Cast iron is a very old and versatile metal, used in many areas like construction and plumbing. It's made mostly of iron, carbon, and silicon. These materials make cast iron strong and good at handling heat. But, like all metals, cast iron can rust, which can weaken it and cause problems like leaks and bursts.
In this guide, we'll look closely at cast iron corrosion. We'll talk about why it happens and how to stop or fix it. Knowing the causes and how to prevent them can help keep cast iron, especially in plumbing, working well for a long time.
Key Takeaways
- Cast iron pipes can last between 75 to 100 years with proper maintenance.
- Corrosion in cast iron pipes can lead to water discoloration, reduced water pressure, leaks, and pipe bursts.
- Preventive measures like coatings, linings, and cathodic protection can mitigate cast iron corrosion.
- Regular inspections and proactive maintenance practices are crucial for detecting and addressing cast iron corrosion issues.
- Extensive corrosion may require cast iron pipe repair or replacement with alternative materials like PVC.
Introduction to Cast Iron and Its Properties
Composition and Manufacturing Process
Cast iron is a strong and versatile material used for centuries. It's mainly iron, carbon, and silicon, with small amounts of other elements. The carbon in cast iron is between 2% and 5%, making it different from steel.
To make cast iron, iron ore is heated with coke and limestone in a blast furnace. This process removes impurities and creates molten iron. The iron is then poured into molds to shape it. Different types of cast iron, like grey and white, have unique carbon levels and structures.
Advantages of Cast Iron
Cast iron is loved for its durability, resistance to corrosion, and ability to reduce noise. It also handles heat well and is cost-effective. Its hard structure makes it great for many uses, from historic markers to stoves and pipes.
Cast iron also forms a protective layer after it's made. This layer helps it resist corrosion better than metals like wrought iron or mild steel.
Type of Cast Iron | Carbon Content | Key Characteristics |
---|---|---|
Grey Cast Iron | 2.5% to 4% | Graphite flakes distributed throughout the metal, providing good machinability and vibration dampening. |
White Cast Iron | 1.8% to 3% | Carbon is chemically combined as carbide of iron, making it extremely hard and brittle. |
Ductile Cast Iron | 3.2% to 4% | Spheroidal graphite particles provide higher strength and toughness compared to grey cast iron. |
Malleable Cast Iron | 2% to 3% | Obtained by heat-treating white cast iron, making it less brittle and more malleable. |
Cast iron's variety and properties make it useful in many fields. It's used in pipes, automotive parts, and decorative items.
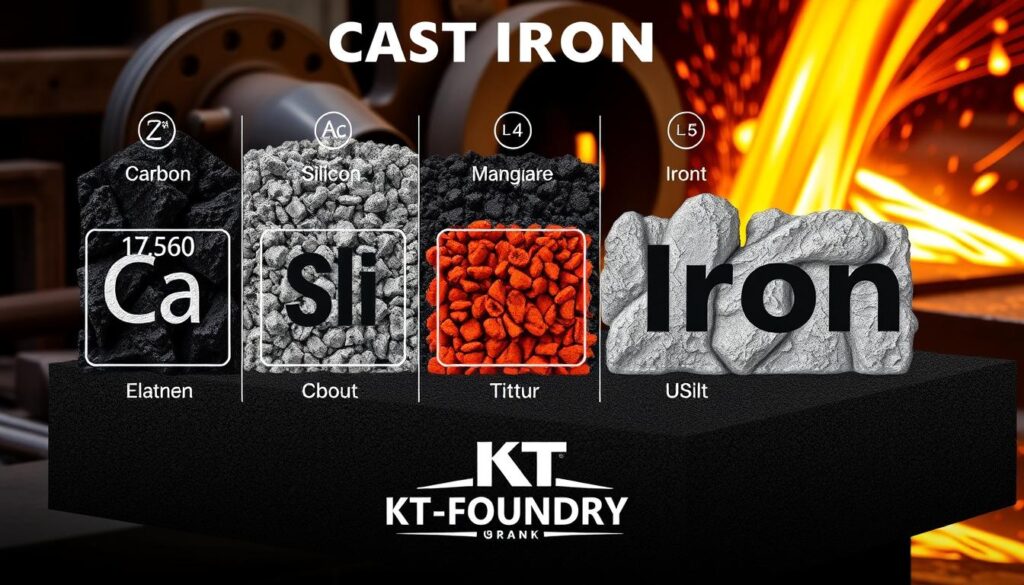
Common Uses and Applications of Cast Iron
Cast iron is a versatile and durable material used for centuries. It has high compressive strength and is good at casting. These qualities make it popular for many uses.
