Pump impellers are key parts of centrifugal pumps. They help move fluid by turning the motor's energy into fluid motion. The impeller spins fast, pushing the fluid outwards. This increases the fluid's pressure and flow rate.
Knowing about different impeller types, designs, and uses is important. It helps pick the best impeller for a job. This choice boosts efficiency, cuts energy use, and shortens downtime.
Key Takeaways
- Pump impellers are a crucial component of centrifugal pumps, responsible for creating the necessary centrifugal force to move fluids.
- Different types of impellers, such as open, closed, and semi-open, are designed to handle various fluid characteristics and applications.
- Impeller selection should consider factors like material compatibility, fluid properties, and performance requirements to optimize pump efficiency and durability.
- Impeller diameter and blade design can significantly impact pump performance, flow rate, and energy consumption.
- Proper maintenance and understanding of impeller types can help improve overall pump system reliability and reduce operational costs.
What is a Pump Impeller?
A pump impeller is key in a centrifugal pump. It turns mechanical energy from the motor into kinetic energy for the fluid. The impeller spins fast, creating a force that pulls fluid into the center and pushes it outwards. This increases the fluid's pressure and flow rate.
Definition and Function
The impeller is what makes a centrifugal pump work. It spins, drawing fluid into the center and then pushing it out. This creates a pressure difference that moves the fluid through the pump and to where it's needed.
Role in Centrifugal Pumps
In a centrifugal pump, the impeller changes mechanical energy into fluid kinetic energy. This is key for the pump to create the needed pressure and flow rate. Without the impeller, the pump can't move fluids, making it vital for many uses.
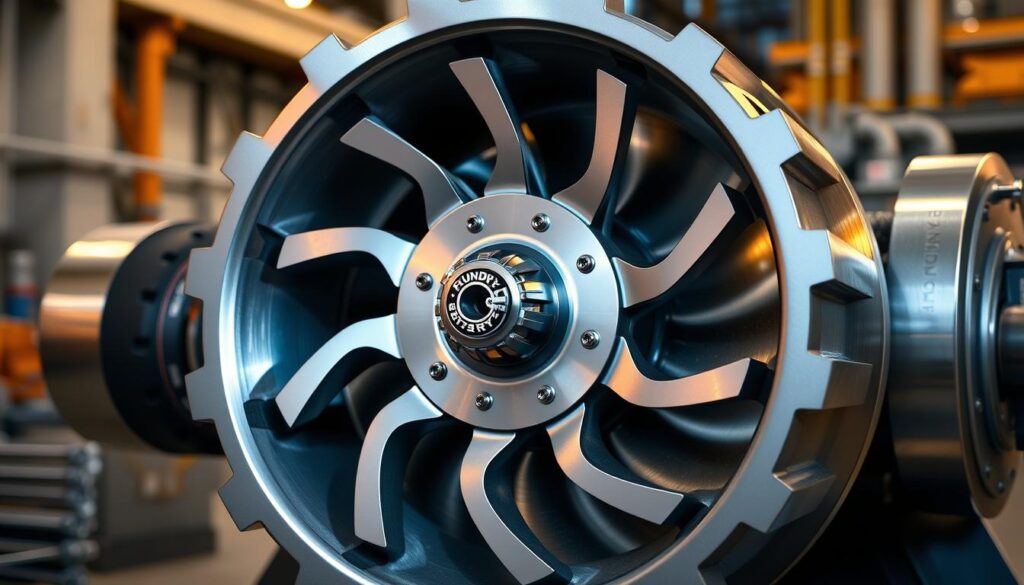
"The impeller is the heart of a centrifugal pump, responsible for driving the fluid through the system and ensuring efficient operation."
Knowing how a pump impeller works is important for picking the right one. It affects the pump's performance, energy use, and lifespan. By looking into different impellers, you can make your fluid handling system better and more reliable.
Types of Pump Impellers
Pump impellers have different designs for different needs. In the world of centrifugal pumps, three main types are open, closed, and semi-open impellers.
Open impellers are great for liquids like water or when solids need to pass through. Their design lets them handle these fluids well.
