In the world of manufacturing, custom casting is key. It helps make many metal parts and components. From detailed jewelry to strong engine blocks, it's a flexible way to shape molten metals into precise products. This guide will explore the materials, processes, and uses of custom casting in today's industry.
Key Takeaways:
- Custom casting is a versatile manufacturing process that allows for the creation of complex metal components and parts.
- A wide range of casting materials, including aluminum alloy, brass, iron, and steel, are commonly used in custom casting applications.
- Custom casting processes, such as sand casting, die casting, and investment casting, offer unique advantages and applications in various industries.
- Advanced techniques, including melting methods and shrinkage control, continually push the boundaries of custom casting technology.
- Custom casting is an essential tool in industries like manufacturing, construction, transportation, and energy, with a promising future of growth and innovation.
Introduction to Casting Materials and Processes
Casting is a key manufacturing method. It involves pouring molten material into a mold and letting it solidify. The type of material used is very important. It affects the product's quality, performance, and use.
Materials range from metals like aluminum, steel, and brass to polymers, ceramics, and concrete. This variety makes casting materials both diverse and versatile.
Overview of Casting Materials
Metals like aluminum alloys, brass, iron, and steel are common. They are strong, durable, and resistant to corrosion. This makes them perfect for many industrial uses.
Polymer materials, such as epoxy, polyester, and silicone, are also popular. They are versatile and cost-effective. Ceramic and concrete are used in special cases where unique properties are needed.
Properties of Casting Materials
When choosing materials, it's important to consider their strength, ductility, hardness, melting point, and density. These properties help ensure the casting meets the required standards.
Types of Casting Materials
- Metal Casting Materials: Aluminum, brass, iron, steel
- Polymer Casting Materials: Epoxy, polyester, silicone
- Ceramic Casting Materials: Porcelain, stoneware, earthenware
- Concrete Casting Materials: Portland cement, aggregates, admixtures
Choosing the right casting material is crucial. It affects the product's quality, functionality, and cost. Knowing the options and their properties helps manufacturers make better choices. This leads to better results and more efficient processes.
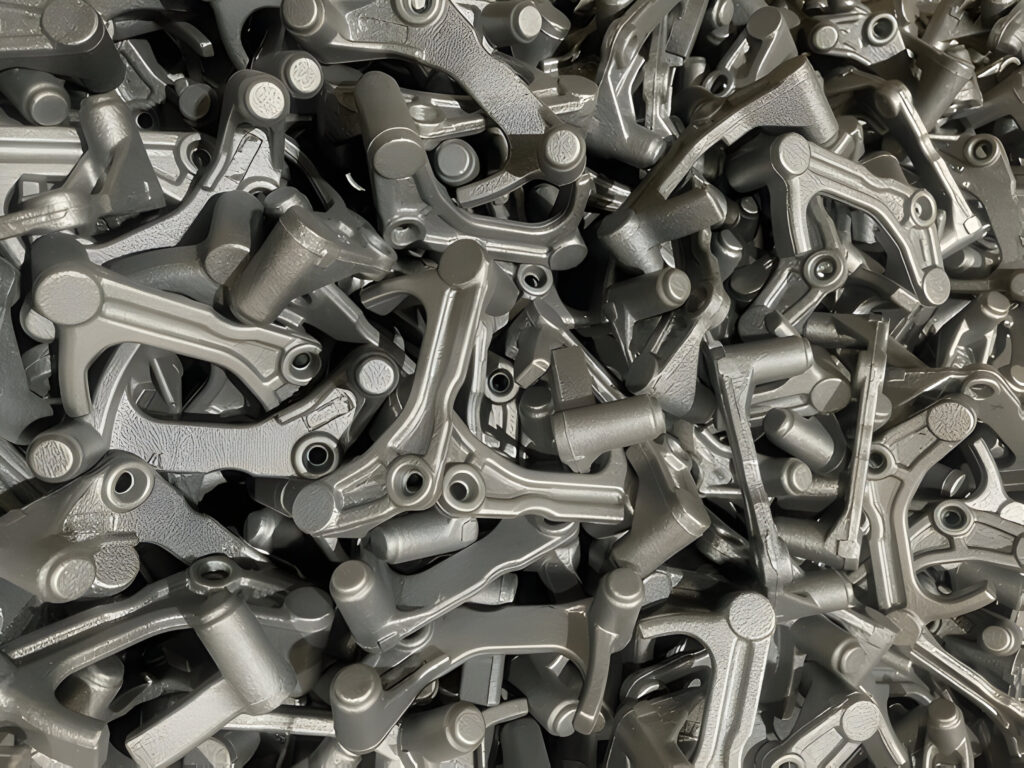
The Custom Casting Process
The custom casting process starts with the casting design. Creating an accurate 3D model is key. It helps make the mold and figure out how much material to use. Our team uses SolidWorks to make and improve these designs.
