Ductile iron and cast iron are key materials in many industries. They have unique qualities that affect project success. Choosing the right iron alloy is vital for durability, lasting value, and cost savings.
This article compares ductile iron and cast iron. It aims to help you make the best choice for your needs. The demand for these materials is growing. People want lighter, more energy-saving, and custom cast iron products.

Overview: Basic Differences Between Ductile Iron and Cast Iron
Ductile iron and cast iron are two different types of materials. Ductile iron, also known as nodular cast iron, has nodular graphite. This makes it more ductile and tough. It's made by adding magnesium to iron, creating spherical graphite.
Cast iron, on the other hand, has graphite in flake form. It's made from iron, carbon, and silicon. This makes it different from ductile iron.
Composition and Manufacturing Processes
Ductile iron has 3.2 to 3.6 percent carbon and 2.2 to 2.8 percent silicon. It also has iron and trace elements like manganese and magnesium. Gray cast iron has 2 to 4 percent carbon and a bit of silicon.
Ductile iron was introduced in the 1940s. Gray cast iron has been used for centuries. It's the most common type found in foundries.
Graphite Structure and Properties
The main difference is in their graphite structure. Ductile iron has nodules that make it stronger and more flexible. Gray iron is harder but more brittle.
Ductile iron is better at handling sudden loads. It's used in industries like agriculture and heavy truck manufacturing. Gray iron is good for vibration damping and is easy to machine.
It's used in manhole covers and park benches. Ductile iron is preferred for its strength and durability. Gray iron is chosen for its vibration damping and machinability.
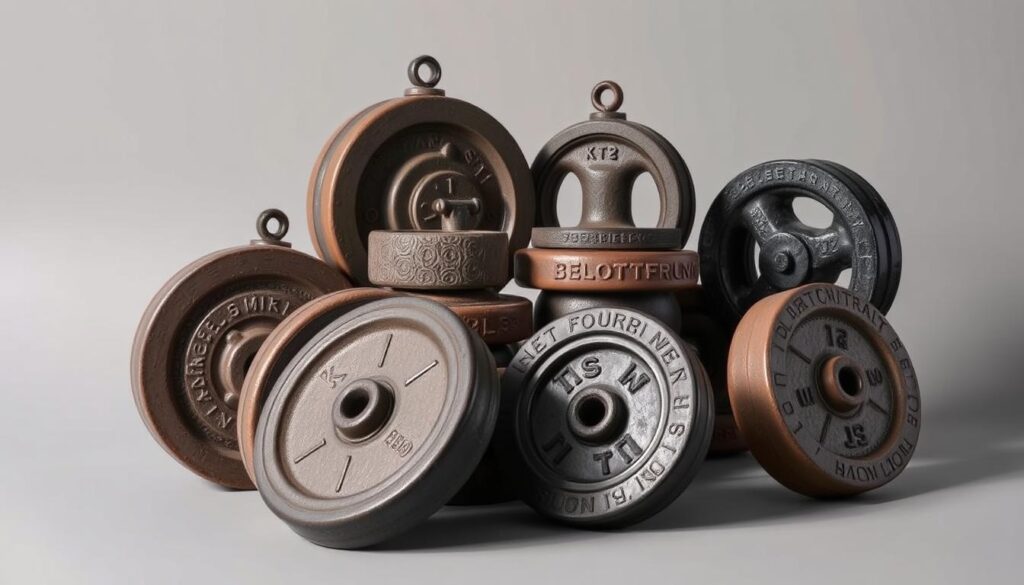
Detailed Analysis of Material Properties
Ductile iron and cast iron have different properties that make them good for certain uses. We'll look at their mechanical, chemical, and how they can be processed.
Mechanical Properties
Ductile iron has higher tensile strength and ductility than cast iron. It also has a measurable yield strength. This makes it great for things that need to be strong and tough.
Cast iron, on the other hand, is stronger under compression but is more brittle.
Chemical Properties
Ductile iron is better at resisting corrosion, especially in water and sewage. Both materials are good at resisting wear. But ductile iron's chemical makeup and structure help it fight off corrosion and oxidation better.
Processability
Cast iron is great for making complex shapes because of its excellent casting properties. Ductile iron can also be cast, but it's easier to machine. This makes it simpler to shape, cut, and finish during production.
