Custom casting is a key method in making high-quality parts and components. It's used in many fields like automotive, aerospace, and medical devices. This guide will dive into the details of custom casting, covering materials, techniques, and its uses.
Key Takeaways
- Custom casting is a flexible and versatile manufacturing process that allows for the creation of highly precise, complex parts and components.
- Custom casting utilizes a variety of materials, including metals, resins, and polymers, to meet the specific requirements of diverse industries.
- Techniques like sand casting, investment casting, and die casting are employed in custom casting to achieve the desired results.
- Custom casting offers a range of advantages, including the ability to produce cost-effective, high-quality parts, as well as the flexibility to accommodate unique design and production needs.
- Custom casting is widely used across various industries, including automotive, aerospace, medical device manufacturing, and more, due to its ability to deliver durable, efficient, and tailored solutions.
What is Custom Casting?
Custom casting is a way to make metal, resin, or polymer parts exactly as needed. It involves pouring molten material into a mold and letting it cool into the right shape. This method is great for making complex, detailed, and precise parts for many industries.
Definition and Overview
Custom casting makes parts by pouring molten material into a mold. This can be metals, resins, or polymers. It's perfect for parts with complex shapes, fine details, and tight fits that other methods can't do.
Applications of Custom Casting
- It's used in the automotive industry for engine and transmission parts, and more.
- In the aerospace industry, it's for making structural parts, turbine blades, and other critical items for planes and space.
- The medical device manufacturing uses it for implants, prosthetics, and surgical tools.
- It's also used in consumer goods and industrial equipment for a wide range of custom products.
Custom casting's flexibility lets manufacturers create high-quality, precise parts. This meets the special needs of many products, making it a key tool in production.
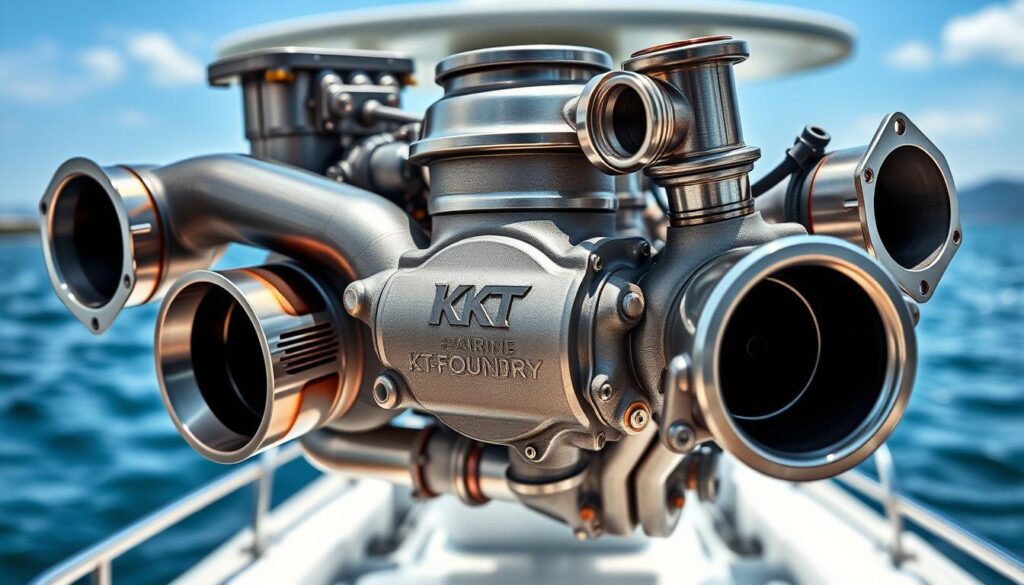
Materials for Custom Casting
Custom casting is a flexible way to make things. It uses many materials, each with special qualities. The right material depends on what the project needs, like strength or look.
Metals and Alloys
Metals and alloys are top picks for custom casting. Aluminum, steel, brass, and more are used because of their benefits. For example, iron melts at 1,538 °C (2,800 °F), perfect for casting.
Gray iron is common because it's easy to work with and wears well. Steel is great for its flexibility and strength in many fields. Stainless steel stands out for its resistance to corrosion and heat.
Aluminum and its alloys are chosen for their low melting points and resistance to corrosion. Copper and its alloys, like brass and bronze, are valued for their strength and resistance to corrosion.
Choosing the right material for custom casting is key. Manufacturers have many options to ensure the best results for each project.
Custom Casting Techniques
There are many advanced techniques for custom casting. These include sand casting and investment casting, each with its own benefits. By knowing these techniques, businesses can choose the best one to make high-quality parts that customers will love.
