At KT-Foundry, we focus on creating custom wear plates for various industries. We tackle the tough challenges of asphalt plants, mining, and construction. Our goal is to make wear parts that last long and work better.
Our team uses advanced technology to make wear plates that meet specific needs. We offer chrome carbide plates for harsh conditions and self-lubricating designs to reduce wear. We aim to provide wear plate solutions that add value to our clients.
We study high-wear areas to find the best materials and designs. This ensures our wear plates are durable and efficient. Our approach helps our clients make smart choices and stay ahead in their fields.
Understanding the Evolution of Industrial Wear Protection
The journey of industrial wear protection has seen big steps forward. Material science and technology have made huge leaps. Now, industries need materials that last long and can handle tough conditions.
Modern materials, like those with chromium and manganese, have changed the game. They help make equipment last longer and work better.
The Science Behind Modern Wear-Resistant Materials
The steel industry has been key in making modern wear-resistant materials. The Bessemer Process, from 1856, made steel cheaper and more available. Adding elements like nickel, chromium, and manganese to steel made it stronger and more resistant to corrosion.
Key Developments in Wear Protection Technology
- Wear-resistant steel plates have made equipment last longer and cut down on repair costs. This is especially true for mining and heavy construction.
- High-performance wear plates offer better protection and last longer than traditional steel. They're perfect for tough environments.
- New discoveries in metallurgy and material science are leading to better wear plates. This includes nanostructured alloys and advanced coatings.
- Leading companies in wear technology are setting new standards. They have top labs and skilled teams.
Impact on Industrial Efficiency and Equipment Longevity
The impact of these advancements is huge. Wear plates in industries like mining and earthmoving save money and time. They reduce the need for new parts and repairs, and cut down on downtime.
This leads to more efficient work and longer-lasting equipment. It saves businesses a lot of money and gives them an edge over competitors.
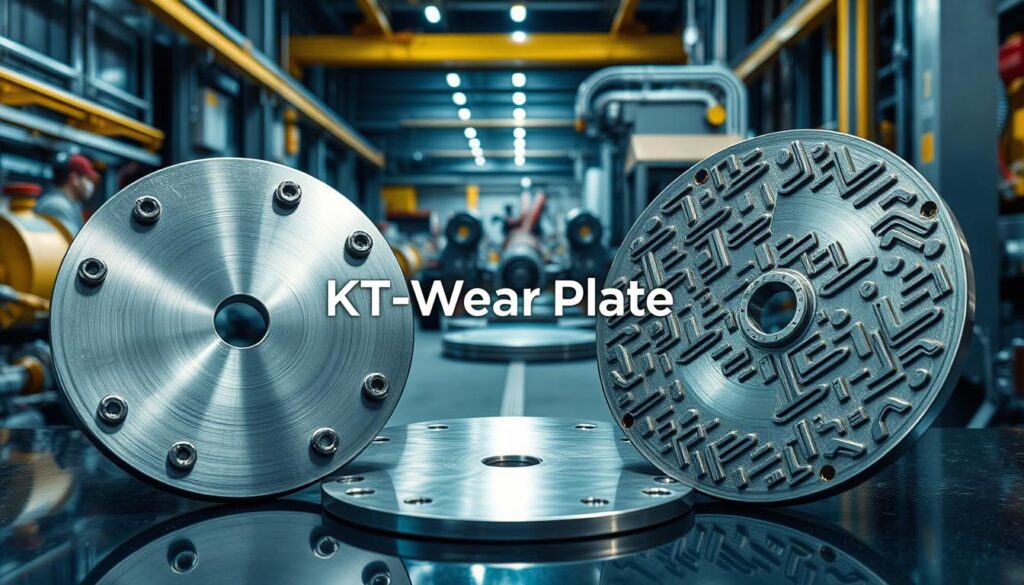
The journey of industrial wear protection is far from over. New discoveries in materials and technology keep pushing limits. As industries evolve, the need for durable and efficient wear protection will keep driving innovation.
Components and Material Composition of Wear Plates
Wear plates are made to handle tough industrial jobs. They face a lot of abrasion, impact, and wear. These parts are made from special alloys chosen for their strength.
They often have a mild steel or chromium steel base for strength. Added alloys improve hardness, toughness, and wear resistance. The Brinell hardness scale checks if they're hard enough for jobs like rolling abrasion and impact.
Material | Hardness (Brinell) | Applications |
---|---|---|
C954 Aluminum Bronze | 200-280 | Steel mills, pipe mills, aluminum mills, chemical companies |
4140QT | 320-400 | Mining, earthmoving equipment |
4340QT | 360-440 | Crushers, shredders, casting equipment |
AR400 | 400-500 | Chippers, scrapers, military applications |
AR500 | 500-600 | Earthmoving equipment, mining |
Choosing the right alloy is key for wear plates to last long. Companies in many industries use these plates to make their equipment last longer and work better.