Property | Ductile Iron | Cast Iron |
---|---|---|
Mechanical Strength | High tensile strength and impact resistance; suitable for load-bearing applications. Tensile strength typically ranges from 60,000 to 100,000 psi (414-690 MPa). | Moderate to high compressive strength but low tensile strength, which makes it prone to brittle failure under tension. Tensile strength is generally around 20,000 to 60,000 psi (138-414 MPa). |
Corrosion Resistance | Good corrosion resistance, especially in environments with water or mild chemicals, though still needs coating for more extreme conditions. | Moderate corrosion resistance, especially in wet environments. More prone to rust and may require extra protective measures like painting or coating. |
Thermal Conductivity | Lower thermal conductivity than cast iron, meaning it retains heat longer, which can be beneficial in some applications, such as engines. | High thermal conductivity, ideal for applications requiring heat dissipation, such as radiators, engine blocks, and cookware. |
Machinability | Relatively easy to machine; produces less wear on tools and allows more intricate designs. | More challenging to machine due to brittleness; machining can produce more wear on tools and can be limited in terms of complexity. |
Elasticity | Has high ductility and can bend without breaking; elongation at break often around 10-18%, which allows it to withstand dynamic and cyclic loads. | Low ductility; typically exhibits little to no elongation before breaking, making it ideal for static loads but unsuitable for dynamic stress. |
Hardness | Typically lower than cast iron, with hardness values around 170-220 Brinell, which provides better ductility but reduced abrasion resistance. | Higher hardness, generally around 180-300 Brinell, which makes it more abrasion-resistant but also more brittle. |
Density | Slightly lighter than cast iron, which can be advantageous for applications where weight is a consideration, around 7.1 g/cm³. | Heavier, with a density around 7.2-7.4 g/cm³, contributing to its use in heavy-duty applications where mass and stability are needed. |
Castability | Excellent castability, allowing for complex shapes and thin-walled sections. | Also highly castable, but brittle nature limits thin-walled sections and intricate details. |
Weldability | Moderate; can be welded but requires specific techniques and pre-heating to avoid cracking and ensure proper fusion. | Low; difficult to weld due to high carbon content, brittleness, and tendency to crack, especially in traditional gray cast iron. |
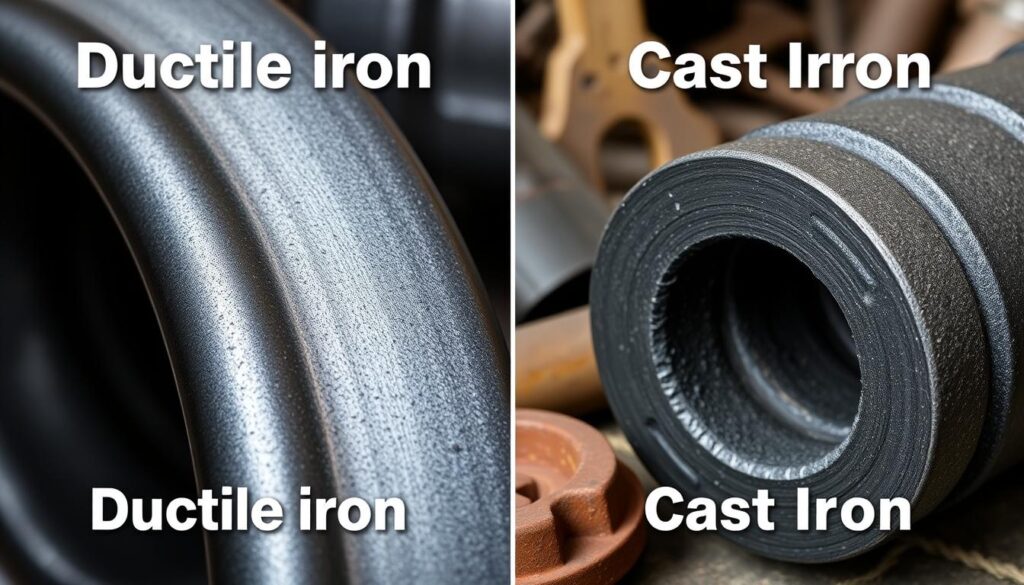
"Ductile iron can be a low-cost alternative to wrought steel products due to its elevated strength-to-weight ratio, castability, and machinability."
