Aluminum and stainless steel are two metal alloys with their own strengths and weaknesses. The casting process is key in making these metals into complex shapes. It's a way to create shapes that are hard or expensive to make otherwise.
Knowing the unique qualities of these metals is crucial. It helps in choosing the right material for your casting needs. This is important in various fields like industry, business, and aerospace.
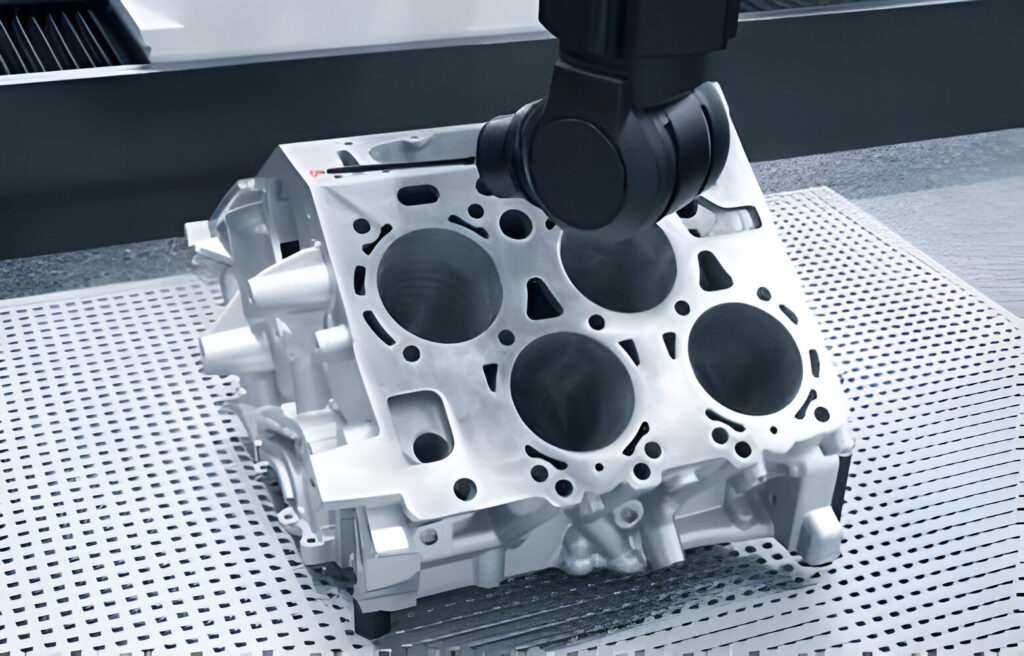
In this detailed comparison, we dive into the differences between aluminum and stainless steel castings. We look at their physical properties, how they perform, their costs, and their environmental impact. Our goal is to help you decide which material is best for your project.
Overview of aluminum and stainless steel castings
Aluminum and stainless steel castings are used in many industries. Aluminum is light, resists corrosion well, and is affordable. Stainless steel is strong, lasts long, and can handle high heat.
The casting process has been around for thousands of years. It's used to make many things, like tools and jewelry. The choice of casting method depends on the material and project needs.
Property | Aluminum | Stainless Steel |
---|---|---|
Heat Resistance | Up to 400°F (204°C) | Up to 2500°F (1371°C) |
Strength-to-Weight Ratio | normal | Good |
Corrosion Resistance | Good | Excellent |
Cost | Lower | Higher |
Aluminum and stainless steel castings are used in many fields. They are found in aerospace, cars, construction, and healthcare. Knowing their properties helps choose the right material for a project.