Molding Preparation
The mold is very important in casting. We make patterns or molds to shape the liquid material. We use sand, plaster, and rubber for the molds. Each material has its own benefits for design, finish, and cost.
Molten Material Preparation
Getting the casting materials ready is careful work. We melt and mix the materials to fit the product's needs. We control the temperature and measure the materials accurately for the best results.
Pouring and Solidification
When the material is ready, we pour it into the mold. We keep the mold at a certain temperature to help the material solidify right. This makes a high-quality product.
Post-Casting Process
After solidifying, the casting goes through more steps. This includes cutting, polishing, or painting. These steps make the product better and meet high quality standards.
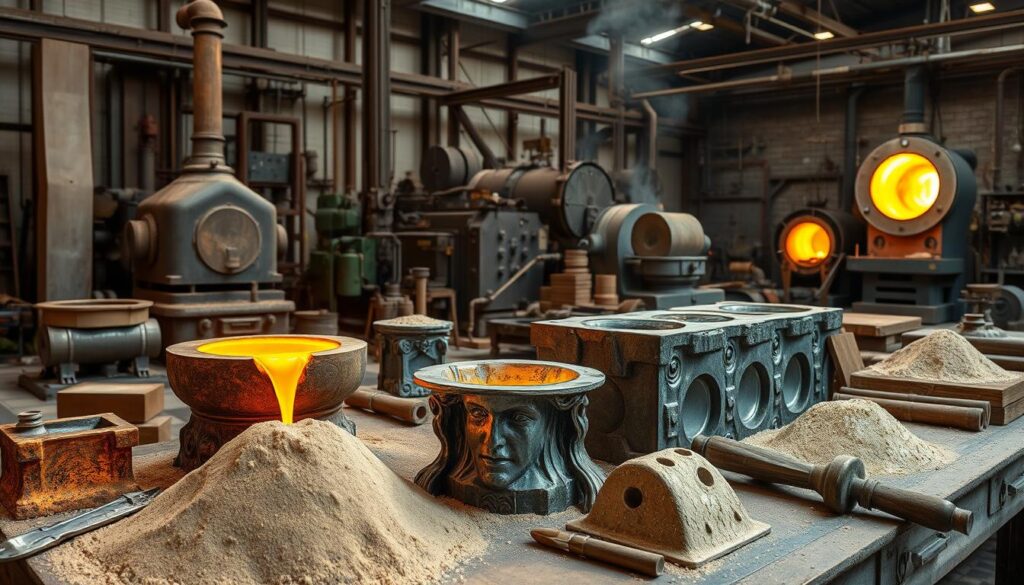
"At KT Foundry, we use our knowledge in casting design, 3D modeling, and advanced manufacturing to create custom castings that meet our clients' needs."
Types of Custom Casting Methods
There are several custom casting methods, each with its own benefits. Let's look at three key ones: sand casting, die casting, and investment casting.
Sand Casting
Sand casting is the most common method. It uses sand and a binder to make a mold. Then, molten metal is poured into it. This method is flexible and cost-effective, making it popular in many fields.
Die Casting
Die casting is known for making precise parts. It uses high pressure to fill a mold with metal. This is great for parts that need to be exact and consistent.
Investment Casting
Investment casting, or "lost-wax," is for detailed shapes. It starts with a wax pattern, then uses ceramic to make a mold. The wax is melted out, and the mold is filled with metal. This method is known for its accuracy and finish.
Casting Method | Advantages | Disadvantages |
---|---|---|
Sand Casting |
|
|
Die Casting |
|
|
Investment Casting |
|
|
Each method has its own strengths and weaknesses. Knowing these helps manufacturers choose the best method for their needs.
