Steel is everywhere in manufacturing and engineering. It's used in many fields, like construction and the military. Alloy steel and stainless steel are two main types of steel. Knowing the difference between them is key for choosing the right steel for a project.
Alloy steel is a mix of iron and carbon with added elements like chromium and nickel. These elements boost the steel's strength and resistance to corrosion. Stainless steel, on the other hand, is famous for its ability to resist corrosion. It has at least 10.5% chromium in it.
This guide will explore alloy steel and stainless steel in detail. We'll look at their unique features and how they differ. Whether you're in manufacturing, engineering, or just curious, this article will help you make better choices for your projects.
Key Takeaways
- Alloy steel and stainless steel are two distinct types of steel with unique properties and applications.
- Alloy steel is enhanced with various alloying elements to improve mechanical properties, while stainless steel is known for its exceptional corrosion resistance.
- Understanding the composition and classification of these steel types is crucial for material selection in manufacturing and engineering projects.
- Factors like tensile strength, hardness, ductility, and corrosion resistance are important considerations when choosing between alloy steel and stainless steel.
- Alloy steel and stainless steel have a wide range of applications, from construction and automotive to aerospace and medical equipment.
Composition and Classification of Alloy Steel and Stainless Steel
Alloy Steel
Alloy steel is a special type of steel. It has more than one alloying element, besides carbon and iron. These elements boost its strength, wear resistance, and hardness.
Alloy steels are divided into two groups: high and low alloy. Low alloy steel has less than 5% alloying elements. High alloy steel has more than 5%.
Stainless Steel
Stainless steel is a high alloy steel known for its corrosion resistance and beauty. It has at least 10.5% Chromium for hardness and resistance to corrosion. It also has less than 1.2% Carbon and other elements like titanium and nickel.
Chromium in stainless steel forms a protective oxide when it meets oxygen. This self-repairing property makes it durable.
Stainless steel production is growing every year. It's valued for its versatility, durability, and cost-effectiveness. It falls into four families: Austenitic, Ferritic, Duplex, and Martensitic & Precipitation Hardening Stainless Steel.
The most common austenitic stainless steel grades are 303, 304, 316, 310, and 321. Ferritic stainless steel grades include 409 and 430. Duplex alloys include 318L, LDX 2101, LDX 2304, 2507, and 4501. Martensitic and precipitation hardening steels include 410 and 420.
Stainless Steel Family | Magnetic Response | Work Hardening Rate | Corrosion Resistance | Hardenability | Ductility | High Temperature Resistance | Low Temperature Resistance | Weldability |
---|---|---|---|---|---|---|---|---|
Austenitic | Non-magnetic | Very high | Very high | None | High | High | High | Very high |
Ferritic | Magnetic | Medium | Medium | None | Medium | High | Low | Low |
Duplex | Magnetic | Medium | Very high | Low | Medium | Medium | Medium | High |
Martensitic and Precipitation Hardening | Magnetic | Medium | Medium | High | Low | Low | Low | Low |
Alloy steel has 1–50 wt% additional elements to enhance its properties. High-alloy steel has more than 8% alloying elements. Low-alloy steel has less.
Most steels have less than 0.35 wt% carbon. Some, like tool steels, have more, between 0.7 and 1.5 wt%.
Alloy steel is commonly used in many areas. It's found in pipes, containers, kitchen tools, military vehicles, and construction equipment. Low-alloy steels are used in CNC machined parts and sheet-cut components for their strength and affordability.
High-alloy steels are more expensive but are chosen for their toughness, corrosion resistance, and strength. They're used in automotive, chemical processing, and power generation equipment.