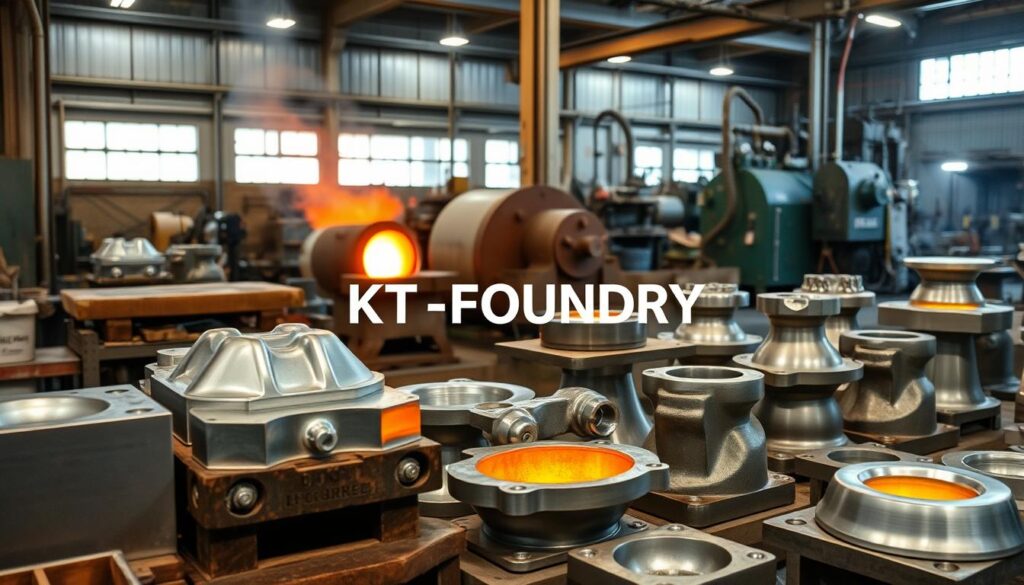
Choosing between aluminum and stainless steel depends on the project's needs. Aluminum is light and resists corrosion. Stainless steel is strong and can handle high heat. By understanding these, professionals can make better choices.
Aluminum Castings: Pros and Cons
Aluminum castings are a great choice for many industries. They are light yet strong, resist corrosion well, and save money. But, they also have some downsides to think about before choosing them.
Advantages: Lightweight, Corrosion-Resistant, and Cost-Effective
Aluminum alloys are very light. They are about one-third the weight of stainless steel. This makes them perfect for cars and planes where weight matters a lot.
They also don't rust easily, which is great for places that are wet or moist. This means they last longer and don't need to be replaced often. Plus, they cost less than stainless steel, especially when making lots of them.
Limitations: Lower Strength, Potential Deformation Under High Loads
Aluminum castings have some big downsides too. They are not as strong as stainless steel. This makes them not good for places that need to hold a lot of weight or stress.
They can also bend under heavy loads, which can hurt their performance. When deciding between aluminum and stainless steel, think about what your project needs. Talking to experts can help you make the best choice.
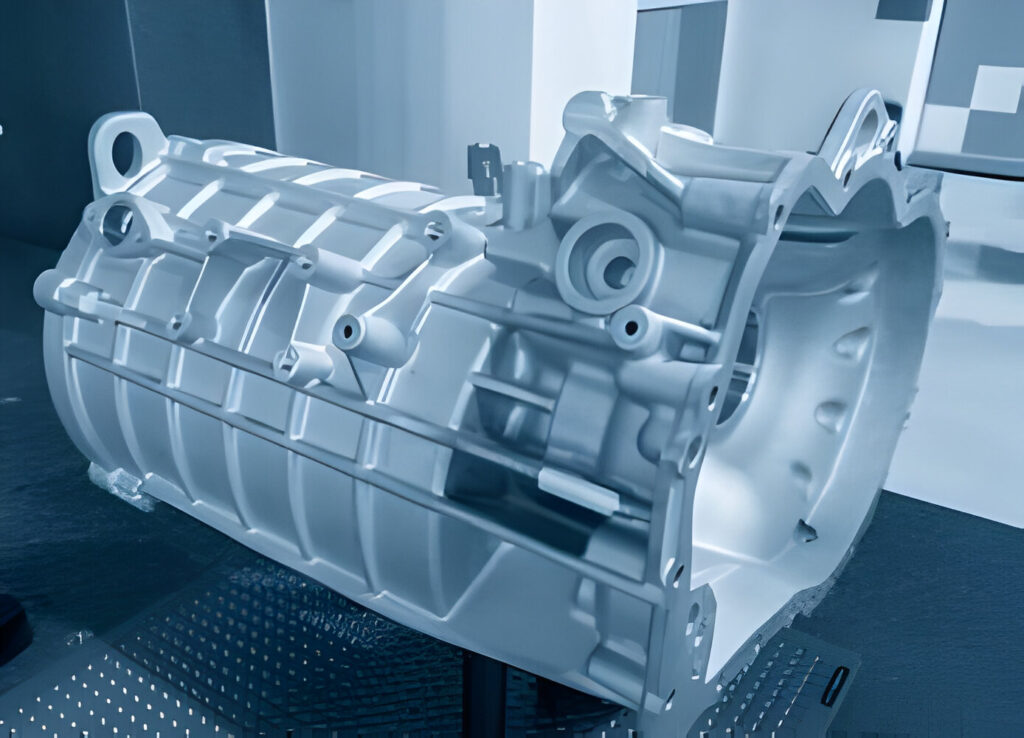
"Aluminum castings offer a compelling combination of advantages that make them a popular choice across various industries."