Cast iron is often used in automotive components. This includes engine blocks, cylinder heads, and gearbox cases. Its ability to handle high temperatures and durability make it perfect for these parts.
- It's also used in construction for columns, balusters, stairs, and connectors. This is because of its strength and durability.
- In plumbing, cast iron pipes are long-lasting and resistant to corrosion. They've been used for centuries.
- Decorative features like historic markers and fences often use cast iron. It's chosen for its beauty and durability.
- Cast iron is also popular in tools and utensils, especially in cooking. It retains heat well, making it great for searing and baking.
Application | Advantages of Cast Iron |
---|---|
Automotive Components | High compressive strength, good casting ability, wear resistance, and ability to withstand high temperatures |
Construction | Durability, strength, and aesthetic appeal for columns, balusters, stairs, and structural connectors |
Plumbing | Longevity and corrosion resistance for pipes and fittings |
Decorative Features | Durability and aesthetic appeal for historic markers, hardware, fences, and firebacks |
Tools and Utensils | Heat-retaining properties for searing, blackening, and baking in the culinary industry |
Cast iron's versatility has made it a key material in many industries. It's used in cars, buildings, and even cooking. Its value and practical uses are clear across different sectors.
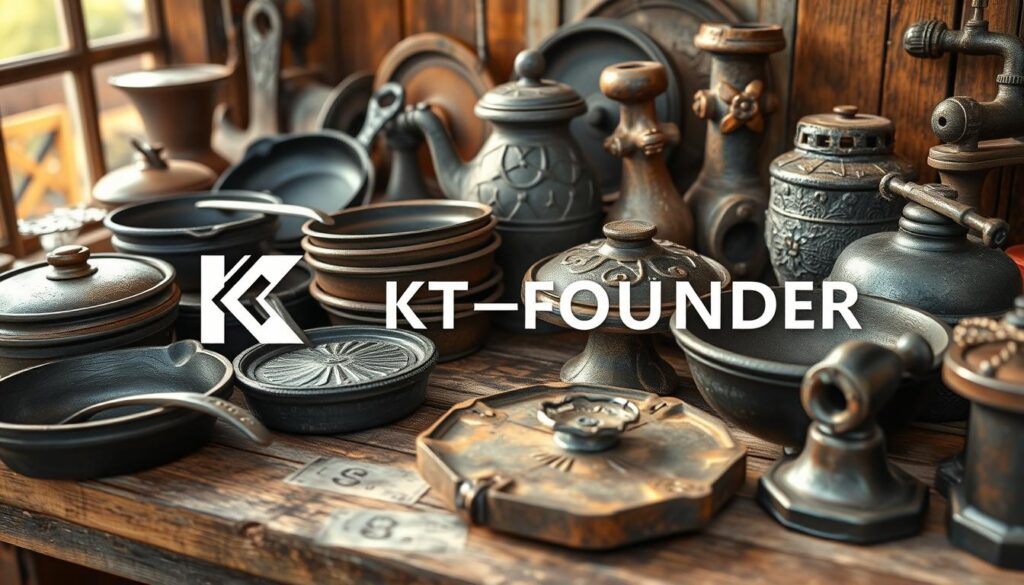
Understanding Corrosion in Cast Iron
Cast iron is a strong and versatile material used in many industries, like the water sector. But, it's very prone to corrosion. This can weaken its structure and shorten its life. It's key to know how corrosion happens and what affects its speed to fight it effectively.
Mechanisms of Cast Iron Corrosion
Cast iron corrodes mainly through a simple oxidation process. This starts when it meets air and water. The metal can then keep breaking down until it's gone. The high carbon in cast iron also leads to graphite formation, causing more corrosion, especially in certain conditions.
Factors Affecting Corrosion Rate
- Protective Coatings: The protection offered by coatings or linings on cast iron greatly impacts corrosion speed.
- Moisture Levels: Moisture in the air or water affects corrosion, with more moisture speeding it up.
