At KT-FOUNDRY, we know how important ball mill shell liners are. They greatly affect how well the grinding process works. The quality and design of these liners change how grinding media moves inside the mill.
This, in turn, impacts the grinding efficiency. We aim to make shell linings that fit each mill perfectly. Our goal is to boost grinding efficiency, cut down on wear, and make our clients' equipment last longer.
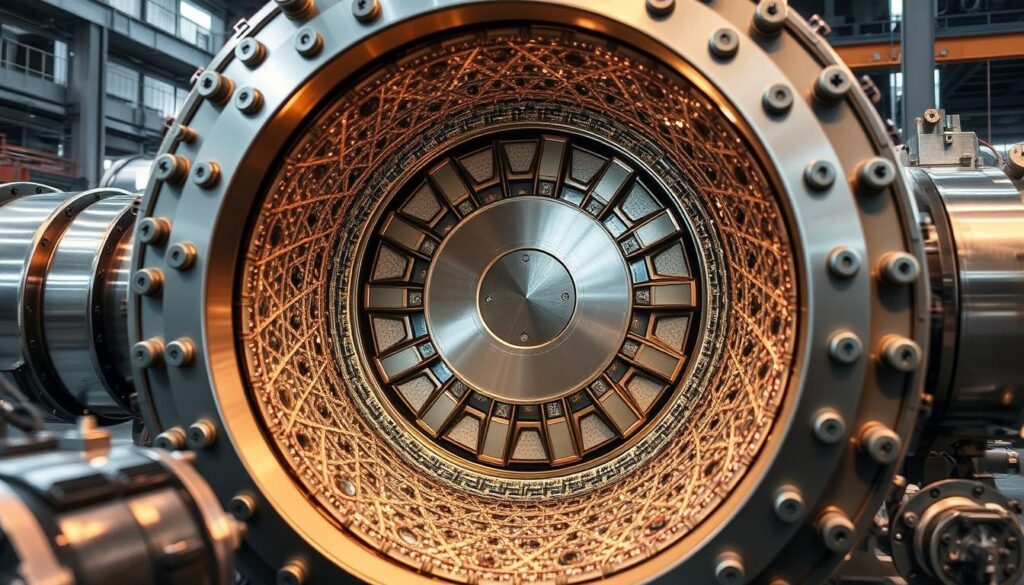
Our team uses the latest in material science and engineering to improve our liners. We think about things like how well they resist wear, how they handle impact, and how they spread out grinding media. Our goal is to make the milling process better and help our mining partners save money.
Understanding Ball Mill Shell Liners: Core Functions and Benefits
Ball mill shell liners are key to making grinding operations more efficient and lasting longer. They have many important roles that help increase productivity and save costs.
Protection Against Wear and Impact
The main job of ball mill shell liners is to protect the mill's inside from the wear and tear of grinding. They act as a shield, taking the impact resistance of the grinding media. This helps prevent damage to the mill shell, saving on maintenance costs and keeping the mill running smoothly.
Role in Grinding Efficiency
Good liners help the grinding process by making the grinding media move better and use energy more efficiently. This leads to better operating conditions and mill uptime, boosting plant productivity and efficiency.
Cost-Effective Operations
Choosing and installing the right ball mill shell liners can save costs in several ways. They help reduce downtime, lower energy use, and boost plant productivity. This all adds up to a healthier bottom line.
Knowing how ball mill shell liners work can help operators get the most out of their grinding operations. It leads to better efficiency, longer equipment life, and a more affordable production process.
