Custom aluminium die casting is a method for making precise metal parts in large quantities. It uses molten aluminum alloy, which is pushed into a steel mold under high pressure. This makes it possible to create complex shapes with smooth surfaces, needing little to no extra machining.
Die casting is perfect for making lots of aluminum parts. It lets you create detailed designs, ensures parts are the right size, and gives them a great finish.
At KT-FOUNDRY, we're experts in aluminum die casting. We offer top-notch services, including expert die design and ISO 9001:2015-certified manufacturing. Our modern facilities and skilled team make sure you get the best custom die cast parts for your needs.
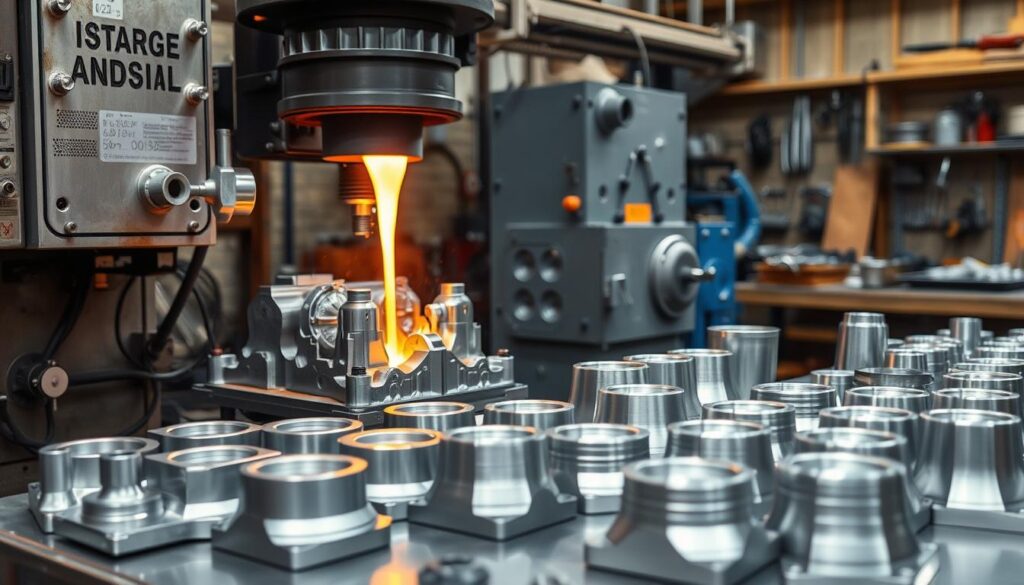
Aluminum die casting is great for many industries, like cars, industrial, and telecom. It's a flexible and efficient way to make metal parts. Whether it's for electrical, hydraulic parts or lighting, our process guarantees top-notch results with precision and consistency.
Understanding the Fundamentals of Die Casting Process
Aluminum die casting is a key method in today's industry. It involves pushing molten aluminum alloy into steel molds under high pressure. This makes complex parts with great surface finish and accuracy.
What Makes Die Casting Unique
The die casting process is special because it can make detailed parts with tight tolerances. The high-pressure injection of molten aluminum into the die cavity lets us create complex shapes. These shapes are hard to make with other casting methods.
The Role of Pressure and Temperature
Controlling pressure and temperature is key in aluminum die casting. The high pressure fills the mold fully and replicates parts accurately. The temperature of the molten aluminum is also important. It helps the metal flow smoothly and solidify well in the die.
Key Components in Die Casting Systems
- Die Halves: The precision-engineered steel molds that form the desired shape of the casting.
- Injection System: The mechanism that propels the molten aluminum alloy into the die cavity under high pressure.
- Clamping Mechanism: The component that securely holds the die halves together during the injection and solidification process.
The die casting cycle starts with clamping the die halves. Then, molten aluminum is injected into the die cavity. After that, the metal solidifies under pressure before being ejected as a finished part. This process is fast and makes parts with great detail and surface finish.
Aluminum Die Casting Advantages
Aluminum die casting is a popular manufacturing process due to its unique benefits, which include:
- Lightweight and Durable
Combines strength with low weight, making it ideal for automotive, aerospace, and consumer products.
