Producing high-quality cast parts means paying close attention to the surface finish. This is the final look and feel of the cast item's surface after it's made. It's defined by three main things: lay, waviness, and roughness.
These small differences from a perfectly flat surface are what make up the surface finish. The process of making the surface finish involves grinding or changing the cast item. This is done to get the right texture on the outside.
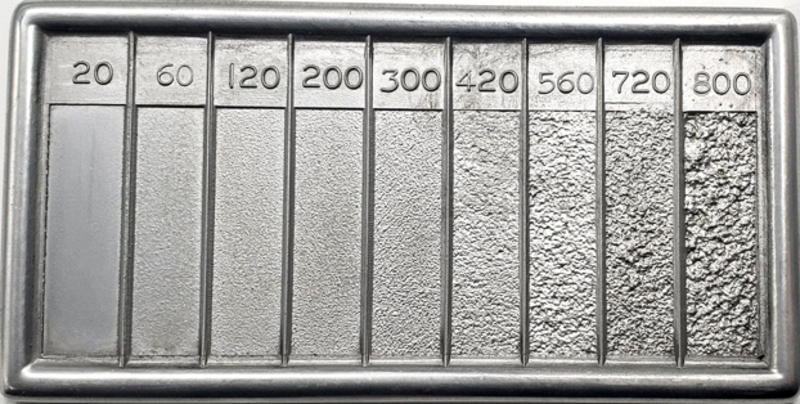
Key Takeaways
- Casting surface finish is a critical factor in producing high-quality cast parts.
- Surface finish is defined by lay, waviness, and roughness characteristics.
- Casting finishing processes, such as grinding, are used to achieve the desired surface texture.
- Surface finish can significantly impact the cost and quality of a casting.
- Understanding surface finish standards and methods is crucial for successful casting production.
Introduction to Casting Surface Finish
In metal casting, the surface finish is key. It affects how well a part works, looks, and is made. Surface finish is about the texture and look of a cast item's surface after it's made.
What is Surface Finish?
Surface finish measures how flat a surface is. It shows how well a cast part works and looks. The process of making a surface finish involves grinding or changing the surface of a cast item.
Importance of Surface Finish in Casting
The surface finish matters a lot. It can change how well a part works, like how it wears or resists corrosion. It also affects how the part looks. A smooth surface can make the part look better. Plus, it can make finishing operations like painting easier and cheaper.
Casting Process | Typical Surface Finish Range (RMS) |
---|---|
Shell Sand Casting | 75-150 |
Vacuum Casting | 150-200 |
Diecasting and Squeeze Casting | 20-150 |
Knowing about surface finish is important. It helps manufacturers and designers make parts that work well, look good, and are cost-effective.
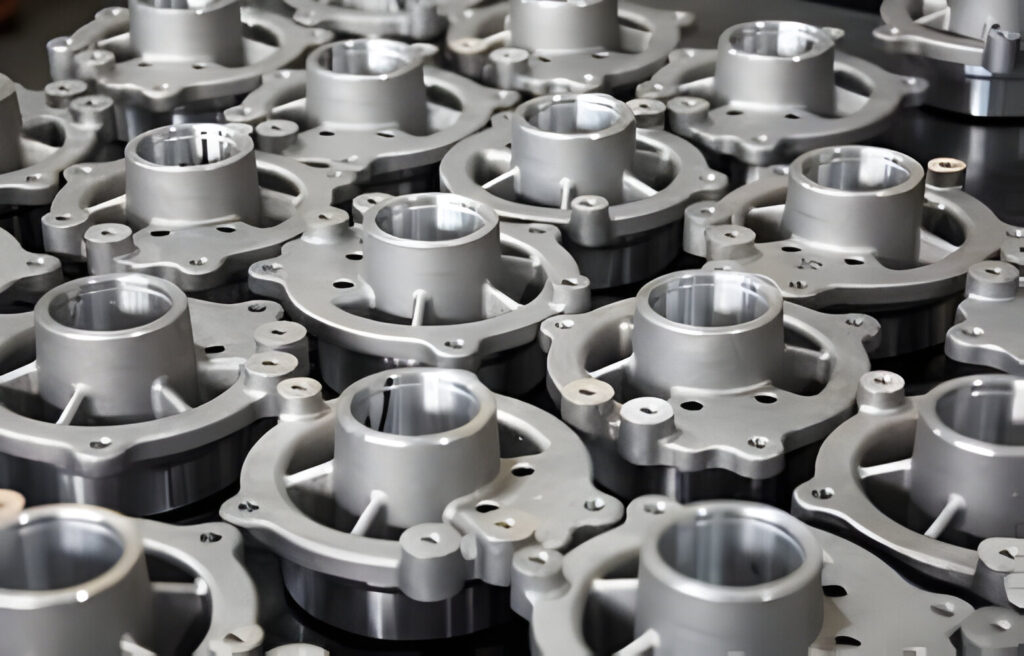
Factors Affecting Casting Surface Finish
The way a part is cast, the materials used, and the choice of alloy are key. Different methods like sand casting, shell mold casting, vacuum casting, and die casting, can change the finish.
