In the world of mineral processing, ball mill liners play a crucial role in enhancing milling performance and ensuring efficient grinding operations. At KT-ball mill liners, we specialize in delivering innovative and durable solutions designed to meet the evolving needs of the industry. Whether you're dealing with steel, rubber, or composite materials, understanding the differences in liner designs is essential for optimizing your milling processes.
Modern mill liners are not just about durability; they're about combining robust materials with advanced engineering to maximize productivity. From simple cast options to complex rubber composite liners, the design evolution has been remarkable. At KT-ball mill liners, we are committed to innovation, ensuring our products align with your long-term goals and reduce downtime.
Understanding Ball Mill Liners and Their Applications
In mineral processing, mill liners are essential for protecting the mill shell and ensuring efficient grinding. At KT-ball mill liners, we focus on creating durable solutions that enhance milling performance.
Function and Importance in Milling Operations
The primary role of mill liners is to protect the mill shell from wear and tear while supporting optimal grinding action. They prevent pulp racing and ensure proper charge movement and energy transfer. This design helps reduce wear patterns and boosts mill performance by balancing the load.
How We Enhance Lifespan and Efficiency
We engineer our liners to improve grinding efficiency and reduce unplanned downtime. By mitigating abrasive impacts during grinding operations, we extend the lifespan of our liners. Our designs align with industry best practices, ensuring a balanced load and reducing wear patterns.
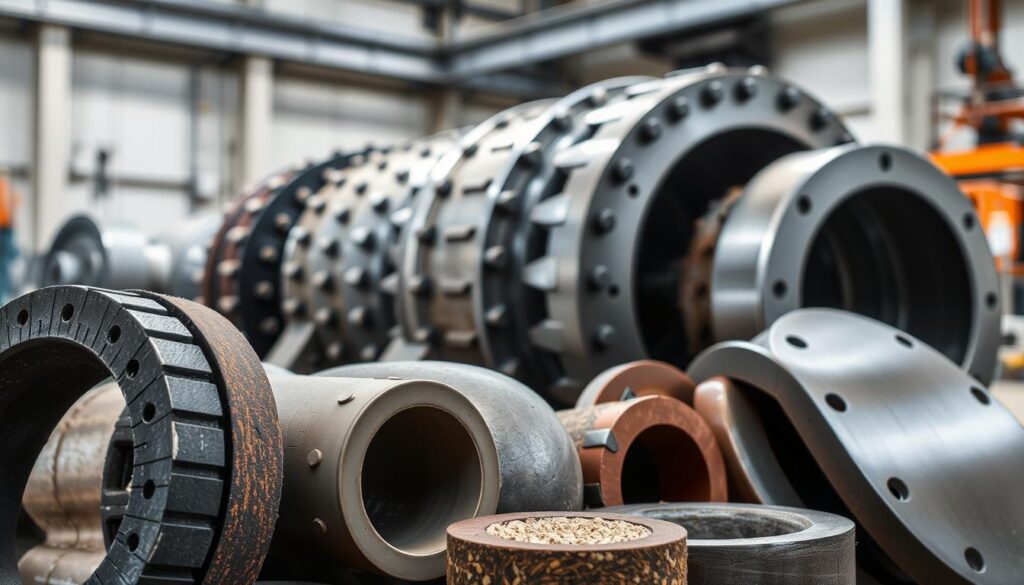
Proper liner design is crucial for maximizing efficiency. Our solutions are based on real-world performance data, ensuring they meet the evolving needs of the industry. By focusing on functional excellence and innovation, we help our clients achieve optimal milling performance.
Exploring Materials and Design Options for Mill Liners
In the realm of mineral processing, the selection of materials and designs for mill liners is pivotal for optimizing grinding operations. At KT-ball mill liners, we pride ourselves on offering a diverse range of high-quality materials, each engineered to withstand the rigors of various grinding environments.
Steel, Rubber, and Composite Materials
When it comes to mill liners, the choice of material is crucial. Steel remains a popular option due to its durability and impact resistance. Manganese steel, in particular, is favored for its exceptional wear resistance in harsh milling conditions. On the other hand, rubber liners are gaining traction for their ability to reduce noise and provide better impact absorption, especially in applications where noise reduction is a priority.
Composite materials offer a balanced approach, combining the strength of steel with the resilience of rubber. These materials are designed to enhance durability while maintaining flexibility, making them ideal for operations that require a mix of robustness and adaptability.
Design Variations for Different Grinding Needs
The design of mill liners plays a significant role in their performance. Thicker plates and the strategic placement of lifter bars can significantly enhance the efficiency of grinding operations. These design elements ensure proper charge movement and energy transfer, leading to improved productivity and reduced wear patterns.
Additionally, design variations such as stepped liners and wave types are implemented to cater to specific processing requirements. These designs are tailored to optimize particle size distribution and energy consumption, ensuring that each operation achieves the desired outcomes efficiently.