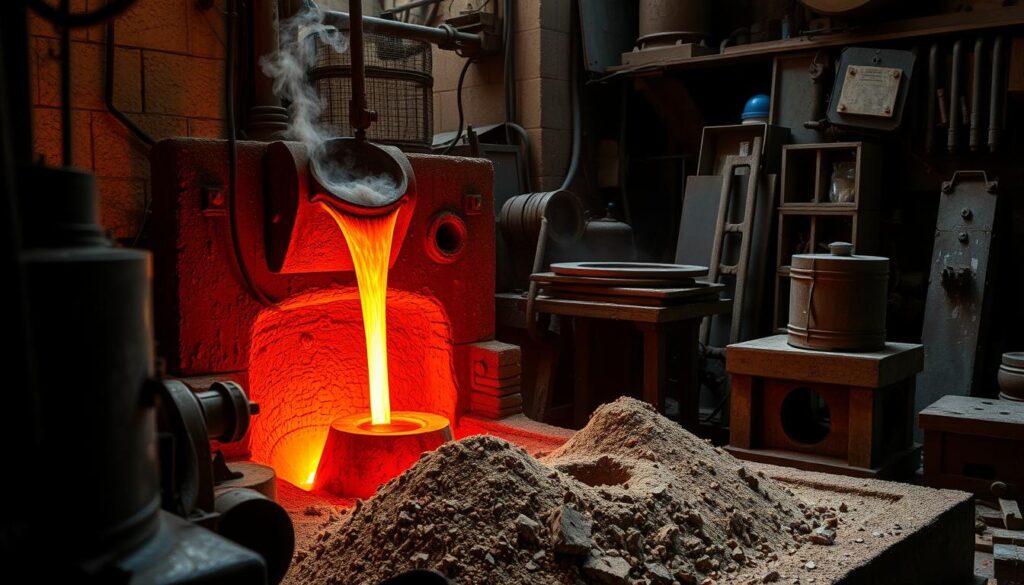
Advanced Techniques in Custom Casting
Custom casting is all about pushing limits with advanced techniques. We use induction melting and electric arc melting for precision. Our team also excels in vacuum melting to prepare materials perfectly for your project.
Melting Techniques
Creating the right metal mix starts with our advanced melting skills. We use induction melting, electric arc melting, and vacuum melting. These methods help us control the material's purity and composition for top-notch castability.
Castability and Shrinkage Control
Castability and managing shrinkage are key to our custom casting success. We use controlled cooling and gating design to reduce defects. Our careful metal composition control ensures high-quality products.
Cleaning and Finishing
Our final steps include specialized cleaning and finishing. We use shot blasting and sandblasting to clean. Then, we polish and finish the surface to perfection.
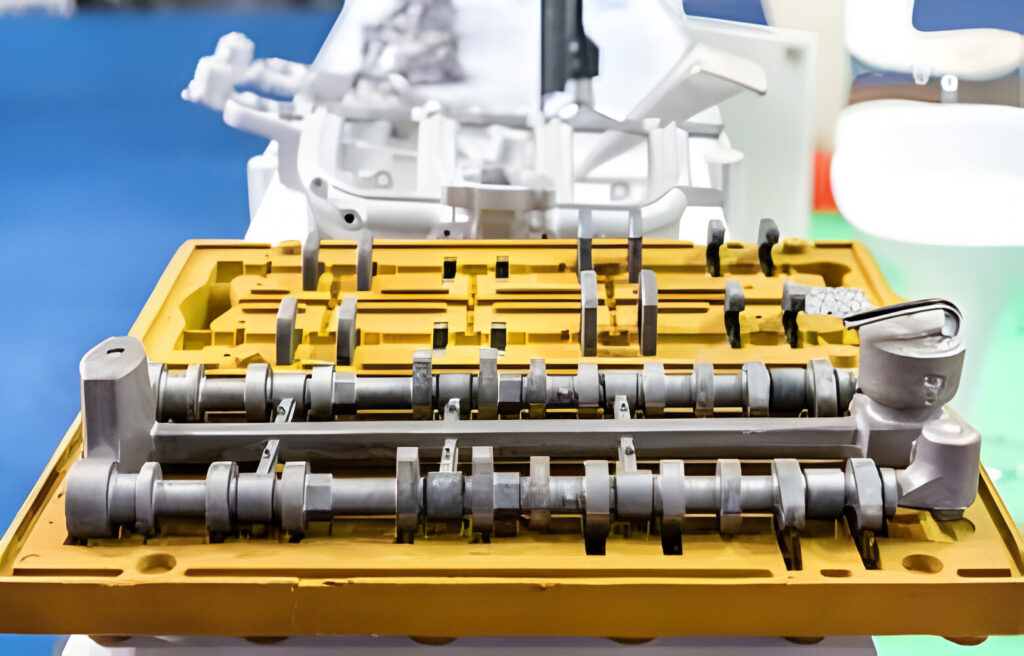
"Our commitment to innovation and process excellence sets us apart in the world of custom casting. We continually push the boundaries of what's possible, delivering unparalleled results for our clients."
