Flywheels are key mechanical parts that store rotational energy. They help smooth out speed changes in engines. This guide will cover the materials, design, and making of flywheel casting. We'll look at how flywheels work, why they're needed, and their operation.
We'll also talk about traditional cast iron and modern composite materials. The casting process will be explained. We'll discuss important design aspects like energy needs, moment of inertia, and geometry.
Stresses in flywheel parts will be analyzed. We'll explore their uses and benefits. Finally, we'll look at the latest in flywheel technology.
Key Takeaways
- Flywheels are essential mechanical devices used to store rotational energy and smooth out variations in shaft speed caused by fluctuating torque.
- Traditional cast iron flywheels and modern composite materials offer different advantages in terms of cost, design flexibility, and performance.
- The casting process is a crucial aspect of flywheel manufacturing, involving sand casting and other techniques.
- Key design considerations include energy requirements, moment of inertia, and geometry optimization to ensure safety and performance.
- Flywheels have a wide range of applications, from automotive and industrial machinery to aerospace and electric vehicles.
Understanding Flywheels: Function, Need, and Operation
Flywheels are key parts in machinery. They store and release mechanical energy as needed. This helps keep operations smooth, especially in engines, where they stabilize the crankshaft's speed.
The Crucial Role of Flywheels in Machinery
In engines, flywheels soak up energy when the piston fires and give it back when it doesn't. This makes the crankshaft's speed steady. They also help systems with on-and-off loads, like piston compressors, punch presses, and rock crushers, run smoothly.
Absorbing and Releasing Energy for Smooth Operation
Flywheels act as energy reservoirs. They store energy when there's too much and give it back when there's too little. This keeps the machinery running smoothly, without sudden speed changes.
Flywheel Type | Characteristics | Applications |
---|---|---|
Single-mass Flywheels | Cost-effective, simple design | Common in car engines |
Dual-mass Flywheels | More common in vehicles with manual transmission and diesel engines, reduce noise and vibration | Newer vehicles |
Billet Steel Flywheels | Made from solid steel, more robust | Heavier-duty vehicles |
High-performance Flywheels | Lightweight, strong materials for reduced inertia | Racing and high-end vehicles |
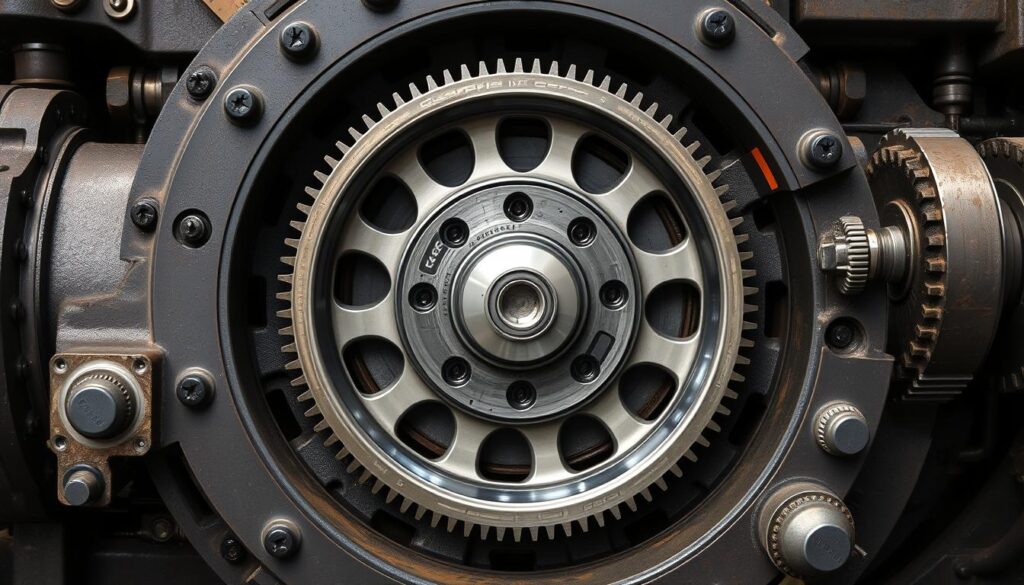
Understanding flywheels shows their vital role in machinery. They ensure smooth and reliable performance in engines and industrial gear.
Materials for Flywheel Casting
Flywheels are key in machinery, helping to absorb and release energy smoothly. Traditionally made of cast iron, they are affordable and can be shaped easily. But, cast iron is not as strong as steel, leading to the use of new materials.
Traditional Cast Iron Flywheels
Cast iron has been a top choice for flywheels because it's cheap and versatile. It can be shaped well and dampens vibrations, making machines run smoothly. But, its weakness compared to steel has led to looking for better options.
The Advent of Modern Composite Flywheels
New materials like carbon-fiber rotors have changed the flywheel world. These flywheels are strong, light, and can spin very fast. They are made to work at high speeds, offering big improvements over old cast iron ones.
