In the world of industrial manufacturing, temperatures can reach extreme levels. The role of heat resistant castings is crucial. They are made to handle the toughest high-temperature settings, ensuring components last long in various industries.
Heat resistant castings can handle temperatures over 1200°F without melting or corroding. They are made with more alloy than regular castings. This includes a lot of nickel (up to 70%) and chromium (10-30%), plus iron, carbon, silicon, manganese, and molybdenum.
These materials help parts work great in tough places like aerospace, oil and gas, and steel production. They also do well in mining, off-road, food processing, and more. Thanks to stainless steel, nickel, and chromium, these castings stay strong and resist corrosion, even in the hottest conditions.
Key Takeaways
- Heat resistant castings are specialized castings designed to withstand high-temperature industrial operations above 1200°F.
- These castings typically contain a high percentage of nickel (up to 70%) and chromium (10-30%), along with other alloying elements.
- Heat resistant castings are essential in industries like aerospace, oil and gas, steel production, mining, and more, where components must endure extreme heat, corrosion, and oxidation.
- The exceptional properties of materials like stainless steel, nickel, and chromium enable heat resistant castings to maintain their mechanical and corrosion resistance even in the most demanding high-temperature environments.
- Investing in high-quality heat resistant castings can lead to long-term savings through reduced downtime and maintenance costs.
What are Heat Resistant Castings?
Heat resistant castings are special metal parts made to handle very high temperatures. They don't melt or corrode at temperatures over 1200°F. These parts are used in many industrial settings where things get very hot.
Defining Heat Resistant Castings and Their Applications
These castings are made from alloys rich in nickel and chromium. This mix gives them great heat and corrosion protection. They keep their shape and strength even in very hot and harsh conditions.
Some main uses for heat resistant castings are:
- Power generation equipment, like turbine blades and boiler parts
- Petrochemical processing units, reactors, and heat exchangers
- Aerospace components, including aircraft engines and exhaust systems
- Industrial furnaces, kilns, and other high-temperature equipment
Benefits of Using Heat Resistant Castings
Using heat resistant castings brings many advantages in high-temperature work. These include:
- Extended component life - Their excellent heat and corrosion resistance can make parts last longer. This means less need for repairs and replacements.
- Improved performance - These castings keep their strength and shape even when it's very hot. This ensures equipment works well and efficiently.
- Enhanced safety - Their ability to handle extreme heat and corrosive environments makes things safer in industrial settings.
By using heat resistant castings, industries can work better, save money, and stay safe in hot environments.
Materials Used in Heat Resistant Castings
Heat resistant castings are made from special alloys. These alloys have lots of nickel and chromium. These elements help the material handle high temperatures and fight off corrosion.
Nickel and Its Significance in Heat Resistant Alloys
Nickel is a big part of these alloys, making up to 70%. It makes the alloys great at handling heat and corrosion resistance. The high nickel content also helps the alloys have an austenitic structure. This structure is key for working well in hot places.
The Role of Chromium in Heat Resistant Castings
Chromium is also important, making up 10% to 30% of the alloy. It helps the material stay strong at high temperatures and fight oxidation. This is important for keeping the parts working well for a long time. Nickel and chromium together make a strong ferralloy for tough high-temperature jobs.
Other elements like iron, carbon, silicon, manganese, and molybdenum are added too. They help the casting's strength, structure, and performance in high-heat settings. The exact mix of these alloys is carefully chosen for different industries, like oil and gas and aerospace.
Alloy | Nickel (%) | Chromium (%) | Carbon (%) | Silicon (%) | Manganese (%) |
---|---|---|---|---|---|
IS 4522 | 0-64.0 | 8.0-58.0 | 0.05-1.70 | 0.5-2.5 | 0.1-4.0 |
DIN 17445 | 0-64.0 | 8.0-58.0 | 0.05-1.70 | 0.5-2.5 | 0.1-4.0 |
ASTM A297 Gr | 0-64.0 | 8.0-58.0 | 0.05-1.70 | 0.5-2.5 | 0.1-4.0 |
These alloys are used in many fields, from oil refining to making furnace parts. They can handle extreme temperatures and resist corrosion. This makes them very important in these tough environments.
