Wrought iron and cast iron are two distinct forms of iron that differ in their composition, texture, production methods, and applications. Understanding the differences between these materials is crucial for selecting the appropriate one for specific manufacturing needs or restoration projects. This article will explore the fundamental distinctions between wrought iron, known for its ductility and malleability, and cast iron, recognized for its brittleness and high carbon content.
What is Wrought Iron?
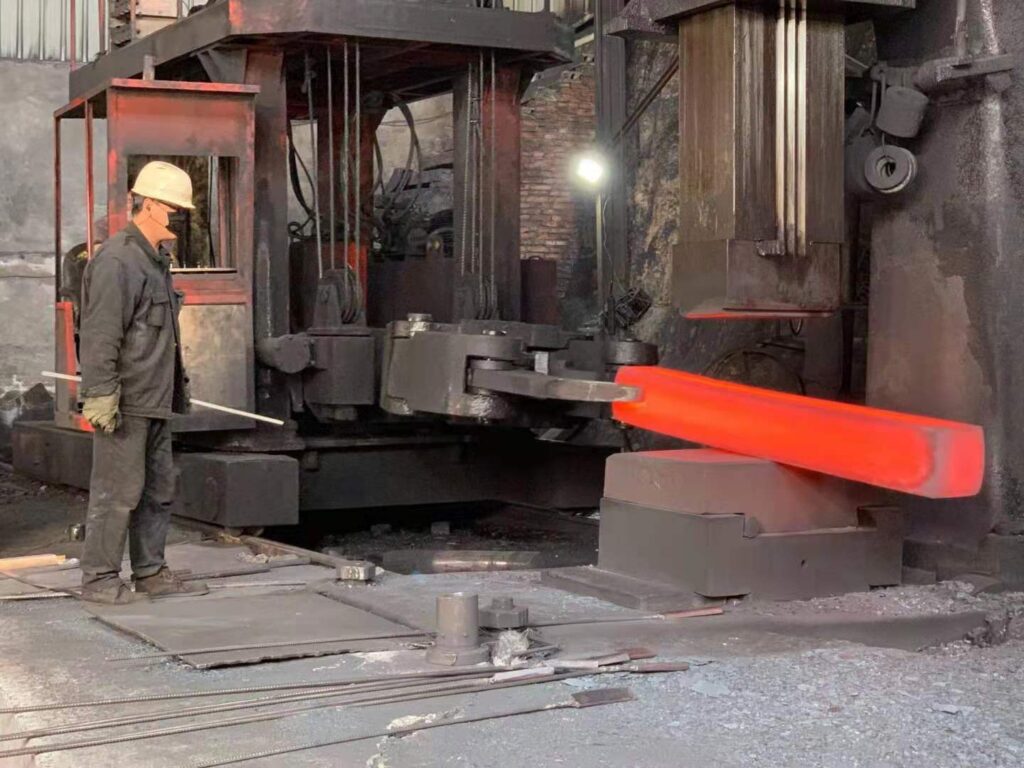
Wrought iron is a form of iron with a very low carbon content in contrast to cast iron. It is a semi-fused mass of iron with fibrous slag inclusions, which gives it a "grain" resembling wood that is visible when it is etched or bent to the point of failure. Historically, wrought iron was known as commercially pure iron; however, it no longer meets the modern definition of traditional pure iron due to its content of some amount of incidental impurities and slag. The term "wrought" refers to the iterative process of working the metal through hammering or rolling, hence its name: wrought means worked in Old English.
This material is highly malleable, meaning it can be heated and then shaped with tools, and its remarkable resistance to fatigue and corrosion once made it an indispensable building material before the advent of steel production techniques. Renowned for its ductile strength and toughness, wrought iron finds itself utilized effectively where integrity and longevity are top priorities, such as in railings, rivets, chains, and various ornamental fixtures. It possesses an inherent ability to withstand tensile stress while exhibiting relative plasticity.
When discussing wrought iron's composition, one should acknowledge that its carbon content does not exceed 0.08%, setting it apart from both steel (which has higher carbon content) and cast iron (which contains significantly more carbon). This distinctive attribute imparts upon wrought iron both specific characteristics in terms of forging capabilities as well as susceptibilities when subjected to certain stresses.
Renowned historically for being manufactured through processes like puddling – where pig iron was converted into wrought iron – this material showcases qualities that have long been valued in various industries. However, despite its advantageous properties at one time holding sway over construction paradigms globally, technological advancements have reduced the incidence of pure wrought iron creation in favor of more contemporary materials that mimic its benefits while offering increased ease of production.
Pros of Wrought Iron
- Superior Ductility: Wrought iron can be drawn into thin wires or hammered into sheets without fracturing, making it ideal for artistic and architectural endeavors.