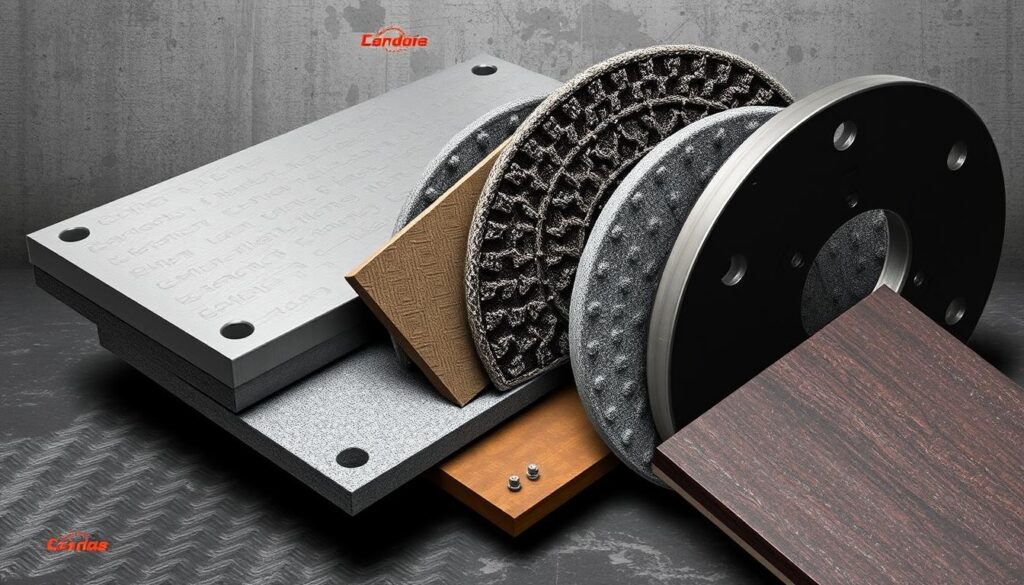
Advanced Applications Across Industrial Sectors
Wear plates are used in many industries to protect equipment and boost efficiency. They are key in mining, earthmoving, asphalt, construction, manufacturing, and processing plants. These plates help make critical equipment last longer and work better.
Mining and Earthmoving Equipment Solutions
In mining and earthmoving, wear plates are used for bucket liners, cutting edges, and loader blades. These areas are very tough and need plates that can handle a lot of wear and tear. Wear plates help equipment last longer, saving time and money on repairs.
Asphalt and Construction Industry Applications
Wear plates are also used in the asphalt and construction industries. They are used in drag lines and other areas where things get worn down fast. This helps keep equipment running smoothly and saves money by reducing downtime.
Manufacturing and Processing Plant Integration
In manufacturing and processing plants, wear plates are used in conveyor systems and mill linings. They protect against wear and tear, helping the production process run better and longer. This makes the whole operation more efficient and reliable.
Wear plates play a big role in keeping equipment safe and improving how things work. They help businesses save money and work more efficiently.
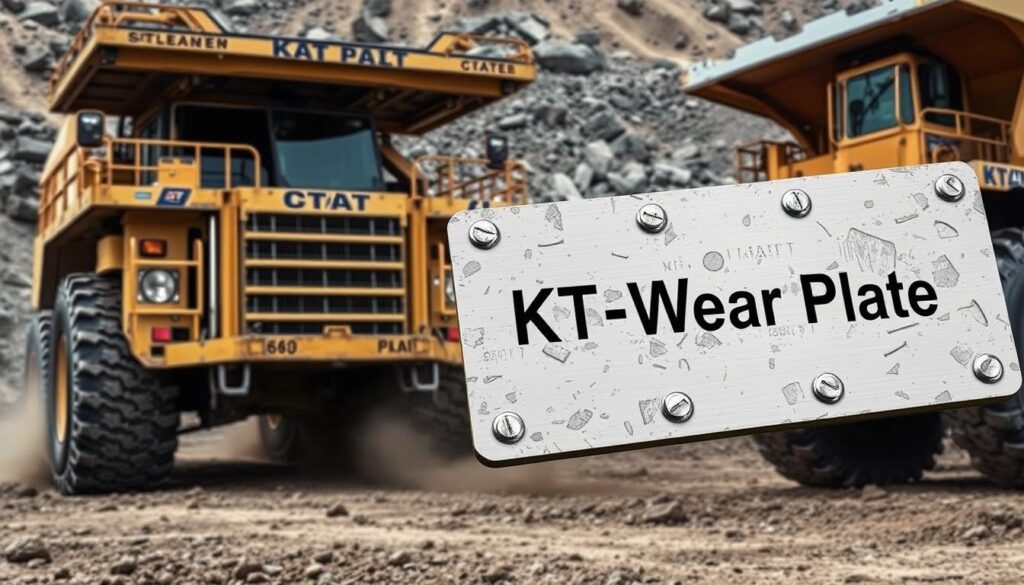
Industry | Key Applications | Benefits of Wear Plates |
---|---|---|
Mining and Earthmoving | Bucket liners, cutting edges, loader blades | Enhanced wear resistance, extended equipment lifespan, reduced maintenance |
Asphalt and Construction | Drag lines, high-abrasion pathways | Smooth material handling, improved productivity, cost savings |
Manufacturing and Processing | Conveyor systems, mill linings | Protection against wear and material buildup, enhanced reliability, efficient production |
Custom Wear Plate Solutions for Specific Needs
At KT-FOUNDRY, we're all about tailored solutions for our clients' unique needs. We start with a detailed site audit and fleet review. This helps us pinpoint the wear challenges each operation faces.
