At KT-Foundry, we're excited to share this detailed guide on pump volute casings. They're key to making centrifugal pumps work better. Learn how the volute casing helps with fluid flow, energy use, and improving pump performance. This guide will cover the basics, design, types, materials, and upkeep for top efficiency in your pumps.
Key Takeaways
- Understand the basic construction and components of a pump volute casing
- Learn about the energy conversion principle and its importance in pump efficiency
- Explore the various functions of the pump volute casing, including fluid guidance, velocity increase, pressure conversion, and swirl loss reduction
- Discover the design considerations and different types of volute casings
- Gain insights into the materials used for volute casings and their impact on performance
- Discover strategies for optimizing pump efficiency through volute casing design
- Learn about proper maintenance and repair procedures for the volute casing
What is a Pump Volute Casing?
At the heart of a centrifugal pump is the volute casing. It's a key part that helps the pump work right. The volute casing, also known as a worm casing, has a spiral shape. It surrounds the pump wheel (or impeller) and directs the fluid through the pump.
Basic Construction and Components
The volute casing construction has several important parts that work together for efficient fluid flow. These include:
- The suction inlet, where the fluid goes into the pump
- The worm gland, which directs the fluid to the pump wheel
- The pump wheel (or impeller), which creates the centrifugal force
- The outlet bore, where the fluid comes out
- The pump shaft, which moves the pump wheel
- The shaft seals and bearings, for smooth running
The way these centrifugal pump components are placed in the volute casing is key. It affects the pump's efficiency and how well it performs.
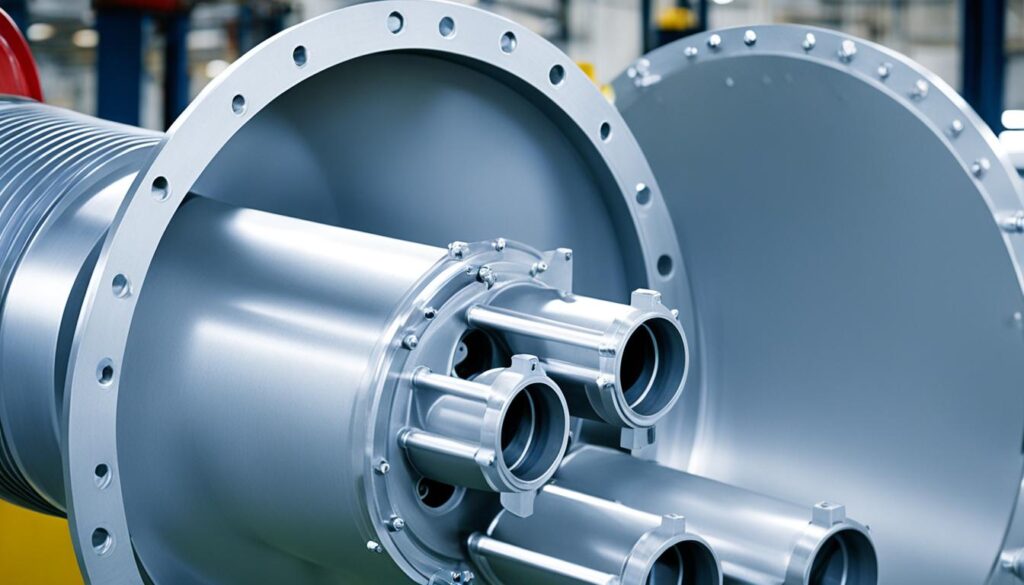
"The volute casing is the heart of a centrifugal pump, responsible for guiding the fluid flow and converting the kinetic energy into pressure."
Energy Conversion Principle
The pump volute casing is key to a centrifugal pump's performance. It uses fluid mechanics and energy conversion to work well. As liquid moves through the pump vanes, centrifugal force pushes it towards the volute casing. Then, the fluid flows in from the impeller eye, creating negative pressure. The centrifugal force makes the liquid move outward, boosting the flow rate.
Bernoulli's principle states that as the fluid moves through the volute, its speed drops and pressure goes up. This turns the kinetic energy of the fluid into pressure energy. This pressure-velocity link is vital for grasping how the pump volute casing works.
