Green sand casting is a key method in metal manufacturing. It's both affordable and good for the environment. This process uses sand, clay, and water to make molds for casting metals. It's used for about 43% of parts made in the U.S., handling simple to complex shapes.
This ancient technique has been around since the Bronze Age. It has evolved over time, staying popular due to its simplicity and effectiveness. Today, it's a top choice for making metal parts, from small to very large.
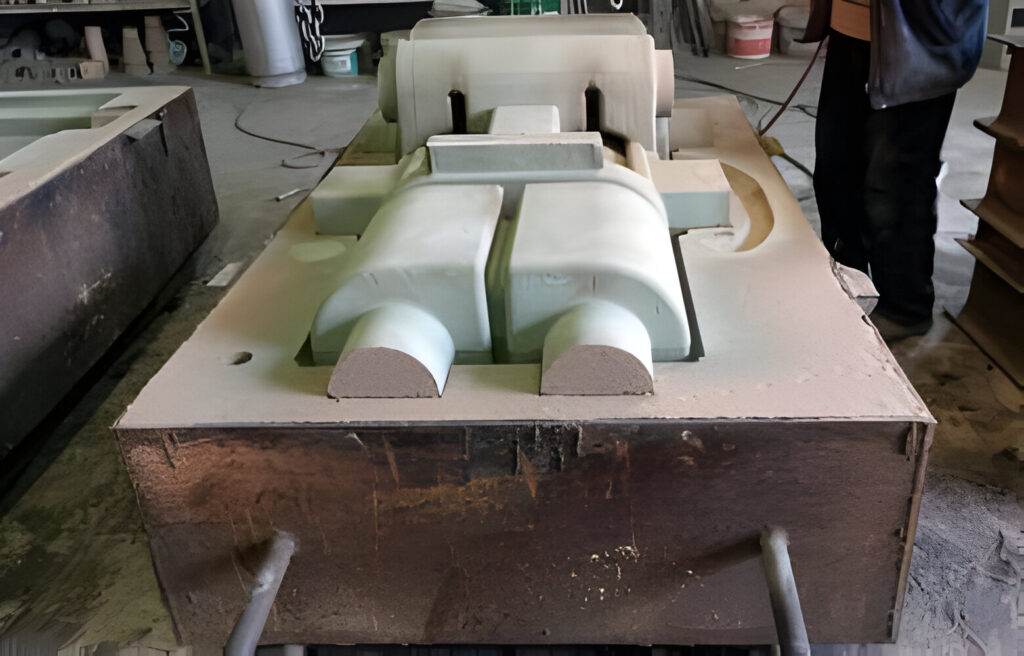
Green sand casting starts with making a mold from sand around a pattern. This can take just an hour, depending on the method and sand type. After the mold is ready, molten metal is poured in, and the part cools. Large parts can take days to solidify.
This process works with many metals, like gold, iron, and titanium. It's great for making one-off parts, small batches, or large quantities. For more on green sand casting, check out our website resources.
What is green sand casting?
Green sand casting is a method that has been around for centuries. It's known for making metal parts with complex shapes and tight tolerances. The "green" in green sand casting doesn't mean the sand is green. It means the sand has moisture in it.
The sand mix is made of 85% sand, 11% bentonite clay, and 4% water. This mix makes molding easy and allows for recycling the sand after casting.
The Timeless Tradition of Green Sand Casting
Green sand casting has a long history in the foundry industry. It's a consistent and reliable method for making metal parts. It's used for parts of all sizes, from small to large.
The sand used in green sand casting is special. It has no chemical additives and is fully recyclable. This makes the process sustainable and cost-effective. The moisture in the sand makes molding easy and recycling simple.
Casting Method | Casting Size Range | Surface Finish | Cost-Effectiveness |
---|---|---|---|
Green Sand Casting | Small to medium (up to 500 kg) | 125-150 RMS | Cost-effective |
Resin Sand Casting | Large (dozens of kg to several tons) | Accurate results | More expensive |
Green sand casting is versatile and used in many fields. It's used for medical equipment, robotic parts, and more. Its consistent performance and cost-effectiveness make it a key part of modern manufacturing.
