Valves are key in many mechanical systems. They control the flow of liquids and gases. This is true for homes and big industrial projects.
The making of valves involves several steps. These include designing, getting materials, machining, finishing, and testing. Each step needs skill and attention to detail.
Valves are made through different methods like sand casting and forging. Each method has its own benefits and drawbacks. These include how well they can handle pressure and cost.
Valves are used in many fields. This includes oil and gas, water treatment, and even food and aerospace. Each field has its own needs and challenges.
Key Takeaways
- Valve castings are produced using a range of manufacturing processes, including sand casting, investment casting, and forging.
- Valve casting materials include cast iron, carbon steel, alloy steel, stainless steel, nickel-chromium alloy, and more, each with unique pressure and temperature ratings.
- Valve castings offer design flexibility, allowing for the creation of complex geometries and internal structures, ideal for large-sized, heavy parts.
- Investment casting is a popular method for valve production, providing design flexibility, high-quality surface finish, and cost-effectiveness for small to medium production runs.
- Valve castings find applications across numerous industries, including oil and gas, water treatment, chemical processing, power generation, and more, each with its own unique requirements.
The Valve Manufacturing Process
The valve making starts with designing and making prototypes. Choosing the right materials is key. The material affects how well the valve works, lasts, and fits the environment and use.
Understanding the Application
First, we figure out where the valve will be used. We look at the type of fluid, temperature and pressure, and environment. Then, we pick materials that fit these needs. For example, we use strong alloys for high-temperature and high-pressure uses, materials that resist corrosion for tough places, and safe materials for food and medicine.
Material Selection for Desired Performance
Picking the right materials is very important. It affects how well the valve works, lasts, and fits its use. We look at temperature, pressure, and environment to choose materials that can handle the job. This means picking materials for high-temperature, high-pressure, corrosive, or non-toxic situations.
Prototyping for Validation
We make prototypes to test the design and materials. This process is often back and forth, with changes made to improve the valve's performance.
Iterative Design Process
The making of valves is a cycle of design and testing. Engineers keep improving the design and material choice based on what they learn from testing. This helps make the valve better for its job.
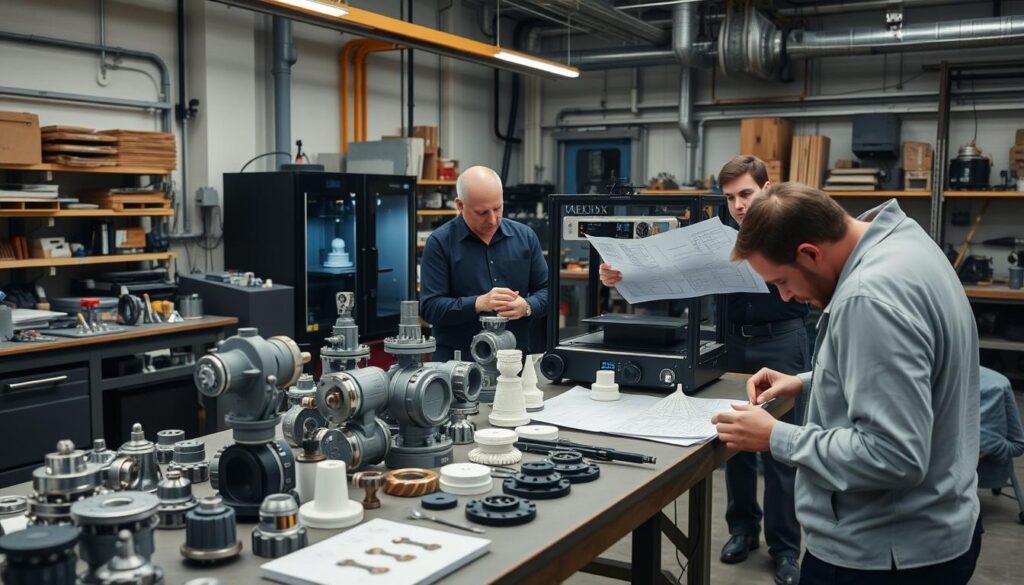
"Valve castings are formed by heating metals to thousands of degrees Fahrenheit, and the casting process of valve blanks is far more complicated than that of general castings."