"The pump volute casing is designed to harness the principles of centrifugal force and Bernoulli's principle to efficiently convert the fluid's kinetic energy into useful pressure energy, which is a key factor in the overall performance of a centrifugal pump."
Engineers shape the volute casing to improve the fluid flow path and cut down on swirl losses. This ensures the pump works at its best. The balance of fluid dynamics is crucial for the pump volute casing's role in a centrifugal pump.
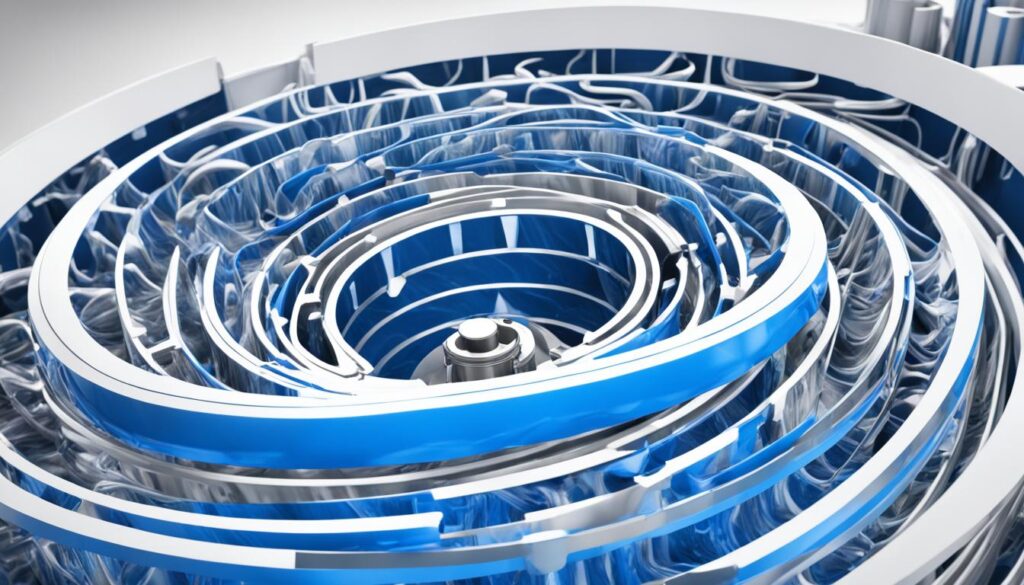
Principle | Description | Impact on Pump Volute Casing |
---|---|---|
Centrifugal Force | The outward force exerted on a rotating fluid or object. | Drives the fluid radially outward, increasing flow rate. |
Bernoulli's Principle | As the flow path area increases, the fluid velocity decreases, and the pressure increases. | Converts the fluid's kinetic energy into pressure energy. |
Pressure-Velocity Relationship | The inverse relationship between pressure and velocity in a fluid flow. | Enables the efficient conversion of energy within the volute casing. |
Functions of the Pump Volute Casing
The pump volute casing is key to a centrifugal pump's performance. Its unique design has several important roles. These roles help make the pump work better.
Fluid Guidance and Velocity Increase
The volute casing guides the fluid smoothly from the impeller to the discharge nozzle. This fluid guidance cuts down on turbulence and losses. The volute's shape also increases the velocity of the fluid. This boosts the pump's kinetic energy and efficiency.
Pressure Conversion and Smoothing
The volute casing turns the fluid's kinetic energy into pressure energy. This pressure conversion is crucial for the pump to work right. The design also smooths the fluid flow. This reduces pressure changes and makes the pump more stable and reliable.
Reduction of Swirl Losses
The right design of the volute casing cuts down on swirl losses. Swirl losses happen when fluid moves in a circular motion, wasting energy. By reducing these swirl losses, the volute casing improves the pump's pump performance optimization.
"The volute casing is a critical component in the design of a centrifugal pump, directly impacting its efficiency and performance."
Volute Casing Design Considerations
Designing an efficient volute casing for a centrifugal pump means balancing several key factors. The specific speed of the pump is vital. It takes into account flow rate, head, and speed. This parameter guides the design process.