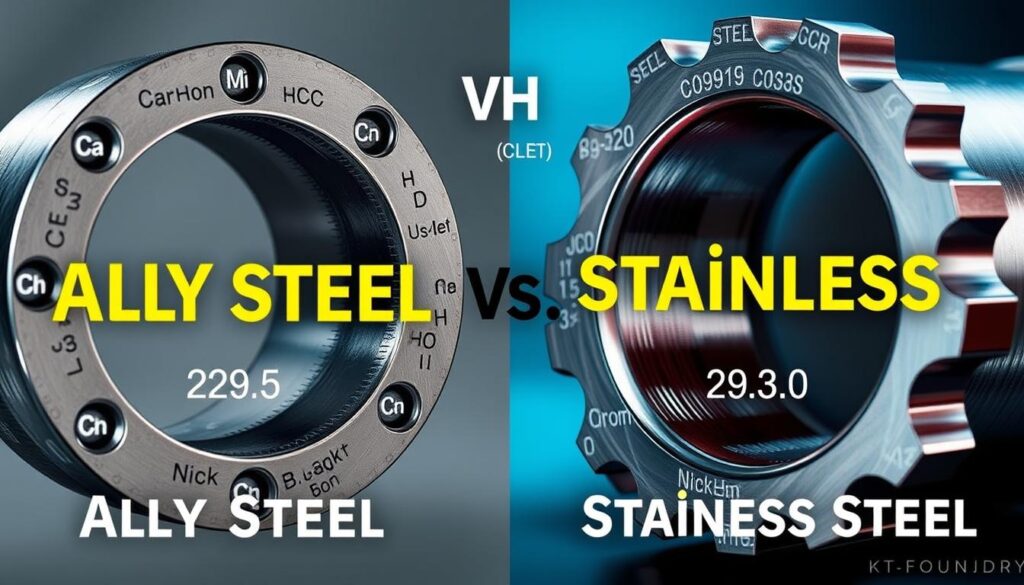
Common Alloying Elements in Alloy Steel
Alloy steel is a versatile material that can be tailored to meet various performance requirements. This is done through the strategic addition of alloying elements. These elements enhance the mechanical properties, corrosion resistance, and overall performance of carbon steel. Common alloying elements include manganese, chromium, vanadium, nickel, and tungsten.
Manganese makes the steel alloy less brittle and more malleable when added in small amounts. Chromium can increase hardness at small percentages or enhance corrosion resistance at higher percentages.
Vanadium, present in about 0.15% of the alloy, increases strength, heat resistance, and grain structure. Nickel, at about 5% addition, increases the strength of the steel. Over 12% nickel enhances its corrosion resistance. Tungsten increases the structural makeup and heat resistance of the steel alloy.
These alloying elements, when combined in specific proportions, create a wide range of alloy steel grades. Understanding their roles is crucial in selecting the right alloy steel for various applications.
Alloying Element | Effect on Alloy Steel |
---|---|
Manganese (Mn) | Increases malleability and reduces brittleness |
Chromium (Cr) | Enhances hardness and corrosion resistance |
Vanadium (V) | Improves strength, heat resistance, and grain structure |
Nickel (Ni) | Increases strength and corrosion resistance |
Tungsten (W) | Enhances structural makeup and heat resistance |
By carefully selecting and balancing alloying elements, steel manufacturers can create alloy steel grades tailored to various industries and applications.
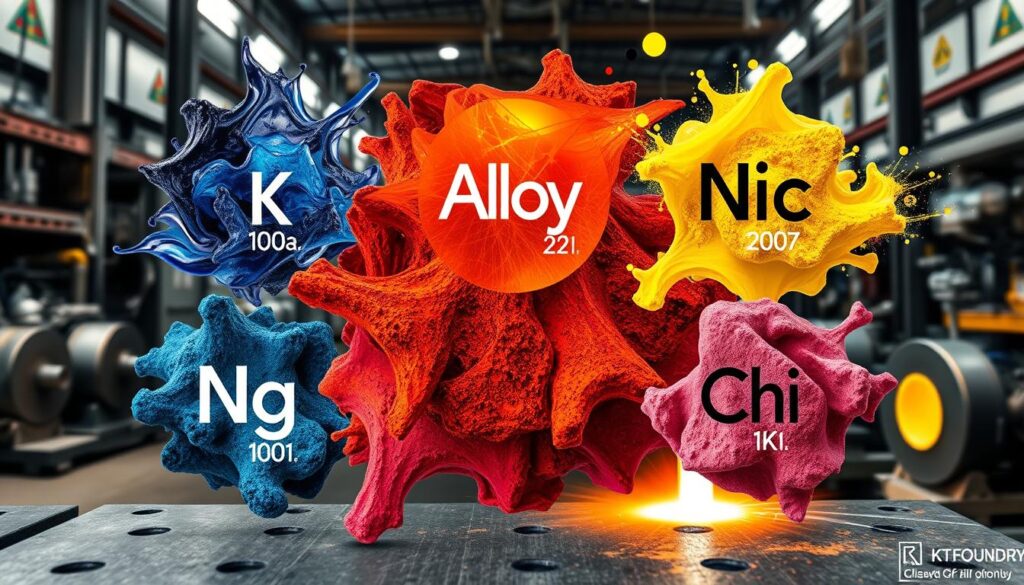
Types of Stainless Steel
Stainless steel is versatile and widely used. It comes in several types, each with its own benefits and uses. Let's look at the main categories of stainless steel and what makes them special.