- High Precision and Accuracy
Produces complex shapes with tight tolerances, reducing the need for additional machining.
- Corrosion Resistance
Naturally resistant to rust, ensuring long-lasting performance in challenging environments.
- Excellent Thermal and Electrical Conductivity
Suitable for heat sinks, electronic housings, and applications requiring efficient heat dissipation.
- Versatile Finishes
Can be painted, powder-coated, or anodized for enhanced functionality and aesthetics.
- Cost Efficiency for High-Volume Production
Once tooling is created, aluminum die casting allows for rapid production with minimal material waste.
Recyclability
Aluminum is eco-friendly and 100% recyclable, making it a sustainable manufacturing choice.
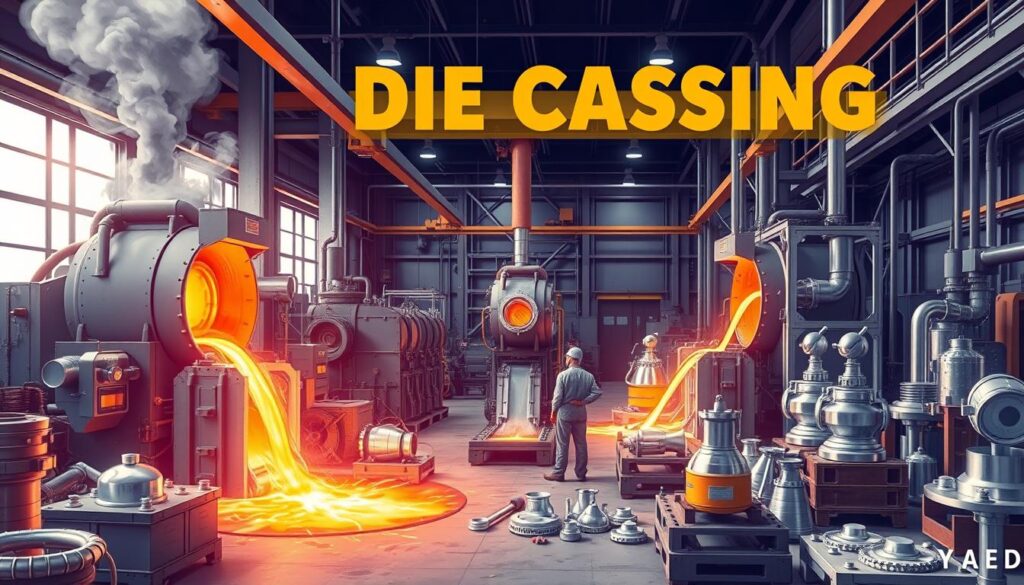
Types of Die Casting Methods: Hot Chamber vs Cold Chamber
In the world of die casting, two main methods stand out: hot chamber and cold chamber die casting. Each has its own benefits and is best for certain materials and uses. Let's explore the main differences between these two techniques.
Hot Chamber Die Casting
Hot chamber die casting is great for metals like zinc and magnesium that melt easily. It has a built-in furnace to keep the metal hot. The metal flows through a gooseneck into the die. This method is fast, with up to 900 cycles per hour, perfect for making lots of parts.
Cold Chamber Die Casting
Cold chamber die casting is best for aluminum and other metals that melt at higher temperatures. The molten metal comes from an outside furnace to the shot chamber. A plunger then pushes the metal into the die. This method might take longer but makes denser parts. It's also good for a variety of metals, including aluminum, magnesium, and copper alloys.
Comparison | Hot Chamber Die Casting | Cold Chamber Die Casting |
---|---|---|
Suitable Metals | Zinc, Magnesium, Low-Melting Alloys | Aluminum, Magnesium, Copper Alloys |
Filling Speed | Up to 540 km/h | Slower than Hot Chamber |
Pressure Range | 700 to 5,000 psi | 2,000 to 20,000 psi |
Production Cycle | 400 to 900 cycles per hour | 50 to 90 cycles per hour |
Porosity | Lower | Higher |
Die Life | Longer | Shorter |
Hot chamber and cold chamber die casting each have their own strengths. The right choice depends on the metal, how many parts you need, and what the parts should be like. Knowing these differences helps pick the best method for your project.