- Increased tensile strength and improved machinability compared to cast iron
- Reduced weight and improved power density for enhanced efficiency
- Ability to withstand higher rotational speeds and centrifugal forces
- Potential for longer service life and reduced maintenance requirements
The flywheel world is growing, and the choice of materials is key. It will shape the future of these important parts in many industries.
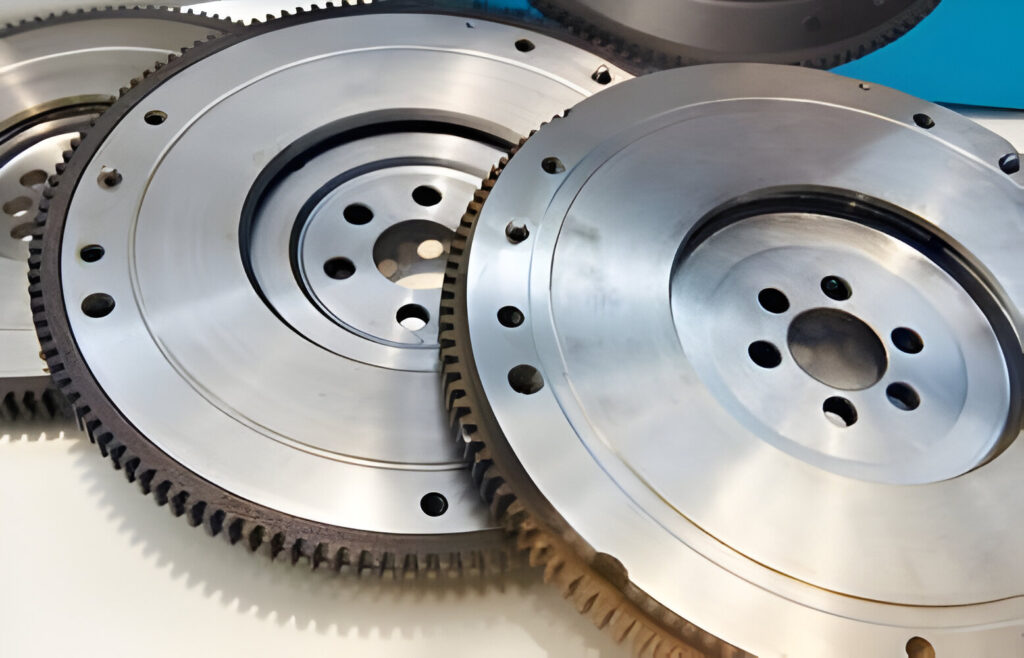
Flywheel Casting: The Casting Process Unveiled
At the heart of high-performance machinery lies a crucial component - the flywheel. The flywheel casting process is an intricate dance of precision and expertise. Molten metal is carefully transformed into a functional masterpiece. Let's unveil the details of this captivating process.
The journey begins with the creation of a two-part pattern, which serves as the template for the mold. This pattern is delicately placed within a flask, and sand is meticulously packed around it to form the mold. To facilitate the smooth flow of molten metal, a runner and riser are strategically incorporated into the mold design.
With the pattern in place, the cope (top box) is removed, and the patterns are carefully tapped and extracted. The mold is then reassembled, ready to receive the molten metal. The moment of truth arrives as the molten metal is poured into the gated mold, filling every nook and cranny with precision. As the casting cools, it transforms from a liquid state to a solid form, ready to be extracted and polished to perfection.
At KT-FOUNDRY, we employ this time-honored sand casting process to produce high-quality flywheel castings. Our expertise in material selection, mold design, and casting techniques ensures that each flywheel meets the rigorous demands of modern machinery. From traditional cast iron to advanced composite materials, we tailor our approach to deliver exceptional performance and longevity.
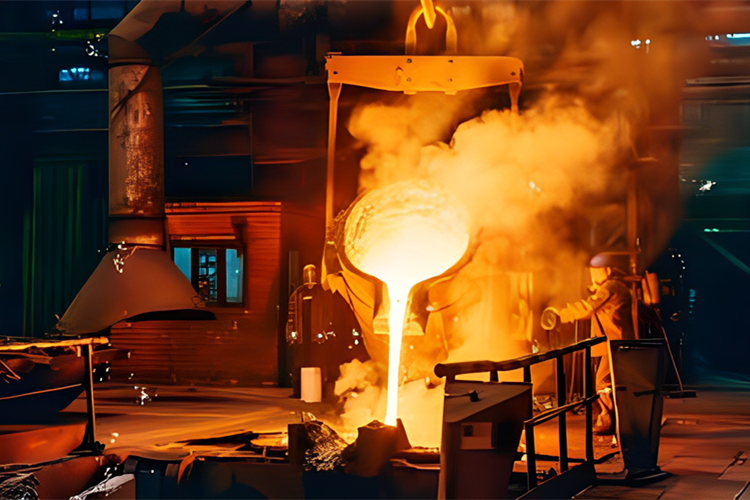
The casting process is not merely a mechanical endeavor; it is a symphony of art and science. By seamlessly integrating the latest technologies and time-tested techniques, we create flywheels that are not only functional but also visually stunning. Join us as we uncover the captivating world of flywheel casting and unlock the secrets to superior performance.
