The Role of Metal Cast Ball Mill Liners in Optimizing Mineral Grinding Efficiency
In the competitive world of mineral processing, maximizing the efficiency of milling operations is essential to maintaining profitability and operational sustainability. Ball mills, as one of the core machines in mineral grinding, require high-quality liners to ensure efficient and cost-effective grinding. Metal cast ball mill liners are a critical component in achieving optimized grinding efficiency, extending equipment lifespan, and reducing operational costs. This article explores how metal cast ball mill liners contribute to these objectives and the factors you should consider when choosing liners for your milling operations.
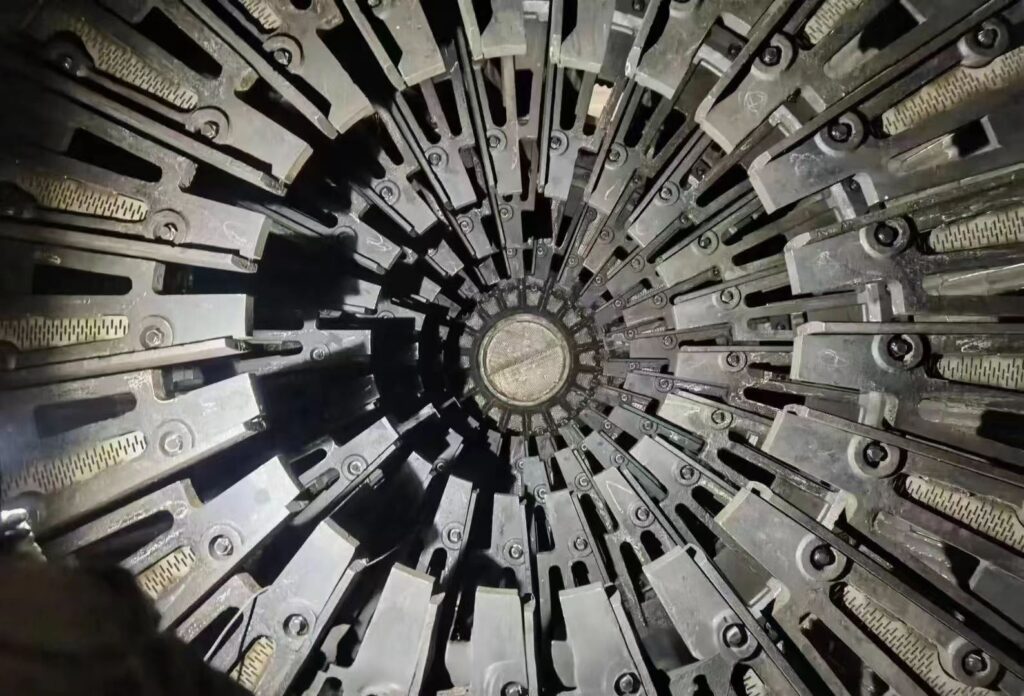
I. Introduction: The Crucial Role of Ball Mill Liners
Ball mills are widely used in the mineral processing industry to grind various ores into fine powders. These machines are pivotal in operations such as copper, gold, iron, and coal processing. However, the efficiency of a ball mill depends significantly on the quality of the liners used.
Ball mill liners serve multiple functions. They protect the mill shell from wear, improve the efficiency of the grinding process, and control the movement of grinding media (balls) within the mill. Metal cast ball mill liners, in particular, offer enhanced durability and wear resistance, which translates into longer service life and reduced downtime. As a decision-maker in the procurement process, understanding the direct impact of liner quality on your plant's efficiency and costs is crucial.
II. Enhancing Grinding Efficiency with Metal Cast Liners
The performance of your ball mill is directly tied to the quality of its liners. Metal cast liners, particularly those made from high-chromium alloys or high-manganese steel, offer several key benefits that contribute to superior grinding efficiency.
1. Wear Resistance and Longevity
Metal cast liners are designed to withstand the harsh conditions within a ball mill. The high wear resistance of materials like high-chromium cast iron ensures that the liners can endure the constant friction and impact forces generated during the grinding process. This resistance helps reduce the frequency of liner replacements, saving you both time and money. For example, plants using high-chromium liners report a 20%-30% increase in liner lifespan, reducing replacement costs and minimizing downtime. When liners last longer, you not only save on maintenance but also avoid production interruptions that can affect your bottom line.
2. Improved Grinding Action
A well-designed metal cast liner optimizes the movement of the grinding media inside the ball mill. The liner's profile, surface hardness, and overall design influence how the balls move and interact with the ore. This, in turn, affects the efficiency of the grinding process. Properly designed liners ensure that the grinding media achieves optimal impact and attrition forces, leading to better ore breakage and finer particle sizes. Research shows that mills with optimized liners can achieve 10%-15% higher throughput, resulting in a more efficient mineral processing operation.
