Manganese steel, also known as Hadfield steel or mangalloy, is a special steel alloy. It has 11-14% manganese. This steel is famous for its strength, toughness, and ability to resist wear.
It's a top choice for tough jobs in many industries. The alloy has high hardness and can get even harder when worked on. It also stands up well to abrasion and impact. This article will dive into how manganese steel casting works, its benefits, and where it's used.
Key Takeaways
- Manganese steel contains 11-14% manganese, which enhances its strength and hardness.
- Manganese steel casting is known for its exceptional toughness, making it suitable for heavy impact loads in industries like mining and construction.
- Manganese casting products exhibit exceptional hardening capacity, becoming highly resistant to damage and abrasion.
- Manganese steel casting is highly resistant to corrosion and suitable for harsh environments.
- Manganese steel casting has a high welding capacity despite its high manganese content.
Introduction to Manganese Steel Casting
Manganese steel, also known as Hadfield steel or mangalloy, is a high-manganese alloy steel. It has been fascinating the industrial world for over a century. This steel, with about 11-14% manganese, was invented by Sir Robert Hadfield in 1882.
Hadfield's discovery of this steel's toughness, hardness, and wear resistance is groundbreaking. It has become essential for many industrial uses.
What is Manganese Steel?
Manganese steel is a high-performance alloy steel. It's known for its unique properties. The high manganese content, along with carbon, silicon, and iron, makes it special.
This steel alloy is famous for its ability to harden under load or impact. It starts soft but becomes extremely hard and resistant to wear.
Historical Background of Manganese Steel
The history of manganese steel begins in the late 19th century. Sir Robert Hadfield, a British metallurgist, made a groundbreaking discovery in 1882. He created a steel alloy with a lot of manganese, unlike traditional carbon steels.
Hadfield's invention, known as Hadfield steel or mangalloy, quickly became famous. It was known for its toughness and wear resistance. This made it a game-changer in the industrial world.
Alloy Composition | Hardness | Applications |
---|---|---|
1.2% Carbon, 12.5% Manganese | 240 BHN to 500 BHN (work-hardened) | Mining, Recycling, Rail, High-Impact Environments |
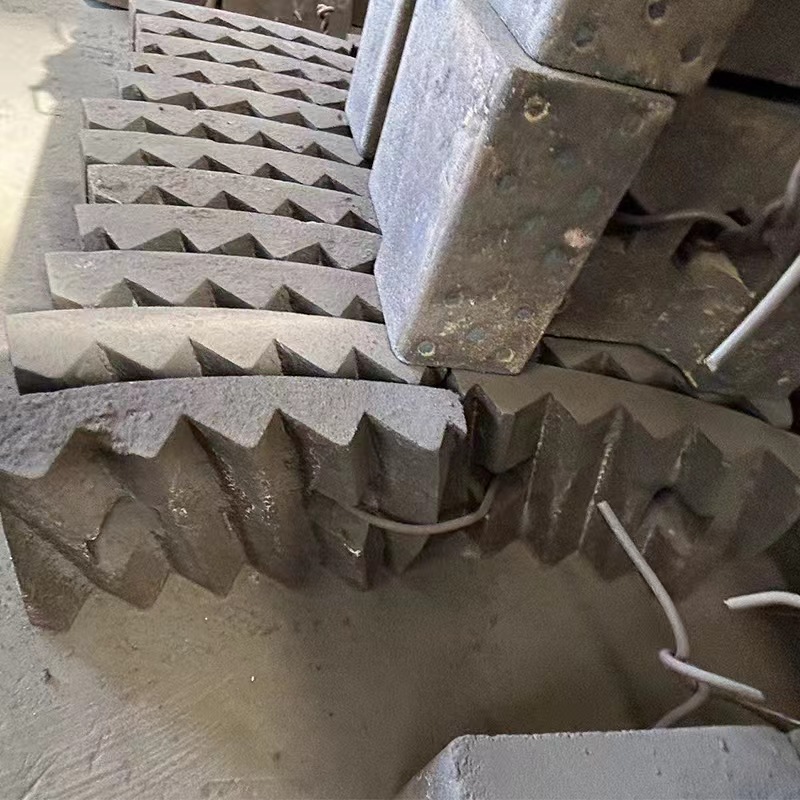
Manganese steel's unique properties have made it crucial in many industries. These include mining, construction, and transportation. Hadfield's invention continues to influence engineering and material science.
Composition and Properties of Manganese Steel
Manganese steel is a special alloy with unique properties. It has about 11-14% manganese, 1.2% carbon, and some silicon and iron. This mix makes manganese steel very strong and durable.