Sand Casting
Sand casting is a cost-effective method. It pours molten metal into a sand mold. This technique is great for making complex shapes and parts of all sizes.
It's often used in big projects. This makes it a top choice for the automotive, construction, and heavy machinery industries.
Investment Casting
Investment casting, or "lost-wax," is known for its precision. It starts with a wax pattern, then uses a ceramic mold. After the wax melts away, molten metal fills the mold, creating detailed parts.
This method is perfect for industries like aerospace, medical, and jewelry. It's all about making parts with tight tolerances and a smooth finish.
Die Casting
Die casting is great for making lots of parts quickly. It uses metal molds that can be reused. This makes it fast and efficient for producing complex shapes.
It's a favorite in the automotive, electronics, and consumer goods sectors. Its ability to make parts with little need for extra work is a big plus.
Casting Technique | Advantages | Applications |
---|---|---|
Sand Casting |
|
|
Investment Casting |
|
|
Die Casting |
|
|
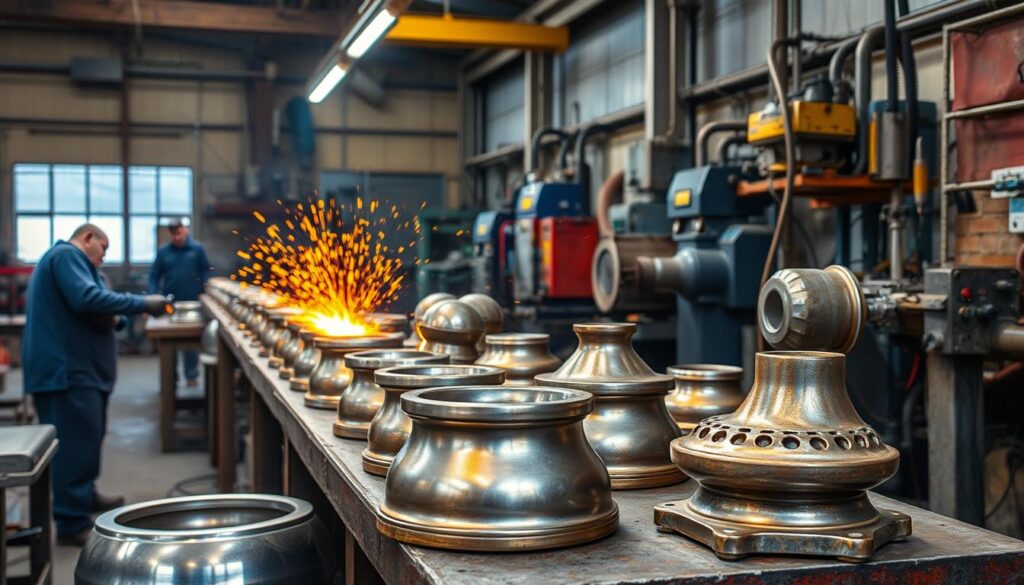
"Custom casting techniques offer manufacturers the flexibility to create unique, high-quality parts that meet the specific needs of their projects. By understanding the capabilities of each method, businesses can select the most suitable approach to deliver exceptional results."
Custom Casting Process
We're proud of our custom casting process at our foundry. It uses the latest tech and top-notch expertise. Our team helps clients through every step, making the journey smooth and quick.
The process starts with making a master pattern. This pattern is the blueprint for the final part. Then, we create a mold using advanced methods like sand or die casting.
Our skilled team then melts and pours the material into the mold. This lets it solidify and take shape.
We keep quality high by testing and inspecting at every stage. This ensures our castings meet our clients' high standards.
We're fast at making castings thanks to our advanced tools and team. We serve many industries, from aerospace to medical devices. Our range of casting methods lets us meet different needs.
Innovation is at the core of our process. We're always looking for new ways to improve quality and efficiency. This means our clients get the best solutions for their metal casting needs.
Key Steps in the Custom Casting Process |
---|
1. Pattern Creation |
2. Mold Making (Sand, Investment, or Die Casting) |
3. Melting and Pouring of Molten Material |
4. Solidification and Cooling |
5. Finishing Operations |
6. Quality Assurance Testing and Inspection |
Our custom casting capabilities let us make a wide range of high-quality metal parts. These parts meet the unique needs of our diverse clients.
"Pentz Cast Solutions can fabricate castings faster than competitors by performing multiple steps of the casting development process simultaneously."
