Ball mill liners are key in the mining world. They protect the mill and make grinding more efficient. Companies use top-notch materials like rubber, steel, and new composite solutions. These are made to fit each mine's needs.
Choosing the right liner maker is important. You need to look at their skills, product quality, and if they follow industry rules.
We aim to give our clients the best ball mill liner options. Our long experience and knowledge of mining challenges help us. We make products that last longer, work better, and use less energy.

We're always exploring new materials and designs, like 3D scanning for liners. Our green practices, like using recycled materials, make our solutions better for the planet. This way, we help the mining industry be more sustainable.
Understanding Ball Mill Liners: Purpose and Function
Ball mill liners are key to the grinding mill's success. They protect the mill and boost grinding efficiency. These parts are vital for the mill's performance.
Protection Against Wear and Tear
Ball mill liners shield the mill's inside from grinding media and material impact. They are made of tough materials like steel, rubber, or ceramic. This helps them last longer in harsh conditions.
Enhanced Grinding Efficiency
Liners also improve grinding efficiency. They help the grinding media move better, making the mill more efficient. This means less energy use and better grinding results.
Types of Liner Materials
The right liner material depends on the grinding task. Steel liners work well with hard ores, while rubber is better for softer materials. Ceramic liners are top for their abrasion resistance and grinding efficiency. Choosing the right liner materials is key for the mill's best performance.
Liner Material | Typical Applications | Advantages |
---|---|---|
Steel | Processing of harder ores and minerals | High durability, abrasion resistance |
Rubber | Softer material processing, secondary grinding | Lower weight, quieter operation, improved impact resistance |
Ceramic | Demanding applications requiring optimal grinding efficiency | Exceptional abrasion resistance, enhanced grinding media movement |
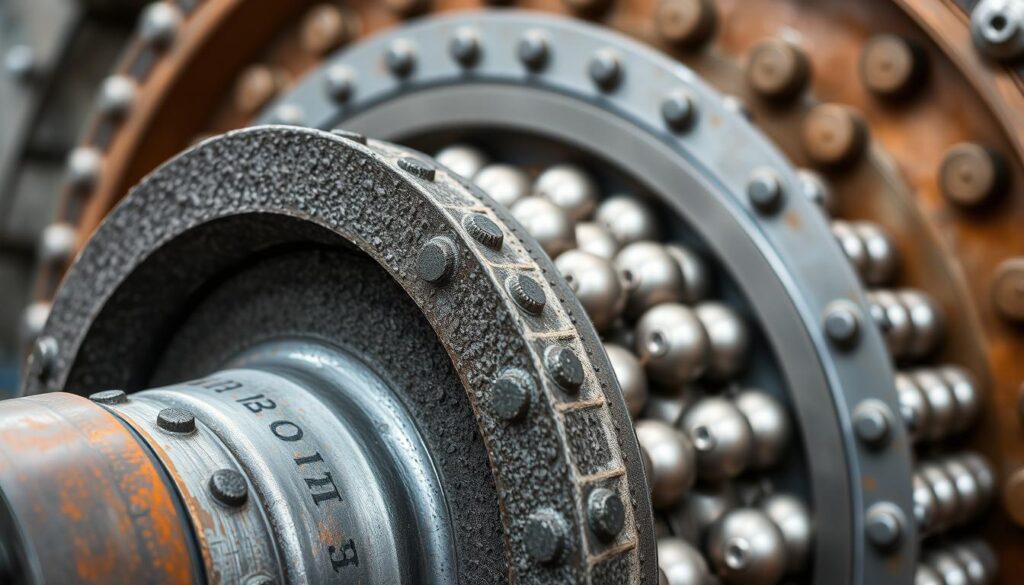
"Ball mill liners are the unsung heroes of the grinding process, protecting the mill's integrity while maximizing efficiency and productivity."
Key Ball Mill Liners Manufacturers and Their Solutions
KT-FOUNDRY is known for its high-quality ball mill liners. They are made to handle tough mining environments.
这些领先的制造商深知定制和特定应用设计在采矿业中的价值。他们根据每台磨机的独特需求量身定制解决方案。这确保了客户的最佳性能、更长的使用寿命和更高的生产力。
These leading manufacturers know the value of
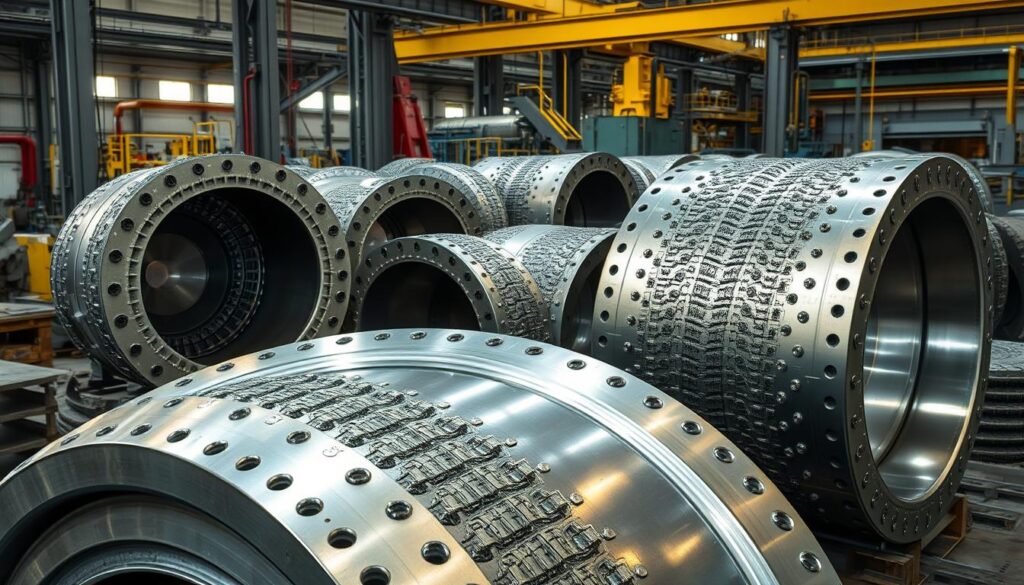
Design and Material Innovations in Mill Liner Technology
The mining and mineral processing industries are changing fast. There's a big need for better and greener mill liner tech. To meet this, makers are using new designs and materials to make their products last longer and work better.