Chemical Composition
Manganese steel stands out because of its high manganese content, between 11% and 14%. This, along with 1.2% carbon, gives it special properties. It also has small amounts of silicon and iron, which help its performance.
Mechanical Properties
Manganese steel's unique mix of elements gives it amazing mechanical properties. These include:
- High Hardness: It's very hard, which means it resists wear and abrasion well.
- Impressive Tensile Strength: It can handle a lot of tensile forces, keeping structures strong.
- Excellent Yield Strength: It resists deformation under load, keeping its shape.
- Outstanding Impact Resistance: It can absorb and spread out a lot of impact energy without breaking.
- Remarkable Toughness: Its strength and flexibility make it very resistant to cracking and breaking.
These properties make manganese steel very valuable. It's used in mining, construction, and transportation because of its strength and durability.
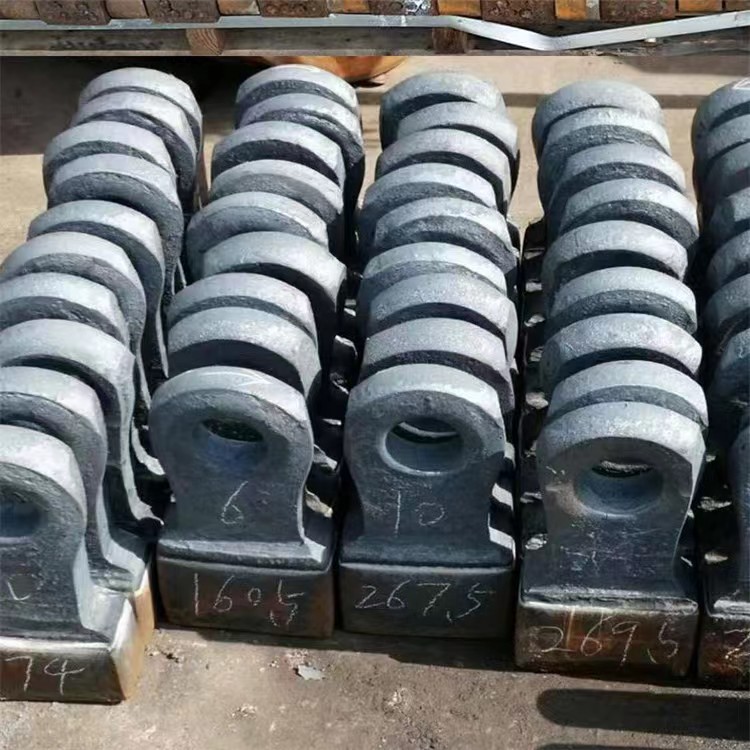
manganese steel casting
Manganese steel is known for its toughness and strength. It's made through different casting methods. These methods help create complex parts needed in many industries.
The process starts with pouring molten manganese steel into molds. It then solidifies into the desired shape.
Casting Processes for Manganese Steel
Two main methods are used to make manganese steel parts: sand casting and investment casting. Sand casting uses a sand mold. Investment casting, or "lost-wax," uses a wax pattern covered in ceramic, then melted away.
Grades of Manganese Steel Castings
Manganese steel castings come in various grades. Each has its own mix and properties for different uses. High manganese steel has five grades, with carbon and manganese levels set by standards.
Ultra-high manganese steel, without a national standard, must have more than 18% manganese. The silicon content affects toughness, aiming for less than 0.5%. Low phosphorus and sulfur levels are also key, with phosphorus under 0.07%. Chromium, at about 2.0%, boosts wear resistance.