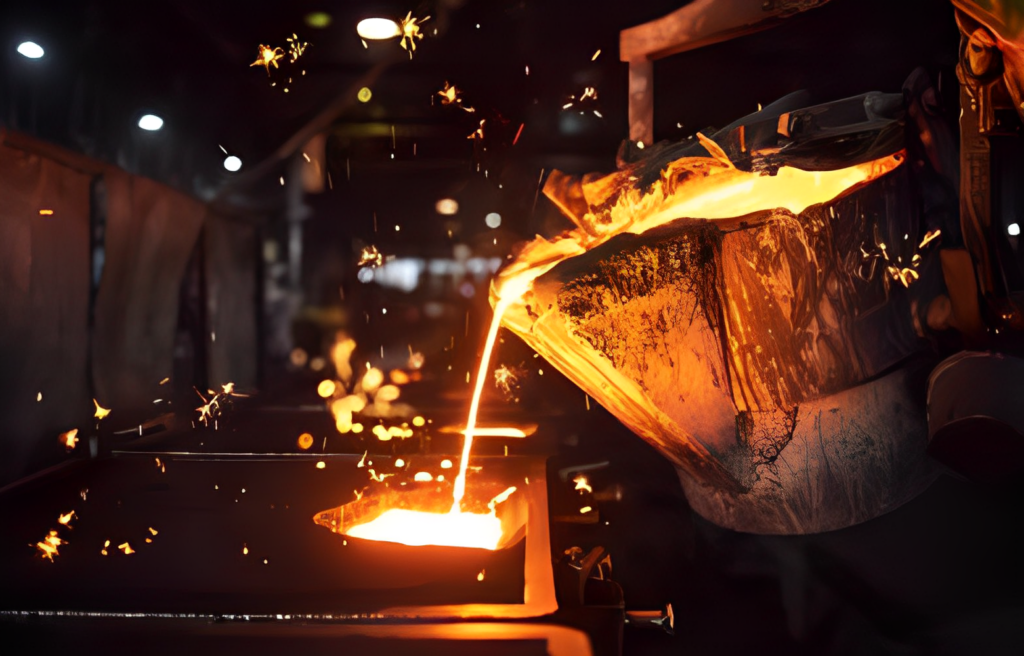
"Green sand casting has been a go-to choice for fabricators due to its consistent and repeatable nature, making it a reliable solution for a wide range of metal components."
The Green Sand Casting Process
The green sand casting process is a key method in making things. It starts with making a pattern and ends with shaking out the sand. Let's explore how this method works.
Preparing the Sand Mold
The heart of green sand casting is the sand mold. It's made from silica sand, bentonite clay, and other stuff. The right mix is 75% to 85% silica sand, 5% to 11% bentonite clay, and 2% to 4% water.
It also has 3% to 5% inert sludge. A bit of anthracite, 0% to 1%, is added to make the mold better.
Mold Making: Crafting the Cavities
To make the sand mold, the mix is packed into a molding box. This box has two parts: the cope (top) and the drag (bottom). Patterns, like wood or metal, shape the cavities in the mold.
Melting and Pouring the Metal
When the mold is set, the metal is poured in. It's heated to 1200-1400 degrees Fahrenheit. This lets the metal take the mold's shape.
Cooling, Shakeout, and Post-Processing
After cooling, the mold is shaken out to get the casting. Then, it's cleaned, finished, and machined. This makes sure it's just right.
"Green sand casting is a cost-effective and versatile process that allows manufacturers to produce a wide range of parts efficiently."
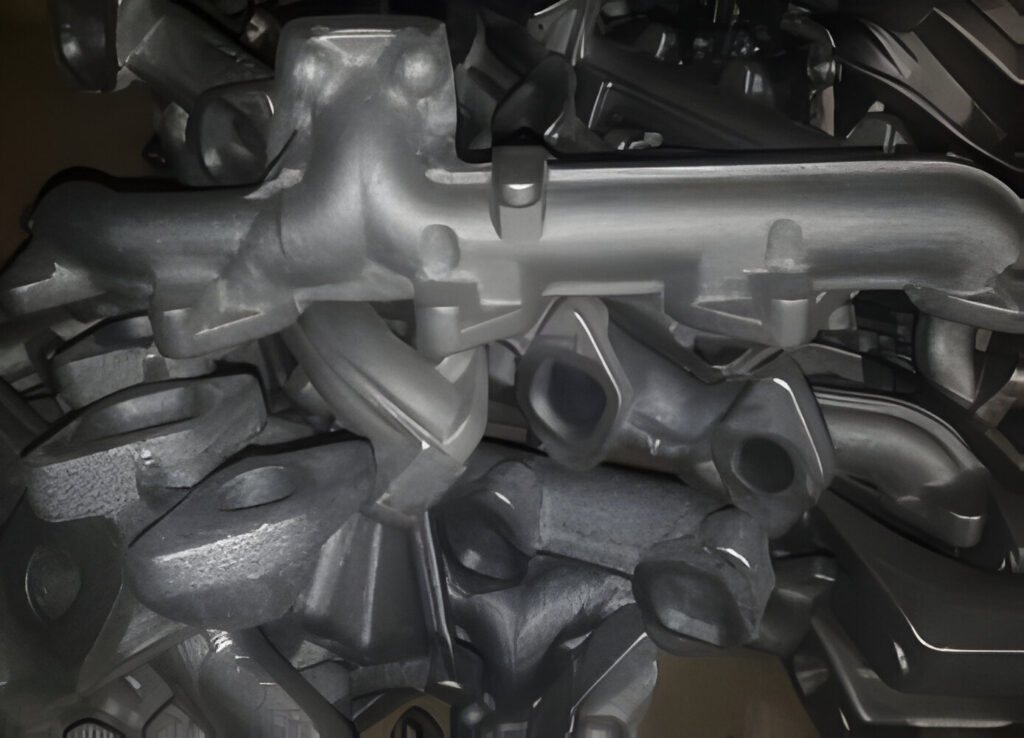
Green sand casting is key in making lots of parts. It's precise and efficient. Knowing how it works helps manufacturers improve their work.