Closed impellers are best for thick liquids, like oils, or when high pressure is needed. They have a cover over the vanes to direct fluid flow.
Semi-open impellers are a mix of open and closed impellers. They work well for many applications, offering a balance between the two designs.
The right impeller type depends on the application's needs. Things like flow, pressure, and fluid properties are key in choosing.
Impeller Type | Design | Typical Applications | Advantages | Disadvantages |
---|---|---|---|---|
Open Impeller | Vanes exposed to the fluid | Low-viscosity liquids, handling solids | Efficient for low-viscosity fluids, can handle solids | Lower pressure capabilities, more susceptible to wear |
Closed Impeller | Vanes enclosed by a cover | High-viscosity liquids, high-pressure applications | Efficient for high-viscosity fluids, higher pressure capabilities | Cannot handle solids, more complex design |
Semi-Open Impeller | Partial cover over the vanes | Varied applications, balancing performance needs | Compromise between open and closed designs, versatile | May not be as efficient as fully open or closed impellers |
Knowing about each impeller type helps engineers and pump operators make better choices. This ensures the best performance and efficiency in fluid handling.
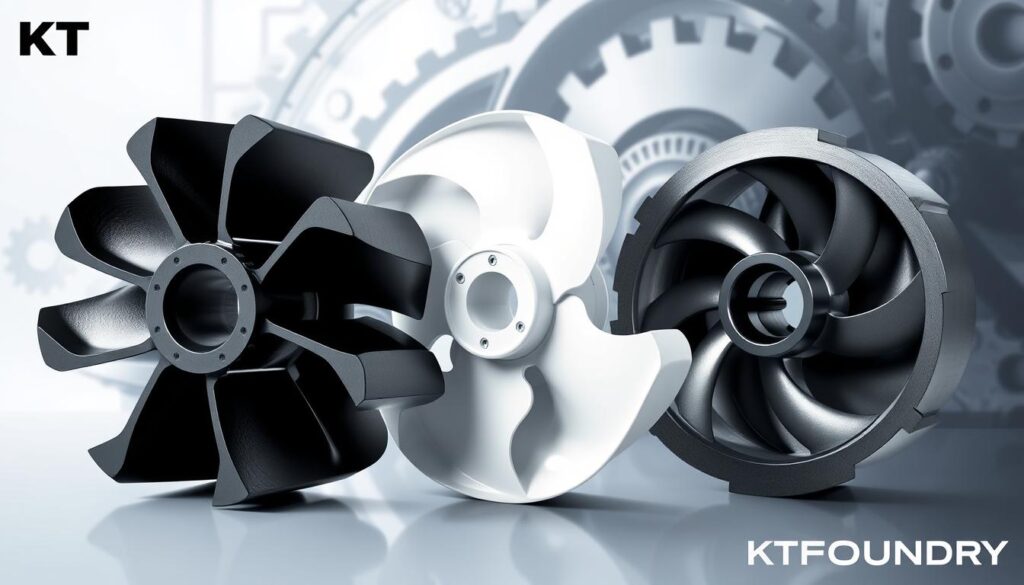
Open Impellers
Open impellers are a special kind of pump design. They have vanes attached to a central hub without a shroud. This design has many benefits for certain uses.
Design and Applications
These impellers are great for moving liquids with particles, like water. Their open design lets fluids flow through easily. This makes them popular in food, chemical, and water treatment industries.
Strengths and Weaknesses
- Easy to clean and maintain: The open design makes them simple to access and clean. This saves time and effort.
- Ability to handle suspended solids: Open impellers can pump liquids with solids well. They prevent clogs and work reliably.
- Lower efficiency: Open impellers are less efficient than closed ones. This is because of their open design.
- Suitable for low-viscosity fluids: They work well with thin liquids. Their design helps fluids flow easily.
Knowing about open impellers is key when picking a pump. Their benefits make them a top choice for handling solids and easy cleaning.