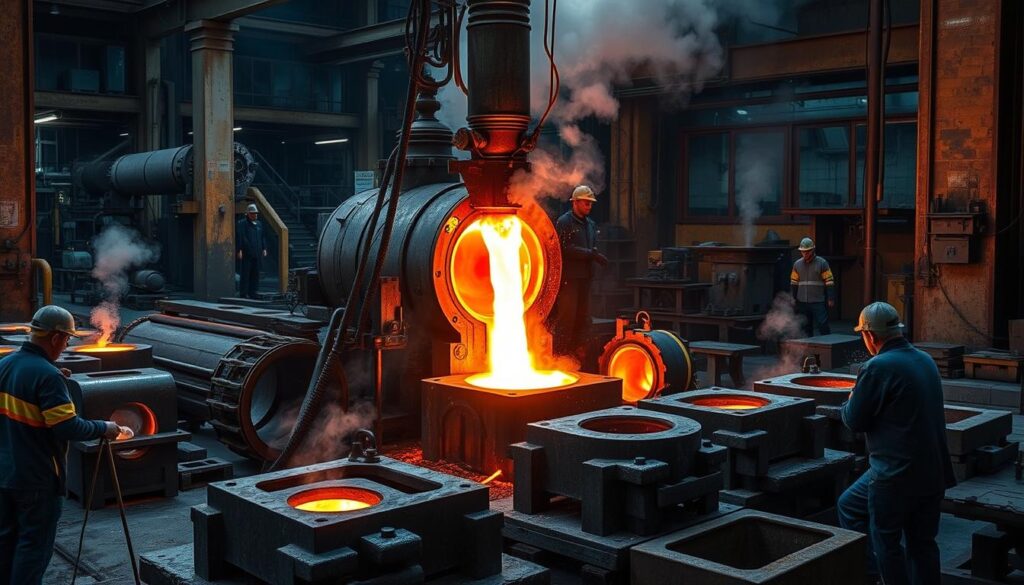
Controlling the chemical mix and production is vital. It ensures manganese steel castings meet their performance needs. This makes them a top choice for mining, construction, and industrial equipment.
Unique Properties of Manganese Steel
Manganese steel, also known as Hadfield steel, is known for its exceptional properties. It has a remarkable work hardening ability. When it faces impact or pressure, it becomes harder and stronger through strain hardening.
This property lets manganese steel handle repeated impacts well. It keeps its toughness even after many hits.
Manganese steel is also famous for its high wear resistance. This is due to its hardness and ability to work harden. Its special microstructure helps it resist abrasion from hard surfaces.
This makes manganese steel perfect for heavy-duty jobs. It's great for mining and construction equipment.
Property | Manganese Steel |
---|---|
Work Hardening Ability | Exceptional |
Abrasion Resistance | High |
Impact Resistance | Excellent |
Hardness | Increased by work hardening |
Strength | Increased by work hardening |
Durability | Exceptional |
Manganese steel's unique properties make it a versatile and durable choice. It's perfect for many industrial needs that require top performance and long life.
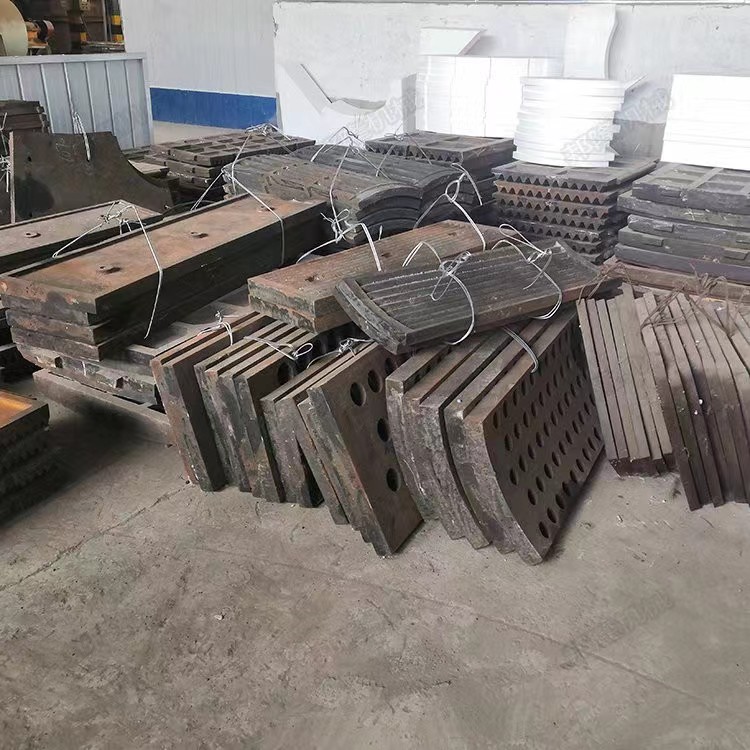
Applications of Manganese Steel Castings
Manganese steel castings are used in many industries because of their great properties. In mining and quarrying, they are key for making crusher jaws, hammers, and wear plates. Their high hardness, toughness, and wear resistance make them perfect for these tough jobs.
Mining and Quarrying Equipment
In mining and quarrying, manganese steel castings are crucial. They are used in crusher parts, excavator buckets, and more. These parts last long because manganese steel is so tough and durable.
Construction and Earthmoving Machinery
The construction and earthmoving sectors also use manganese steel castings a lot. Things like excavator buckets, bulldozer blades, and other high-impact equipment are made with it. This is because manganese steel can handle a lot of wear and tear without breaking down.