- Water Chemistry: The water's pH, alkalinity, and oxygen levels also play a part. Higher alkalinity and less oxygen can slow corrosion.
- Soil Conditions: The soil's type and corrosiveness can also influence corrosion speed. Acidic or salty soils tend to cause faster damage.
Grasping these factors is vital for fighting cast iron corrosion. It helps keep cast iron parts lasting longer and ensures cast iron pipes and other key systems work well.
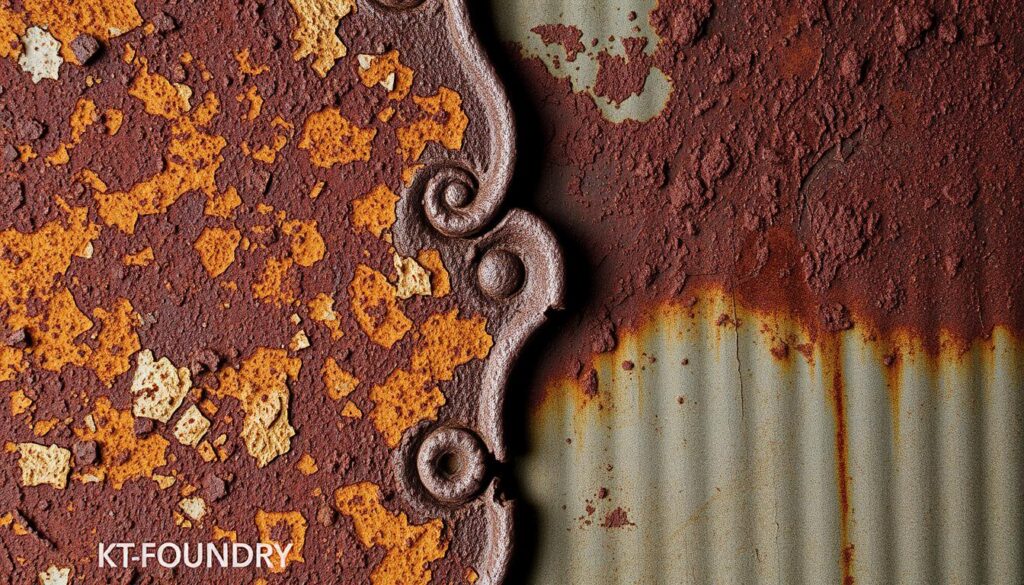
Material | Corrosion Resistance | Service Life (years) |
---|---|---|
Steel | Best in buried bare conditions | 50+ |
Gray Cast Iron | Requires no external coating for 50+ years | 50+ |
Ductile Cast Iron | Similar to steel in severely corrosive soil | 50+ |
Rusting: The Primary Form of Cast Iron Corrosion
Rusting, or oxidation, is the most common and easily recognizable form of cast iron deterioration. Cast iron, a ferrous alloy, is highly susceptible to rusting when humidity levels exceed 65%. In the presence of water vapor (H2O), iron combines with oxygen (O) to form rust. This rust is a characteristic orange-colored surface coating that can be scaly or powdery in texture.
The presence of rust shows that some of the original iron material has been lost. This corrosion process can be sped up by various environmental factors. These include sea water, salt air, cements, plasters, ashes, sulfur, soils, and acids.
Factors Accelerating Cast Iron Corrosion | Impact on Corrosion Rate |
---|---|
Sea water | Significant increase |
Salt air | Significant increase |
Cements, plasters, ashes | Moderate increase |
Sulfur | Moderate increase |
Soils | Moderate increase |
Acids | Significant increase |
Rusting can be a big problem for cast iron pipes. It can cause cracks, holes, and eventual pipe failure if not fixed. Regular inspections and proactive maintenance are key to fighting cast iron rust. They help keep cast iron plumbing systems in good shape.
