and the material's properties. Knowing these techniques helps our customers make the right choice for their projects.
Casting Method | Advantages | Ideal Applications |
---|---|---|
Sand Casting |
|
|
Die Casting |
|
|
Permanent Mold Casting |
|
|
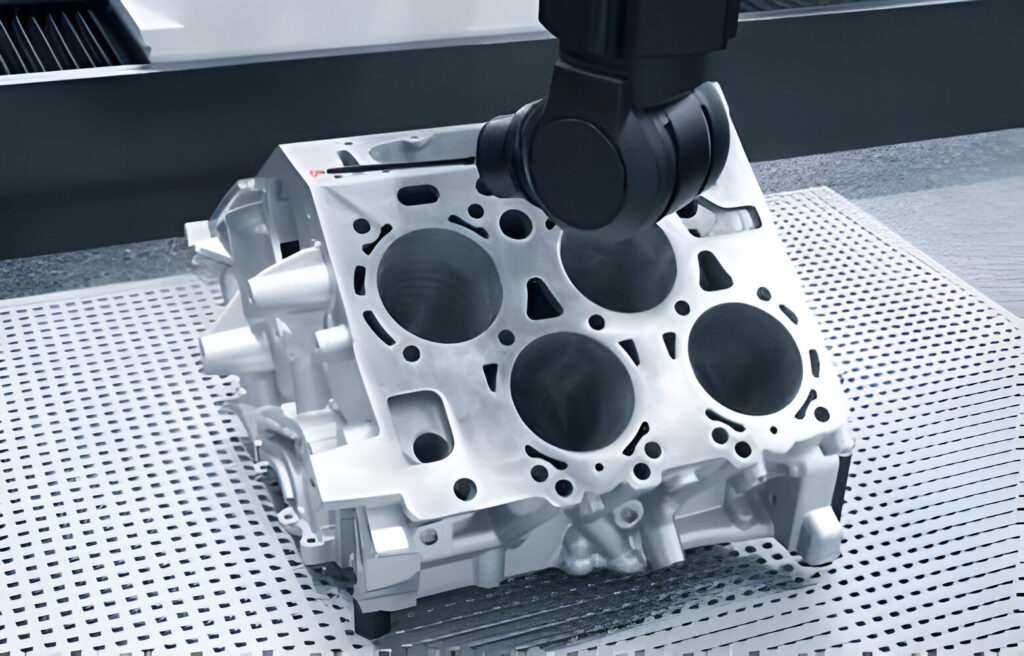
Whether you're in the culinary, aerospace, automotive, or any other industry. We offer custom aluminum casting solutions tailored to your needs. Our expertise in die casting, permanent mold casting, and sand casting ensures quality and performance for your aluminum components.
KT--Casting
Bring Your Designs to Reality– Experience Custom Perfection with On-Demand Casting!
Custom Aluminum Casting Services
At KT-Foundry, we know how crucial custom aluminum casting is for many industries. Whether you're in automotive, aerospace, or construction, our skills in design, alloy choice, and small batch production can make your ideas real.
Key Considerations for Custom Casting
Designing custom aluminum parts requires careful thought. Our team looks at mold design, where to inject the aluminum, and part thickness. This ensures the aluminum flows well and parts come out easily. For complex designs, we might use more than one injection point to avoid solidifying too soon.
Choosing the right alloy is key in custom aluminum casting. We have many options like A380, A390, A360, and A413, each for different needs. Our metallurgists help pick the perfect alloy for your project.
Casting Method | Advantages | Disadvantages |
---|---|---|
Sand Casting | - Lowest relative cost - Versatile for various part sizes | - Lower dimensional accuracy - Slower production rates |
Die Casting | - Highest production rate - Excellent surface finish | - Higher tooling costs - Limited to smaller part sizes |
Permanent Mold Casting | - High structural density - Tight dimensional tolerances | - Higher tooling costs - Limited to specific alloys |
At KT-Foundry, our experts are committed to providing custom aluminum casting solutions. We focus on mold design and alloy selection, using our deep industry knowledge. This ensures top-notch results for your custom aluminum parts project.
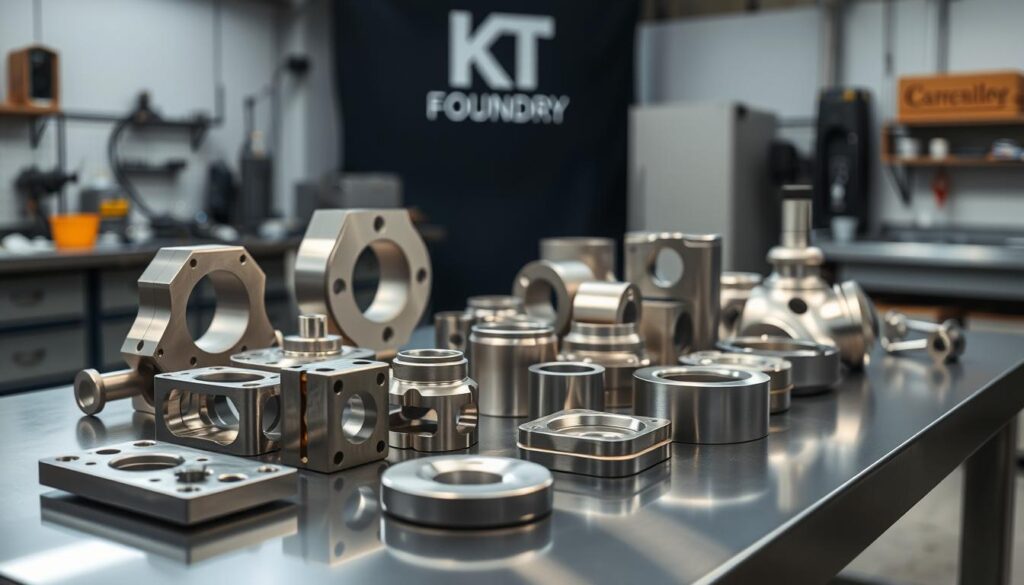
Case Study: Custom Automotive Component for Global Client
The automotive world uses lightweight aluminum castings to boost fuel efficiency and performance. A top global car maker asked KT-Foundry to make a special aluminum part for a new car. The part needed to be light, strong, and meet specific performance goals.
