Pumps are key in many industries, like manufacturing and oil and gas. Centrifugal pumps handle high flow rates well. They're great for low-viscosity fluids. On the other hand, positive displacement pumps control flow and pressure well. They're best for viscous liquids in oil and gas or chemical industries. The pump casing is the outer part of the pump. It keeps the inside sealed from the outside. The casing design changes based on the pump type.
Key Takeaways
- Centrifugal pumps are the most common type of pumps found in DOE facilities and operate over a wide range of flow rates and pump heads.
- Double volute pumps are designed to minimize radial forces on the shaft and bearings due to pressure imbalances around the impeller.
- Diffusers in centrifugal pumps increase efficiency by providing a more gradual expansion for the liquid.
- Multi-stage centrifugal pumps are designed to develop high pressures and are more economical than single impeller designs.
- Wearing rings in centrifugal pumps minimize liquid leakage, reducing maintenance costs.
Introduction to Pump Casings
The pump casing is the outer part that protects the pump's inside from the outside. It keeps the fluid pressure right and stops leaks. This part is key for the pump to work well and efficiently.
Definition and Purpose of Pump Casings
The pump casing is like a shell that holds the pump's parts, like the impeller and rotor. It keeps the pump's inside safe from the outside. This helps the pump move energy to the fluid well.
Importance of Proper Casing Design
The design of the pump casing is very important. A good design supports the parts inside and helps the fluid flow better. A bad design can cause problems like wear and less efficiency.
To learn more about pump casings, check out our guide on premium OEM motor housing solutions.
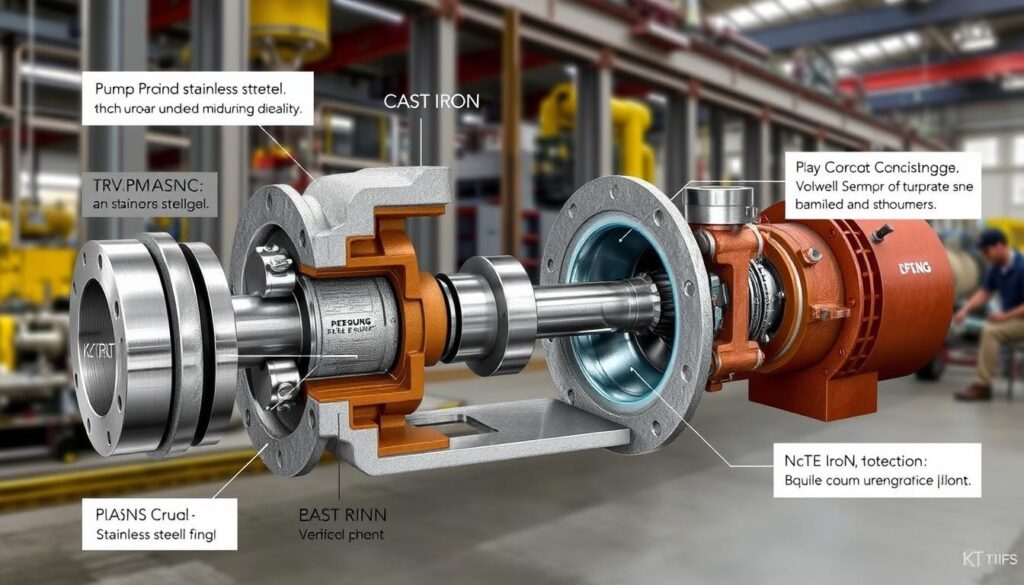
Types of Pump Casings in Centrifugal Pumps
Centrifugal pumps are key in today's industries. They come in different casing types to improve fluid flow and pressure. The volute, vortex, and guide blade casings each have their own benefits for various uses.
Volute Casing
The volute casing is the most common. It's shaped like a spiral. This design slows down fluid and increases pressure by widening the flow area. It's great for handling low to medium flow rates, making it a favorite for many applications.
Vortex Casing
The vortex casing has a circular chamber. It helps reduce eddies, boosting efficiency. This design is perfect for handling solids and liquids in wastewater and industrial settings.
Casing with Guide Blades
This design includes stationary vanes around the impeller. These vanes slow down the liquid and increase its pressure. It's often used in multistage pumps to add extra pressure for better performance.
The pump casing is crucial for the pump's operation and efficiency. Its design affects fluid flow, distribution, and pressure. Choosing the right casing is key to achieving the best pump performance.