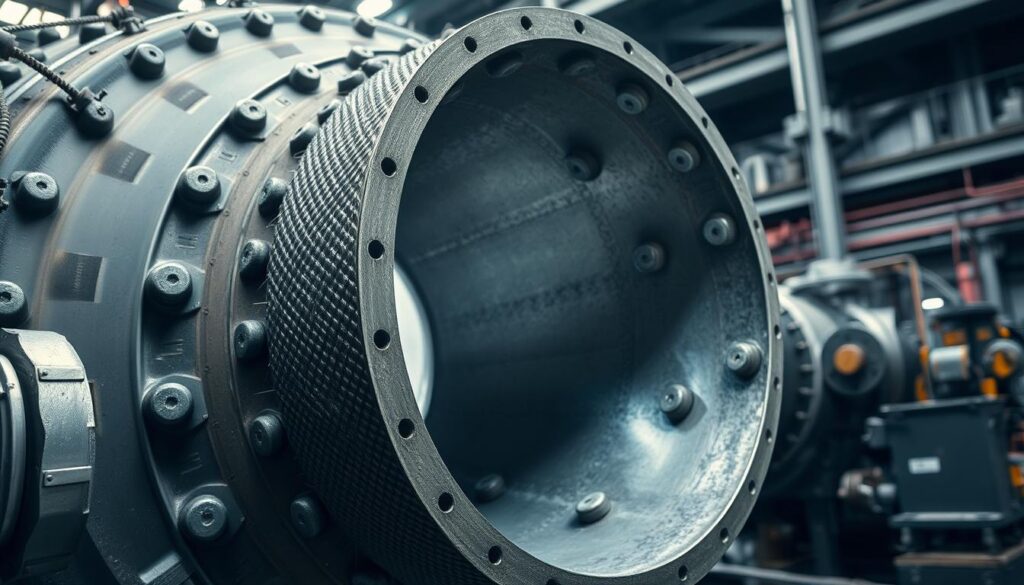
Innovative Liner Designs for Enhanced Performance
At KT-FOUNDRY, we create innovative liner designs to boost industrial grinding mill performance. Our activator lining systems lift grinding balls up with little slip. This ensures they hit with maximum impact in the first grinding area. This boosts the efficiency of the initial coarse grinding.
In the second grinding area, our classifying liner technology sorts the ball charge by size. This makes finer grinding more efficient. This focused grinding process improves the mill's overall performance.
Our compact spiral solutions mix activator plates with plow plates. Together, they optimize ball load movement and energy transfer in mono-chamber mills or long second grinding areas. This design enhances the grinding process's effectiveness.
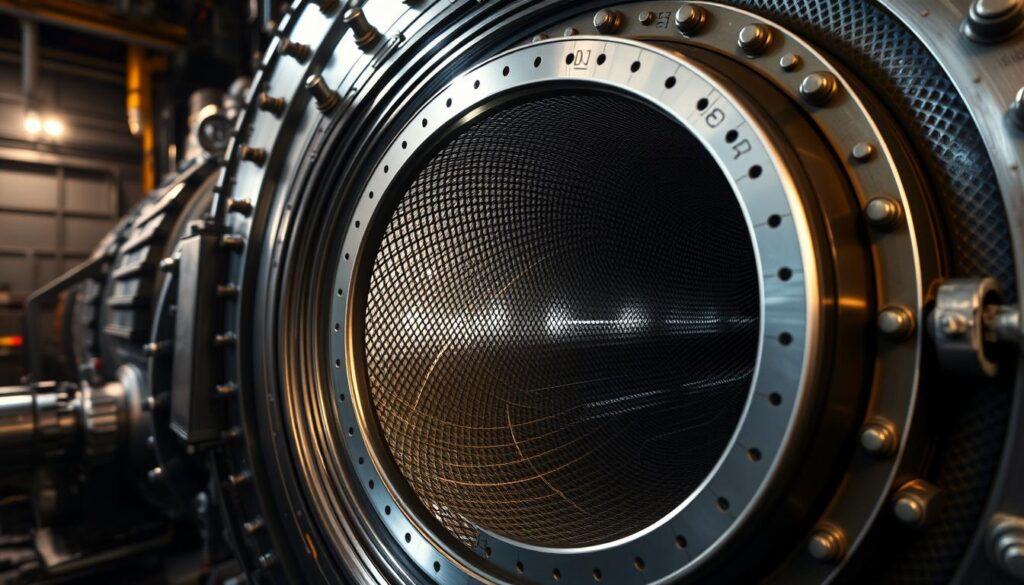
By using these advanced liner technologies, we help our customers get the most out of their grinding mills. This leads to better productivity and cost savings.
Material Selection and Manufacturing Excellence at KT-FOUNDRY
At KT-FOUNDRY, we take pride in our focus on material selection and manufacturing. Our liners are made from top-notch, wear-resistant materials. They're designed to handle tough industrial tasks. We offer a variety of liners, from durable steel to resilient rubber and composite options.
Our advanced manufacturing ensures each liner meets high standards. We use cutting-edge methods to make liners that last long and work well. Whether you need steel for mining or rubber for abrasive environments, we aim to boost your productivity and save costs.
Material | Key Features | Applications |
---|---|---|
Steel Liners |
| Mining, mineral processing, cement production |
Rubber Liners |
| Aggregate processing, coal preparation, recycling |
Composite Liners |
| Chemicals, pharmaceuticals, food processing |
At KT-FOUNDRY, we aim to lead in liner technology. We invest in research and development to bring you innovative solutions. Our goal is to improve your ball mill performance and increase your productivity.