Application | Manganese Steel Casting Benefits |
---|---|
Mining and Quarrying Equipment | High hardness, toughness, and wear resistance for crusher parts, hammers, and wear plates |
Construction and Earthmoving Machinery | Durability and impact resistance for excavator buckets, bulldozer blades, and other high-impact components |
Railroad Components | Increased service life and reduced maintenance for railroad switches, crossings, and other rail components |
Power Generation | Corrosion resistance and wear protection for components in power generation equipment |
Cement Industry | Abrasion resistance and long service life for crusher parts, mill liners, and other wear-prone components |
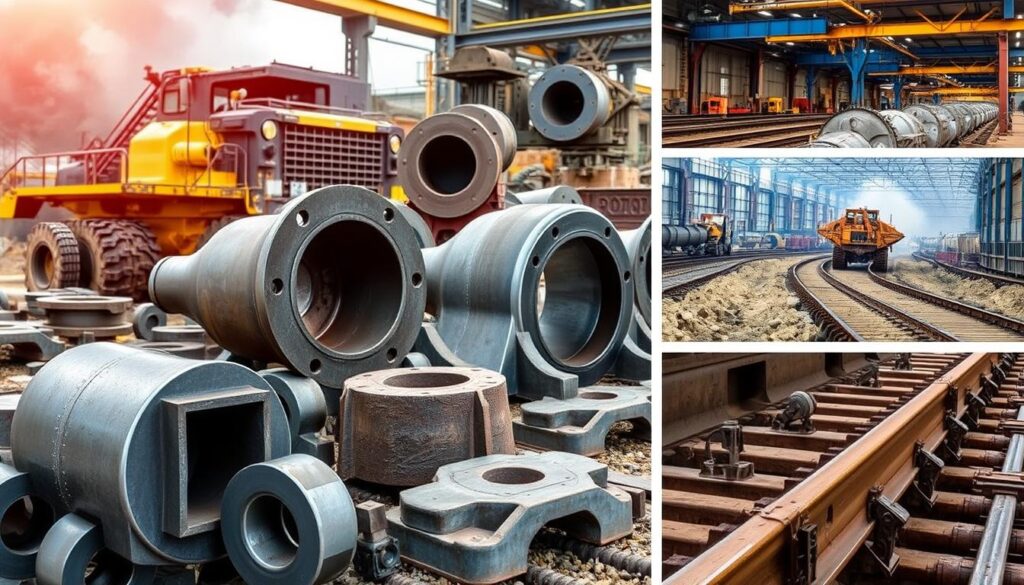
"Manganese steel castings are essential in the construction and operation of mining and quarrying equipment, ensuring the durability and reliability of critical components."
Heat Treatment of Manganese Steel
To make manganese steel even better, different heat treatments can be used. It's usually sold in an annealed state, which makes it easy to work with. But, to boost its hardness and wear resistance, it can go through quenching and tempering.
Annealing and Quenching Processes
Annealing heats the steel to a certain point, then cools it slowly. This makes the material softer and more flexible, perfect for shaping. On the other hand, quenching rapidly cools the steel, making it harder and stronger.
Using annealing and quenching can really improve manganese steel. These methods enhance its strength, wear resistance, and overall properties optimization. This is great for applications that need high hardness and durability.
Heat Treatment Process | Purpose | Typical Parameters |
---|---|---|
Annealing | Softens the steel and improves machinability | Heating to 850-900°C, holding for 1-2 hours, slow cooling |
Quenching | Increases hardness and strength | Heating to 1050-1100°C, rapid cooling in water or oil |
By carefully managing the heat treatment of manganese steel, including annealing and quenching, makers can tailor the material's properties. This is to meet the exact needs of their projects, whether it's better strength, wear resistance, or overall performance optimization.
Advantages of Manganese Steel Castings
Manganese steel castings have many benefits that make them popular in different fields. Their durability and long life come from their high hardness and wear resistance. This means they last longer, need less upkeep, and cause less downtime. All these factors make them cost-effective for users.
The work hardening ability of manganese steel makes it stronger and more resistant to wear over time. This property keeps manganese steel components strong and tough for a long time. It also means they don't need to be replaced or fixed often, saving money.
Durability and Long Service Life
Manganese steel is known for its durability and long service life. It's a top choice for areas with high impact and abrasion. Its special mix and heat treatment give it great wear resistance. This ensures manganese steel parts can handle tough environments and stay strong for a long time.
Cost-Effectiveness
Manganese steel castings are also cost-effective. They need less maintenance and last longer, which saves money and time. This leads to higher profits and a better return on investment for businesses.
"Manganese steel is cost-effective for applications subjected to high impact and abrasion."
