iron casting
Iron Casting
Iron casting is a manufacturing process used to create metal parts by pouring molten iron into a mold and allowing it to cool and solidify into the desired shape. Iron casting is widely used to manufacture mechanical parts, pipes, valves, automotive components, and construction materials due to its relatively low cost, simple process, and suitability for large-scale production.
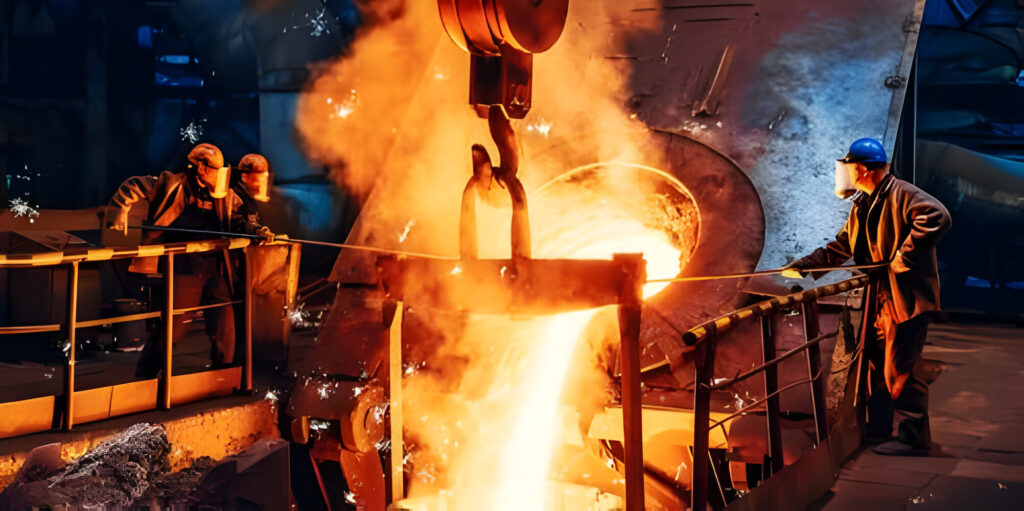
Types of Iron Castings
Iron castings come in various types, each with distinct properties and applications. Two common types are ductile iron casting and gray iron casting.
Ductile Iron Casting: Also known as nodular cast iron or spheroidal graphite iron, ductile iron is characterized by the presence of spherical graphite inclusions in the metal. This microstructure gives ductile iron superior tensile strength, impact resistance, and ductility compared to other types of cast iron. Ductile iron castings are commonly used in applications that require toughness and flexibility, such as automotive components (e.g., crankshafts, suspension parts), pipes, and machinery.
Gray Iron Casting: Gray iron is the most widely used type of cast iron, named for its gray-colored fracture surface which is due to the presence of flake graphite in its microstructure. This type of iron has excellent machinability, good thermal conductivity, and vibration damping properties. However, it is more brittle compared to ductile iron. Gray iron castings are often used in applications where these properties are advantageous, such as engine blocks, cylinder heads, housings, and various machine bases and frames.
Casting Processes
Among various casting processes, sand casting is a widely used method, particularly valued for its versatility and cost-effectiveness. Our sand casting process involves several key steps that ensure high-quality and precise castings.
Pattern Making: The process begins with creating a pattern, which is a replica of the final product. The pattern is made from wood, metal, or plastic and is used to form the mold cavity.
Mold Preparation: A mixture of sand and a binder material is packed around the pattern in a mold box to create the mold. The sand mixture must have the right properties to hold the shape and withstand the molten metal's temperature.
Core Making: If the casting requires internal cavities or complex geometries, cores made of sand are placed inside the mold. These cores are also created using patterns.
Melting and Pouring: The desired metal is melted in a furnace and then poured into the prepared mold through a gating system. The molten metal fills the mold cavity, taking the shape of the pattern.
Cooling and Solidification: The mold is allowed to cool, and the metal solidifies into the shape of the casting. Cooling time varies depending on the metal and the size of the casting.
Shakeout and Cleaning: Once the metal has solidified and cooled, the sand mold is broken apart to remove the casting. The casting is then cleaned to remove any remaining sand, scale, or residues.
Finishing and Inspection: The final step involves removing any excess material, such as gating and risers, and performing any necessary machining or finishing operations. The casting is then inspected for quality and accuracy.