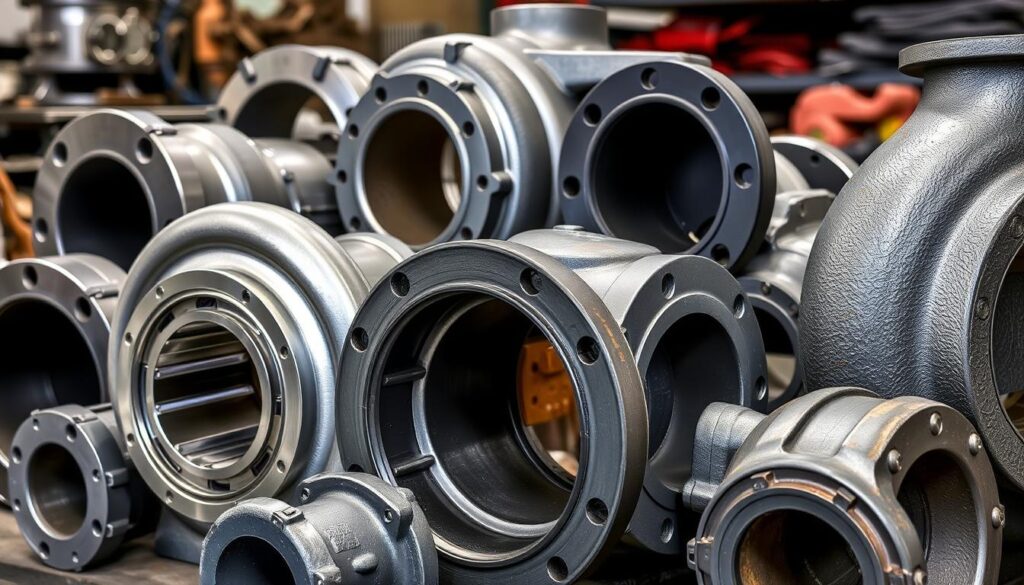
Single Volute vs. Double Volute Casings
Choosing between single volute and double volute casings for centrifugal pumps is a big decision. It's about finding the right balance between cost, simplicity, and performance. Both types guide fluid flow, but they handle radial thrust forces differently.
The single volute casing has one cutwater that directs liquid flow. It's cheaper because it's simpler to make. But, it can cause more wear on parts like seals and bearings due to uneven pressure.
The double volute casing has two cutwaters, 180 degrees apart. It helps reduce the radial thrust issues of single volute casings. But, it doesn't get rid of these forces completely.
Feature | Single Volute Casing | Double Volute Casing |
---|---|---|
Radial Thrust | Increased net radial stresses on the rotor | Significantly reduced radial forces, but not eliminated entirely |
Bearing and Seal Life | Shorter bearing and seal life due to increased radial forces | Improved bearing and seal life compared to single volute |
Efficiency at Best Efficiency Point (BEP) | Higher efficiency at the pump's BEP | Slightly lower efficiency at the pump's BEP compared to single volute |
Cost | Less expensive due to simpler design and casting process | More expensive due to the additional cutwater and complexity |
Deciding between single and double volute casings depends on your needs. Single volute casings are simpler and efficient at the BEP. Double volute casings offer better life for bearings and seals, especially in off-design flow rates. Knowing the differences is key to picking the best pump casing for your system.
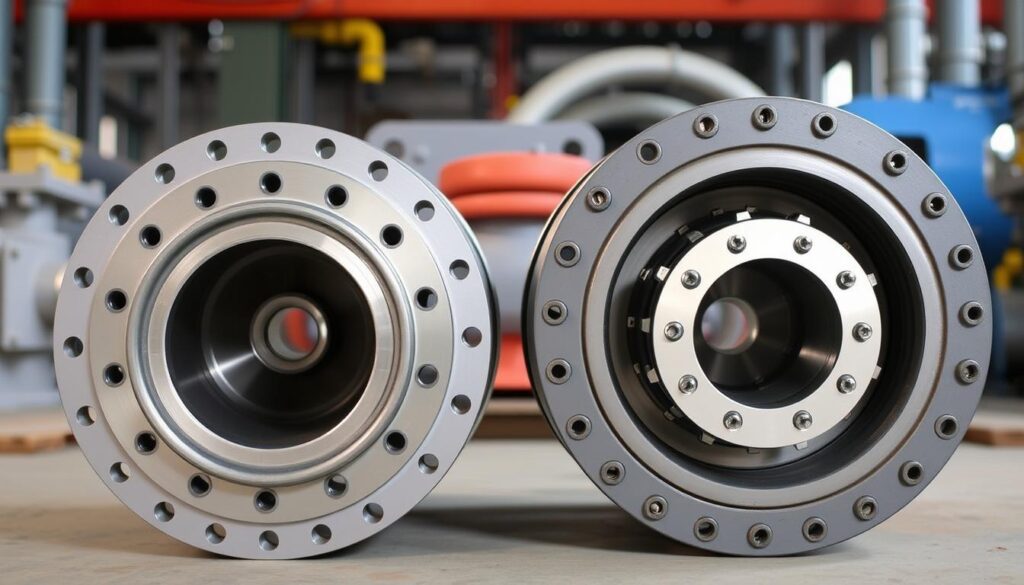
Vaned Diffuser Casings
Vaned diffuser casings are a special design for centrifugal pumps. They have an impeller surrounded by guide blades, or a diffuser. These vanes help the fluid flow smoothly from the impeller.