Stage 2: Material Procurement & Inspection
After the design is set, the next step is getting the right materials. This means getting bar-stock, raw forging, or raw casting from trusted suppliers. These materials then go through a detailed check to make sure they're up to standard.
The check-up follows strict rules, like the ANSI/MSS-SP 55 standard. It looks at the materials' looks, chemical makeup, and size. Tests like visual checks, X-rays, sound waves, and special lights are used to find any problems.
Foundries and valve makers might buy materials from others, team up, or make their own. In places with ISO 9001 certification, the checks are even more thorough. Auditors look at many things, like ISO status, valve maker reviews, and how materials are treated.
The API Committee has made special rules for valve parts, like API 20A for castings. The MSS-SP standards also help check things like surface quality and size. These rules help make sure valve parts are good and consistent.
When repairs are needed, they're sorted into major, minor, or cosmetic types. This follows the ASME B16.34 rules. This careful way of getting and checking materials is key to making valves that work well and are safe.
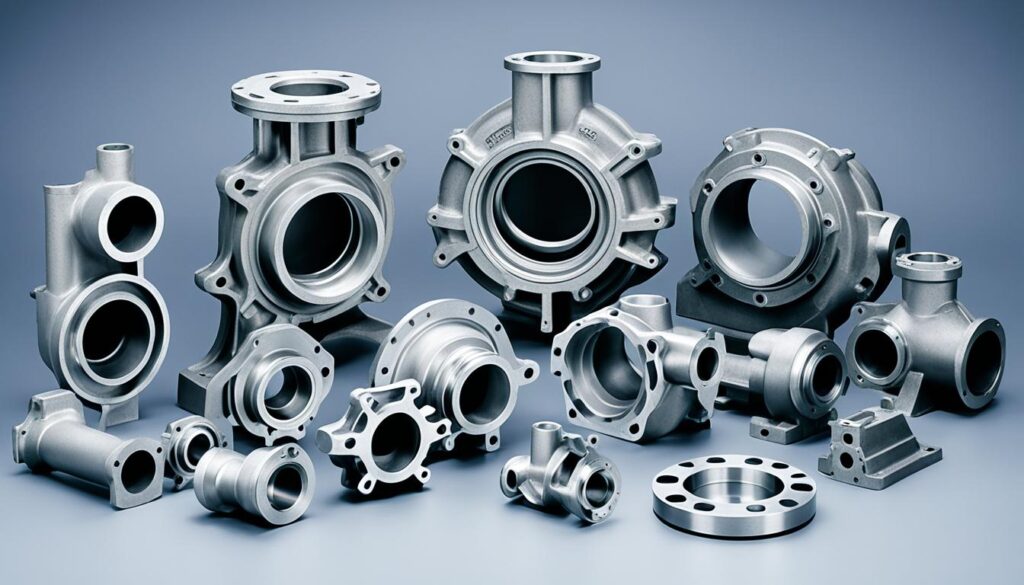
"Proper material selection and rigorous inspection are the foundation of producing high-quality valve castings that can withstand the demands of the industry."
Stage 3: Precision Machining & Component Fabrication
The valve manufacturing process moves to precision machining and component fabrication. This stage turns raw materials into detailed valve parts. Our team uses advanced techniques and top-notch equipment to meet strict standards.
CNC machining is a key process here. Our CNC lathes and mills help us achieve high accuracy and consistency. We also use cylindrical grinders for the right surface finish and size.
At this stage, precision is crucial. The valve parts must fit perfectly for the valve to work well and last long. Our machinists use turning, drilling, and milling to shape the parts as needed.
Machining Capability | Benefits |
---|---|
CNC Machining |
|
Cylindrical Grinding |
|
Turning, Drilling, Milling |
|
Our expertise in precision machining and component fabrication ensures top-quality valve components. This sets the stage for a reliable and durable valve assembly.