Stainless Steel Castings: Pros and Cons
Stainless steel castings are top-notch for high-performance needs. They have great durability, resist corrosion well, and handle heat. They are stronger than aluminum, making them a favorite in many fields.
Advantages of Stainless Steel Castings
- High Strength: Stainless steel's chromium content gives it top-notch tensile strength. It can handle heavy loads and stress without losing its shape.
- Excellent Corrosion Resistance: The chromium oxide layer on stainless steel's surface protects it from corrosion. It works well even in tough environments.
- Heat Resistant: Stainless steel keeps its strength up to 900 degrees Fahrenheit. This makes it great for jobs that need to handle high temperatures.
Limitations of Stainless Steel Castings
- Heavier Weight: Stainless steel castings are much heavier than aluminum. This can be a problem when you need to save on weight.
- Higher Cost: Making stainless steel castings costs more than aluminum. This is because of the complex processes and higher material prices.
- Complex Machining: Stainless steel is hard to machine because of its hardness and resistance to bending. It needs special tools and skilled workers.
Even with their downsides, stainless steel castings have big pluses. They are strong, durable, resistant to corrosion, and good for high-temperature jobs. This makes them a great pick for many industries.
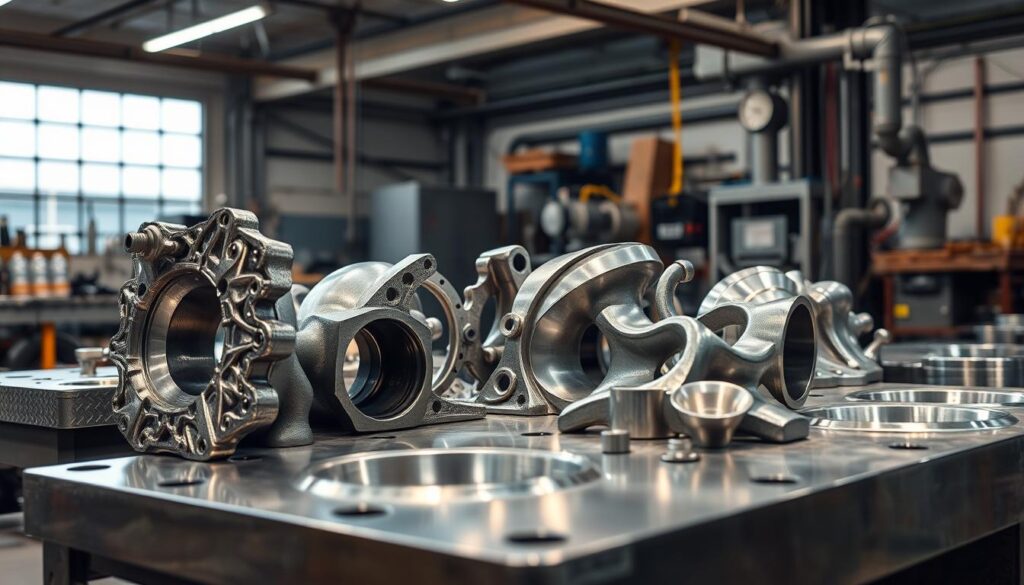
"Stainless steel castings offer unparalleled strength and corrosion resistance, making them a preferred choice for high-performance applications."
Material Characteristics: A Head-to-Head Comparison
Choosing the right material for motor casings is key. We need to understand the physical properties and performance of aluminum and stainless steel. Let's compare them based on material properties, conductivity, wear resistance, heat resistance, and mechanical stress.
Physical Properties: Weight, Strength, and Ductility
Aluminum is lighter, with a density of 2.7 g/cm³ compared to stainless steel's 7.9 to 8.0 g/cm³. This makes aluminum great for reducing weight, like in the automotive industry. But, stainless steel is stronger, with tensile strength from 520 to 1,100 MPa. Aluminum's strength is lower, ranging from 90 to 570 MPa.
Stainless steel also has higher yield strength. This means it can handle more mechanical stress without deforming permanently.
Thermal and Electrical Conductivity
Aluminum is excellent at conducting heat, with a range of 205 to 235 W/mK. Stainless steel's heat conductivity is much lower, between 15 to 25 W/mK. Aluminum's ability to transfer heat makes it perfect for electric motor casings.
Resistance to Wear, Heat, and Corrosion
Stainless steel can handle high temperatures better, up to 750-1,550°C. Aluminum starts to soften at around 400°F (204°C). Both materials resist corrosion well, but stainless steel performs better in harsh conditions.