The vanes also make the fluid's area bigger. This reduces the fluid velocity and boosts the static pressure. After going through the vanes, the fluid moves through the casing. Vaned diffuser casings are often found in multistage pumps. They help make the pump more efficient by turning velocity into pressure.
Working Principle
The vaned diffuser changes fast-moving fluid into slower, higher-pressure fluid. It does this by making the flow passage wider. This reduces the fluid's speed and increases its pressure.
Applications
- Vaned diffuser casings are common in multistage centrifugal pumps. They improve the pump's efficiency and performance.
- They're great for high-pressure needs, like in oil and gas, power plants, and water treatment.
- The design of vaned diffusers can be adjusted for different needs. This makes them useful for many industrial uses.
"Diffuser pumps, especially those designed for lower flow rates, have been noted to have a higher maximum efficiency compared to volute pumps."
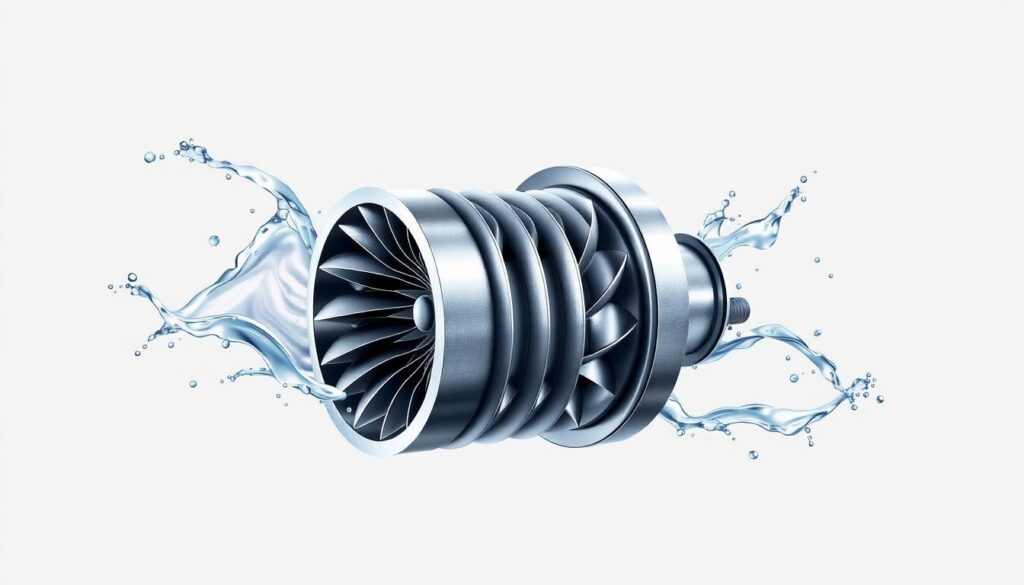
Materials for Pump Casings
Manufacturers have many materials to choose from for pump casings. Each material has its own benefits and uses. The right choice depends on the application, the fluid being pumped, and the operating conditions.
Cast iron is a common and affordable choice. It resists corrosion well and dampens noise. Ductile iron is stronger and more durable, making it better for tough environments.
Carbon steel is used when pumps need to handle high pressure. Stainless steel is best for handling harsh or corrosive fluids because it resists corrosion well.
For very tough conditions, high-alloy materials like Hastelloy, Monel, or titanium are used. They can handle extreme temperatures, aggressive chemicals, or abrasive substances.
Choosing the right material for pump casings is very important. It affects the pump's reliability, longevity, and performance. The right material ensures the pump works well and lasts long.