Our factory produces pictures
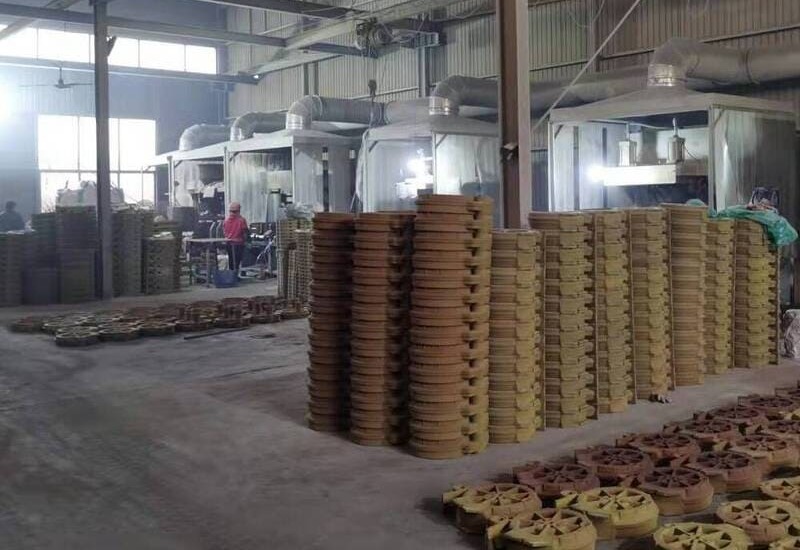
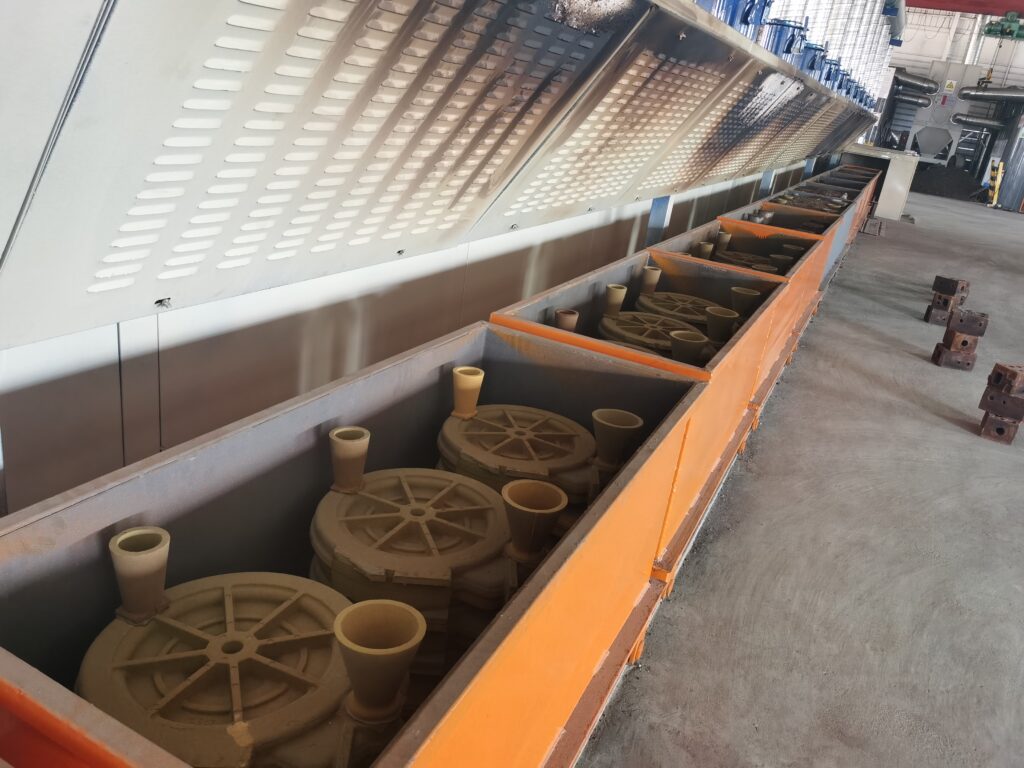

Leading Iron Casting Manufacturers and Companies
KT-Foundry stands out among leading iron casting manufacturers due to our commitment to quality, innovation, and customer satisfaction. We use premium-grade materials and employ advanced manufacturing techniques to ensure precision and durability. Our skilled workforce and flexible production processes allow us to customize castings for various industries, including automotive, aerospace, machinery, and construction. Additionally, our comprehensive services span from design and prototyping to final production and finishing, ensuring timely delivery and cost efficiency. KT-Foundry’s dedication to excellence and sustainable practices makes us a trusted leader in the iron casting industry.