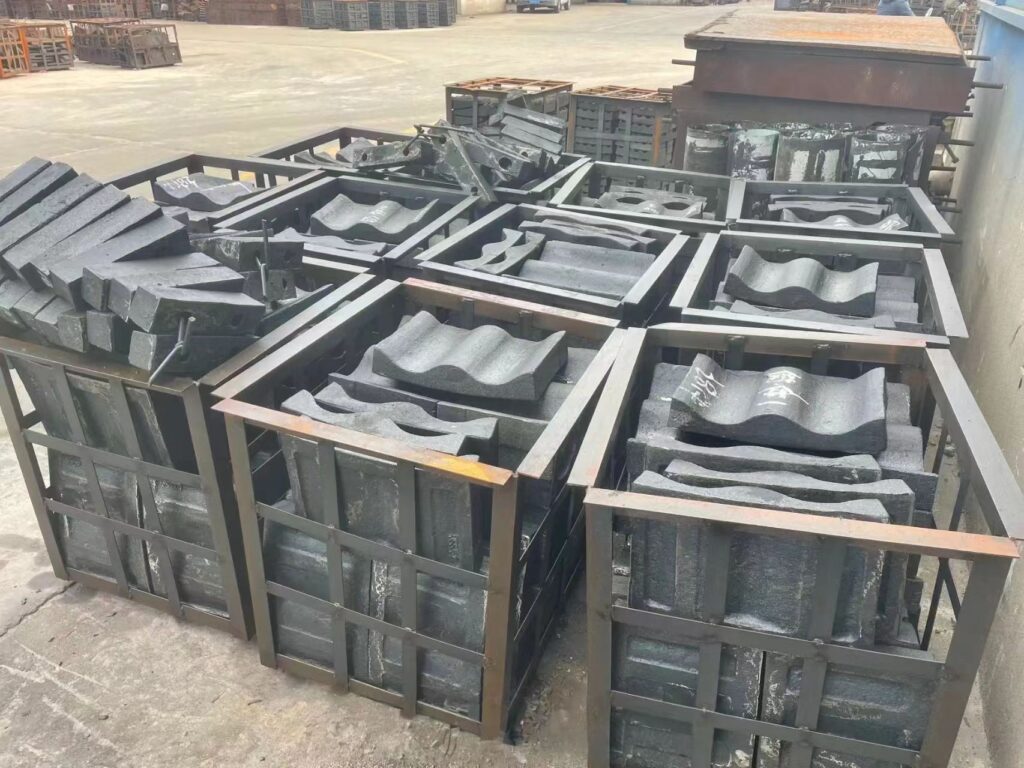
By focusing on quality materials and innovative designs, we help our clients achieve consistent grinding performance while minimizing maintenance frequency. Our solutions are backed by real-world performance data, ensuring they meet the evolving needs of the industry.
Types of Ball Mill Liners: Examining Variations and Innovations
Our expertise at KT-ball mill liners allows us to differentiate between various liner types and develop innovative solutions that address specific operational needs in modern milling. The selection of appropriate liner types is critical for achieving optimal milling performance.
Lifter Liners Versus Smooth Liners
Lifter liners feature raised bars that promote efficient ball movement, enhancing grinding efficiency. In contrast, smooth liners are ideal for delicate materials, reducing wear and tear. The choice between these types significantly impacts slurry flow, energy consumption, and discharge efficiency.
Advanced Designs for Optimized Grinding Performance
Advanced liner designs, such as composite materials, combine the strength of steel with the resilience of rubber, offering improved wear properties. These innovations enhance operational performance and energy efficiency, ensuring reliable and high-quality solutions tailored to diverse customer needs.
Optimizing Performance Through Installation and Maintenance
At KT-ball mill liners, we recognize that precise installation and proactive maintenance are essential for achieving peak performance and extending the life of your equipment. Drawing on insights from industry leaders like Metso and Multotec, we've developed a comprehensive approach to ensure optimal results.
Installation Techniques and Best Practices
Proper alignment and secure fastening of liners and head plates are critical. Misalignment can increase wear by up to 20%, while correct installation enhances efficiency and safety. Our solutions are designed to ensure the mill remains balanced, operating at peak levels and reducing noise.
Monitoring Wear and Enhancing Milling Efficiency
Regular monitoring of wear patterns allows for proactive maintenance, extending liner life and reducing downtime. By recording performance data, we can identify potential issues early, preventing unexpected stoppages and optimizing wear levels.
Installation Aspect | Best Practices | Benefits |
---|---|---|
Alignment | Ensure proper alignment to prevent wear | Reduces wear by up to 20% |
Fastening | Secure liners and head plates | Enhances efficiency and safety |
Monitoring | Regular inspections and data recording | Extends equipment life, reduces downtime |
By focusing on these strategies, we help our clients achieve consistent performance while minimizing maintenance needs. Our solutions are backed by real-world data, ensuring they meet industry demands effectively.
Bringing It All Together for Successful Milling Operations
At KT-ball mill liners, we bring together our expertise to deliver comprehensive solutions tailored to every operational requirement, ensuring successful milling operations from start to finish. Our approach integrates lifecycle service models and technical optimizations to enhance grinding efficiency and overall mill performance.
Selecting the right liner design and material is crucial for specific milling operations. Proper installation, maintenance, and consistent monitoring are key to improving performance and reducing downtime. Factors like manganese content and end-of-life criteria are vital for product selection and operational planning.
Understanding your mill’s performance requirements is essential for choosing the optimal liner strategy. We emphasize our commitment to research, innovation, and service excellence in every project. Consider KT-ball mill liners as your strategic partner for long-term success in milling operations.