Casting Process
The casting process greatly affects the finish. For example, die casting's pressure and temperature control matter a lot. Sand casting's mold design and venting also play a role in the part's smoothness.
Molding Materials
The type of molding materials used, like sand, shell, or investment, also matters. The size of the grains, how well they let air pass through, and how well they wet the surface can all impact the finish.
Alloy Selection
The alloy selection is crucial for the finish. Metals like aluminum, iron, and steel have different melting points and how they flow into the mold. This affects the surface quality.
Casting Process | Molding Materials | Alloy Selection |
---|---|---|
Sand Casting | Silica Sand | Aluminum, Iron, Steel |
Shell Mold Casting | Resin-Bonded Sand | Aluminum, Zinc, Magnesium |
Vacuum Casting | Ceramic Shells | Stainless Steel, Titanium |
Die Casting | Metal Molds | Aluminum, Zinc, Magnesium |
Knowing how the casting process, materials, and alloy choice affect the finish helps manufacturers. They can then make parts that meet the needs of various industries, like automotive, aerospace, consumer electronics, or medical equipment.
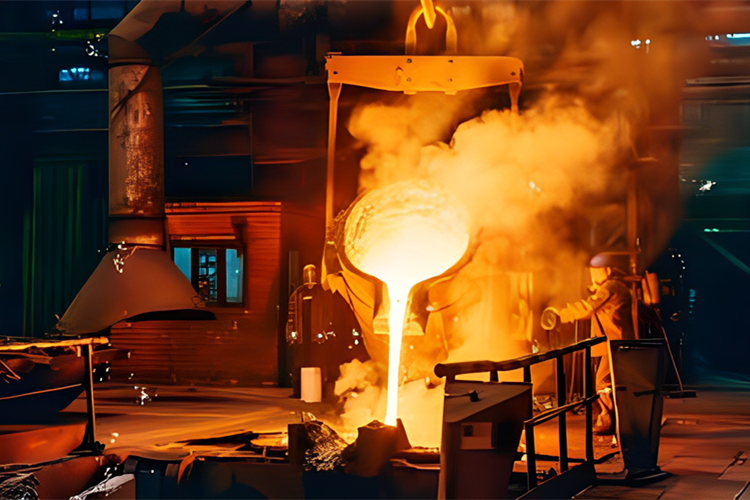
Casting Finishing Methods
There are many ways to get the perfect finish for cast parts. From sand casting to vacuum casting, each method has its own benefits. They all need special finishing steps to reach the best tool quality and die maintenance.
Sand Casting
In sand casting, fettling and linishing are key to remove extra material. Shot blasting and peening are used to smooth out the surface. They get rid of sand and imperfections.
Shell Mold Casting
Shell mold casting usually gives a smoother finish than sand casting. But, parts might still need secondary machining and polishing to meet exact finish needs.
Vacuum Casting
Vacuum casting makes parts with very smooth finishes. This is because it casts in a controlled, bubble-free environment. Still, extra finishing can make parts look and work even better.
Die Casting
Die casting is very precise and can make parts with great finishes. But, sometimes, parts need more work like abrasive blasting, secondary machining, and polishing to get the perfect casting finishing methods.