Advanced Composite Materials
Composite liners, like FLSmidth's PulpMax, mix rubber's toughness with metal's strength. This makes a top-notch lining option. These materials help mills last longer and grind more efficiently.
Customization and Application-Specific Designs
Thanks to 3D scanning technology, makers can now make liners that fit each mill perfectly. This customization means better performance, safety, and less upkeep for the mill.
Sustainable Manufacturing Practices
With a focus on being green, makers are using recycled materials in liners. This cuts down on waste and saves resources. It also makes making liners more energy efficient.
New liner designs, like wave blocks and uni-directional liners, make maintenance easier. They also help the milling process run better and are kinder to the environment.
"We are committed to developing composite liners that offer unparalleled performance and durability, while also prioritizing sustainable manufacturing practices that minimize our carbon footprint."
Installation and Maintenance Best Practices
Proper installation and careful maintenance are key to the best performance of ball mill liners. Our experts suggest a detailed approach to protect your investment and keep grinding efficiency high.
Careful Installation
The first step is to check the mill shell for any damage or issues. Then, place the liner carefully and tighten the bolts as the manufacturer suggests. This ensures a secure fit and helps avoid early wear.
Regular Inspections and Cleaning
- Regular checks for wear, damage, or buildup are vital. They help spot problems early and fix them quickly.
- Keeping the mill clean is also crucial. Regular cleaning prevents material buildup and extends liner life.
Safety-Conscious Liner Replacement
When liners need to be replaced, safety comes first. Always shut down the mill and disconnect power before starting. Our team stresses following all safety guidelines to protect people and ensure a smooth replacement.
Composite liners are designed for faster, safer installation. They reduce downtime and boost production efficiency.
Focus on proper liner installation, follow maintenance procedures, and use strong safety measures and inspection routines. This way, you can get the most out of your ball mill and keep it running well for a long time.
"Careful attention to the installation and maintenance of ball mill liners is crucial for optimizing grinding efficiency and extending the useful life of this critical equipment."
Conclusion
Choosing the right ball mill liner is key to better grinding. We need to think about the material (rubber, metallic, or composite), the mill size, and what the application needs. The right liner can make our mills work better, last longer, and need less downtime.
New materials and designs are making liners work even better. They also help us use resources more wisely.
The right ball mill liner can really help our mining work run smoothly. It boosts how well we process minerals and makes our operations more profitable. By picking the best liner, we can make our mining and processing better.
The market for ball mill liners is growing. This is because more mines want to process ore efficiently and more projects are starting up worldwide. Keeping up with new liner tech and best practices is important. It helps us stay ahead and keep our operations strong.
FAQ
What are ball mill liners and why are they important?
Ball mill liners are protective coverings that line the interior of a ball mill. Their primary function is to provide protection against wear and tear while facilitating optimal grinding performance. By minimizing the impact of grinding media on the mill shell, these liners enhance the grinding efficiency and extend the overall lifespan of the ball mill. The right mill lining solution can significantly influence the throughput and performance characteristics of the grinding mill.
What materials are commonly used for mill liners?
Mill liners can be made from various materials, including steel, rubber, and composite materials. Steel mill liners are known for their durability and strength, making them suitable for high-impact applications. Rubber liners are often used for their flexibility and ability to absorb vibrations, enhancing grinding efficiency. Composite liners combine the benefits of both materials, offering protection against wear and tear while optimizing grind conditions.
How do I choose the right mill liner solution for my application?
Selecting the right mill liner solution involves considering several factors, including the type of mill (e.g., ag or sag mills), the material being processed, and the desired grinding efficiency. A thorough understanding of your operating conditions and the nature of the grinding media will help you choose a mill liner that optimizes performance and extends its wear life. Consulting with manufacturers can provide valuable insights into the best options available.
What are the benefits of using high-quality mill liners?
Using high-quality mill liners ensures enhanced performance of your ball mill. They provide better protection against wear and tear, which can reduce maintenance costs and downtime. Additionally, high-quality liners improve the grinding efficiency by maintaining optimal contact with the grinding media, leading to increased throughput and overall productivity. Investing in quality liners is essential for achieving