Design Considerations for Flywheels
Creating an efficient flywheel is a detailed task. It requires balancing design considerations carefully. The goal is to find the right energy requirements and moment of inertia for smooth speed. Also, the flywheel geometry must be optimized for safety and performance.
Determining Energy Requirements and Moment of Inertia
To start, we need to figure out the kinetic energy needed for smooth speed. This depends on the torque-time relationship and the coefficient of cyclic variation. For electric motor-driven compressors, the coefficient is between 1/30 to 1/40. Diesel-driven compressors have the lowest coefficient, around 1/10.
Optimizing Flywheel Geometry for Safety and Performance
After figuring out the energy requirements and moment of inertia, we define the flywheel's geometry. We aim for a design that's both efficient and safe. The right shape, size, and material properties are crucial for performance at the designed operating speeds.
Overdesigning can cause problems like overheating motors and heavier loads on bearings. It can also lead to vibrations and fractures.
Material | Density (kg/m³) | Yield Strength (MPa) | Ultimate Strength (MPa) | Poisson's Ratio |
---|---|---|---|---|
Grey Cast Iron | 7200 | 240 | 276 | 0.28 |
Carbon Steel | 7850 | 250 | 460 | 0.3 |
Aluminum Alloy | 2770 | 280 | 310 | 0.33 |
By focusing on these design factors, engineers can make flywheels that store and release energy well. This ensures smooth and efficient machine operation in many applications.
Stress Analysis in Flywheel Components
Flywheels are key parts in machines and face stress from their fast spin. The rim holds most of the flywheel's weight and deals with tensile stress from spinning. It also faces tensile bending stress from the arms holding it in place. Knowing these stresses is vital for the flywheel's safety and reliability.
Centrifugal and Bending Stresses in the Rim
The rim's centrifugal stress is like the stress in a thin, pressurized cylinder. It depends on the material's density, the square of the spin speed, and the radius. The bending stress in the rim is based on the rim being fixed at both ends and loaded evenly.
To lessen these stresses, it's important to analyze and improve the flywheel's design. Choosing the right material, designing the cross-section, and controlling the spin speed are all key.
Stress Component | Gray Cast Iron | Aluminum Alloy |
---|---|---|
Equivalent (von-Mises) Stress | 0.02189 MPa | 0.02164 MPa |
Normal Stress | 0.003073 MPa | 0.003591 MPa |
Shear Stress | 0.001474 MPa | 0.001556 MPa |
Total Deformation | 1.419 x 10^-5 mm | 2.24 x 10^-5 mm |
By grasping the stresses on the flywheel, especially the rim, designers can make it better. They can choose the right materials and design for safety and performance.
Applications and Benefits of Flywheels
Flywheels are becoming more important in many fields. They are great at storing and releasing energy, which is better than batteries in some cases.
Aerospace and Electric Vehicle Applications
In space, flywheels beat batteries because they hold more energy and weigh less. They last longer and work better, which is key for space travel.
For electric cars, flywheels can make them go faster and climb hills better. They use high-speed rotors to pack a lot of power in a small space.
They also help keep the power grid stable by providing backup power quickly. Flywheels are easy to maintain and respond fast, making them useful in many areas.
Application | Benefits of Flywheels |
---|---|
Aerospace |
|
Electric Vehicles |
|
Grid Interruption Backup |
|
Flywheels are very useful in many areas. They help in space, electric cars, and keeping the power grid stable. Their benefits make them a valuable technology.
Advances in Flywheel Technology
Flywheel technology has made huge strides in recent years. High-speed composite flywheels are leading this change. They use materials like carbon fiber to spin at speeds up to 100,000 rpm.
These flywheels are made light but strong. They spin in a vacuum to cut down on energy loss. This makes them very efficient at storing energy, rivaling traditional methods.
Powering the Future with High-Speed Composite Flywheels
Today, flywheels can spin from 20,000 to over 50,000 rpm. This speed allows them to quickly charge and discharge energy. They can do this in just minutes.
These flywheels can last for decades with little upkeep. They store 100–130 Wh/kg of energy and can be up to 90% efficient. They're set to change how we store and manage energy.
At KT-FOUNDRY, we lead in flywheel technology. We offer custom flywheel solutions for many uses. Our knowledge in materials, aerodynamics, and electronics helps us create top-notch flywheel energy storage systems.
Conclusion
Flywheel casting is key in making these important parts. They help smooth out speed changes and store energy. This is crucial for many uses.
From old cast iron to new composite materials, flywheel tech has come a long way. This has led to better performance, efficiency, and safety.
At KT-FOUNDRY, we keep up with flywheel casting advancements. We aim to make custom flywheel castings for our clients. We use the latest in materials and techniques.
The need for good energy storage systems is growing. Flywheel casting will be more important in many fields. We're dedicated to making flywheel parts better and more efficient.