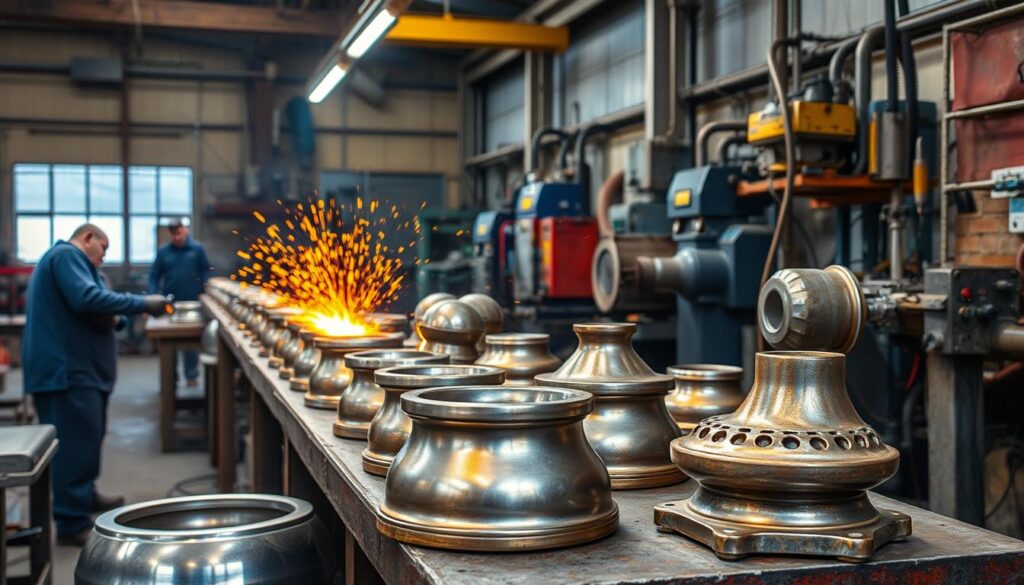
Measuring Surface Roughness
In manufacturing, knowing and measuring surface roughness is key. It ensures parts are of high quality and work well. The main way to measure this is through Ra, or Roughness Average.
Ra shows the average height difference of a surface from its mean line. It's a simple number used to decide if parts are good enough. But, there are other ways to measure surface roughness too.
Ra (Roughness Average)
Ra is the most common way to measure surface finish. It shows the average height difference from the mean line. In the U.S., this is measured in micro-inches. Internationally, it's in micrometers.
Other Surface Roughness Parameters
While Ra is popular, other measurements offer more details:
- Rz (Mean Roughness Depth): Shows the average height of peaks and valleys.
- Rp (Maximum Peak Height): Measures the highest peak's height.
- Rv (Maximum Valley Depth): Shows the deepest valley's depth.
- Rmax (Maximum Roughness Depth): The biggest peak-to-valley height.
- RMS (Root Mean Square): A measure of overall surface roughness.
Knowing these parameters helps in accurately measuring surface roughness. This is crucial for quality in manufacturing.
Surface Roughness Parameter | Description | Typical Range (Microinches) |
---|---|---|
Ra (Roughness Average) | Arithmetic mean of the absolute values of the surface height deviations | 8 - 63 |
Rz (Mean Roughness Depth) | Mean of the maximum peak-to-valley heights | 40 - 160 |
Rp (Maximum Peak Height) | Height of the highest peak from the mean line | 20 - 80 |
Rv (Maximum Valley Depth) | Depth of the deepest valley from the mean line | 20 - 80 |
Rmax (Maximum Roughness Depth) | Maximum peak-to-valley height within the evaluation length | 40 - 160 |
RMS (Root Mean Square) | Root mean square of the surface height deviations | 8 - 80 |
Understanding these surface roughness parameters helps manufacturers improve their processes. This ensures their products are of high quality.
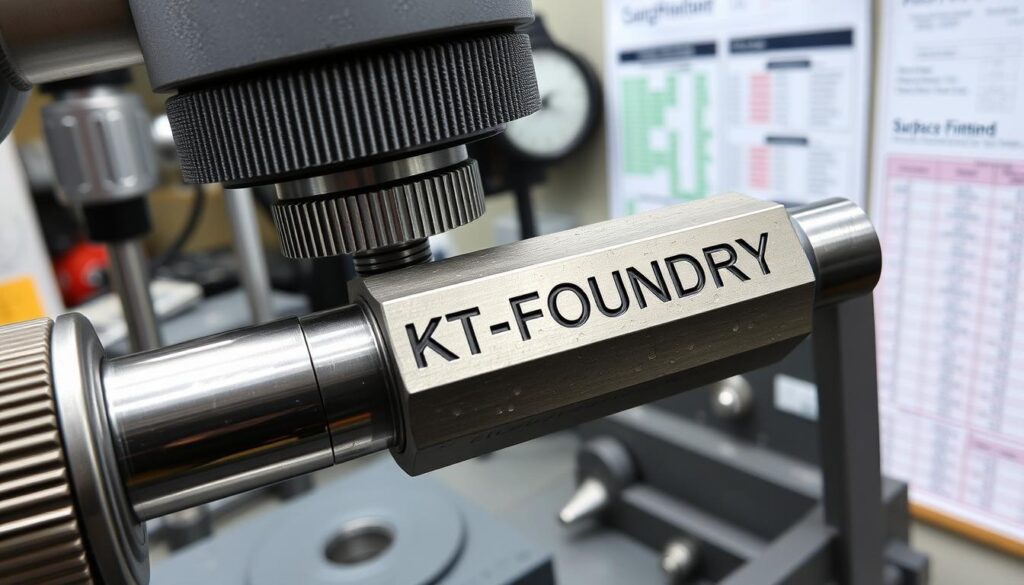
Standard Surface Finishes in Casting
In the casting industry, we see many standard surface finishes. These finishes differ in look, feel, and how they're made. Let's look at some common ones:
- As-Machined Finish: This finish is what you get after CNC machining. It has Ra values from 3.2 μm to 0.8 μm, based on the machining tools used.