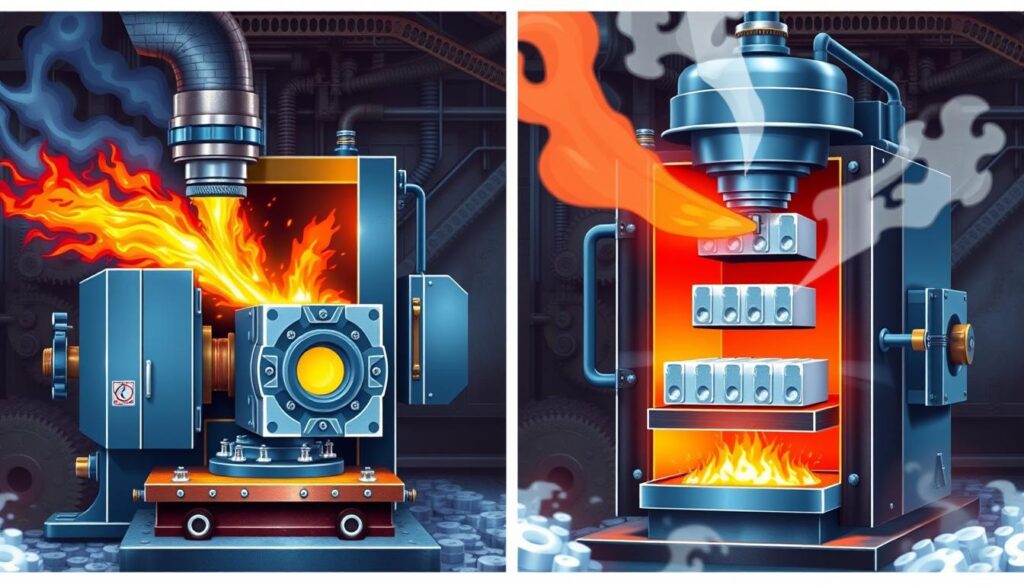
Essential Materials and Properties of Aluminium Die Castings
Choosing the right alloy is key in aluminium die casting. The A380 alloy is the most popular. It has great casting and mechanical properties.
Popular Aluminium Alloys for Die Casting
Other alloys like 383, B390, A413, A360, and CC401 are also used. Each has special properties for different uses. For example, A360 is great for resisting corrosion, while B390 is hard and wears well.
Material Selection Criteria
Many factors influence the alloy choice. These include strength, corrosion resistance, and how the metal flows when melted. The right alloy depends on the application, like car parts or industrial tools.
Performance Characteristics of Different Alloys
Here's a look at how different alloys perform:
Alloy | Tensile Strength (MPa) | Elongation at Break (%) | Hardness |
---|---|---|---|
AC 46100 | 310 | 3.5 | 75 |
AC 46500 | 317 | 2.5 | 80 |
Zamak 2 | 359 | 7 | 100 |
Zamak 3 | 283 | 10 | 82 |
Zamak 4 | 317 | 7 | 86 |
Zamak 5 | 328 | 7 | 91 |
Zamak 7 | 283 | 13 | 80 |
These numbers show how different alloys perform. This helps manufacturers pick the best one for their needs.