Impeller Type | Common Applications | Advantages | Disadvantages |
---|---|---|---|
Open Impeller | Food processing, chemical processing, water treatment | Easy to clean, handle suspended solids, suitable for low-viscosity fluids | Lower efficiency compared to closed impellers |
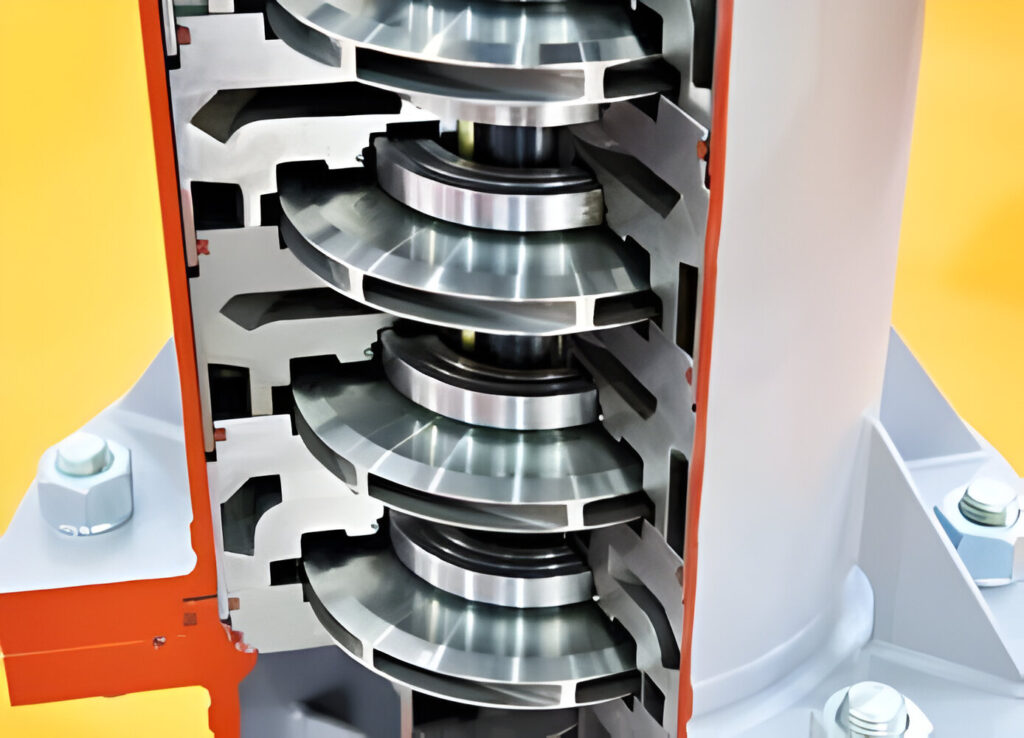
"Open impellers are the go-to choice for industries that need to handle liquids with suspended solids, as their design allows for easy passage and reduced clogging."
Closed Impellers
Closed impellers are known for their high efficiency and versatility. They have vanes surrounded by a shroud or cover. This design boosts their efficiency and lets them handle fluids with solids. They're often used in wastewater treatment, paper and pulp processing, and mining.
The closed design of these impellers has many benefits. They are the strongest type of radial flow impeller because of the two shrouds. This makes them more reliable and extends the life of bearings. They're also great for handling volatile and explosive fluids because of their tight seal.
But, their design also brings some challenges. Cleaning and maintaining closed impellers is harder than open ones. This is because you often need to take the pump apart for maintenance. This can be time-consuming and increase costs.