Machining and Welding Manganese Steel
Manganese steel is known for its toughness and resistance to wear. However, it poses challenges when machining and welding. Its hardness makes it hard to cut and shape using common methods. Special tools and techniques are needed to work with this alloy.
Machining Manganese Steel
Machining manganese steel is tough because it hardens quickly. It can't be easily softened by annealing. This means using special tools like carbide or diamond tips to cut it.
Drilling this metal is especially hard. Diamond or carbide drill bits are often needed. Oxy-acetylene torches can cut it, but plasma or laser cutting is better. These methods give cleaner cuts.
Welding Manganese Steel
Welding manganese steel needs careful attention. It's important to manage heat well and cool the weld fast to avoid cracks. Special welding electrodes, like those in the AWS EFeMN group, help a lot.
This metal is also toxic, so safety is key. Good ventilation and protective gear are essential when welding it.
Key Considerations for Machining and Welding Manganese Steel |
---|
|
Knowing how to work with manganese steel is key. By using the right methods, we can use its strength in many ways. This makes it valuable in many industries.
Comparison with Other Steel Alloys
Manganese steel stands out when compared to other steel alloys. It has a unique mix of properties. Carbon steel is strong and hard but can't beat manganese steel in wear resistance and toughness. Stainless steel is great against corrosion but can't match manganese steel's hardness and ability to harden when worked.
Also, manganese steel doesn't attract magnets, which is a plus in some situations where magnetic interference is a problem.
Manganese Steel vs. Carbon Steel
Carbon steel is common and strong. But manganese steel is better at resisting wear and being tough. This is because manganese steel gets harder and stronger when it's worn or hit, unlike carbon steel.
Manganese Steel vs. Stainless Steel
Stainless steel is known for fighting off corrosion. But manganese steel is harder and better at hardening when worked on. This makes manganese steel great for tough jobs like mining and construction. Plus, manganese steel doesn't attract magnets, which is useful in some cases.
Steel Alloy | Strength | Hardness | Wear Resistance | Corrosion Resistance | Magnetic Properties |
---|---|---|---|---|---|
Manganese Steel | High | High | Exceptional | Good | Non-magnetic |
Carbon Steel | High | High | Good | Moderate | Magnetic |
Stainless Steel | Moderate | Moderate | Good | Excellent | Magnetic |
The table shows the main differences between manganese steel, carbon steel, and stainless steel. It helps us see how these alloys compare.
Challenges and Limitations
Manganese steel is known for its great wear resistance and ability to harden when worked. Yet, it also has some big challenges and limits. One major issue is how hard it is to machine this material well.
Its high hardness and tendency to harden when worked make it tough to cut and grind. You need special tools and methods to work with manganese steel. This can make production more expensive. Also, manganese steel can crack under very hard impacts, which is a worry in some uses.
Machining Difficulties
Manganese steel's hardness and tendency to harden make machining hard. Regular cutting tools and grinding methods often can't shape and finish it well. You need special tools and techniques, which can increase costs a lot.
High Initial Cost
Manganese steel costs more than regular steel at first. This can be a problem in some situations where saving money is key. The need for special tools and ways to work with manganese steel raises its price. This cost must be balanced against its excellent performance.
Even with these challenges, manganese steel is still a good choice for certain jobs. Its unique benefits, like great wear resistance and hardening, are worth the extra cost and effort.
"Proper mold construction and pouring system quality are essential to avoid defects like porosity and inclusions in manganese steel castings."
Conclusion
Manganese steel casting is a standout material. It has high hardness, toughness, and wear resistance. It also gets stronger when worked on.
These qualities make manganese steel castings popular in many fields. This includes mining, construction, power generation, and transportation. While it can be hard to machine and is more expensive at first, its durability and long life make it worth it.
As industries look for better materials, manganese steel castings will stay important. They perform well under tough conditions. This makes them a good choice for many uses, like rail tracks, mining gear, and construction machines.
From this look into manganese steel casting, we see its great properties and uses. There's also ongoing research to make it even better. As we go forward, we'll see more improvements in manganese steel casting technology. This will meet the need for strong, reliable materials in today's industries.
KT-FOUNDRY excels in producing manganese steel castings known for their exceptional durability, impact resistance, and long wear life. With our extensive experience and specialized expertise, we focus on precise alloy composition, state-of-the-art casting techniques, and thorough quality checks to ensure every casting performs reliably in the most demanding conditions. Our manganese steel castings are ideal for heavy-duty applications, offering outstanding strength and resilience. We also offer tailored solutions to meet specific project needs, ensuring optimal results.
To help us provide a customized solution for you, please fill out the form below.