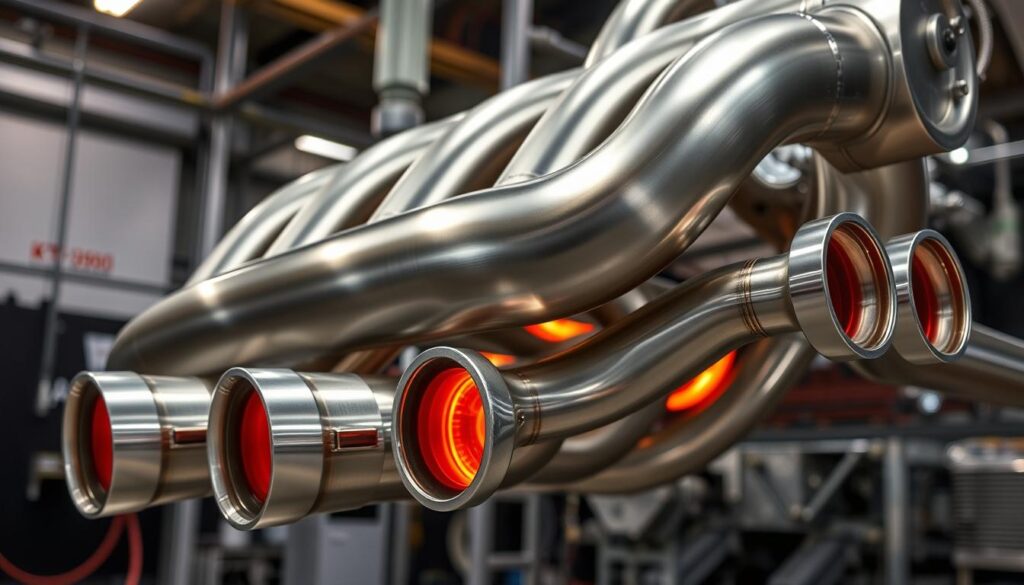
"The development of high-performance heat-resistant materials is crucial for enhancing automobile engine efficiency and reducing environmental emissions."
Heat Resistant Castings
Heat resistant castings are made to handle very high temperatures and tough industrial settings. They are crafted from alloys like nickel and chromium. These materials help them resist heat and corrosion well, making them reliable in many uses.
These castings are used in many fields like aerospace, oil and gas, and steel making. They are also used in mining and more. They help parts work safely and efficiently in hot conditions.
The dataset shows a wide range of heat resistant castings. You can find trays, spacer grids, and more in different sizes. For example, trays can be as big as 24 x 36 x 3 inches.
These castings are made from materials like cast steel and alloyed irons. They have strong mechanical properties. This includes tensile strength from 540 N/mm² to 770 N/mm² and can handle temperatures up to 1150°C.
These castings also go through a strict quality check. They are certified under ISO 9000:2015. The company offers machining and installation services. They also test samples in their lab to ensure top quality.
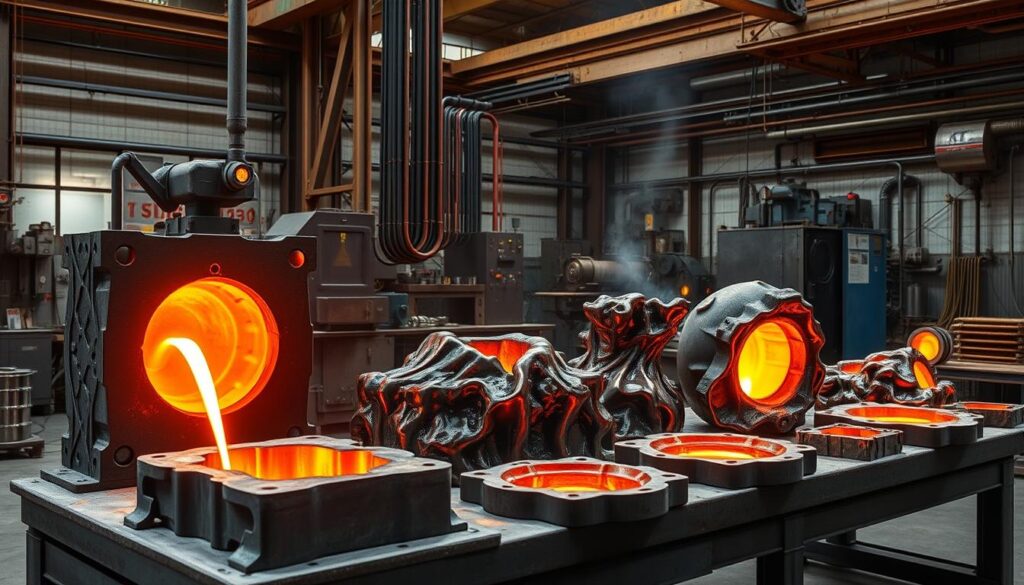
"Heat resistant castings are essential components in a wide range of high-temperature applications, allowing manufacturers to overcome the challenges posed by harsh industrial environments and ensure the reliable performance of their products."