Austenitic Stainless Steel
Austenitic stainless steel, like 304 and 316, is very common. It has 17-25% chromium and 8-20% nickel. This makes it strong, resistant to corrosion, and easy to weld. It's also non-magnetic and can be shaped easily, making it great for many uses.
Ferritic Stainless Steel
Ferritic stainless steel, such as 409 and 430, has about 10.5% chromium. This gives it good corrosion resistance. However, it's not as tough as other steels and is mainly used in sheet and coil form.
Martensitic Stainless Steel
Martensitic stainless steel, like 410, 420C, and 431, has 12-16% chromium and 0.08-2% carbon. It can be hardened through heat treatment. But, it's harder to weld and not as flexible as other types.
Duplex Stainless Steel
Duplex stainless steel, such as 2205 and S32750, has a mix of austenite and ferrite. It has 18-29% chromium, 3-8% nickel, and other elements. It's very strong and resistant to corrosion. But, it can't be heat-treated and is not good for cold working.
Precipitation-hardening Stainless Steel
Precipitation-hardening stainless steel, like 17-4 PH and 15-5 PH, has 12-16% chromium and 3-9% nickel. It's heat-treatable and can be strengthened. It's strong, ductile, and easy to machine, making it versatile.
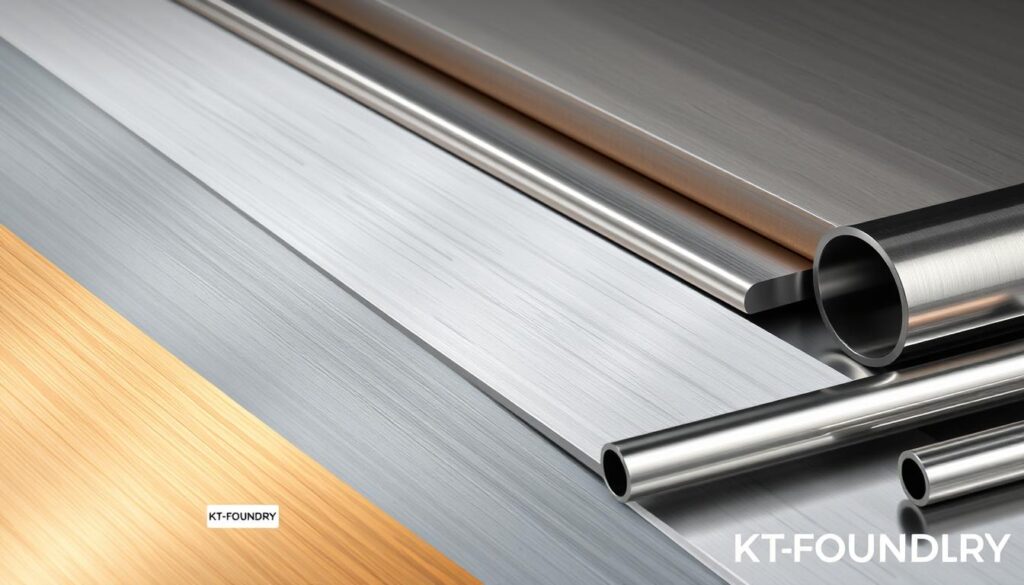
Each type of stainless steel has its own strengths and uses. Choosing the right one is key for any project. Knowing the differences helps engineers and manufacturers make the best choice for their needs.
Mechanical Properties: Alloy Steel vs. Stainless Steel
Alloy steel and stainless steel have different mechanical properties. This makes each material better for certain uses. Let's look at what makes them unique.