Material | Advantages | Applications |
---|---|---|
Cast Iron | Cost-effective, good corrosion resistance, noise dampening | General-purpose applications |
Ductile Iron | Superior strength and durability | Demanding environments |
Carbon Steel | Higher pressure and strength | Applications requiring higher pressure |
Stainless Steel | Excellent corrosion resistance | Pumps handling harsh or corrosive fluids |
High-Alloy Materials | Withstand extreme conditions (high temperature, aggressive chemicals, abrasive substances) | Specialized applications |
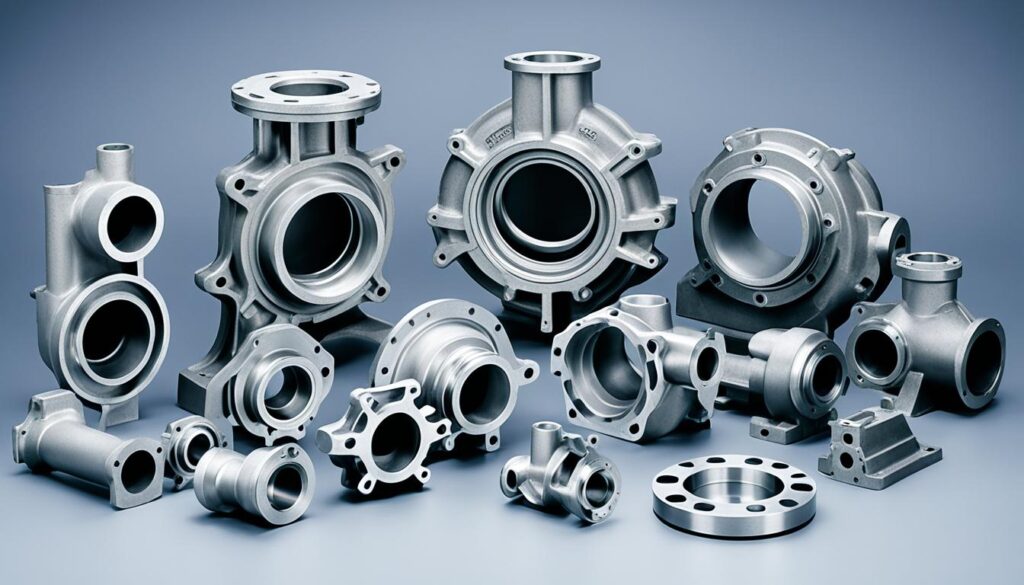
Choosing the right material for pump casings is key. It affects the pump's performance, reliability, and longevity. The right material ensures the pump works efficiently and lasts long.
Casing Design Considerations
When designing pump casings, we must think about the fluid's properties and the pump's operating conditions. Choosing the right material for the casing is key. It must handle the fluid's corrosive or abrasive effects and keep its shape under various temperatures, pressures, and flow rates.
Fluid Properties
The fluid's viscosity, density, and chemical makeup greatly affect the casing design. For instance, thick or heavy fluids might need a stronger casing to avoid leaks or damage. Also, fluids that are corrosive, like those with high chloride ion content, require corrosion-resistant materials for the casing.
Operating Conditions
The pump's operating conditions, like temperature, pressure, and flow rate, are also vital in casing design. The casing must keep a tight seal and stay strong under these conditions for efficient and safe operation. Important factors like specific speed (Ns) and suction specific speed (Nss) also influence the casing design.
By carefully looking at the fluid properties and operating conditions, engineers can pick the best casing material and design. This ensures the pump works well, reliably, and lasts a long time.
"Preliminary casing design presents significant opportunities for cost savings in the overall well construction process."
pump casing
Over time, the pump casing can wear down and erode due to fluid flow. This wear causes more space between the impeller and casing. This results in higher leakage rates and less pump efficiency. To solve this, many pumps have wearing rings.
These rings fit between the impeller and casing. They keep the space small without damaging the casing or impeller. Regular pump maintenance and replacement of these rings are key. They help keep the pump working well and avoid expensive repairs.
Component | Function | Typical Lifespan |
---|---|---|
Pump Casing | Provides structural support and guides fluid flow | 10-20 years |
Wearing Rings | Maintain clearance between impeller and casing | 2-5 years |
Regular checks on the pump casing and timely replacement of wearing rings can extend your pump's life. This approach keeps your pump running at its best. It also saves you from expensive pump replacement costs.
"Proper maintenance and timely replacement of wearing rings are crucial for maintaining the efficiency and longevity of centrifugal pumps."
Pump Casing Types for Specific Applications
In the world of industrial pumps, the choice of pump casing type is key. It depends on the specific application and industry needs. ANSI pumps follow American National Standards Institute (ANSI) standards. They are used in many industries like manufacturing, agriculture, and water systems.
These pumps have cast iron or ductile iron casings. This makes them good for general use.
API610 pumps, on the other hand, are made for the oil and gas industry. They handle dangerous or corrosive fluids. These pumps use materials like carbon steel, stainless steel, or high-alloy materials.
