In the world of metalworking, cast steel and forged steel are two different ways to make things. They have their own benefits and uses in many industries. We'll look at what makes them different, their strengths and weaknesses, and when to use each.
Casting is when molten steel is poured into molds to make complex shapes. Forging shapes solid steel by applying pressure. These methods change the steel's properties and how it's made. Knowing these differences helps us choose the right steel for our projects.
Exploring cast and forged steel, we'll see their unique qualities. This knowledge helps us make smart choices based on what we need. Let's dive into the world of steel making and find the best solution for you.
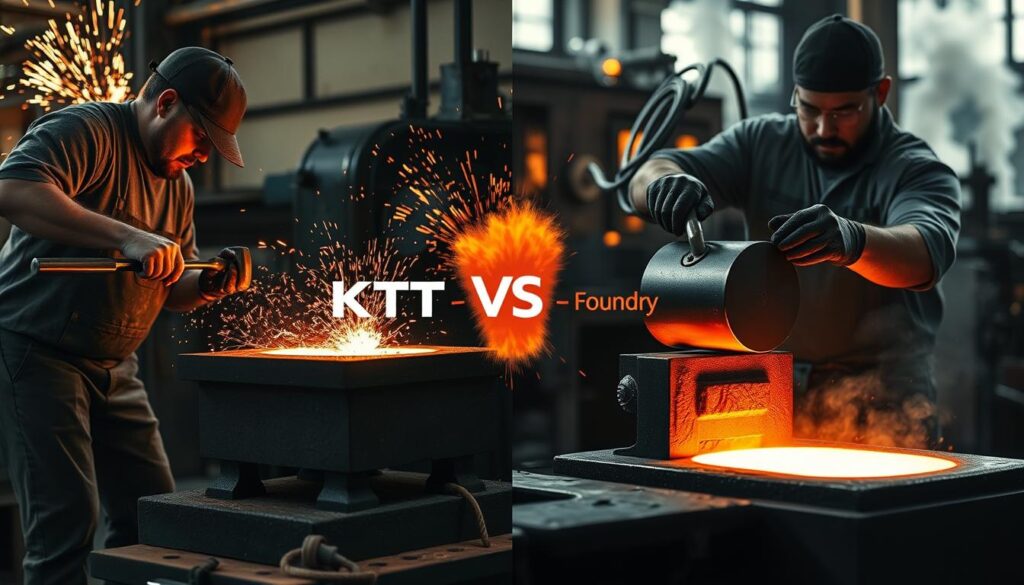
Cast Steel
Cast steel is a versatile material that combines design flexibility and alloy versatility. It's different from forged steel, which is shaped by force. Cast steel is made by pouring molten metal into molds, creating complex shapes and parts.
This process allows for new designs and materials in various industries. It's a way to explore new possibilities in product development.
Advantages of Cast Steel
- Design Flexibility: The casting process makes it easy to create parts with complex shapes and unique features. This is hard or impossible with traditional methods like machining or forging.
- Alloy Versatility: Cast steel can use many alloys, including those with high nickel and molybdenum. This lets you tailor material properties for specific needs.
- Cost-Effective Production: For small to medium production runs, cast steel is often cheaper than forged steel. This is especially true for parts with complex designs.
Limitations of Cast Steel
Cast steel has some limitations. The casting process can cause internal defects like porosity. These defects can weaken the product's strength and durability.
Cast steel might not be as strong as forged steel. This makes it less ideal for applications needing high strength and load-bearing capabilities.
Despite these drawbacks, cast steel is still popular in many industries. It's favored for its design flexibility, alloy versatility, and cost-effectiveness. This includes the automotive, marine, and aerospace sectors. By using cast steel manufacturing, engineers can create innovative products.
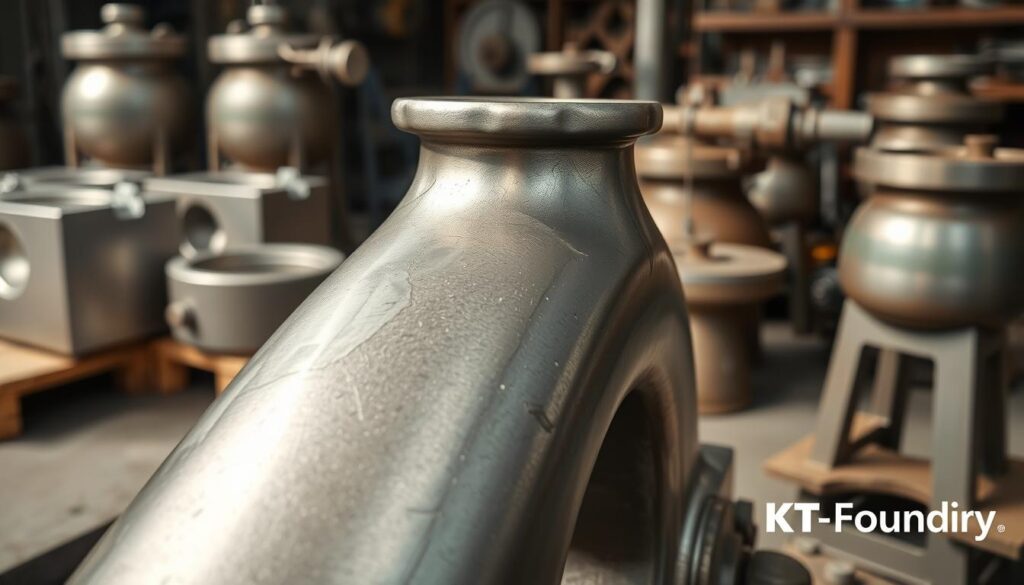
Forged Steel
Forged steel is made by shaping hot solid steel with mechanical force. It has many benefits for different industries. The forging process improves the metal's internal structure, making it stronger and more durable.