Tensile Strength
Alloy steel is stronger than stainless steel. It has a tensile strength of 758-1882 MPa. Stainless steel's strength is 515-827 MPa. This is why alloy steel is better for strong structures.
Hardness
Hardness shows how well a material resists wear and abrasion. Alloy steels are harder, with a range of 200HB to 600HB. Stainless steel is softer, with a range of 150HB to 300HB. This makes alloy steels better for wear-resistant applications.
Ductility
Ductility is how much a material can stretch without breaking. Alloy steels are more ductile than stainless steel. This is good for making precise shapes without breaking.
Impact Resistance
Alloy steels are also better at handling impacts. Their higher hardness means they can withstand shocks better. Stainless steel is more likely to break under impact.
Fatigue Strength
Fatigue strength is how well a material handles stress over time. Alloy steels generally have better fatigue strength than stainless steel. But, some stainless steel types, like duplex, are very strong in this area.
In short, alloy steels are stronger, harder, and more ductile than stainless steel. They're great for applications needing these qualities. Stainless steel, however, is excellent at resisting corrosion. This is why it's often chosen for many industrial and commercial uses.
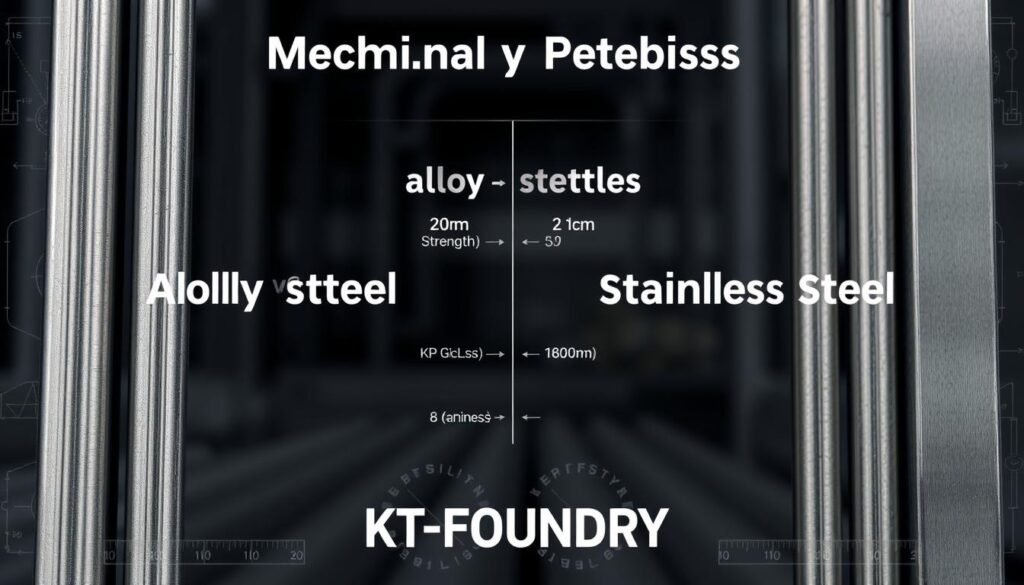
Corrosion Resistance: Alloy Steel vs. Stainless Steel
Stainless steel is far better at resisting corrosion than alloy steel. This is because stainless steel has a lot of chromium. This chromium creates a protective layer on the metal's surface. This layer keeps the steel safe from harmful elements.
Alloy steel also has chromium, nickel, and copper. But it doesn't resist corrosion as well as stainless steel does.
Pitting and Crevice Corrosion
Stainless steel is better at fighting off pitting and crevice corrosion. These are types of corrosion that can happen in certain spots. They can cause small, deep holes in the metal.
Stainless steel's high chromium content helps keep its protective layer strong. This makes it less likely to get damaged by these types of corrosion.
Galvanic Corrosion
Galvanic corrosion happens when one metal causes another to corrode. It needs a metal anode, cathode, and an electrolyte. Alloy steel is more likely to get damaged by galvanic corrosion than stainless steel.