This choice ensures they last long in tough environments. When picking between ANSI and API610 pumps, you must think about the fluid, operating conditions, and industry rules.
Pump Casing Type | Typical Industry Applications | Key Features |
---|---|---|
ANSI Pumps | Manufacturing, Agriculture, Municipal Water Systems | Cast iron or ductile iron casings, suitable for general-purpose applications |
API610 Pumps | Oil and Gas, Petrochemical, Chemical Processing | Carbon steel, stainless steel, or high-alloy materials, designed for hazardous or corrosive fluids |
Choosing between ANSI and API610 pump casings depends on the application's needs. It's important to pick a pump that can handle the fluid safely and meet industry standards.
Emerging Trends and Innovations
The pump casing industry is changing fast. New materials, technologies, and ways to optimize are making a big difference. Advanced materials like high-performance plastics are being used. They make pump casings last longer and resist corrosion better, perfect for tough jobs.
3D printing technology is also changing the game. It lets makers create complex designs that were hard or impossible before. This means pump casings can be made to fit exactly what customers need.
Another big change is using computational fluid dynamics (CFD) simulations. These simulations help engineers design pump casings for better flow and efficiency. This leads to pumps that work better and use less energy.
These trends and innovations will keep shaping pump casings in the future. They promise to improve energy use, customization, and overall system performance.
Emerging Trend | Impact on Pump Casings |
---|---|
Advanced Materials | Improved corrosion resistance and durability |
3D Printing | Enables more complex and customized casing designs |
Computational Fluid Dynamics (CFD) | Optimizes casing design for improved efficiency and performance |
"The pump casing design and manufacturing industry is continuously evolving, and the introduction of new materials, technologies, and optimization techniques is driving significant advancements in the field."
What is a pump casing and its purpose?
A pump casing is the outer shell or structure that encases the internal components of a pump, particularly in a centrifugal pump. Its primary purpose is to provide a containment area for the fluid being pumped, while also allowing for the necessary inlet and outlet connections. The casing helps to direct the flow of fluid, ensuring that it passes through the impeller and into the discharge nozzle efficiently. Additionally, a well-designed pump casing contributes to the overall pump reliability and efficiency when pump flow is optimized.
What types of materials are used in pump casings?
Pump casings can be constructed from various materials, each selected based on the application requirements. Common materials include cast iron, stainless steel, and various plastics. Cast iron is favored for its durability and cost-effectiveness, making it suitable for many industrial applications. Stainless steel offers excellent corrosion resistance, which is vital in chemical processing environments. In contrast, plastics are used in applications where weight reduction and corrosion resistance are paramount. The choice of material directly affects the casing design, pump efficiency when pump flow changes, and the overall lifespan of the pump casing.
What are the different casing types available for centrifugal pumps?
There are several casing types for centrifugal pumps, including single volute, double volute, and diffuser casing. A single volute casing has one spiral channel that guides fluid to the discharge nozzle, while a double volute casing features two channels, which helps balance radial thrust and reduce vibration. The diffuser casing employs a series of stationary vanes that convert kinetic energy into pressure, offering high efficiency. Each type has its advantages and is chosen based on specific operational requirements, such as flow rate and pump efficiency when pump flow rates vary.
How does casing design impact pump efficiency?
Casing design significantly influences pump efficiency by determining how fluid flows through the pump casing. An
Conclusion
Pump casings are key to a pumping system's success. They affect the system's efficiency and reliability, whether it's a centrifugal or positive displacement pump. The choice of design and materials for pump casings greatly influences the pump's performance.
Centrifugal pumps use special casing designs to control fluid flow and pressure. Positive displacement pumps need a casing to house their moving parts. This shows how important the casing is for each pump type.
The pump industry is always improving, thanks to new materials and design tools. Companies like Asimer Group lead this progress. They focus on engineering and precision to make high-quality pump casings.
By understanding the role of pump casings, users can improve their systems. This leads to better efficiency and productivity in industrial processes. It's all about making the most out of your pumping system.
In short, choosing the right pump casing is vital. It affects the pump's performance and its fit for certain tasks. As technology advances, the role of pump casing design will grow even more important.
At KT-FOUNDRY, we are committed to producing top-quality pump casings that are engineered for durability and exceptional performance. With our advanced manufacturing processes and in-depth material expertise, we ensure each casing is crafted to withstand demanding industrial environments. Our focus on precision casting, corrosion resistance, and rigorous quality control allows us to deliver pump casings that enhance system reliability and efficiency. We also provide customized solutions to meet specific project requirements, ensuring that our products meet the highest standards.
To help us tailor a solution to your needs, please complete the form below.