- Smooth Finish: This is made by polishing the casting. It has Ra values of 1.6 μm or less. It's great for parts that need to look sleek.
- Textured Finish: This finish is made to add interest or function, like better grip. Its Ra values range from 3.2 μm to 0.8 μm, depending on the texture needed.
- Mirror Finish: This is very smooth and shiny. It's made by lots of polishing or special techniques. Its Ra values can be as low as 0.4 μm, making it almost flawless.
- Anodized Finish: Anodizing makes a strong, protective layer on the casting. It comes in many colors. It's good for looks and also protects against corrosion.
Choosing a surface finish depends on the project's needs. Things like cost, how long it lasts, and how it looks are important. These factors help pick the right finish for a casting.
Knowing about standard surface finishes helps us make better choices. We can improve how a casting looks, works, and feels.
Casting Surface Finish
Surface finish is key in the performance and look of cast parts. A good surface finish can improve how well a part works and how it looks. It can also save money. Let's look at why surface finish matters and what's possible in investment casting.
Importance of Surface Finish in Casting Applications
The finish of a cast part greatly affects its performance. A smooth finish can make the part last longer and work better. It can also make the part look better and work more smoothly.
Achievable Surface Finishes in Investment Casting
Investment casting, or the "lost-wax process," is a precise method. It can make parts with very fine finishes. Finishes can range from 125 Ra for top-quality parts to 250 Ra for general use.
This method uses a wax pattern and a ceramic shell mold. It's great for making complex shapes with high accuracy and finish. The tight tolerances, about 0.005 inches per inch, make it perfect for precise finishes.
Investment casting is great for making parts that need a high-quality finish. It's used in many fields, like aerospace, automotive, medical, and consumer goods. This method is perfect when surface finish is very important.
Benefits of Improved Surface Finish
Improving the surface finish of cast parts offers many benefits. These include cost savings and enhancements in function and looks. By refining the casting process and using finishing techniques, makers can greatly improve their products and work flow.
Cost Savings
Casting lets makers control dimensions and surface quality well. This means they don't need to do extra work or use complex setups. This saves on labor costs, cuts down production time, and lowers overall expenses.
Castings with better finishes also have fewer defects. This includes less dislocations, cracks, and porosity. This makes quality control and rework cheaper.
Functional and Aesthetic Advantages
Better surface finishes make cast parts more functional and attractive. They have more impact strength, so they can handle heavier loads without breaking. This means they work better and last longer.
Also, a smooth, consistent surface finish makes parts look better. This is great for logos, texture patterns, and oil retention. It makes the parts more visually appealing.
By improving the casting process and using finishing techniques, makers can gain many benefits. These benefits help their profits, product quality, and customer happiness.
Surface Finishing Options
There are many ways to improve the look and feel of cast parts beyond the initial casting. These extra steps can make the parts look better and work better. They help get the surface just right, whether it's for looks or function.
Abrasive Blasting
Abrasive blasting, or shot blasting, uses sand, steel shot, or glass beads to smooth out the surface. It removes blemishes and makes the surface even. This method is great for a matte or satin finish.
Secondary Machining
Secondary machining, like CNC milling and grinding, refines the surface. It removes extra material and controls the roughness. This makes the surface smoother and more even. It's used for parts that need to be precise and look great.
Polishing
Polishing uses abrasives and buffing to make the surface shiny. It's perfect for parts that need to look like mirrors, like decorations. Polishing takes a lot of time and effort but makes the surface very smooth and attractive.