- Higher Tensile Strength: Compared to cast iron, wrought iron has notably higher tensile strength, making it more resistant to tension and less prone to brittle failure under stress.
- Corrosion Resistance: The presence of slag fibers embedded within wrought iron provides inherent resistance to rusting, making it suitable for outdoor furnishings and structures exposed to weather elements.
- Weldability: Wrought iron can be easily welded, joined, or fashioned at high temperatures, facilitating intricate designs and allowing for easy repairs.
- Aesthetic Appeal: The grain-like appearance resulting from slag fibers gives wrought iron a unique texture, enhancing the visual appeal of metalwork pieces.
- Recyclability: Wrought iron can be reheated and reshaped multiple times without significant loss in quality, making it environmentally friendly and economically viable.
- Inherent Strength and Finesse: Wrought iron is inherently strong yet capable of showcasing delicate finesse in design, making it an enduring material often associated with heritage and timelessness.
Cons of Wrought Iron
- Labor-Intensive Production: The production process of wrought iron is labor-intensive, involving manual work at high temperatures, resulting in longer production times compared to other metals like cast iron.
- Susceptibility to Corrosion: Despite its durability and corrosion resistance, wrought iron can corrode in consistent high-moisture environments, requiring maintenance such as painting or galvanizing to prevent rust.
- Rarity and Higher Costs: Wrought iron is becoming increasingly rare due to declining manufacturing methods, making it challenging to find and comparatively more expensive than other metals like mild steel. This scarcity leads to higher costs associated with both the material itself and the craftsmanship required for manipulation.
- Weight: Wrought iron is heavy, which can pose handling difficulties in transportation and installation processes, particularly for large-scale structures or design elements.
- Brittleness at Low Temperatures: While strong under tension, wrought iron can exhibit brittleness at low temperatures, potentially leading to failure when subjected to sudden or intense impacts.
- Quality Concerns in Recycled Material: Existing wrought iron, often recycled multiple times over decades or centuries, may have inconsistent quality compared to newly-manufactured counterparts, where control over composition ensures uniformity across batches.
Applications of Wrought Iron
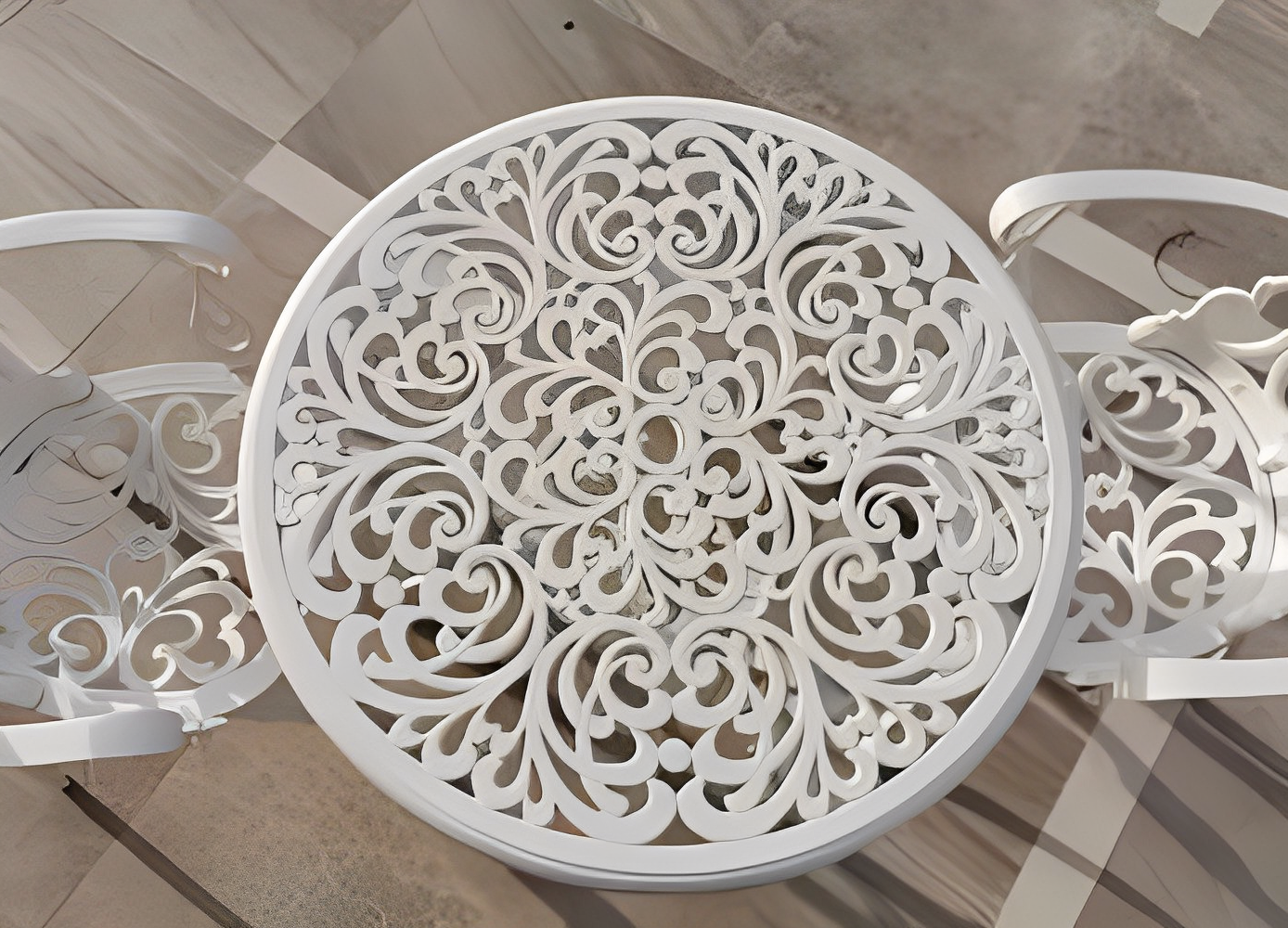
Wrought iron, due to its malleability and toughness, has found applications in a variety of areas. Historically revered for its use in the crafting of intricate designs, wrought iron lends itself well to decorative and architectural elements. Commonly seen in fencing, gates, and railings, it brings an element of elegance alongside security and durability. Not only limited to outdoor uses, wrought iron is also prevalent in interior design; it's utilized for ornamental furniture like bed frames, tables, chairs, and light fixtures – each piece bearing the distinctive mark of skilled craftsmanship.
In the realm of construction, wrought iron’s tensile strength makes it a preferred material for structures that require a certain aesthetic without compromising integrity. Historical buildings often feature wrought iron beams and columns which speak to its longevity. It's especially popular for restoration projects where maintaining the authentic look is paramount.