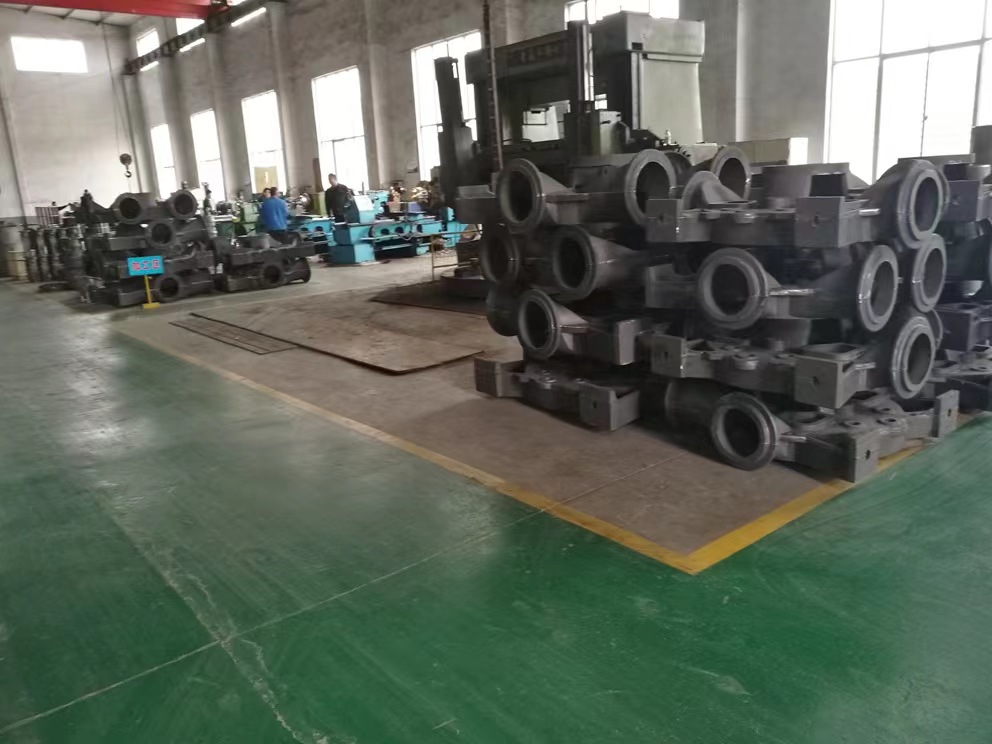
Advantages and Disadvantages of Custom Casting
Custom casting is a popular choice for many industries. It allows for the creation of complex, precise parts that meet specific needs. This method uses a variety of materials, including metals and resins, to produce parts with unique properties.
It's also cost-effective, especially for making small or large batches of parts. The ability to make design changes quickly is another big plus. This flexibility helps manufacturers keep up with changing market demands and customer needs.
Advantages of Custom Casting
- Ability to produce complex, intricate, and high-precision parts
- Versatility in material selection, including metals, alloys, resins, and polymers
- Cost-effective solutions for both low-volume and high-volume production runs
- Flexibility to accommodate design changes and customization
Disadvantages of Custom Casting
Custom casting has its downsides too. It often needs special equipment and skilled workers, which can make production slower. Also, starting up and setting up tools can cost more than other methods.
Advantages | Disadvantages |
---|---|
Ability to produce complex, intricate, and high-precision parts | Requirement for specialized equipment and skilled personnel |
Versatility in material selection, including metals, alloys, resins, and polymers | Potential for longer lead times |
Cost-effective solutions for both low-volume and high-volume production runs | Higher initial setup and tooling costs |
Flexibility to accommodate design changes and customization |
Despite these challenges, the benefits of custom casting usually outweigh the drawbacks. It's a top choice for industries looking to make high-quality, cost-effective, and customizable parts.

Quality Assurance in Custom Casting
Ensuring the quality of custom castings is crucial. These parts must meet strict performance and safety standards. At our custom casting facilities, we have a detailed quality assurance program. It checks the integrity and consistency of our cast products.
Testing and Inspection
Our quality control starts with thorough inspections and tests at different stages. We use non-destructive testing (NDT) methods like visual checks, size measurements, and mechanical tests. These help ensure the cast parts meet the required standards.
Our advanced quality control steps help us find and fix any issues early. This way, we can deliver high-quality products without any problems.
Certifications and Standards
We follow industry-leading certifications and standards, including ISO. These show our commitment to quality and consistency. Our ISO certifications highlight our strong quality management systems and dedication to quality assurance in custom casting.