Corrosion Resistance Comparison | Alloy Steel | Stainless Steel |
---|---|---|
Pitting and Crevice Corrosion | More susceptible | More resistant |
Galvanic Corrosion | More susceptible | More resistant |
Overall Corrosion Resistance | Moderate | Excellent |
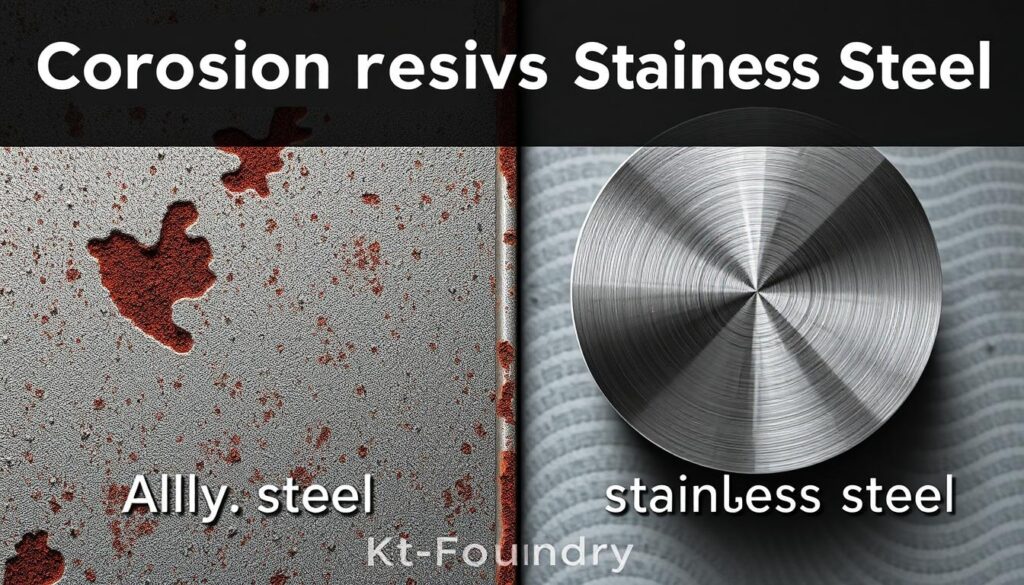
In short, stainless steel is much better at fighting corrosion than alloy steel. It can handle pitting and crevice corrosion and galvanic corrosion well. This makes stainless steel last longer and be more durable in harsh environments.
Alloy Steel vs. Stainless Steel: Strength and Durability
Choosing between alloy steel and stainless steel depends on what you need in terms of strength and durability. Alloy steel is the clear winner when it comes to being tough and lasting long. It's made to handle heavy use and last a long time.
Alloy steel is special because it has elements like nickel, molybdenum, and chromium. These help it stay hard, even when it's hot. This makes it perfect for jobs that need a lot of strength. Stainless steel is good at fighting off corrosion, but it's not as strong as alloy steel, especially in hot-rolled products.
But, stainless steel is better at keeping things looking good and staying free from rust. It's great for places where moisture or chemicals are a problem. Even though it's not as strong as alloy steel, it's still a good choice for many projects.
So, whether to use alloy steel or stainless steel depends on what your project needs. Alloy steel's unmatched strength and durability are perfect for tough tasks. Stainless steel's ability to resist corrosion is great for places where chemicals are a concern.
"Alloy steel is generally more robust and long-lasting than stainless steel, thanks to its unique composition and superior mechanical properties."
Applications of Alloy Steel and Stainless Steel
Alloy steel and stainless steel are used in many industries. They have different benefits based on their properties. Alloy steel is strong and durable, making it great for cars, buildings, tools, and oil rigs. Stainless steel, with its ability to resist corrosion, is often used in kitchens, medical tools, and chemical plants.
Choosing between alloy steel and stainless steel depends on what you need. Consider the strength, corrosion resistance, environment, and cost. For example, alloy steel is better for high-strength needs. But stainless steel is better at handling heat in some cases.
Application | Alloy Steel | Stainless Steel |
---|---|---|
Automotive Parts | Gears, axles, crankshafts | - |
Construction | Bridges, buildings | - |
Tools and Dies | Tool and die manufacturing | - |
Oil and Gas Industry | Equipment and components | - |
Food Processing | - | Equipment and utensils |
Medical Devices | - | Surgical instruments |
Chemical Processing | - | Tanks, piping, and equipment |
Architecture | - | Facades, structural elements |
Kitchen Appliances | - | Cutlery, cookware |
Choosing the right material is key for success. Whether it's stainless steel in kitchens or alloy steel in cars, the right choice affects performance and cost.