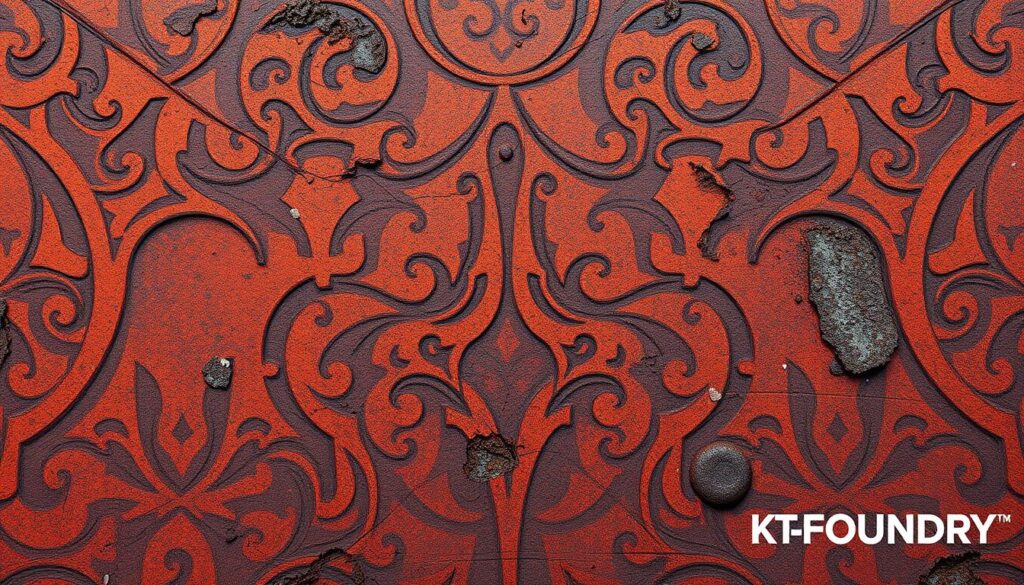
"Rust can accelerate the deterioration of cast iron pipes, potentially leading to cracks, holes, and leaks."
cast iron corrosion
Cast iron is known for its strength and flexibility. Yet, it faces a special kind of corrosion called graphitic corrosion or graphitization. This happens when non-alloy cast iron meets medium acid or soft water. The high carbon in cast iron helps this process, as graphite forms and causes corrosion.
Graphitization works slowly, making it hard to spot. It creates a layer of iron oxide with graphite on the surface. This layer keeps the shape of the cast iron, even as it corrodes.
Cast iron parts in aerated and alkaline water systems at room temperature last well. This is thanks to their thickness and moderate corrosion. This means graphitization might not be a big problem in some cases, if the water and environment are right.
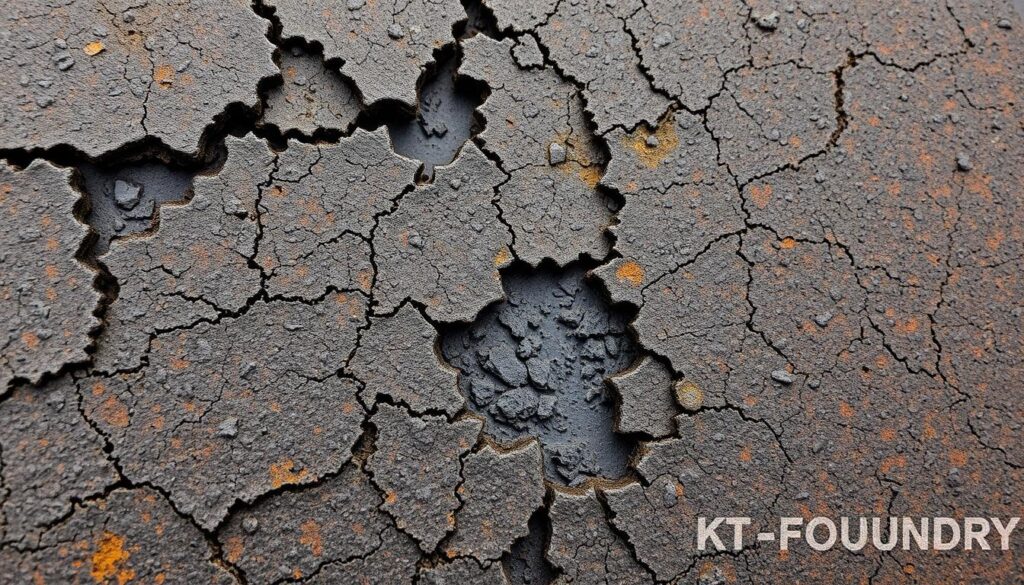
But, cast iron's weakness to graphitic corrosion is a big deal. Knowing how it works and taking steps to prevent it is key. By doing this, we can make cast iron last longer and work better in many places.