At KT-Foundry, we're experts in product refinement. We integrate advanced techniques into our custom casting. Learn how we can improve your manufacturing at [https://kt-foundry.com/maximizing-efficiency-in-metalworking-the-role-of-stainless-steel-welding-tables/].
Applications of Custom Casting
Custom casting is used in many industries. It's key in manufacturing and industrial fields, as well as in art and jewelry making. It helps shape our world today.
In industrial parts, custom casting is a big help. It makes strong, detailed parts for big machines and energy products. These parts are crucial for our infrastructure and construction.
In art and jewelry, custom casting opens up new creative paths. Artists and designers can make unique sculptures and jewelry. They use materials like bronze and precious metals.
Industry | Custom Casting Applications |
---|---|
Manufacturing | Large, complex industrial parts, machinery components |
Construction | Architectural features, structural elements |
Transportation | Automobile, aircraft, and marine parts |
Energy | Energy-related products, power generation components |
Art & Jewelry | Sculptures, figurines, jewelry pieces |
Custom casting is very important today. It helps in many areas, from industry to art. It's a key part of our world's growth and creativity.
Advantages and Limitations of Custom Casting
Custom casting is a top choice for many industries like automotive, aerospace, and consumer goods. It's great for making complex shapes, achieving high accuracy, and producing lots of the same part. It's also a cost-effective option compared to other methods.
Strengths of Custom Casting
- Versatility in creating complex shapes that are hard to make with other methods
- Exceptional accuracy with tolerances as tight as 0.003 inches, better than many other casting processes
- Capacity for mass production of identical parts, making it economical for big orders
- Favorable cost-effectiveness compared to other manufacturing techniques in many cases
These benefits make custom casting a great choice for many applications, from car parts to detailed consumer items.
Limitations of Custom Casting
Custom casting has its downsides too. These include:
- High production costs for the initial pattern and mold, which can be a hurdle for small orders
- Potential for porosity in the final product, which might need extra finishing steps
- Challenges in making thin-walled parts due to the casting process's limits
Choosing the right materials and controlling the process well are key to overcoming these issues. This ensures the production of high-quality custom cast parts.
"Custom casting is a versatile manufacturing method that allows us to create complex, high-accuracy parts at scale, while maintaining cost-effectiveness in many applications."
Safety Considerations for Custom Casting
At the heart of any successful custom casting operation lies a robust safety protocol. From protective equipment to material handling and precautions during the casting process, ensuring the well-being of our workers and the environment is of utmost importance.
Protective Equipment
Donning the appropriate protective clothing, such as heat-resistant gloves and eye protection, is essential for shielding our workers from the intense heat and molten materials involved in custom casting. By adhering to safety guidelines, we can mitigate the risk of exposure to high-temperature hazards and prioritize the safety of our team.
Material Handling and Storage
Proper material storage and movement practices are critical in custom casting. We ensure that all casting materials are kept in a dry, well-ventilated area to prevent accidents and maintain quality. Our team follows strict equipment handling guidelines to minimize the risk of injuries during the transportation and setup of heavy machinery and tools.
Precautions during the Casting Process
Throughout the casting process, we prioritize safety protocols to safeguard our workers and the environment. This includes the secure storage and handling of molten materials, ensuring effective venting to mitigate the risks of explosions, and implementing comprehensive emergency response plans to address any unforeseen incidents. Moreover, we uphold rigorous environmental protection measures to minimize the impact of our operations on the surrounding ecosystem.