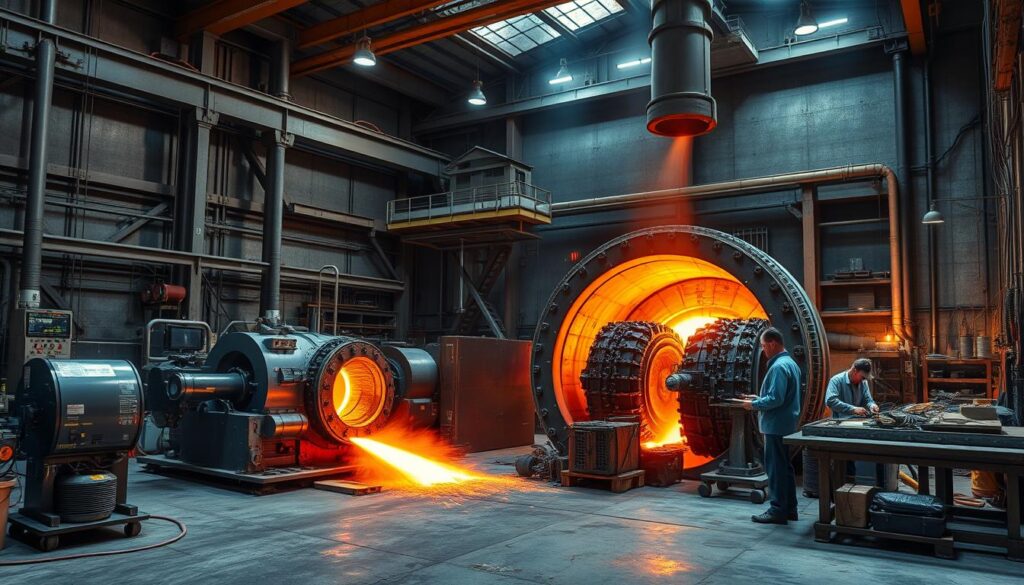
"Our commitment to material excellence and manufacturing expertise is the foundation upon which we build lasting partnerships with our clients."
See the KT-FOUNDRY difference for yourself. Discover how our high-quality, wear-resistant liners can change your operations.
Revolutionary Ball Mill Shell Liners: Impact on Grinding Efficiency
At KT-FOUNDRY, we've created ball mill shell liners that boost grinding efficiency. They improve how grinding media moves, leading to better energy use and smaller particles. Our liners, with special shapes and lifter bars, cut down energy use and boost grinding power.
Dynamic Movement Optimization
Our liners are made to help the grinding media move right. This design cuts down on slipping and boosts energy transfer. The lifter bars and liner shape work together to make the grinding media's impact more effective.
Energy Transfer Enhancement
Our liners are shaped to pass more energy to the grinding media. This means better grinding efficiency and less energy consumption for the same particle size reduction. The liners' design helps the grinding media move in ways that use energy more efficiently.
Grinding Media Distribution
Our liners are key in making sure the grinding media moves right. The lifter bars help create the right impact patterns in the mill. This leads to better grinding efficiency and makes the most of the mill's space.
"The integration of wear rates measured by changes in liner profile over time and laser-based thickness gauging technology can assist in establishing a more efficient liner profile."
KT-FOUNDRY has made big strides in ball mill technology. Our liners improve movement, energy use, and media distribution. This means better productivity, energy savings, and overall efficiency for our customers.
Optimizing Mill Performance Through Advanced Liner Profiles
At KT-FOUNDRY, we know how important advanced liner profiles are for mill performance. Our liner designs balance mill capacity and grinding efficiency well. This ensures the best energy usage in the milling process.
Our liners are designed to improve material flow and grinding media movement. This makes the grinding process more effective. Also, our liners help reduce noise, making the work environment safer and more comfortable.
We use the latest software and tools to create innovative liners. These liners use impact, attrition, and abrasion to improve grinding. This way, we increase mill throughput and lower maintenance needs.
For example, our shell lifter designs follow specific ratios for the best grinding action. In autogenous mills, a certain lifter spacing can greatly improve grinding.
We understand the unique needs of different mills, like SAG, rod, and ball mills. We choose the right liner materials and designs for each mill. This ensures our clients' mills work efficiently every day.
"The success of a milling operation is heavily dependent on the design and performance of the mill liners. KT-FOUNDRY's advanced liner profiles have consistently delivered unparalleled results for our clients, driving significant improvements in grinding efficiency, energy efficiency, and overall mill capacity."