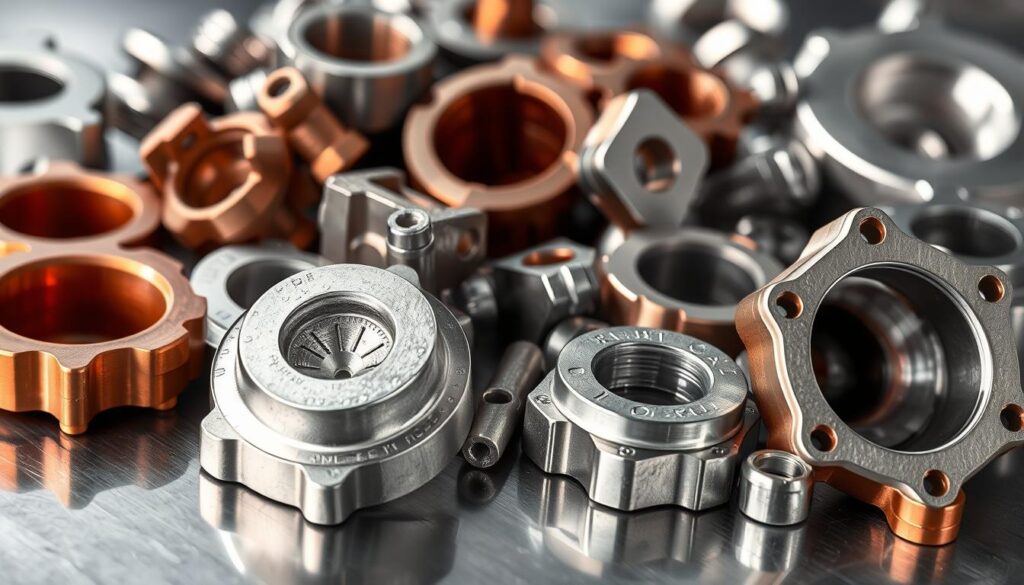
Design Considerations for Custom Die Cast Parts
Creating custom die cast parts requires careful thought. The parting line, where the two halves meet, needs careful planning. This ensures a smooth transition.
Keeping wall thickness consistent is key. Walls that are too thin can block metal flow. Walls that are too thick waste material and slow solidification.
Die casting involves complex shapes, which need special design care. The right draft angles help remove parts easily. Ejector pins must be placed thoughtfully to affect part look and function.
Designers must watch out for undercuts and overhangs. These might need special tools or design tweaks. Fillets and radii help metal flow smoothly and avoid extra work on sharp edges.
Bosses, used for mounting, need careful design. They should have the right wall thickness and fillets for good metal flow. Ribs add strength without using too much material and help with metal flow.
Designing for holes and windows can cut down on post-molding work. This makes the whole process more efficient. By focusing on these details, manufacturers can make parts that are top-notch in quality and performance.
"Castings generally shrink between 0.4-0.6% of their volume, aiding in the ejection of the product from the external walls of the die."
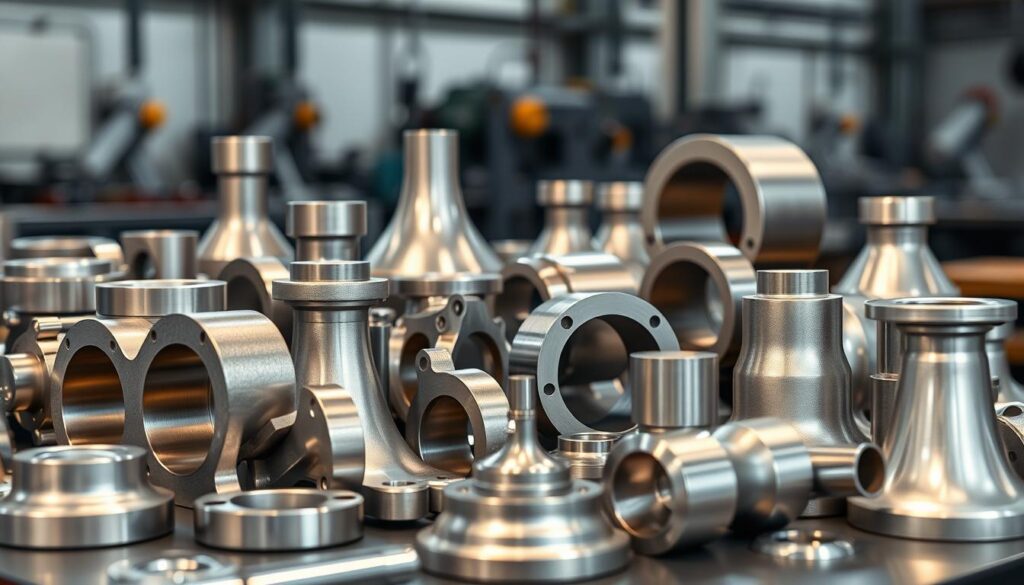
Manufacturing Process Steps and Quality Control
At KT-FOUNDRY, we start making custom aluminum die castings with a detailed 3D CAD file and die design. This step makes sure the die fits perfectly for the part we want to make.