Advantages and Disadvantages of Ductile Iron
Ductile iron, also known as nodular cast iron, has many benefits. It is very good at withstanding impacts, better than traditional cast iron. This makes it perfect for parts that face a lot of stress and impact, like in machinery and cars.
Another great thing about ductile iron is how easy it is to machine. It can be shaped into complex parts more easily than cast iron. This is great for making custom parts and equipment where precision matters.
Ductile iron also lasts a long time and dampens vibrations well. These traits are key for things that need to work smoothly for a long time, like in water systems and vehicles.
But, ductile iron is more expensive than cast iron. The process to make it is more complex, which raises the cost. This might be a problem for projects with tight budgets.
Advantages of Ductile Iron | Disadvantages of Ductile Iron |
---|---|
|
|
Ductile iron is a great choice for many reasons, like its strength and ease of shaping. But, its higher price might limit its use in some projects. It's important to weigh the benefits against the cost.
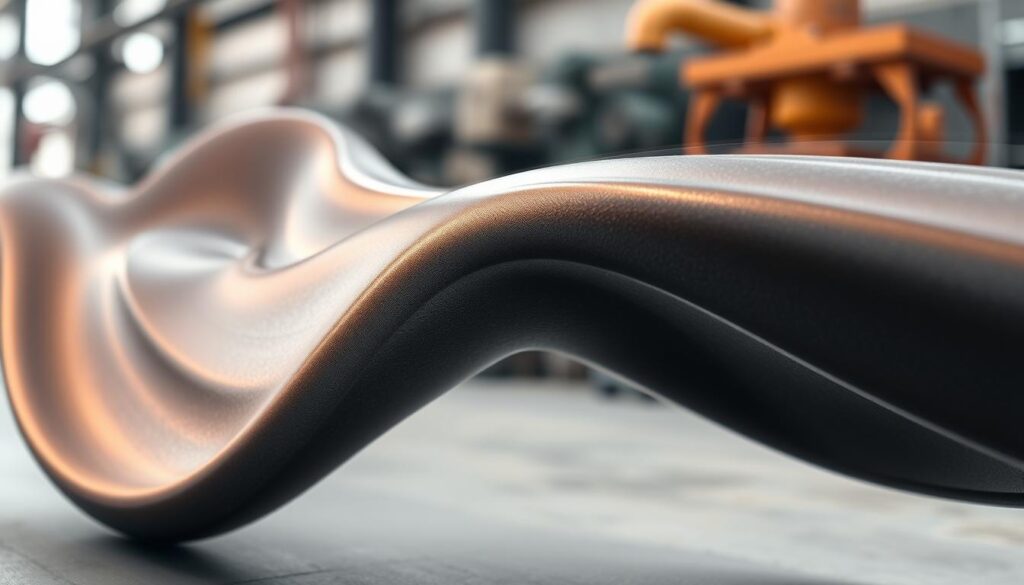
Advantages and Disadvantages of Cast Iron
Cast iron is a versatile material with many benefits. It is rigid and affordable, making it popular in many fields. It also retains heat well and conducts it efficiently, perfect for cookware and industrial gear.
Cast iron is also good at resisting wear and dampening vibrations. This is why it's used in engine blocks and machinery parts. It's also cheap to make and can be recycled, which is good for the environment. But, it can be brittle and break easily under stress or impact.
Rigidity and Cost-Effectiveness
Cast iron is great for things that need to be strong and rigid. It's used in machine tool beds, gears, rollers, and brake drums. It's also cheaper than ductile iron, which is a plus for projects that don't need super strength.
Thermal Properties and Wear Resistance
Cast iron is excellent at holding and conducting heat. This makes it perfect for cookware and industrial equipment that need to keep temperatures steady. It's also durable and absorbs vibrations well, which is why it's used in car parts like engine blocks and cylinder heads.
Cast iron pipes were once key in water and sewage systems because they resist corrosion and can handle high pressure. But, they can corrode over time, which can reduce their performance and lead to failure. So, they need to be installed, maintained, and fixed properly.
Limitations: Brittleness and Low Ductility
Despite its many benefits, cast iron has two major drawbacks. It's very brittle and doesn't bend well, which means it can crack under stress or impact. This is a big issue in some applications. Ductile iron, which is stronger and more flexible, might be a better choice in these cases.