The forging process also makes steel lighter and more resistant to wear. This is why it's often used in the aerospace and automotive industries. Forged steel parts are known for their strength, toughness, and ability to withstand fatigue.
Advantages
- Increased strength and durability due to refined internal structure
- Improved grain structure and enhanced wear resistance
- Higher strength-to-weight ratio for lightweight, high-performance applications
- Preferred for high-stress industries like aerospace and automotive
Limitations
Forged steel has its downsides too. It can be more expensive to make and has size limits. Also, making complex shapes can be tricky, sometimes needing extra steps.
There are different forging methods like hot forging, closed die forging, and open die forging. The right method depends on what the part needs. It's all about finding the right balance between cost, complexity, and performance.
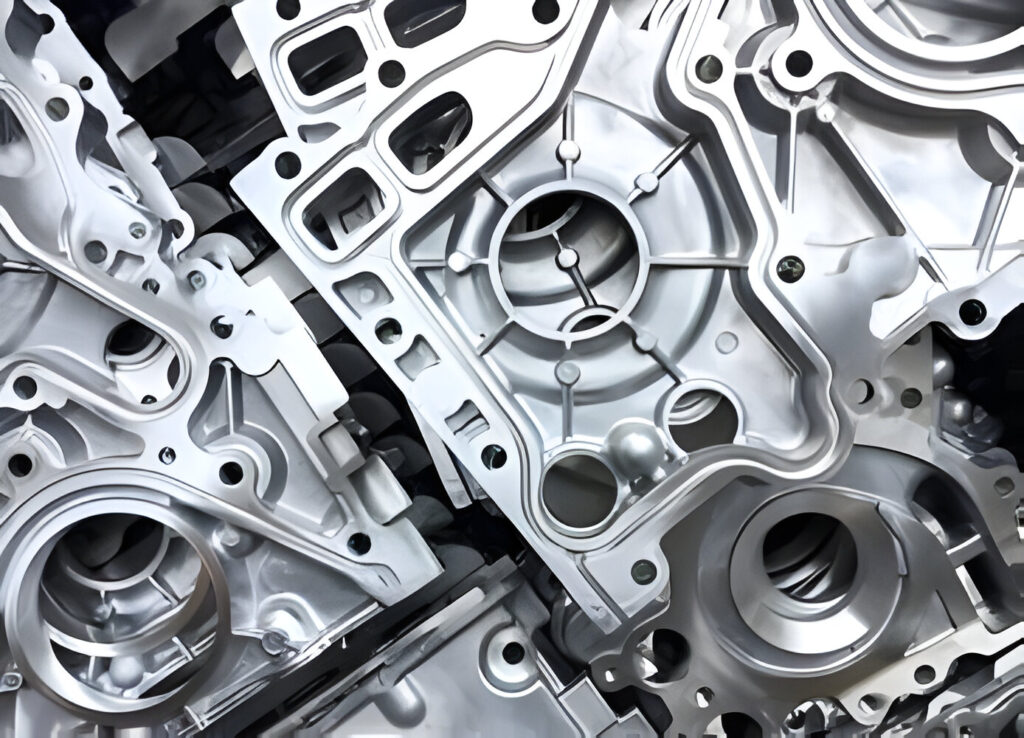
"Forged steel is the material of choice for high-stress, high-performance applications where strength, durability, and reliability are paramount."
Performance Comparison
When comparing cast steel and forged steel, several important factors come into play. Forged steel usually beats cast steel in tensile strength, fatigue resistance, and impact resistance. This is because forging creates a finer grain structure, boosting forged steel's mechanical properties. Cast steel, however, is better at making large and complex parts, with no size limits.
Strength and Durability
Forged steel parts are stronger, tougher, and better at handling impacts than cast steel. This is due to their tight grain structure and the metal's directional flow. Studies show forged parts can have up to 26% higher tensile strength and 37% higher fatigue strength than cast parts. This makes forged steel ideal for high-stress fields like aerospace and automotive.