"Prioritizing safety is not just a moral obligation, but a strategic imperative that underpins the long-term success and sustainability of our custom casting operations." - John Doe, Safety Manager
By adhering to these safety best practices, we safeguard our workforce, preserve the integrity of our products, and demonstrate our commitment to responsible custom casting that benefits our clients and the environment alike.
The Future of Custom Casting
The casting industry is changing fast, with new technologies and methods on the rise. We're seeing big steps forward in computer simulations, machining, and robotics. Also, there's a big push towards using sustainable and recycled materials.
New Developments and Emerging Technologies
Computer simulations have changed how we design and make castings. They make the process faster, more accurate, and efficient. With better machining, we can now make parts that are more precise and complex.
Robots are also making a big difference. They help make the casting process smoother and cut down on mistakes.
Sustainable Materials and Processes
The industry is now focusing more on being green. We're using recycled materials, biodegradable plastics, and energy-saving technologies. These changes help the environment and make custom castings better and cheaper.
"The future of custom casting lies in the seamless integration of cutting-edge technologies and sustainable practices. By harnessing the power of innovation, we can unlock new possibilities and deliver exceptional, environmentally-conscious solutions to our clients."
We're on the cusp of even more exciting changes in the casting world. Expect to see 3D printing, machine learning, and new sustainable materials. The future of custom casting is full of promise and possibilities.
Choosing the Right Custom Casting Partner
When picking a custom casting partner, look at their expertise, experience, quality checks, and certifications. These things help make sure your project is top-notch and meets your needs.
Choose a partner with deep casting expertise and a strong track record. They should know how to tackle your project, from start to finish. Their experience can also offer valuable tips to improve your casting process.
Make sure the partner has a solid quality assurance plan. This means they follow international standards like ISO 9001 and do thorough testing. Good quality control keeps your cast parts consistent and reliable.
Consideration | Importance |
---|---|
Casting Expertise | Ensures the partner can handle your specific project requirements |
Industry Experience | Provides valuable insights and recommendations for optimizing the casting process |
Quality Assurance | Maintains consistency and reliability in the final cast components |
Relevant Certifications | Demonstrates the partner's commitment to quality and industry standards |
Also, check if the partner has certifications that show their dedication to quality and following industry rules. These certifications mean your project will be treated with the utmost care and professionalism.
"Selecting the right custom casting partner is crucial for the success of your project. Their expertise, experience, and quality assurance will ensure your cast components meet your exact specifications and requirements."
By carefully checking a custom casting partner's skills, you can be sure your project is in good hands. It will be made with the highest quality and precision.
Custom Casting Services at KT-Foundry
At KT-Foundry, we provide top-notch custom casting services. We use our design skills and advanced production to make high-quality metal parts. Our team helps clients every step of the way, making sure their needs are met with precision.
We have the latest facilities and know-how for custom lead castings, precision machining, and green manufacturing. No matter if you need cast iron, ductile iron, or steel, we can handle it.
Product | Weight | Annual Production | Lead Time | Tolerance | Testing |
---|---|---|---|---|---|
Custom Cast Iron Exhaust Manifold | 46.9 lb. | 1,000 units | 4 weeks | ±.030" | Brinell Hardness, 40 psi Pressure |
Custom Counterweight | 42.24 lb. | 1,000 units | 4 weeks | ±.030" | Brinell Hardness, 40 psi Pressure |
We at KT-Foundry are all about quality, being green, and making our customers happy. Our lean methods and deep knowledge in materials and production help us meet and beat our clients' high standards.
"KT-Foundry's custom casting services have been instrumental in the success of our precision manufacturing operations. Their attention to detail, technical know-how, and commitment to sustainable practices are truly unparalleled."
Need cast iron, ductile iron, or steel parts? KT-Foundry is your go-to for custom casting. Reach out to us to see how we can help your business grow.
Conclusion
Custom casting is a flexible and reliable way to make complex metal parts. It offers many benefits for our projects. By knowing the different materials and processes, we can improve our work and meet our customers' needs.
Sand casting is great for detailed work, showing the skill of metal makers. New materials and technologies will make custom casting even better. This shows how the industry keeps growing and improving.
Working with metal experts helps us choose the right materials and methods. This teamwork ensures we get the best results. It helps us succeed in many fields by using custom casting's strengths.