Then, we follow a clear process. The die is closed, and molten aluminum is pushed in under high pressure. Once it solidifies, the part comes out. After that, we remove flash and trim it to get the exact shape.
Quality Assurance Measures
Our ISO 9001:2015-certified facility is all about quality control. We do detailed checks, visual inspections, and material tests. This makes sure our die casting machine parts are top-notch.
We also use X-ray radiography and ultrasonic testing. These methods help us check the mold release and flash removal processes. This ensures our parts are of the highest quality.
We use statistical process control (SPC) to keep an eye on our quality control. By checking key process parameters, we catch any issues early. This helps us make sure our products are always high-quality.
We're also proud of our extra certifications. We have IATF16949 for automotive and ISO14001 for environmental management. These show our commitment to making the best die casting machine parts for many industries.
Surface Finishing and Post-Processing Options
At KT-FOUNDRY, we know how important the surface finish of aluminum die castings is. It affects both looks and performance. We offer many surface finishing and post-processing options to meet our clients' needs. Our team works hard to deliver top-notch results every time.
We use orbital sanding to improve the surface finish of our die cast aluminum parts. This method creates a smooth, even surface. For better corrosion resistance and a nice look, we can apply anodizing or powder coating. These finishes not only look good but also protect the part from the environment.
Shot peening is another important post-processing option we offer. It's used to make our aluminum components more resistant to fatigue. This process involves hitting the surface with small metal shots. It helps to make the part more durable.
We also do additional machining operations, like drill tapping, to add features or improve tolerances. Our e-coating and powder coating finishes meet strict customer specifications. They ensure a flawless and lasting result.
Surface Finishing Technique | Key Benefits |
---|---|
Sanding and Sandblasting | Improves surface finish and smoothness |
Anodizing | Enhances corrosion resistance and aesthetic appeal |
Powder Coating | Provides a durable, high-quality finish |
Shot Peening | Improves fatigue resistance and overall durability |
Machining (Drill Tapping) | Adds features and improves tolerances |
E-Coating and Powder Coating | Meets specific customer requirements |
At KT-FOUNDRY, we're dedicated to giving our clients top-quality aluminum die castings. We offer a wide range of surface finishing and post-processing options. Our expertise and attention to detail ensure your parts look great and perform well.
Applications Across Various Industries
Aluminum die casting is used in many industries. It's found in the automotive, telecommunications, and industrial sectors. Die-cast parts are key to meeting today's manufacturing needs.
Automotive Sector Implementation
In cars, aluminum die castings are used for engine blocks and more. They're light and strong, perfect for cars that need to be both fast and fuel-efficient. The car market is growing, and so is the need for these parts.
Telecommunications Equipment
Die-cast parts are crucial for making telecommunications equipment. They can create complex shapes with precision. As 5G technology grows, so will the demand for these parts.
Industrial Components
Die-cast parts are used in many industrial components. They're made for pumps and machinery parts. The construction industry also uses them for building frames and more.
Aluminum die casting is vital for many industries. It's used in cars, electronics, and construction. Die-cast parts help make products better and more efficient.
Industry | Application of Aluminum Die Castings | Market Value/Growth Projection |
---|---|---|
Automotive | Engine blocks, transmission cases, chassis components | USD 58.4 billion by 2026, CAGR of 6.19% |
Telecommunications | Electrical housings, equipment enclosures | Increasing demand for 5G infrastructure |
Industrial | Pumps, valves, machinery parts, construction components | Growing demand for lightweight, durable parts |
"Aluminum die castings have become the dominant die castings produced, finding widespread applications in automotive components, electronic enclosures, aerospace parts, and consumer goods."
Cost Analysis and Production Volume Considerations
Custom aluminium die castings start with big tooling costs. But, they get much cheaper for making lots of parts. The cost to make the tool can be from $5,000 to $75,000. This depends on how big and complex the parts are.
Die casting is great because it saves on labor. It has quick cycles and uses very little material. Labor costs for making these parts are only about 1.5% of the total cost.