Size and Complexity
Cast steel has its own strengths, especially in size and complexity. The casting method allows for bigger and more detailed parts. This is great for industries needing design flexibility and beauty, like medical devices and architecture.
Material Utilization
Both cast and forged steel have their own material usage benefits. Casting can be more efficient for certain designs, reducing material waste and machining needs. Forging, on the other hand, is cost-effective, with lower rejection rates and faster production times.
The choice between cast and forged steel depends on the project's needs. It's about finding the right balance between strength, size, complexity, and cost. Knowing the strengths of each process helps engineers and designers make the best choice for their projects.
KT Foundry's cast iron pump impellers combine the benefits of both cast and forged steel. They are reliable and cost-effective, making them versatile for many pumping needs.
Applications of Cast Steel and Forged Steel
Cast steel and forged steel have their own strengths. They are used in different ways in industry. Let's look at where they are most useful.
Cast Steel Applications
Cast steel is great for making big valve bodies and complex parts. It's also used in power generation, mining, and water treatment. These areas need parts with special designs.
- Large valve bodies for petrochemical industry equipment
- Machinery components for mining equipment
- Complex structural elements in architectural projects
- Automotive parts like differential covers and gear housings.
- Structural components in industries requiring high corrosion resistance.
Forged Steel Applications
Forged steel is best for high-stress jobs. It's used in aerospace, automotive, and heavy machinery. It makes parts like crankshafts, connecting rods, and high-pressure valves.
- Crankshafts for automotive and aerospace applications
- Connecting rods for high-performance engines
- High-pressure valves for industrial machinery
- High-pressure fittings in energy and petrochemical sectors.
The mining industry also uses both cast and forged steel. New casting technologies have made cast steel more like forged steel. This means we can choose the right material for each job.
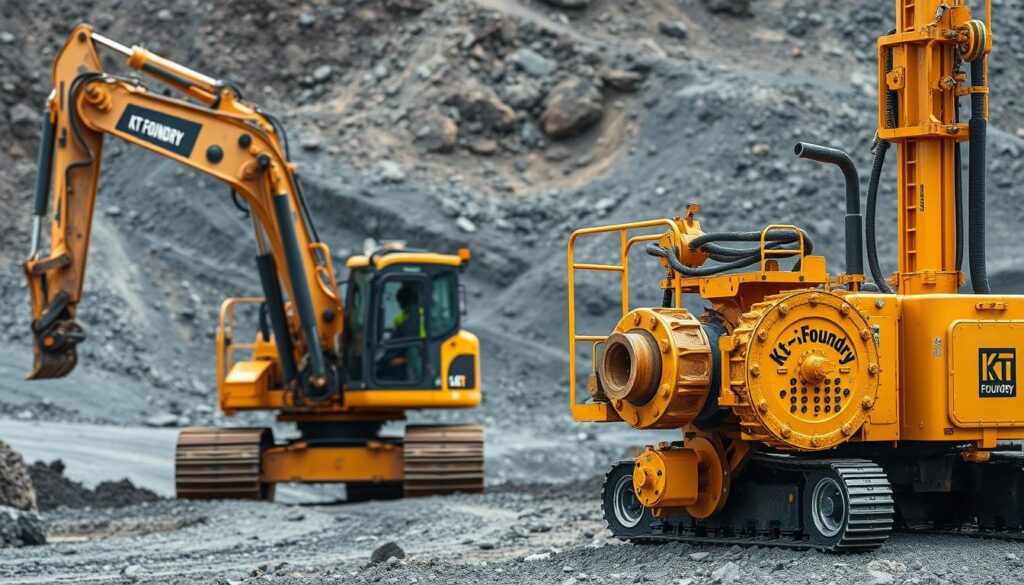
"The choice between casting and forging depends on project priorities, with casting favored for low cost, exotic alloys, and complex geometries, and forging favored for strength and structural integrity."
Case Study: KT-FOUNDRY's Expertise in Cast Steel Manufacturing
At KT-FOUNDRY, we were approached by a client in the mining sector seeking a solution for large wear-resistant pump housings. The parts required complex internal geometry to optimize fluid flow while enduring harsh operating conditions.
Challenge:
The client initially considered forged steel but faced challenges in achieving the necessary design intricacy. Forged steel's cost and lead time for prototyping were also prohibitive.
Solution:
Our team recommended cast steel, leveraging its ability to meet the design's geometric requirements without compromising durability. By using advanced simulation software, we optimized the mold design and alloy composition to enhance the component's wear resistance and mechanical performance.
Outcome:
Delivered components 25% faster than the client’s initial timeline.
Reduced costs by 30% compared to forging alternatives.
Enhanced performance with minimal post-casting machining.