3. Reduced Operational Costs
One of the most compelling reasons to invest in high-quality metal cast liners is their potential to lower operational costs. By enhancing grinding efficiency and reducing the frequency of liner replacements, these liners contribute to overall cost savings. Additionally, the wear resistance of these materials reduces the need for additional maintenance and ensures smoother operations. A comprehensive study in a major copper mine showed that the adoption of high-chromium cast liners led to a 15%-20% reduction in energy consumption, an essential factor given the energy-intensive nature of milling operations. Furthermore, energy-efficient grinding helps reduce your plant's carbon footprint, aligning with sustainability goals.
4. Improved Product Quality
Achieving consistent product quality is a fundamental goal in mineral processing. Metal cast liners ensure that the grinding process remains stable and efficient, which results in a more consistent and finer grind. A better grind leads to improved recovery rates in subsequent processes, such as flotation or leaching. Consistency in particle size distribution also enhances the downstream processes, ensuring that your final product meets the desired specifications.
III. Selecting the Right Metal Cast Liners for Your Milling Operations
When choosing metal cast liners for your ball mills, several factors need to be considered to ensure optimal performance.
1. Material Selection
Choosing the right material for your ball mill liners is essential. The most common materials include high-chromium cast iron, high-manganese steel, and other specialized alloys. High-chromium liners are particularly effective in reducing wear, while high-manganese liners offer better resistance to impact. The choice of material depends on the type of ore being processed, the mill's operating conditions, and the desired wear resistance.
For example, in a plant processing highly abrasive ores, high-chromium cast liners would be the preferred choice due to their superior hardness and wear resistance. On the other hand, mills handling softer ores might benefit from the impact resistance of high-manganese steel liners.
2. Liner Design and Customization
In addition to material selection, the design of the ball mill liners plays a crucial role in optimizing grinding efficiency. Custom liners tailored to your specific mill design can significantly enhance grinding performance. The profile of the liner should align with the mill's operating conditions to ensure that the grinding media is correctly directed and energy is efficiently transmitted.
Many suppliers offer customized liner designs based on your milling process. The ability to tailor the liner profile to suit specific ore characteristics can lead to up to 10%-12% improvement in mill efficiency, providing a clear edge in the highly competitive mineral processing market.
3. Cost-Effectiveness
While the upfront cost of premium metal cast liners may seem higher, the long-term savings they provide in terms of maintenance, energy consumption, and improved throughput far outweigh the initial investment. It's important to balance cost with performance, as low-quality liners may result in more frequent replacements and higher operational costs over time. A careful analysis of life-cycle costs can help determine the true value of investing in high-quality metal cast liners.
IV. Case Study: Impact of Metal Cast Liners in a Copper Mine
A major copper processing plant recently upgraded its ball mill liners to high-chromium cast liners. Prior to the upgrade, the plant experienced frequent liner replacements, leading to extended downtimes and high maintenance costs. After switching to the new metal cast liners, the plant saw significant improvements in both performance and cost-efficiency.
- Liner lifespan increased by 25%, reducing replacement costs and downtime.
- Mill throughput improved by 18%, leading to higher production rates.
- Energy consumption decreased by 15%, resulting in substantial savings on electricity costs.
This case illustrates how investing in high-quality metal cast liners can translate into tangible benefits, from improved grinding efficiency to reduced operational costs.
V. The Future of Metal Cast Liners in Mineral Grinding
The future of metal cast ball mill liners is bright, with ongoing advancements in materials and design. Innovations in alloy compositions, such as the development of composite materials, promise even greater wear resistance and durability. As the industry moves toward more sustainable practices, eco-friendly materials and manufacturing techniques will also play a role in the evolution of mill liners.
Additionally, the integration of smart monitoring technologies will allow for real-time performance tracking, enabling predictive maintenance and further optimization of grinding processes. These advancements will continue to enhance the efficiency and profitability of mineral processing operations.
VI. Conclusion
Metal cast ball mill liners play a pivotal role in optimizing mineral grinding efficiency by enhancing wear resistance, improving grinding action, reducing operational costs, and ensuring consistent product quality. For decision-makers involved in purchasing or upgrading milling equipment, investing in high-quality metal cast liners offers a clear path to achieving significant operational improvements and cost savings.
The right liners can make a substantial difference in your mill's performance, ensuring higher throughput, reduced energy consumption, and longer-lasting equipment. By considering material selection, liner design, and long-term cost savings, you can make an informed decision that enhances your plant’s profitability and efficiency.
For more information on metal cast solutions and how they can optimize your mining operations, check out our crusher cast solutions.