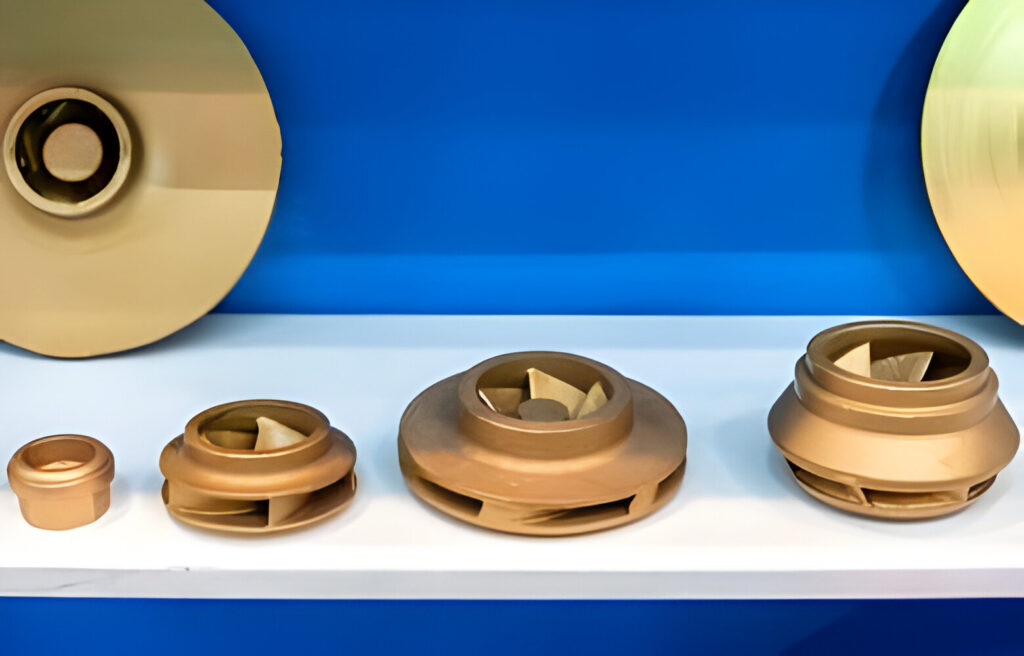
Despite these challenges, closed impellers are still a top choice in many fields. They offer high-pressure capabilities, improved reliability, and can handle fluids with low solids content. When choosing an impeller, it's key to think about the application's needs. This includes the fluid's properties, flow rates, and energy use to make the best choice.
pump impeller
Semi-open impellers are a top pick for pump designs. They mix efficiency with flexibility. These impellers have vanes on one side of a central hub, leaving the other side open. This design is great for fluids with suspended solids, needed in chemical, food, and mining industries.
These impellers have big pluses. They're more efficient than open impellers, using less energy to do more work. This means they save money over time. Plus, their open side lets suspended solids pass through, making them ideal for fluids with particles.
But, their design comes with some downsides. Making semi-open impellers is harder than open ones. They also need careful upkeep to keep working well.
Advantages | Disadvantages |
---|---|
|
|
Despite the hurdles, semi-open impellers are still a favorite in many fields. They offer a balance of efficiency and flexibility, making them crucial in various industrial settings.
Recessed Impellers
Recessed impellers are great for pumping fluids with lots of solids. They have a special design with a shroud and a central cavity. This helps them move slurries, sludges, and other liquids without getting clogged.
Recessed impellers are perfect for slurry pumping and wastewater treatment. The design creates a vortex that keeps the fluid flowing, even with lots of solids. They can handle fluids with up to 40% solids and solid spheres up to 8 inches in diameter.
However, recessed impellers use more energy than other types. They might not be the most efficient choice for every application. But, they are great for handling fluids with lots of solids.
Recessed impellers are very popular in mining, oil and gas, wastewater management, food processing, and agriculture. They are essential for these industries because they can handle fluids with high solid content. Their design prevents clogging, making them a reliable solution.
Model | Capacity | Pressure | Applications |
---|---|---|---|
PumpWorks Model PWA-RC | Up to 2,700 GPM | Up to 285 PSIG | Municipal sludges, mining tailings and slurries, food waste, crystal suspensions |
Goulds Pumps HSU and HSUL Recessed Impeller Submersible Pumps | N/A | N/A | Handling large, stringy, or fibrous materials without binding or clogging |
Recessed impellers are vital in many industries. They are key for managing fluids with high solid content. This makes them essential in a wide range of applications.
Vortex Impellers
Vortex impellers are unique in design. They have a recessed chamber that creates a vortex. This helps them handle fluids with a lot of gas well.
They are very useful in the oil and gas industry. This is because they can pump liquids with air or gas in them.
Design and Usage
The vortex design is key to their success. The recessed chamber makes a whirlpool-like action. This pulls the fluid into the pump with little contact with the impeller.
This design helps avoid clogs. It also lets the products move freely without getting stuck.