In addition to structural uses, wrought iron’s appeal extends to art as well. Artists elect this medium for sculptures because it can be heated and worked into complex shapes that capture the viewer's imagination yet withstand the test of time.
Landscaping is another domain where wrought iron products shine – garden trellises, arbors, benches designed from this metal integrate seamlessly with nature while adding an air of sophistication. Furthermore, owing to its resistance against corrosion when properly treated, these items maintain their appearance despite being exposed to various weather conditions.
Overall, the versatility and classic beauty of wrought iron continues to make it a sought-after material in both functional objects and artistic creations.
What is Cast Iron?
Cast iron is a group of iron-carbon alloys with a carbon content greater than 2%. Its usefulness derives from its relatively low melting temperature. The alloy constituents affect its color when fractured: white cast iron has carbide impurities which allow cracks to pass straight through, while grey cast iron has graphite flakes which deflect a passing crack and initiate countless new cracks as the material breaks.
Historically, cast iron has been manufactured by heating iron ore and melting it in a blast furnace. The liquid cast iron is then poured into molds to create shapes such as pipes, cookware, and machinery parts. The high carbon content of cast iron, which generally ranges from 2-4%, makes it very hard and brittle. Due to its brittleness, cast iron is not suitable for forging or bending; instead, it is known for its compressive strength and ability to be cast into intricate shapes.
Since cast irons are susceptible to rusting when exposed to moisture, they often undergo various surface treatments such as painting or coating to improve corrosion resistance. The presence of silicon also helps form the usually protective surface-layer of graphite that impedes oxidation.
In summary, cast iron is an alloy prized for its ability to be molded into complex formations and for its utility in producing heavy-duty components in several industries. Despite being hard and fragile due to the high carbon content, it remains a fundamental material in applications where tensile strength can be sacrificed for compression resistance and shape diversity.
Pros of Cast Iron
- Exceptional Durability: Cast iron is highly durable, capable of withstanding wear, pressure, and damage, contributing to its longevity in various applications from cookware to architectural elements.
- Efficient Heat Retention and Distribution: Cast iron efficiently retains and evenly distributes heat, particularly valuable in culinary applications where consistent temperature maintenance is essential for even cooking.
- Resistance to High-Temperature Deformation: Cast iron maintains stability and structural integrity when exposed to thermal stress, resulting in less warping or cracking over time compared to other metals.
- Cost-Effectiveness in Production: Cast iron's low production cost is attributed to fewer steps and less energy required for production, thanks to its lower melting point, allowing for ease of casting into complex shapes and enabling mass production at a reduced cost.
- Natural Non-Stick Properties: Cast iron develops natural non-stick properties through seasoning, making it an excellent choice for cooking surfaces without the need for synthetic coatings.
- Recyclability: Cast iron can be melted down and reformed into new products repeatedly without a significant loss in quality, highlighting its commendable recycling capabilities.