We consider things like machine type, operating conditions, and environmental factors. This way, we create custom wear plates that boost equipment life, efficiency, and cut down maintenance costs.
Our team of industrial wear consultants works hand-in-hand with clients. Together, we craft wear plates that meet their exact needs. Whether it's for mining, construction, or manufacturing, we're ready to tackle the toughest challenges.
From our cutting-edge facility, we provide a variety of custom wear solutions. This includes bi-metallic high chromium cast iron wear plates and site-specific wear parts. Our focus on quality and innovation means our clients get top-notch protection for their equipment and infrastructure.
"KT-FOUNDRY's custom wear plate solutions have been a game-changer for our mining operations. The tailored design and superior performance have significantly extended the lifespan of our equipment, improving productivity and reducing costly downtime."
- John Smith, Mining Operations Manager
Self-Lubricating Technologies and Groove Patterns
Self-lubricating technologies and groove patterns are changing wear plate design. They use graphite to reduce friction and last longer. The groove patterns help spread lubricant evenly, especially in hot and heavy-duty areas.
Graphite Integration Benefits
Graphite in wear plates makes them self-lubricating. This cuts down on friction and wear. It's great for places where it's hard to keep things lubricated, like high heat or hard-to-reach spots.
These self-lubricating technologies improve performance and cut down on maintenance costs.
Groove Design and Lubricant Distribution Systems
Custom groove patterns are key for better lubricant distribution. They spread lubricant evenly, preventing wear and ensuring consistent performance. These patterns are made for specific needs, like operating conditions and load distribution.
Performance Optimization Techniques
Wear plate solutions combine material choice and groove design for best performance. This approach, called performance optimization, matches the wear plate to the application's needs. It leads to better efficiency and less maintenance.
"Incorporating self-lubricating technologies and custom groove patterns has revolutionized the way we approach wear protection, delivering unparalleled performance and extended component lifespans."
Installation and Maintenance Best Practices
At [https://kt-foundry.com/mastering-excellence-china-casting-slurry-pump-parts/], we know how important installation and maintenance are. They help your equipment work better for longer. Our advice will help your wear plates last longer and work better.
Starting with the right installation is key. Our experts will guide you on how to fit the wear plates correctly. This way, you avoid downtime and keep your equipment running smoothly.
- Regular checks for wear are crucial for good maintenance.
- Make maintenance plans that fit your specific needs and conditions.
- Replacing parts on schedule and monitoring their condition can really help.
We want to give you the skills and tools to keep your wear plates in top shape. By following our installation and maintenance tips, you'll get the most out of our wear plate technology. This will boost your productivity and efficiency.
Maintenance Interval | Recommended Actions |
---|---|
Every 6 months to 3 years | Calibrate surface plates to ensure accuracy in measurements |
Annually or when noticeable wear is present | Rotate the surface plate's orientation to slow the formation of wear spots |
As needed | Clean the surface plate using acetone or alcohol-based cleaners to prevent water absorption |
During use | Ensure even weight distribution to avoid uneven pressure on the plate |
Ongoing | Protect the surface plate from direct sunlight to prevent quick and uneven heating |
As needed | Use a silicon carbide stone to remove burrs around scratches and nicks |
Continuously | Avoid placing food or drinks on the surface plate to prevent damage from acids |
By sticking to these best practices, your wear plates will perform well and last longer. This means less downtime and more value for your money.
Conclusion
Custom wear plates from KT-FOUNDRY are made for specific needs in industries. They offer top-notch wear protection and boost work efficiency. Our plates use advanced materials and self-lubricating tech for longer equipment life and lower upkeep costs.
As industries grow, the need for custom wear protection grows too. We're all in on making innovative, top-notch wear plates for today's industrial needs.
Our custom wear plates serve many sectors, like mining, construction, agriculture, and manufacturing. We pick the best materials and designs for better durability and efficiency. Our solutions help our clients tackle their challenges, saving them money and improving their work.
We're always looking to improve with new research and development. Our team works hard to make wear plates that go beyond what's expected. We're here to help our clients succeed in a changing world.
KT-Casting
Bring Your Designs to Reality– Experience Custom Perfection with On-Demand Casting!