Strengths and Limitations
Vortex impellers are great at handling fluids with a lot of gas. But, they are not as efficient as other types. They can be 25-30% less efficient than non-clog designs.
This means they might need bigger motors and cost more to run. But, their ability to move a lot of fluid is a big plus.
They are especially useful in the oil and gas industry. Plumbing engineers might also choose them for places like arenas or restaurants. This is because they can handle high-gas-content liquids well.
Impeller Type | Efficiency Compared to Non-Clog Designs | Suitable Applications |
---|---|---|
Vortex Impeller | 25-30% less efficient | Oil and gas industry, sewage pumping in public places |
Non-Clog Impeller | Half the efficiency of traditional fully enclosed impellers | Potable water pressure boosters, hydronics |
"The space between the inlet and impeller in a vortex pump allows for more movement of products without clogging."
Factors to Consider in Impeller Selection
Choosing the right impeller involves several important factors. The material, the fluid's properties, and the pump's compatibility are key. Each plays a crucial role in the impeller's performance.
Material and Compatibility
Stainless steel is a top pick for impellers because it resists corrosion and heat. Bronze or cast iron impellers are also viable, depending on the application's needs. It's vital that the impeller material matches the fluid's chemical makeup for efficient pumping.
Fluid Properties
The fluid's viscosity and solids content affect impeller selection. Thicker or more solid fluids need special impellers. The pump's flow rate and head also influence the choice.
Finally, think about the cost and maintenance of the impeller. This ensures the pump works well and is cost-effective over time.
Impeller Material | Key Advantages | Typical Applications |
---|---|---|
Stainless Steel | Corrosion resistance, durability, easy maintenance | Chemical processing, water treatment, food and beverage industries |
Bronze | Corrosion resistance, strength, cost-effectiveness | Seawater applications, general industrial pumps |
Cast Iron | Affordability, wear resistance, good for high-solids applications | Wastewater treatment, mining, pulp and paper industries |
Polymer Coating | Corrosion resistance, low maintenance, cost-effectiveness | Chemical processing, water treatment, food and beverage industries |
"Selecting the right impeller material and design is crucial for the long-term performance and efficiency of a centrifugal pump."
Impact of Impeller Diameter
Flow Rate and Energy Consumption
The size of the pump impeller greatly affects its performance. A bigger impeller diameter can move more water but uses more energy. This means it costs more to run. On the other hand, a smaller impeller diameter uses less energy but can only move less water.
When choosing an impeller diameter, engineers must think about the needed flow rate and energy consumption. Finding the right balance is key to making the pump efficient and effective. This ensures it works well for the system it's in.
Impeller Diameter | Flow Rate | Energy Consumption |
---|---|---|
Larger Diameter | Higher Flow Rate | Higher Energy Consumption |
Smaller Diameter | Lower Flow Rate | Lower Energy Consumption |
Thanks to advanced techniques like those at KT Foundry, making pump impellers has changed. These methods allow for custom impeller designs. They help match flow rate and energy consumption better, boosting the pump's efficiency and performance.
"Carefully selecting the appropriate impeller diameter is crucial for optimizing pump efficiency and meeting the specific needs of the application."
Conclusion
Pump impellers are key parts of centrifugal pumps. They turn mechanical energy into kinetic energy and move the fluid. Knowing about different impellers and their designs is important for better pump performance.
Choosing the right impeller for a job is critical. It depends on the fluid, flow rate, and energy use. The right impeller can boost efficiency, cut costs, and ensure pumps work well.
Regular care and maintenance are vital for impellers. Keeping them balanced and in good shape helps them last longer. Understanding impeller types helps us make better choices for our pumps. This improves their performance and value in many industries.
At KT-FOUNDRY, we specialize in producing high-quality pump impellers that deliver outstanding performance and reliability. Leveraging years of experience and cutting-edge manufacturing techniques, we prioritize the finest material selection, precision casting, and strict quality control to ensure each impeller meets high standards of durability and corrosion resistance. Our products serve a wide range of industrial applications, and we offer customization options to meet specific project requirements, ensuring that our impellers achieve peak efficiency and longevity.
To help us better understand your needs, please fill out the form below, and we’ll provide a customized solution tailored to your specifications.