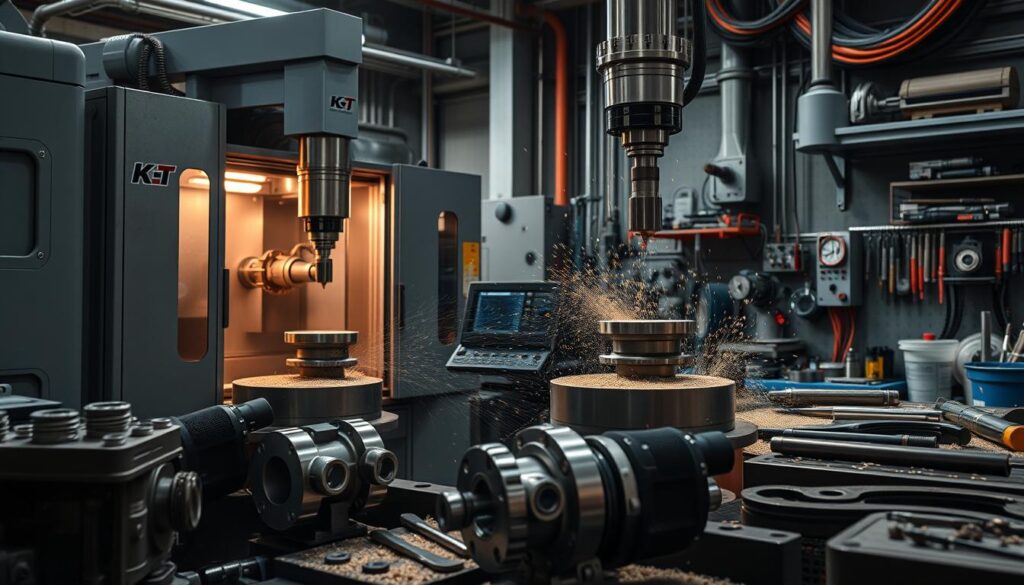
Stage 4: Finishing & Coating
As the valve parts are carefully machined, the next step is applying surface treatments or coatings. This is key to boost the valve's corrosion resistance, surface strength, and durability. Various coatings like epoxy, zinc, or nickel plating are used, depending on the application.
The investment casting method has been perfected over 5,500 years. Aero Metals, a top manufacturer, uses materials like stainless steel, steel, and ductile iron for their castings. This variety ensures the valves can handle many industries, from aerospace to agriculture.
Investment casting can make surfaces as smooth as 125 RMS. This is crucial for a durable valve surface. It also saves time and money compared to other methods, making it popular for valve making.
"Investment casting allows for highly accurate and repeatable designs, ensuring consistent performance and reliability in our valve products."
The finishing and coating end with a detailed quality check. The valves are inspected for size, surface, and inner defects. This ensures they meet high standards, giving customers confidence in our quality.
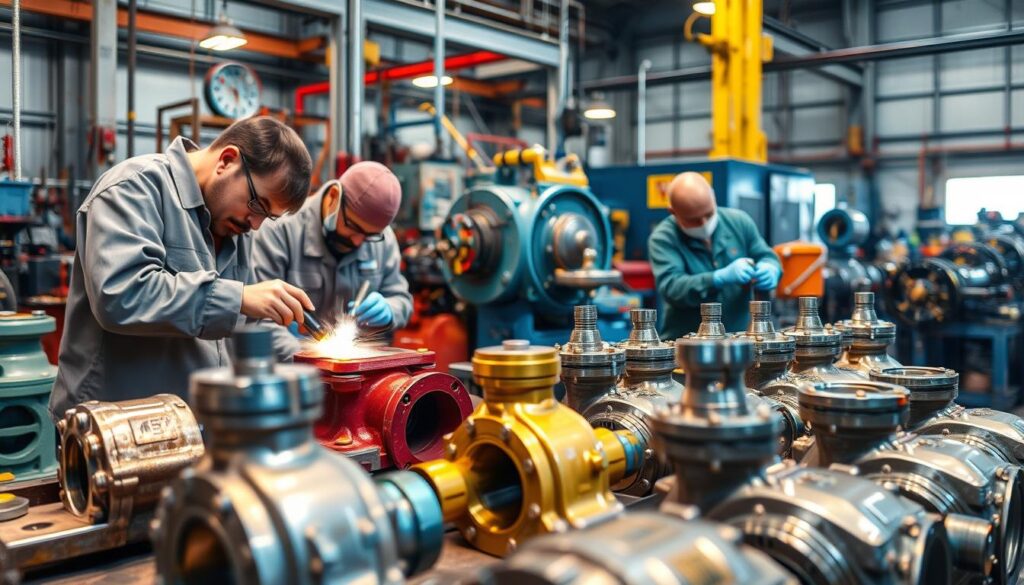
Stage 5: Assembly & Integration
At this stage, all the parts made with precision are put together to form the complete valve. This detailed process needs skilled technicians and special machines. They work together to join parts like the body, disc, seat, stem, and actuators.