Aluminum has a protective oxide layer, which helps it resist corrosion. This makes it a good choice for many applications.
Durability under Mechanical Stress
Stainless steel is stronger and more rigid, making it ideal for applications needing high durability. Aluminum is more flexible but can deform under heavy loads. However, its strength-to-weight ratio is still beneficial in some cases.
Property | Aluminum | Stainless Steel |
---|---|---|
Density (g/cm³) | 2.7 | 7.9 - 8.0 |
Tensile Strength (MPa) | 90 - 570 | 520 - 1,100 |
Thermal Conductivity (W/mK) | 205 - 235 | 15 - 25 |
Heat Resistance (°C) | Up to 204 | 750 - 1,550 |
Corrosion Resistance | Good to Excellent | Excellent |
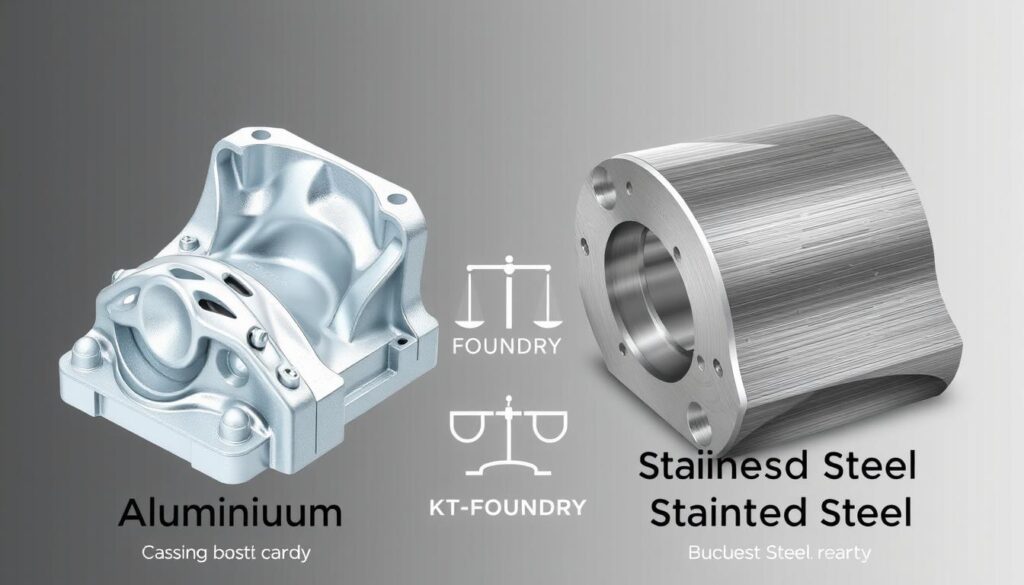
Case Study: Switching from Stainless Steel to Aluminum Castings – Balancing Cost and Performance
A client in the consumer equipment industry relied on stainless steel castings for their product housings. While durable and resistant to rust, the high cost of stainless steel significantly impacted their profit margins. After consulting with KT-FOUNDRY, the client agreed to switch to aluminum castings.
Results
- Cost Reduction: Aluminum castings reduced the price to 35% of the stainless steel cost, making it a more budget-friendly solution.
- Trade-offs: While aluminum is lighter and cheaper, it is less durable, more prone to dents, and less heat-resistant compared to stainless steel. For this application, however, the reduced durability was acceptable.
Key Insight
This case highlights the trade-off between cost and performance:
- Aluminum: Cost-effective, lightweight, but less durable and heat-resistant.
- Stainless Steel: More expensive, but highly durable, rust-resistant, and capable of withstanding higher temperatures.
Choosing the right material depends on the specific requirements of your application. Learn more about material selection at KT-FOUNDRY by visiting our casting solutions page.
Conclusion
Choosing between aluminum and stainless steel castings depends on your project's needs. Aluminum is best for projects that need to be light, conduct heat well, and save money. Stainless steel is better for projects that need to be strong, resist corrosion, and handle high temperatures.
Recap of Major Differences
Aluminum is great for products in wet or humid places because it doesn't rust easily. But stainless steel is stronger, making it better for heavy-duty tasks. Aluminum is also easier to work with because it melts at a lower temperature and casts more easily.
Guidance on Making an Optimal Choice
When picking between aluminum and stainless steel, think about weight, strength, and how they resist corrosion. Also, consider their heat properties and cost. Talk to the experts at KT-FOUNDRY to find the best material for your project.
They can help you choose based on your project's needs, like how long it will last, how much maintenance it needs, and if it's good for the environment. Knowing what each material can do will help you make a smart choice for your project.