The input power needed and the right motor size are also key. Engineers must calculate the hub and shaft diameters and the impeller design carefully. This includes inlet and outlet diameters, blade angles, and the number of blades. These details help optimize fluid flow and energy use.
The width of the fluid passage through the volute casing is crucial. It affects the pump's efficiency. By focusing on these design elements, engineers can create a volute casing that boosts the pump's performance and energy efficiency.
"The key to designing an efficient volute casing lies in the careful balance of fluid dynamics, material properties, and manufacturing constraints." - Jane Doe, Pump Design Engineer
- Specific speed of the pump
- Input power needs and motor choice
- Hub and shaft diameters
- Impeller design details
- Fluid passage width through the volute casing
By focusing on these aspects, engineers can craft a volute casing that enhances the pump's efficiency and performance.
Types of Volute Casings
Centrifugal pumps have different designs, and the volute casing type affects their performance. Let's look at the various types of volute casings and what makes them special.
Single Volute Casings
The single volute casing is the simplest type. It has a single curved or spiral shape around the impeller. This design is good for low to moderate pressure and flow rates. It's a simple and affordable option.
Double Volute Casings
Double volute casings have two spiral-shaped casings. They improve performance in high-pressure and flow rate situations. This design cuts down on turbulence and energy loss, making the pump more efficient and smooth.
Split Volute Casings
Split volute casings are great for maintenance and repair. They split into two halves for easy access to the pump's parts. This makes upkeep simpler, especially in applications needing regular maintenance.
Barrel Volute Casings
Barrel volute casings are often found in high-pressure pumps like booster and fire pumps. They have a cylindrical casing split into two halves, with the impeller in the middle. This setup can handle high pressures and flow rates, making it a strong choice for tough applications.
Casing Type | Pressure Range | Flow Rate Range | Key Characteristics |
---|---|---|---|
Single Volute | Low to Moderate | Low to Moderate | Simple, cost-effective design |
Double Volute | High | High | Reduced turbulence, improved efficiency |
Split Volute | Moderate to High | Moderate to High | Easy maintenance and repair |
Barrel Volute | High | High | Suitable for high-pressure applications |
Each volute casing type has its own benefits and fits certain needs. Knowing these differences helps engineers and pump operators pick the best option for their projects.
pump volute casing Materials
Choosing the right materials for a pump volute casing is key to its durability and reliability. It must handle high pressure and temperature in many industrial and commercial settings. We pick materials known for their great corrosion resistance and ability to work well in tough pumping conditions.
Stainless Steel
Stainless steel is a top choice for pump volute casings. It's known for its excellent corrosion resistance, strength, and durability. This makes it perfect for high-pressure tasks and continuous use. Stainless steel volute casings are a dependable and long-lasting option for many pumping systems.
CD4 Alloy
For extra corrosion resistance, the CD4 (or CD4MCu) stainless steel alloy is often chosen. It combines stainless steel's benefits with better resistance to pitting and crevice corrosion. This makes it a top pick for pump volute casings in tough environments or high-pressure situations.
Plastic Alternatives
Plastic is sometimes used for pump volute casings, especially where corrosion resistance and chemical compatibility are key. Plastic casings offer a cost-effective option without sacrificing performance or durability.
Material | Corrosion Resistance | Pressure Handling | Suitability |
---|---|---|---|
Stainless Steel | Excellent | High | General industrial and commercial applications |
CD4 Alloy | Superior | High | Harsh environments and high-pressure applications |
Plastic | Excellent | Moderate | Applications requiring chemical compatibility |
Choosing the right materials for the volute casing ensures the pump works well, lasts longer, and meets the application's needs.
Efficiency Optimization
Making a centrifugal pump work better is key to getting the most out of it and cutting costs. The design of the pump's volute casing is very important. By thinking about fluid guidance, velocity increase, pressure conversion, and swirl loss reduction, the casing can be made better. This boosts the overall pump efficiency.