The assembly might also include welding and adding extra parts or controls. This depends on the valve's design and use. From simple ball valves to sophisticated multi-functional units, the goal is to make a valve that works well and lasts long.
Casting Method | Advantages | Limitations |
---|---|---|
Cast Ball Valves |
|
|
Forged Ball Valves |
|
|
Choosing between casting and forging depends on design, cost, and strength needs. No matter the method, the assembly stage is key. It ensures the valve works well, is reliable, and safe.
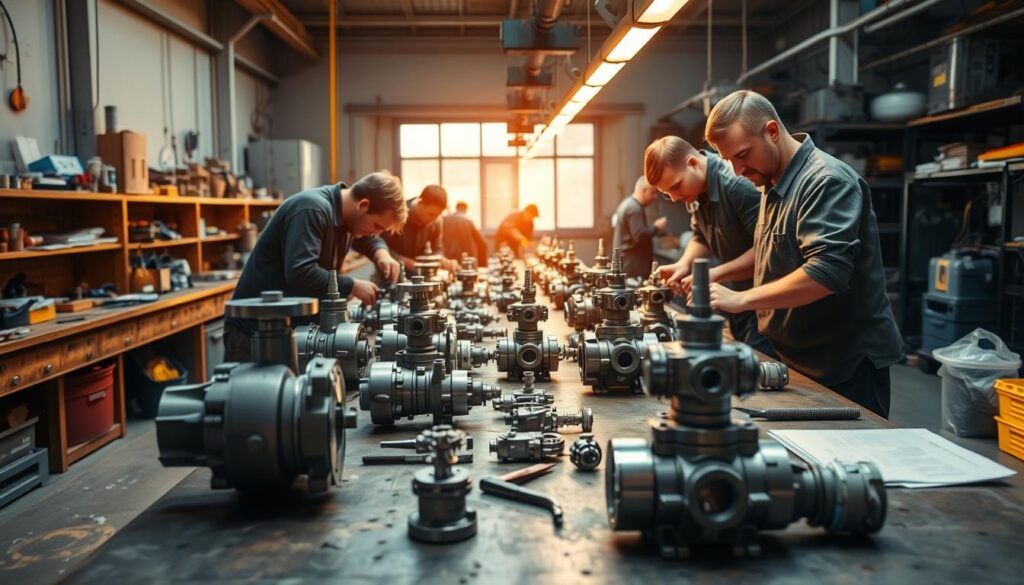
Quality checks are done at every step of assembly. These include checks for size, leak tests, and pressure tests. These tests help make sure the valve works perfectly. This way, we get dependable valve solutions for many industrial needs.
Stage 6: Rigorous Testing and Quality Assurance
Quality is at the core of our valve making process. Before our valves are ready for use, they go through many tests. These tests check if they work perfectly and last a long time. We test everything, from how they handle pressure to how they operate.
We take quality very seriously. A small problem in a valve can cause big issues later. So, we have strict checks to find and fix any issues early on.
Our testing process looks at many things. We check the materials, how well they fit, and if they work right. By testing them in conditions like real-world use, we find and fix any problems. This way, our customers get the best products.
Quality is more than just a goal for us. It's a key part of how we make valves. We choose the best materials and pay close attention to every step. This ensures we always deliver top-notch results.
"Quality is never an accident; it is always the result of high intention, sincere effort, intelligent direction, and skillful execution. It represents the wise choice of many alternatives."
Our dedication to quality makes us stand out in the valve making world. By testing and checking our products, we can promise our customers the best performance and reliability. We do this every time.
Step 7: Packaging & Distribution
After our high-quality valves pass quality checks and get their final touches, we start packaging and distribution. It's crucial to pack them right to keep them safe during transport. This way, they arrive at the customer's place ready to install and use without a hitch.
We pick the best packaging materials and methods to protect our valves. This includes strong, shock-resistant boxes, special padding, and tight seals. By focusing on packaging, we ensure our products stay safe during distribution and transportation.
Our wide distribution network makes sure our valves get to customers fast and reliably all over the world. We use both trusted logistics partners and our own advanced distribution setup. This helps us handle global distribution challenges well. It also lets us meet the varied needs of our customers on time.