Preventing and Mitigating Cast Iron Corrosion
Cast iron is a strong and versatile material used in many places. It's found in plumbing and industrial machines. But, like other metals, it can rust, causing problems and extra costs. Luckily, there are ways to stop or slow down cast iron corrosion.
Protective Coatings and Linings
Using protective coatings and linings is a common way to keep cast iron safe from rust. In the old days, cast iron pipes were lined with simple varnish. Now, we use better stuff like cement or plastic to block rust.
For the outside, we put on a thick bituminous coating. We also add extra protection like zinc spray or cathodic protection at the joins.
Environmental Control
Controlling the environment is key to preventing cast iron corrosion. Regular checks and proper cleaning can help a lot. Keeping humidity low and avoiding corrosive substances also helps.
By using protective coatings, linings, and controlling the environment, we can prevent and mitigate cast iron corrosion. This keeps cast iron assets working well for a long time.
"Proper maintenance and the right protective measures are key to ensuring the long-term performance and safety of cast iron components."
Inspection and Maintenance Practices
Keeping cast iron pipes in good shape is key for reliable plumbing. Regular checks and care help avoid corrosion and costly repairs. Let's look at the important steps in this process.
Regular Inspections
It's wise to check cast iron pipes every five years, or more often for older systems. Inspections include looking at the outside, using video to see inside, and testing the pipe's strength. They also check for corrosion spots. Based on what they find, plumbers can suggest fixes, like small repairs or replacing parts of the pipe or all of it.
Water Treatment and Drainage Care
Good care, like regular checks and avoiding harsh chemicals, helps cast iron pipes last longer. Using softeners to stop mineral buildup and non-corrosive cleaners also helps. By being proactive with inspection and maintenance, you can keep your plumbing system working well for a long time.
"Maintaining cast iron plumbing systems necessitates regular inspections at least once every five years."
Regular checks and care are crucial for a durable cast iron plumbing system. By being quick to address problems, you can dodge expensive corrosion and water treatment issues. This ensures your plumbing stays efficient for many years.
Cast Iron Pipe Repair and Replacement Options
Homeowners and property owners have many ways to fix corroded cast iron pipes. The damage's size and location decide the best fix.
For small problems like leaks or cracks, epoxy lining or pipe patching can work well. Pipe relining is also an option for small issues. It puts a new lining inside the old pipe.
- Epoxy lining: A strong coating for the pipe's inside to stop leaks and corrosion.
- Pipe patching: Using clamps, rubber sheets, or kits to fix small cracks or holes.
- Pipe relining: A new, smooth lining inside the old pipe to fight corrosion.
But, for big cast iron pipe corrosion problems, you might need to replace the whole pipe. This means taking out the bad parts and putting in new ones, maybe even PVC.
Choosing between cast iron pipe repair or replacement needs a pro plumber's help. They can check the pipes and suggest the best fix. This ensures your plumbing system works well for a long time.
"Accurate Leak and Line recommends against spot repairs for cast iron piping systems due to the inevitability of full deterioration post leakage detection."
Conclusion
Cast iron is a strong and lasting material used for ages in building and plumbing. But, it can rust, which can cause serious damage and even break pipes if not fixed. Knowing how cast iron corrosion works and what makes it worse is key to stopping it.
Regular checks, good water treatment, and drainage care can help keep cast iron pipes going strong. If cast iron pipe corrosion gets bad, fixing it with epoxy lining, patching, or replacing the pipe might be needed. This keeps the plumbing system safe and working well.
Knowing about cast iron's special traits and common problems helps homeowners and professionals take care of it. Taking steps to prevent cast iron corrosion and being ready for repairs or replacements is crucial. This protects the value and function of cast iron structures.
Our company's experience in manufacturing cast iron
At our company, we have spent years perfecting cast iron manufacturing, focusing on durability and resistance to corrosion. Environmental factors like moisture, pollutants, and salt can cause cast iron to deteriorate if not properly treated. Through extensive research, we’ve identified key causes of corrosion and adapted our processes to minimize these risks.
We’ve developed cast iron products with enhanced resistance by using advanced coatings and materials. By embracing modern technology, we ensure our products exceed industry standards, delivering quality and reliability that our clients trust. Our commitment to innovation and precision ensures our cast iron products stand the test of time.