Choosing the right surface finishing depends on what you need, how the part will be used, and your budget and time. By picking the best method, manufacturers can get the perfect mix of surface quality, cost, and time for their projects.
Surface Finishing Option | Key Characteristics | Typical Applications |
---|---|---|
Abrasive Blasting |
|
|
Secondary Machining |
|
|
Polishing |
|
|
Selecting the Right Surface Finish
Choosing the right surface finish for a cast part involves several key factors. You need to balance the part's use, its functional needs, and how it looks. Also, consider the cost and the finishing methods available.
Considerations for Surface Finish Selection
The main things to think about when picking a surface finish are:
- Application requirements: Think about how the part will be used. Will it face stress, loads, or vibrations? This affects the needed surface roughness.
- Functional needs: What does the part need to do? Does it need to resist wear, protect against corrosion, or have specific friction? This might require a certain finish.
- Aesthetic requirements: What does the part need to look like? You might want a certain gloss, color, or texture. Finishing methods can help achieve this.
- Production budget: How much can you spend on casting and finishing? More advanced techniques might cost more.
Cost vs. Quality Trade-offs
When picking a surface finish, think about the balance between cost and quality. Advanced techniques like CNC machining or electroplating can give you a top-notch finish. But, they might be pricier than simpler methods like sand blasting or shot peening.
ISO 4287 sets standards for surface roughness, from 25 μm to 0.025 μm. For example, Xometry Europe offers four levels for CNC machining: 3.2 μm Ra, 1.6 μm Ra, 0.8 μm Ra, and 0.4 μm Ra. Parts under stress should not exceed 3.2 μm Ra. The finest, 0.4 μm Ra, is best for parts under high tension.
By considering the part's use, needs, looks, and budget, you can pick the best surface finish. This ensures the part meets quality and performance standards while keeping costs in check.
Surface Finish Standards and Classes
The casting industry has set up different surface finish standards and classes. These help choose the right surface finish for each use. They range from utility-grade to superior-grade finishes. Let's dive into the details of these standards and classes.
Utility Grade
The utility-grade surface finish is the simplest and most affordable option. It's best for parts that aren't seen or where looks don't matter much. This finish may have pits, scratches, or mold lines and is good for parts that need to work well.
Functional Grade
The functional-grade surface finish meets the basic needs of a part. It balances cost and looks, offering enough quality for its use. This finish is often used in parts that face stress or are structural.
Commercial Grade
The commercial-grade surface finish is for parts used in business or industry settings. It has some flaws but is okay for its use. This finish is for decorative coatings or parts seen by the public but not in high-end settings.
Consumer Grade
The consumer-grade surface finish is for parts in retail or consumer use. It has fewer flaws and is expected to look better. This finish is for parts that are shown off or handled by users.
Superior Grade
The superior-grade surface finish is the top quality in casting. It has a smooth, flawless surface. This finish is for high-end, decorative items or parts needing a premium look, like in cars, planes, or luxury goods.
Knowing these standards and classes helps manufacturers and users pick the right surface quality. They balance cost, function, and looks for their needs.
Surface Finish Standard | Utility Grade | Functional Grade | Commercial Grade | Consumer Grade | Superior Grade |
---|---|---|---|---|---|
Typical Applications | Parts not visible, functional performance is primary | Structural parts, high-stress areas | Decorative coatings, parts exposed to public | Parts in consumer or retail environments | High-end, decorative applications |
Surface Imperfections | Visible pits, scratches, mold lines | Some visible imperfections, within acceptable limits | Moderate level of visible imperfections | Fewer visible imperfections | Minimal to no visible imperfections |
Cost | Lowest | Moderate | Moderate | Higher | Highest |
Conclusion
In the world of cast parts, the casting surface finish is key. It affects cost-effectiveness, functional performance, and aesthetic appeal. Knowing the surface finish standards and techniques helps manufacturers improve their products.
The manufacturing process, molding materials, and alloy choice are crucial. They determine the surface finish quality of cast parts. Sand casting, shell mold casting, vacuum casting, and die casting are some options for different needs.
Measuring surface roughness with Ra, Rmax, Rz, and CLA is important. It helps ensure consistent quality and better performance. Using methods like abrasive blasting, secondary machining, and polishing can enhance appearance and function.
The team at KT-FOUNDRY stays updated on casting surface finish standards and best practices. We aim to provide high-quality cast parts. Our goal is to meet our clients' needs, from cost-effectiveness to functional performance and aesthetic appeal.