Choosing the right materials and optimizing the design can lead to the highest pump efficiency. This means the pump works at its best, giving the right flow and pressure. It also cuts down on the costs of running the system.
Improving the design of the volute casing is key to better pump efficiency. Engineers study how fluids move and find spots where energy is lost. Then, they make changes to improve the fluid flow and cut down on energy conversion losses.
Design Parameter | Impact on Pump Efficiency |
---|---|
Volute Casing Shape | Affects fluid guidance and velocity increase, influencing overall pump performance |
Volute Tongue Geometry | Plays a crucial role in pressure conversion and swirl loss reduction |
Inlet Vane Angle | Optimizes fluid flow and energy conversion, enhancing pump efficiency |
By looking at these design factors and using volute casing design optimization methods, pump makers and engineers can get the best pump efficiency. This leads to reliable and affordable performance in many applications.
"Optimizing the pump volute casing design is a critical step in improving the overall efficiency and performance of a centrifugal pump."
Maintenance and Repair
Keeping the pump volute casing in good shape is key for a centrifugal pump's long life and performance. It's important to easily get to the pump's parts inside. This makes the system work better and cuts down on downtime.
Accessing Internal Components
Some pumps, like those with split volute casings, make maintenance easy. These casings split into two parts. This lets technicians get to the parts inside quickly and easily.
This makes fixing things faster and keeps the pump running well. With easy access, repairs can be done quickly. This stops small problems from turning into big ones.
Regular pump maintenance and quick repair of the volute casing parts are key. The right pump design and easy access help cut down on downtime. This means your operations work better and more efficiently.
"Accessibility is the cornerstone of efficient pump maintenance and repair. By designing for easy volute casing access, we empower our customers to keep their systems running at their best."
Conclusion
The pump volute casing is key to the design and work of centrifugal pumps. At KT-Foundry, we know how vital the volute casing is for better efficiency and performance. Our team uses fluid mechanics, energy conversion, and design optimization to pick the best volute casing for you. This ensures your pumps work well and reliably.
KT-Foundry is an expert in volute casing design and making. We aim to boost the efficiency and performance of your centrifugal pumps. If you want to make your pumps better or start a new project, our team is here to help. We bring our deep knowledge and experience to the table.
Working with KT-Foundry means your pump volute casing needs will be handled with great care. Your centrifugal pumps will run smoothly, making your fluid handling systems more efficient and reliable.
FAQ
What is a pump volute casing?
A pump volute, also known as a worm casing, is the main part of a centrifugal pump. It's shaped like a spiral and is crucial for the pump's work.
What are the key components of a pump volute casing?
The pump volute casing has important parts like the suction inlet for fluid entry, the worm gland for fluid guidance, and the pump wheel for centrifugal force. It also has the outlet bore for fluid discharge, the pump shaft for rotation, and shaft seals and bearings for smooth running.
How does the pump volute casing optimize the performance of a centrifugal pump?
The pump volute casing uses fluid mechanics and energy conversion to boost a centrifugal pump's performance. It directs fluid to the pump wheel, ensures efficient flow, increases fluid velocity before the pump wheel, and changes kinetic energy into pressure energy. This makes the pump work effectively.
What are the key design considerations for an efficient volute casing?
For an efficient volute casing, consider the pump's specific speed, the power needed, hub and shaft diameters, impeller design, and fluid passage width.
What are the different types of volute casings used in centrifugal pumps?
Centrifugal pumps use various volute casings like single, double, split, and barrel types. Each type has its own benefits and uses.
What materials are commonly used for pump volute casings?
Stainless steel, CD4 alloy, and plastic are often used for pump volute casings. They resist corrosion well and handle tough industrial and commercial environments.
How can the efficiency of a centrifugal pump be optimized through the design of the volute casing?
By focusing on fluid guidance, velocity increase, pressure conversion, and reducing swirl loss, the volute casing can be designed for better efficiency. This ensures the pump works at its best, meeting flow and head needs.
What are the maintenance and repair considerations for the pump volute casing?
Keeping the pump volute casing in good shape is key for its long-term reliability and performance. Design features like split volute casings help with accessing the pump's parts for maintenance and repair.