At THINKTANK, we aim to give our customers the best experience from the beginning to the end. By carefully handling packaging and distribution, we keep our valve castings' quality and integrity high. This makes us a top choice in the industry.
"Exceptional packaging and seamless distribution are essential components of our unwavering commitment to customer satisfaction."
We're always working to improve and innovate in packaging and distribution. This keeps us ahead and meets our customers' high expectations. By consistently delivering excellent valve castings, we build strong partnerships and move the industry forward.
Applications of Valve Castings Across Industries
Valve castings are used in many industries. Each one has its own challenges and needs. These parts are key in controlling the flow and pressure of fluids and gases in important systems.
Oil and Gas Industry
In the oil and gas industry, valve castings are vital. They help with drilling, extraction, refining, and moving oil and gas. High-pressure valves made of strong materials are needed for these tough jobs.
Water and Wastewater Treatment
The water and wastewater treatment sector needs valve castings. They help control water flow and manage waste. These parts must be durable and resistant to corrosion to work well and keep the environment safe.
Chemical Processing Industry
The chemical processing industry uses special valve castings. These valves can handle corrosive or toxic chemicals. They are made of materials like Teflon or PVC to ensure safety and control.
Power Generation
Power plants use valve castings to manage steam and water flow. These valves must handle high temperatures and pressures. They are crucial for power plants to work efficiently and reliably.
Food and Beverage Industry
In the food and beverage sector, stainless steel valve castings are used. They are used in processing, packaging, and moving products. These valves help keep food safe and meet high hygiene standards.
Aerospace and Aviation
Aerospace and aviation need lightweight valve castings. These parts must handle high pressures and extreme temperatures. They ensure fuel, hydraulic, and environmental systems work safely and reliably.
Consumer Appliances
Valve castings are in consumer appliances too. They control water, gas, and refrigerant flow in systems like plumbing, HVAC, and water supply. These valves focus on being affordable, reliable, and safe for users.
Residential and Industrial Plumbing and HVAC
Valve castings are key in plumbing and HVAC systems. They manage water, steam, and other fluids. This helps systems work well and efficiently.
Valve Casting
In the world of industrial operations, controlling fluid and gas flow is key. Valve casting is a vital process that turns molten metal into precise valve parts. It's used in pipelines and processing plants to ensure efficient and safe operation.
Unveiling the Art of Valve Casting
Valve casting involves pouring molten metal into a mold to create valve parts. This method makes many types of valves, each for different flow control needs. Common types include:
- Gate Valves: Control fluid or gas flow with a sliding gate.
- Globe Valves: Regulate flow through a circular opening with a movable disc or ball.
- Ball Valves: Shut off fluids quickly with a rotating ball.
- Butterfly Valves: Use a rotary disc for flow control, offering a cost-effective solution.
Valve castings are made from materials like cast iron, carbon steel, and stainless steel. The choice depends on the application's needs.
Valve Type | Typical Materials | Applications |
---|---|---|
Gate Valve | Cast iron, carbon steel, stainless steel | Oil and gas, water and wastewater, chemical processing |
Globe Valve | Cast iron, alloy steel, stainless steel | HVAC, power generation, chemical processing |
Ball Valve | Carbon steel, stainless steel, nickel-chromium alloy | Oil and gas, industrial automation, water and wastewater |
Butterfly Valve | Cast iron, carbon steel, stainless steel | Water and wastewater, HVAC, power generation |
Valve casting lets manufacturers create custom solutions for different industries. This ensures optimal flow control and system performance.
"Valve casting is the heart of efficient flow control, enabling industries to harness the power of fluids and gases with precision and reliability."
Conclusion
The valve manufacturing process is key to making systems work well in many industries. It starts with designing and prototyping, where we pick the right materials for each job. Then, we move to assembly, testing, and getting the valves to customers.
Valves are made in different ways, like sand casting, investment casting, and forging. They are used in many fields, from oil and gas to home appliances. We tackle each industry's unique needs by knowing a lot about materials and how they perform.
We focus on using materials that are cost-effective, reliable, and safe. This way, our valves can handle fluids, gases, and steam in many situations. Our goal is to keep improving and offer top-notch solutions to our customers.
We are all about innovation and making things better. Our commitment to excellence makes us a reliable partner in the valve industry. We aim for efficiency, safety, and sustainability in everything we do.