Industries Utilizing Heat Resistant Castings
Heat resistant castings are used in many industries. They meet the needs of high-temperature environments. These metal parts are key to keeping equipment running well and lasting long.
Aerospace and Aircraft Applications
In aerospace and aircraft, these castings are crucial. They handle extreme temperatures and pressures. They are used in turbine blades and engine parts, making flying safe and efficient.
Oil and Gas, Steel Production, and Mining Uses
The oil, gas, steel, and mining sectors use these castings a lot. They are in furnace parts, burners, and valves. This ensures smooth operations and avoids costly downtime.
Off-road, food processing, and railroad also use these castings. They help machines work well in tough conditions.
Industry | Applications of Heat Resistant Castings |
---|---|
Aerospace and Aircraft | Turbine blades, engine components, and other mission-critical assemblies |
Oil and Gas | Furnace parts, burners, valves, and other high-temperature equipment |
Steel Production | Furnace parts, burners, and other steel manufacturing equipment |
Mining | Furnace parts, burners, and other mining equipment |
Off-Road Equipment | Components for machinery used in harsh outdoor environments |
Food Processing | Equipment for high-temperature food processing operations |
Railroad | Components for railroad vehicles and infrastructure |
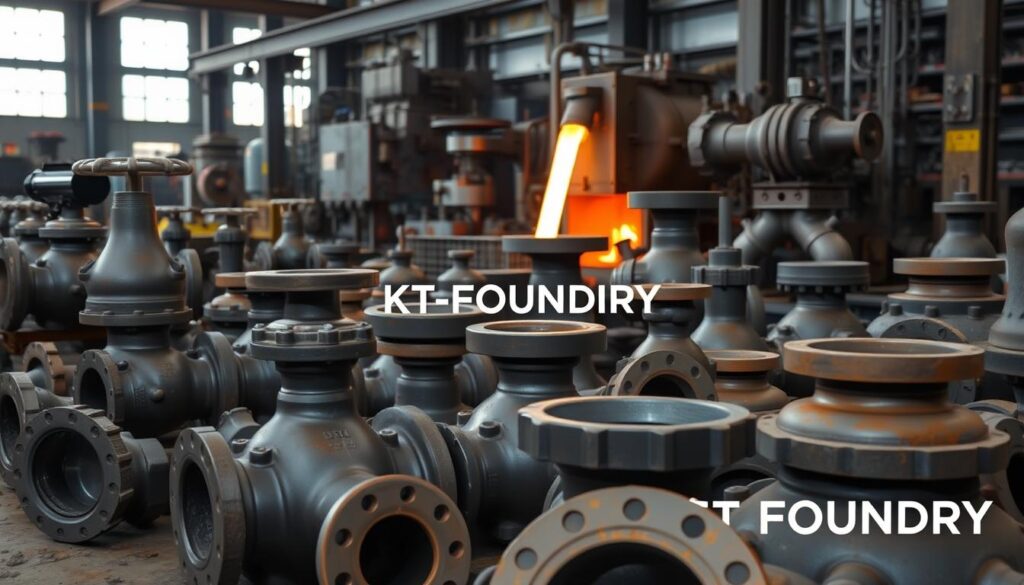
Heat resistant castings are very useful in many industries. They help equipment work well even in tough conditions.