KT-Casting
Bring Your Designs to Reality– Experience Custom Perfection with On-Demand Casting!
Advantages of Green Sand Casting
Green sand casting is a popular metal casting method. It's known for being affordable, flexible, and good for the environment. These benefits make it a top choice for many industries.
Cost-Effective Production
Green sand casting is cheap to produce. It uses materials like sand, clay, and water, which are easy to find and don't cost much. The tools needed for this process are also simple and don't break the bank.
Versatility and Scalability
This method can make many shapes and sizes, from small parts to big castings. It's great for making a few items or lots of them. You can easily change the design of the tools, making it very flexible.
Environmental Friendliness
Green sand casting is good for the planet. The sand in the molds can be recycled, cutting down on waste and pollution.
Surface Finish and Dimensional Accuracy
Green sand casting might not have the best surface or exactness compared to other methods. But, it can still make parts with a good surface and close to the right size. With careful control and skilled workers, the quality can meet many needs.
Advantage | Description |
---|---|
Cost-Effective | Uses cheap and easy-to-find materials, with simple and affordable tools. |
Versatile and Scalable | Can make many shapes and sizes, from small to big, for both small and large orders. |
Environmentally Friendly | The sand can be recycled, reducing waste and pollution. |
Surface Finish and Dimensional Accuracy | Can get a good surface and size, though not the best. |
KT-FOUNDRY Case Study: Automotive Component CastingKT-FOUNDRY
Recently, KT-FOUNDRY collaborated with a leading automotive manufacturer to produce high-strength cast iron components using the green sand casting process. The client required precise geometries and excellent dimensional accuracy for engine brackets.
Challenges Faced
- Ensuring uniform cooling to prevent shrinkage defects.
- Achieving a balance between cost efficiency and high performance.
Our Solution
Leveraging our advanced sand preparation techniques and stringent quality control measures, we successfully delivered 10,000 units within the agreed timeline. Our expertise in cast iron solutions ensured the client received durable components that exceeded their expectations.
This case demonstrates our ability to handle complex requirements and deliver top-tier results, reinforcing our commitment to quality and reliability.
Disadvantages of Green Sand Casting
Green sand casting has some downsides. It can have defects like sand spots, air bubbles, and shrinkage. The surface might not be as smooth as other methods. It also might not be as precise, especially for big castings.
Despite these, green sand casting is still a valuable and common metal casting method. It's affordable, flexible, and eco-friendly for many manufacturing needs.
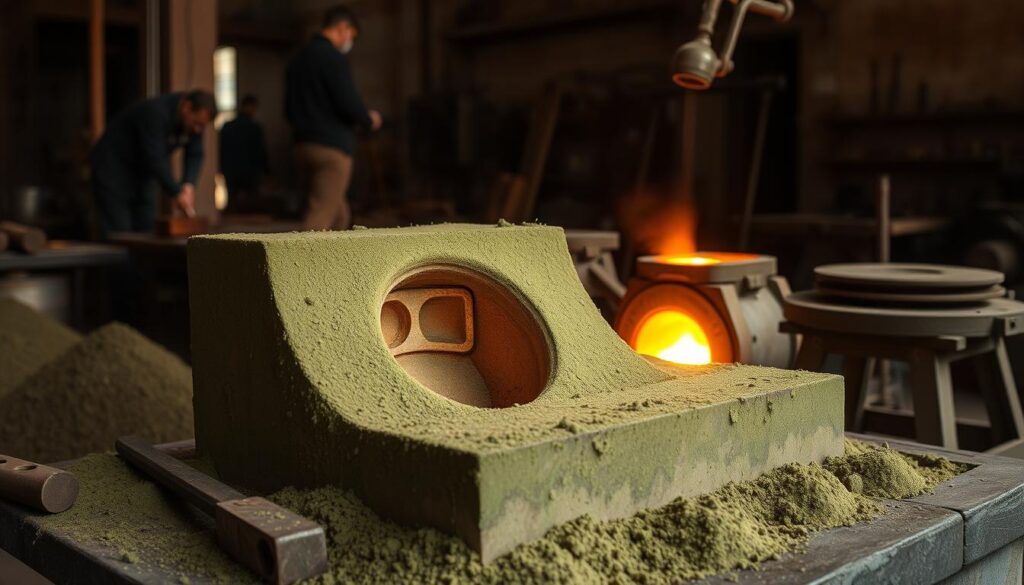
How to choose the right casting technology for different projects?
Choosing the right casting technology is key. It depends on the part's complexity, the needed production volume, and specific industry needs. At KT-Foundry, we help our clients pick the best casting process for their projects.
Die casting is great for parts with simple shapes and lots of production. It's perfect for detailed work and keeping dimensions precise. But, for parts needing more design freedom or larger sizes, investment or permanent mold casting might be better.
Green sand casting is very common and works for many projects. It's used for parts like robotic arms, medical devices, and farm equipment. But, for parts needing a smoother surface or better accuracy, no-bake or shell sand casting could be better.