Cons of Cast Iron
- Heavyweight: Cast iron is comparably heavier than other cookware materials, making handling cumbersome, especially with larger pots or pans. Sturdy shelving is required for storage to support its weight, and transportation can be challenging.
- Susceptibility to Rust: Cast iron is prone to rust when not properly seasoned or cared for, necessitating regular maintenance, including thorough drying after each wash and application of oil to preserve the protective seasoning layer.
- Slow Heating and Cooling Times: Cast iron's thermal properties lead to slower heating up and cooling down times, making quick temperature adjustments difficult during cooking processes.
- Reactivity with Acidic Foods: Acidic foods can strip away the seasoning on cast iron and potentially react with the metal if left in contact for too long, affecting both the flavor of the food and the integrity of the cookware.
- Complex Upkeep: Inexperienced users may struggle with the initial seasoning process and ongoing maintenance required for cast iron, which is critical in preventing rust and ensuring non-stick properties.
Applications of Cast Iron
Cast iron, thanks to its durability and excellent heat retention, has been a favored material in various applications. Its resistance to deformation and wearability make it suitable for the manufacturing of heavy-duty cookware such as skillets, pots, and pans which are not only long-lasting but also enhance cooking by providing even heat distribution. Cast iron cookware is renowned for its ability to maintain high temperatures making it ideal for searing meats and frying.
Beyond the kitchen, cast iron's structural strength allows it to be used in building construction, particularly in the form of beams or columns where tensile strength is paramount. Architectural elements like fences, gates, and decorative ornaments benefit from cast iron's capacity to be molded into intricate designs without sacrificing robustness. This makes it a popular choice for both functional and aesthetic components in building facades.
The automotive industry utilizes cast iron for engine blocks and cylinder heads due to its exceptional machinability coupled with resilience under high pressure and temperature conditions—factors that are critical in automotive powertrain components. Brake rotors and discs are also commonly fabricated from cast iron because of their need for temperature management during intense use.
In public infrastructure, you’ll find that manhole covers, sewer pipes, street lamps, and benches frequently utilize this versatile metal. The corrosion-resistant quality of certain types of cast iron makes them apt choices for outdoor furnishings exposed to the elements.
Industrial machinery often incorporates cast-iron parts where their sturdiness is vital for maintaining the integrity of heavy equipment under demanding operational circumstances. The usage extends to gears, bases for machinery, pump housings, valves, and pistons owing largely to its cost-effectiveness when considering the combination of durability and performance that cast iron offers.
All these varied applications showcase how integral cast iron has become across multiple industries due not only to its physical properties but also due to its adaptability into various shapes through foundry techniques.
Differences Between Cast Iron and Wrought Iron
Characteristic | Wrought Iron | Cast Iron |
---|---|---|
Manufacturing Process | Worked by repeated rolling or hammering to shape | Produced by melting iron into a liquid state and pouring into molds to solidify |
Carbon Content | Lower carbon content | Higher carbon content (usually > 2%) |
Ductility | High ductility, easily shaped and welded | Low ductility, not suitable for bending or shaping once formed |
Tensile Strength | Relatively lower | Impressive compressive strength, sturdy under heavy loads |
Appearance | Rustic aesthetic with an uneven surface | Smoother finish with potential surface imperfections from mold seams or texturing |
Corrosion Resistance | Generally better resistance due to purity | May degrade faster under corrosive environments but can last with proper maintenance |
Preferred Applications | Delicate and malleable applications | Retaining complex shapes during volume production |
Which is Better for Cooking: Cast Iron or Wrought Iron?
when it comes to cooking purposes, cast iron stands out as the superior choice due to its exceptional heat retention, even heat distribution, and the ability to develop a well-seasoned non-stick surface over time. While wrought iron offers durability and malleability, its inferior heat retention makes it less optimal for cooking methods requiring consistent temperature maintenance. Therefore, for precise temperature control and flavor enhancement, cast iron cookware is unequivocally preferred over wrought iron.
Is Wrought Iron More Expensive Than Cast Iron?
wrought iron tends to be more expensive than cast iron due to its labor-intensive production process, rarity, and craftsmanship involved. Cast iron production is more automated and can be carried out at a higher volume, leading to lower costs. Additionally, wrought iron's superior weathering characteristics and unique aesthetic contribute to its premium pricing. Overall, consumers can expect to pay more for wrought iron products compared to cast iron ones.
In Conclusion
In conclusion, while both wrought iron and cast iron are forms of carbon-rich iron alloys, they exhibit significant differences in their composition, manufacturing process, and applications due to their distinct physical properties.
To make informed decisions for your construction or design needs, take these differences into account. We invite you to get in touch with our expert team for further guidance on choosing the right type of iron for your project.