Manufacturing Processes for Heat Resistant Castings
Creating high-quality heat resistant castings requires special techniques. Sand casting and investment casting are two main methods used.
Sand Casting: Versatile and Cost-Effective
Sand casting pours molten metal into a sand mold. It then cools and solidifies. This method is great for making big, complex castings.
By controlling the materials, melting, and cooling, makers can get the right structure and performance. This ensures the castings work well at high temperatures.
Investment Casting: Precision and Intricate Designs
Investment casting uses a ceramic mold for detailed, precise parts. It's perfect for complex shapes. KT-Foundry excels in this, making custom castings for their clients.
Manufacturing Process | Applications | Advantages |
---|---|---|
Sand Casting | Larger, more complex heat resistant castings | Cost-effective, versatile |
Investment Casting | Intricate, near-net-shape heat resistant parts | Exceptional dimensional accuracy, complex geometries |
Both sand and investment casting need careful control. This ensures the castings have the right structure and performance at high temperatures.

"At KT-Foundry, we are committed to providing our clients with exceptional heat resistant casting solutions tailored to their specific needs. Our expertise in sand casting and investment casting allows us to deliver high-quality, durable, and reliable castings for a wide range of applications."
Common Heat Resistant Casting Products
In the world of high-temperature industrial uses, heat resistant castings are key. They help make many specialized products. For example, furnace rolls and radiant tubes are made to handle extreme heat and stress.
Furnace Rolls, Radiant Tubes, and Burner Nozzles
Furnace rolls are vital in many industrial furnaces. They handle intense heat and mechanical stress. These components ensure materials move smoothly through the furnace, keeping heat distribution consistent.
Radiant tubes are crucial for heat transfer in furnaces and ovens. They distribute thermal energy well. Burner nozzles, made from heat-resistant materials, control fuel combustion efficiently in high-temperature processes.
Baskets, Trays, and Retorts for Heat Treatment
Heat resistant castings are also used in heat treatment processes. Baskets, trays, and retorts support workpieces during heat treatment. They keep their shape and function well at high temperatures.
At RMC Casting Foundry, we provide a wide range of heat-resistant steel and alloy castings. Our team works hard to offer solutions that perform well in tough environments.
"Heat-resistant steel castings occupy a large proportion in the field of heat-resistant steel, as high-alloy heat-resistant steels are difficult to process and deform, leading to the production of castings being more cost-effective than rolled products."
Choosing the Right Heat Resistant Casting Solution
When picking a heat resistant casting for your needs, think about the temperature range, corrosive environments, and mechanical properties. KT-FOUNDRY's team can help you choose the best alloy and casting method. This ensures your high-temperature parts work well for a long time.
Heat-resistant castings handle temperatures over 1000°C well. Materials like nickel-based superalloys are great for this. They keep their shape and don't warp, even with temperature changes.
These castings are also tough and last longer than regular materials. They can handle high heat and don't deform easily. Plus, they form protective layers against corrosion, which means less upkeep.
Using heat-resistant castings means less maintenance and lower costs. They can handle a lot of stress and sudden impacts. This makes them safe and reliable for industrial equipment.
To talk about your project and how our solutions can help, contact us today.
Property | Benefit |
---|---|
High-temperature resistance | Withstand temperatures above 1000°C |
Dimensional stability | Prevent warping or distortion during thermal cycling |
Thermal shock resistance | Withstand abrupt temperature changes without structural damage |
Corrosion resistance | Generate protective oxide layers to minimize maintenance |
Mechanical properties | High tensile strength, fatigue strength, and impact resistance |
By thinking about these factors and working with KT-FOUNDRY, you can find the perfect casting for your high-temperature needs. This ensures your parts work well and last a long time.
Conclusion
Heat resistant castings are key in many industries where high temperatures are common. Made from alloys like nickel and chromium, they stand up to heat and corrosion well. This makes them perfect for harsh environments in fields like aerospace and mining.
Working with KT-FOUNDRY means getting the right casting for your needs. We know all about materials and manufacturing. This helps us find the best casting for your high-temperature work.
KT-FOUNDRY can provide castings that resist high temperatures, corrosion, and oxidation. Our experience and innovation help save costs and improve efficiency. We aim to make your operations more reliable and efficient.