For more on our capabilities in wear-resistant components, visit our industrial applications page.
Making the Right Choice
Selecting between cast steel and forged steel depends on your project’s unique requirements:
- Opt for cast steel when shape complexity, cost, or material variety are primary concerns.
- Choose forged steel for applications prioritizing strength, toughness, and fatigue resistance.
If you're unsure which material suits your needs, our experts at KT-FOUNDRY can provide guidance and tailored solutions. Learn more about our custom casting services.
"KT-FOUNDRY's cast steel manufacturing expertise and commitment to quality have been instrumental in our ability to deliver innovative solutions to our customers. Their flexibility and technical know-how are truly unmatched in the industry."
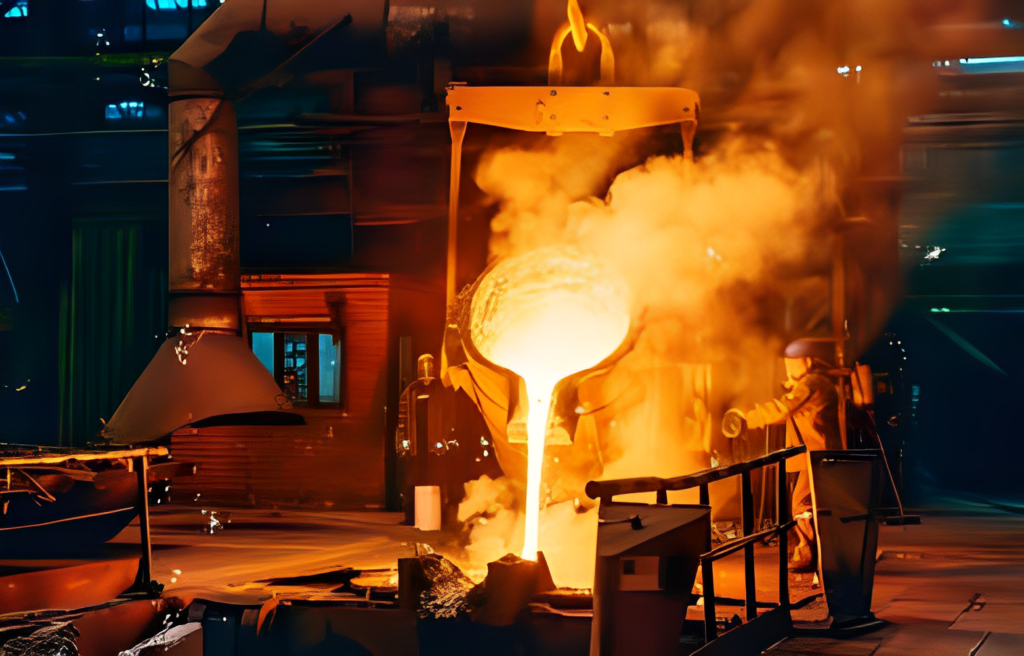
Conclusion
Choosing between cast steel and forged steel depends on what you need. Forged steel is stronger and lasts longer, perfect for tough jobs in aerospace and defense. Cast steel is better for making complex shapes and is used in things like appliances and art.
New tech has made cast steel stronger, closing the gap with forged steel in some areas. Knowing the strengths and weaknesses of each is key for picking the right material. Both types of steel are important in many fields, with new tech making them even better.
Deciding between cast and forged steel takes careful thought. You need to think about how many you'll make, the shape, the alloy, and any extra steps needed. Working with foundries and forges early on helps make sure you get the best product.
What is the main difference between casting and forging?
The primary difference between casting and forging lies in their processes. Casting is the process of pouring molten metal into a mold to create cast parts, while forging involves shaping metal through deformation under high pressure. In forging, the metal is heated and then mechanically deformed to achieve the desired shape, resulting in forged parts with improved mechanical properties, such as high strength and better ductility.
What are the advantages of forged steel over cast steel?
Forged steel typically exhibits greater strength and toughness compared to cast steel. This is due to the refined grain structure created during the forging process, which enhances the overall mechanical properties of the metal. Forged parts are less likely to contain defects such as porosity or inclusions, which can be common in casting. Additionally, forging allows for better consistency in production, making it ideal for high-performance applications.
In what applications is casting preferred over forging?
Casting is often preferred in applications where complex shapes are required or where large parts need to be produced. The casting process allows for intricate designs that would be challenging or impossible to achieve through forging. Common applications include engine blocks, pump housings, and other large components where casting is economically viable. Investment casting and sand casting are popular methods used for these types of applications.
What are the common types of forging?
There are several types of forging methods, including die forging, hot forging, and cold forging. Die forging involves the use of a mold to shape the metal under high pressure, while hot forging requires metal to be heated to a temperature where it becomes malleable. Cold forging, on the other hand, is performed at room temperature and