KT-FOUNDRY is a leader in mill liner innovation. We use our expertise and advanced tools to create custom solutions. These solutions help our clients get the most out of their milling operations.
Installation and Maintenance Best Practices
At KT-FOUNDRY, we focus on helping with ball mill shell liner installation and upkeep. Our skilled engineers ensure safe and quick setups, following strict safety rules. We help plan maintenance to cut downtime and extend liner life.
Professional Installation Procedures
The base of grinding mills must be strong, at least 1½ times the mill's weight and media. This prevents settling and misalignments, saving on maintenance costs. Concrete bases for big machines like ball mills need a solid slab with extra support under the bearings.
Our foundation plans include all the details for the concrete base. This includes space for grouting, steel, bolts, and pipes. It's important to follow these plans closely. Also, make sure to tighten the liner bolts as the manufacturer suggests.
Maintenance Scheduling
Regular upkeep can make liners last longer and improve mill performance. Our advanced wear monitoring systems give us real-time info on liner health. This helps us plan maintenance and replace liners when needed.
Wear Monitoring Systems
Our wear monitoring systems give us insights into liner condition. This lets us do maintenance on time and avoid unexpected stops. By watching wear patterns, we help our clients get the most from their liners.
Getting help from pros is wise if you're not sure about installing liners. Checking the liners ensures they're aligned and bolted right for smooth mill operation. After installing, a test run at low speed is key. This helps catch any issues before running at full speed.
"Regular maintenance can extend the lifespan of liners and improve the mill's efficiency."
Maximizing ROI with Strategic Liner Selection
At KT-FOUNDRY, we know picking the right liner is key to getting the most from your investment. We look at many things like mill size, how fast it spins, and what your ore is like. This helps us make sure your mill works well and doesn't cost too much.
Working with our team means you get liners made just for your mill. We use the latest tech like Finite Element Analysis (FEA) and Discrete Element Modeling (DEM). This helps us make liners that work better and last longer.
Studies have shown new tools and accurate liner wear checks can really boost mill performance and save money. For example, a 20% drop in power use was seen in a Hicom mill. This happened when DEM was used to predict liner wear and make changes during its life.
Key Factors for Maximizing ROI | Benefits |
---|---|
Optimized Liner Design | Increased mill availability, longer liner lifetimes, and decreased scrap metal content |
Precision Liner Wear Monitoring | Improved mill performance and economics |
Innovative Liner Materials | Enhanced impact wear protection and reduced maintenance costs |
With our help in choosing liners and our advanced tech, you can boost your ROI. This means your mineral processing operations will run at their best.
"The discrete element method (DEM) has been successful in predicting the power draw and load behavior in mills, aiding in the design of milling equipment and particle breakage prediction."
Conclusion
At KT-FOUNDRY, we're all about changing the ball mill shell liner game. We use top-notch designs and manufacturing skills. Our advanced liners make grinding more efficient, cut costs, and make mills last longer in mining and ore processing.
We focus on the latest liner tech to help our clients boost their plant's output. Our deep knowledge of ball mill shell liners lets us create new, better designs. These designs improve mill performance and efficiency.
As the industry grows, KT-FOUNDRY leads the way with new ball mill shell liner tech. We work with our clients to reach new heights in grinding efficiency, energy use, and product quality. This helps them succeed in the global market for the long haul.
FAQ
What are ball mill liners and why are they important?
Ball mill liners are essential components of a ball mill that serve to protect the mill shell from wear and tear during the grinding process. They help in achieving better grinding efficiency by optimizing the motion of the grinding media within the mill. The right type of liner can significantly enhance mill capacity, reduce maintenance costs, and extend the wear life for your ball mill.
How do lifter bars contribute to grinding efficiency?
Lifter bars are a type of mill liner designed to raise the grinding media as it rotates within the mill, allowing for a more effective grinding process. Their design can influence the trajectory of the ball charge, ensuring that the grinding media is lifted to the optimal height for impact. This action not only improves grinding efficiency but also reduces the overall energy consumption of the mill.
What are the benefits of using rubber liners in ball mills?
Rubber liners offer several advantages, including being lightweight and having a high level of wear-resistant properties. They can reduce noise levels during operation and are less prone to chipping compared to traditional metal liners. Additionally, rubber liners can provide a longer wear life, which leads to reduced downtime and improved mill uptime.
What is the impact of liner wear on mill efficiency?
Liner wear can significantly affect mill efficiency by altering the motion of the grinding media and reducing the mill’s shell protection. As liners degrade, they may not provide sufficient lifting or protection, leading to increased energy consumption and potentially damaging the