Project Overview
A global automotive client approached KT-FOUNDRY to produce a lightweight yet durable component for their latest electric vehicle model. The part required tight tolerances, excellent surface finish, and high corrosion resistance.
Our Solution
- Technique Used: High-pressure die casting.
- Material: A356 aluminum alloy for its strength-to-weight ratio.
- Outcome: Delivered 10,000 units within 6 weeks, meeting all design and performance specifications.
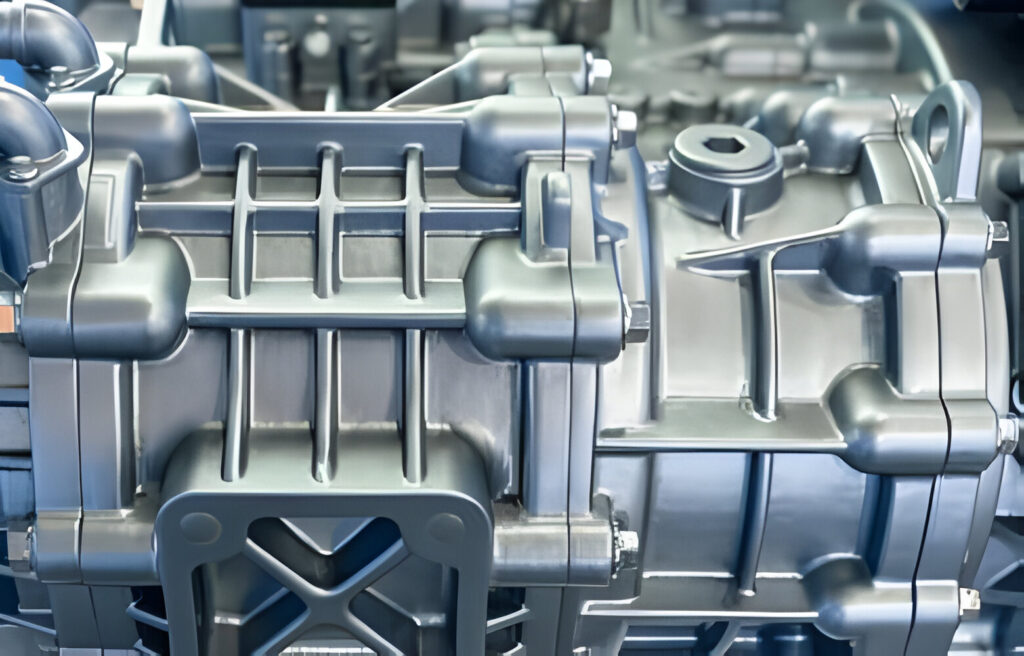
"KT-Foundry's die casting expertise and commitment to quality were instrumental in delivering a custom automotive component that exceeded our performance expectations."
Metric | Details |
---|---|
Batch Size | 10,000 units |
Delivery Time | 6 weeks |
Defect Rate | < 0.5% |
This successful project highlights our commitment to quality and precision. Read more about our custom casting solutions.
Conclusion
Aluminum casting has changed the game for many industries. It's light yet strong, and can make complex shapes with great finishes. This makes it a top choice for car, plane, medical, and consumer goods makers.
The aluminum casting market is set to grow fast. KT-Foundry is leading the way with innovative solutions and top-notch custom casting. They understand the changing needs of the industry and aim to deliver the best products and services.
Aluminum casting's flexibility and KT-Foundry's expertise mean it will keep shaping the future of making things. We'll see even more amazing uses of aluminum casting as we go on.
What is aluminum casting?
Aluminum casting is a manufacturing process where molten aluminum is poured into a mold to create various shapes and parts. This process allows for the production of complex geometries and high-quality cast aluminum components. The aluminum casting process can be executed through several casting methods, including die casting, sand cast, and investment casting, each with its own unique characteristics and advantages.
What are the different types of aluminum casting processes?
There are several types of aluminum casting processes, including:
- Die casting: A high-pressure process that produces precise and complex shapes.
- Sand casting: Involves creating a mold from sand and is suitable for larger parts.
- Investment casting: Also known as lost-wax casting, it is used for intricate designs.
- Permanent mold casting: Uses reusable molds and is ideal for high-volume production.
- Lost foam casting: Involves creating a mold from foam, which is vaporized when molten aluminum is poured.
Each of these methods has its own specific applications and benefits, making them suitable for different applications of cast aluminum.
What are the benefits of aluminum casting?
Aluminum casting offers several advantages, including:
- Lightweight: Aluminum is significantly lighter than other metals like cast iron, making it ideal for applications where weight is a concern.
- Corrosion resistance: Aluminum naturally forms a protective oxide layer, which enhances its durability.
- High strength-to-weight ratio: This means that cast aluminum parts can maintain strength while being lightweight.
- Versatility: The ability to create complex shapes and finishes makes it suitable for various industries, including automotive and aerospace.
KT--Casting
Bring Your Designs to Reality– Experience Custom Perfection with On-Demand Casting!