Machinability and Weldability
Alloy steel is easier to machine than stainless steel. This is because alloy steel is softer and doesn't harden as much when cut. This makes tools last longer, speeds up machining, and improves the finish.
Stainless steel, especially the tough austenitic grades, is harder to machine. It can wear down tools faster and make machining slower. But, some stainless steels like SS 303 and SS 416 are easier to work with.
Machinability
The ease of machining depends on hardness, toughness, and how well it conducts heat. Here's how alloy steel and stainless steel compare:
Characteristic | Alloy Steel | Stainless Steel |
---|---|---|
Machinability | Generally easier to machine, especially in the annealed condition | Can be more challenging to machine due to work-hardening, particularly the austenitic grades |
Cutting Speed | Higher cutting speeds possible | Lower cutting speeds often required to avoid excessive tool wear |
Tool Life | Longer tool life | Shorter tool life due to increased wear |
Surface Finish | Easier to achieve better surface finishes | May require more careful machining to prevent surface defects |
Weldability
Both alloy steel and stainless steel weld well, but with some differences. Alloy steel might need heating before or after welding to avoid cracks. Stainless steel, especially the austenitic types, welds well but needs special care to avoid problems during welding.
"Stainless steel is a popular material option for metal manufacturing, used in applications ranging from cookware to automotive components to chemical processing equipment."
Cost Comparison: Alloy Steel vs. Stainless Steel
Choosing the right material for metalworking is all about cost. Alloy steel is often cheaper than stainless steel. The price of alloy steel changes based on the mix of elements used. Stainless steel, on the other hand, costs more because of its high chromium and nickel content.
Stainless steel might cost more upfront, but it's worth it for long-term use. Its durability and resistance to corrosion make it a smart choice for certain industries. Even though it's pricier, its benefits can save money in the long run.
Property | Alloy Steel | Stainless Steel |
---|---|---|
Cost | Generally less expensive than stainless steel | Typically more expensive due to higher alloying content |
Corrosion Resistance | Moderate to high, depending on alloying elements | Excellent due to the presence of at least 10.5% chromium |
Strength | High, especially for high-carbon alloy steels | Moderate to high, depending on the specific grade |
Weldability | Generally easier to weld than stainless steel | Requires more careful welding techniques |
Choosing between alloy steel and stainless steel depends on your needs. Consider the cost, corrosion resistance, strength, and weldability. By understanding these materials, businesses can make better choices for their metalworking.
Alloy Steel vs. Stainless Steel
Both alloy steel and stainless steel are key in the industrial world. Alloy steel is strong and affordable, perfect for where strength matters most. Stainless steel, with its ability to resist corrosion, is ideal for clean and rust-free environments.
Alloy steel gets its strength from elements like chromium and nickel. It's stronger and more durable than regular steel. It's a favorite in construction and manufacturing for its toughness and price.
Stainless steel stands out for its fight against corrosion. It's a top pick for places needing to stay clean and rust-free. It's used in food, medicine, and even cars for its looks and durability.
Attribute | Alloy Steel | Stainless Steel |
---|---|---|
Strength | High | Moderate |
Corrosion Resistance | Moderate | Excellent |
Cost | Lower | Higher |
Machinability | Good | Moderate |
Weldability | Good | Moderate |
Choosing between alloy steel and stainless steel depends on what you need. Consider strength, corrosion resistance, environment, and budget. This helps industries pick the best material for their projects.
Conclusion
At KT-FOUNDRY, we have the skills to find the perfect steel for your project. Our team will help you pick the right alloy steel or stainless steel. We aim to meet your specific needs, whether it's for strength or resistance to corrosion.
Introduce our advantages in manufacturing and guide customers to contact us
We use advanced methods and know a lot about steel. Our modern facilities and skilled workers mean top-quality products every time. Reach out to us to see how we can help with your next project.
We're dedicated to giving you the best steel solutions at a good price. Our experts are ready to find the best material for you. Contact us to talk about your project and see how we can help you succeed.