By focusing on quality assurance, we provide parts that meet our customers' exact needs. Our technical skills, strict testing, and adherence to standards ensure our castings are top-notch. They meet or exceed the expectations of demanding industries.
Custom Casting Industries
Custom casting is a flexible manufacturing method for many industries. It meets the specific needs of each field. This includes the automotive, aerospace, and medical device sectors. It helps create high-quality, custom parts and components.
Automotive Industry
In the car world, custom casting makes key engine and transmission parts. These parts need to be strong, durable, and precise. This process lets car makers make complex, high-performance parts. These parts improve the car's performance and reliability.
Aerospace Industry
The space world uses custom casting for parts that are light, strong, and resistant to corrosion. These parts are for aircraft and spacecraft. It ensures the safety and performance of these products.
Medical Device Manufacturing
Medical devices also benefit from custom casting. It makes specialized implants and surgical tools. These must follow strict quality and safety rules. It allows for parts tailored to patient and healthcare needs.
Custom casting is key in these industries for its flexibility, precision, and quality. It helps manufacturers meet their market's unique demands. This keeps them competitive.
Custom Casting
At KT-FOUNDRY, we lead in custom casting services. We offer a variety of materials and techniques. Our team works with clients to meet their needs with quality castings.
KT-FOUNDRY serves industries like automotive, aerospace, and medical devices. We use advanced methods like sand, investment, and die casting. This ensures our parts are precise and durable.
We handle both small and large custom casting projects. Our modern facilities and technology guarantee high-quality parts. We aim for accuracy and consistency in every piece.
We're dedicated to quality and customer satisfaction at KT-FOUNDRY. We listen to our clients to deliver beyond their expectations. Reach out to discuss your project and get a quote. We're excited to work with you.
Custom Casting Capabilities | Materials | Applications |
---|---|---|
Sand Casting | Aluminum | Automotive |
Investment Casting | Stainless Steel | Aerospace |
Die Casting | Bronze | Medical Devices |
Precision Machining | Brass | Industrial Equipment |
Finishing and Coating | Titanium | Energy and Power |
"At KT-FOUNDRY, we are committed to providing our customers with the highest-quality custom casting solutions. Our team of experts and state-of-the-art facilities allow us to deliver unparalleled precision and reliability, no matter the project."
FAQ
What is Custom Casting?
Custom casting is a manufacturing process that involves pouring molten metal into a mold to create specific shapes and components. This process is tailored to meet the unique requirements of a project, allowing for the production of specialized parts that are not available through standard manufacturing methods. Custom metal casting enables manufacturers to produce intricate designs and complex geometries, making it an ideal choice for various industries, including automotive and aerospace.
What are the Different Types of Casting Methods?
There are several casting methods used in the industry, each suited for different applications. The most common types include:
Sand casting: Utilizes sand as a mold material, ideal for larger parts.
Die casting: Involves forcing molten metal into a mold under high pressure, suitable for high-volume production.
Investment casting: A precision method that uses a wax pattern, allowing for complex shapes and high-quality surface finishes.
Permanent mold casting: Uses a reusable mold, often made from metal, suitable for high-volume production runs.
Each method offers unique advantages depending on the metal casting needs and requirements of the casting project.
What Materials are Used in Custom Casting?
Various materials can be used in custom metal casting, including:
Alloys: Mixtures of metals that enhance specific properties such as strength or corrosion resistance.
Steel casting: Known for its strength and durability, often used in structural applications.
Aluminum: Lightweight and corrosion-resistant, ideal for automotive and aerospace applications.
Bronze: Offers excellent corrosion resistance and is often used for marine applications.
Choosing the right material is crucial for achieving the desired characteristics of the final cast metal product.
What is the Casting Process Like?
The casting process typically involves several key steps:
Designing a casting mold based on the specifications of the required part.
Preparing the mold by ensuring it is clean and free of defects.
Melting the chosen metal to create molten metal.
Pouring the molten metal into the mold to allow
Conclusion
At KT-FOUNDRY, we know how powerful and flexible custom casting is. It's great for many industries like cars, planes, and medical devices. Our experts can turn your ideas into top-notch metal parts that fit your exact needs.
We offer a wide range of materials and techniques to ensure quality. From sand to investment and die casting, we can handle tough projects. We use the latest tech to make sure your project is done right.
KT-FOUNDRY is a top choice for custom casting. We help many industries meet their production needs. Need special parts for engines or medical devices? Our team can handle big orders and make parts that impress. Reach out to us to talk about your custom casting needs. Let's work together to make your vision real.