Production Volume | Unit Price | Tooling Cost | Lead Time |
---|---|---|---|
500 parts | £6.91 | £4,992.00 | 32 days |
5,000 parts | £5.18 | £4,992.00 | 32 days |
50,000 parts | £5.18 | £4,992.00 | 32 days |
For making fewer parts, sand casting might be cheaper. But, die casting is better for making lots of parts. It's important to think about how complex the parts are and how many you need to make.
Die casting is very good for saving money. It uses about 90% to 95% of the material, which cuts down on waste. Also, making a 1 kg part costs about $1 USD. This makes die casting very cost-effective.
Die casting is a smart choice for making lots of parts. It's important to look at the costs of making the tool, how many parts you need, and other economic factors. This way, businesses can use die casting to make their manufacturing better and stay ahead in the market.
Comparing Die Casting to Alternative Manufacturing Methods
Die casting is a top choice for making precise parts. It beats sand casting and permanent mold casting in many ways. Die casting gives parts that are very accurate and have a smooth finish, perfect for detailed designs.
Die casting also makes parts that are complex. Permanent mold casting makes parts that are strong. But die casting is better at making parts with lots of details.
Die casting is great for making lots of parts quickly. It's faster than machining and uses less material. But for making a few parts or very big parts, sand casting might be cheaper.
Manufacturing Method | Dimensional Accuracy | Surface Finish | Strength of Parts | Suitable for High-Volume Production | Economical for Low-Volume/Large Parts |
---|---|---|---|---|---|
Die Casting | Excellent | Excellent | Good | Yes | No |
Sand Casting | Good | Fair | Fair | No | Yes |
Permanent Mold Casting | Good | Good | Excellent | Moderate | No |
Choosing between die casting, sand casting, permanent mold casting, extrusion, and machining depends on several things. These include the part's design, how many you need, and what the part needs to be made of. Die casting is the best for making lots of precise, complex parts without breaking the bank.
Conclusion
Custom aluminum die casting is a smart way to make complex, high-quality parts in big numbers. It combines the best of materials, design freedom, and fast production. KT-FOUNDRY is a top choice for making precise aluminum parts thanks to their skill and quality systems.
Knowing how die casting works, what materials are used, and how to design and finish parts is key. This knowledge helps makers create new, affordable solutions for their projects.
Die casting is popular in car, plane, and tech industries because of its benefits. It makes parts that are light, don't rust, and work better. This makes die-cast aluminum parts a big deal in making things.
As technology gets better, so does die casting. It will keep getting better, making making things faster, more flexible, and meeting new market needs.
Working with KT-FOUNDRY means getting the latest in die casting tech. They focus on quality, new ideas, and making customers happy. KT-FOUNDRY is ready to help businesses grow with custom aluminum die castings.
FAQ
What is aluminum die casting and how does it work?
Aluminum die casting is a manufacturing process that involves pouring molten metal into a mold, known as a die, to create various components. The die casting process typically utilizes aluminum alloys due to their lightweight and strength properties. The process can be categorized into two main types: high-pressure die casting and low-pressure die casting. In high-pressure die casting, molten aluminum is injected into the die cavity at high speeds, allowing for the production of intricate shapes with high dimensional accuracy.
What are the advantages of aluminum die casting?
The advantages of aluminum die casting are manifold. Firstly, components produced via this method exhibit excellent surface finishes and dimensional precision. Secondly, aluminum die cast parts are lightweight yet strong, making them ideal for various applications in automotive, aerospace, and consumer electronics. Additionally, the process allows for high-volume production, reducing per-unit cost. Furthermore, aluminum has a natural resistance to corrosion, which enhances the longevity of the cast aluminum parts.
What types of aluminum alloys are typically used in die casting?
Various aluminum alloys can be utilized in the die casting process, with the most common being 380, 383, and 384. These die casting alloys possess different mechanical properties, such as strength and ductility, making them suitable for a range of applications. The choice of alloy for die casting depends on the specific performance requirements of the final cast part.
What is the difference between high-pressure die casting and low-pressure die casting?
High-pressure die casting involves forcing molten aluminum into a die at high speeds, allowing for rapid production of complex shapes. Conversely, low-pressure die casting uses a lower pressure to fill the die cavity, resulting in less turbulence and better surface quality but at a slower pace. Each method has its specific applications and is chosen based on the project requirements.