In summary, cast iron is great for many things because of its strength, heat handling, and cost. But, its brittleness and lack of flexibility are important things to think about when choosing materials for a project.
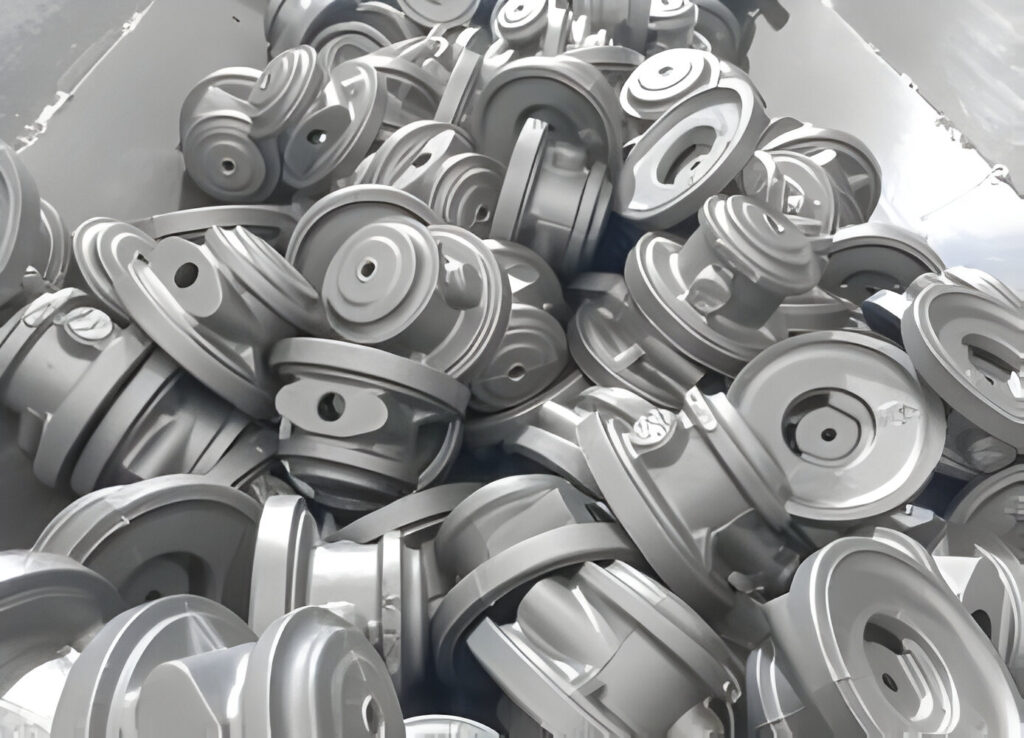
Comparison of Suitable Projects
Choosing between ductile iron and cast iron is crucial for your project. Ductile iron combines strength and flexibility, perfect for many uses. Cast iron, especially gray iron, is great for high compressive strength and managing heat well.
Ductile Iron: Versatile and Durable
Ductile iron is top-notch for projects needing strength and flexibility. It's great for water and sewage systems, car parts, and construction. It's also strong against impact and corrosion, ensuring long-lasting performance.
Cast Iron: Strength and Thermal Management
Cast iron is ideal for high strength and heat management needs. It's used in machine bases, engine blocks, and cookware. In construction, it's valued for its rigidity and ability to dampen vibrations.
Deciding between ductile iron and cast iron depends on your project's needs. Consider load-bearing, environmental, and cost factors. Knowing each material's strengths helps you choose wisely for your project's success and longevity.
"Ductile iron utility poles offer a unique combination of strength and flexibility, making them a suitable choice for areas prone to high winds or heavy snowfall."
Conclusion: Balancing Material Properties and Cost
Choosing between ductile iron and cast iron depends on several factors. Ductile iron is strong, flexible, and can handle impacts well. It's more expensive but perfect for projects needing durability and flexibility. Cast iron, on the other hand, is cheaper and great for projects needing high strength and good heat management.
Ductile iron is often chosen for water systems and car parts because of its excellent performance. In building and industrial equipment, the choice depends on the project's needs. It's important to focus on long-term performance and safety, even if it costs more upfront.
By considering material selection, project needs, cost, durability, and performance, we can make smart choices. This way, we can get the most out of ductile iron and cast iron in many applications.
KT-Casting
Bring Your Designs to Reality– Experience Custom Perfection with On-Demand Casting!